化学镀液多周期后的维护
文/姬玉林·山东蓝星清洗防腐公司
化学镀液的维护在生产中占有重要地位,一旦维护不慎,会对施镀造成严重的影响和巨太的浪费。
化学镀镍工艺在1946年发现以来,已经从一个实验室的奇迹,发展成为工业上有实际应用价值的镀层技术,被众多行业广泛地接受和认可。其迅速发展的原因是由于镍磷合金镀层具有优异的物理、化学和机械性能,还由于其工艺简便可行,不受复杂生产设备的限制,并且其镀覆速率、镀液的稳定性、镀液的维护、补充和再生性能等都取得了重要的进展。由于这些问题得到了较好的解决,从而延长了镀液的使用周期,降低了生产成本,为其创造了美好的应用前景。
但是随着镀液使用周期的增加,镀液要求的维护条件也越来越苛刻,一旦维护不慎便造成镀液的分解、槽壁及加热盘管上的沉积、工件的退镀,其浪费是十分惊人的,丽且尺寸要求严格的工件是无法退镀的,所以笔者认为选择较好的配方和工艺固然很重要,更重要的是对镀液后期的精心呵护,确保施镀过程的顺利进行。
根据多年从事化学镀工作的经验,笔者总结出一些对高磷镀液后期维护的措施及分析。
pH值的调整。
pH值的高低直接影响镀覆的速率和镀液的稳定性。随着pH值的升高,镀覆速率提高,镀覆时间缩短、能耗下降,同时也提高了次磷酸盐的利用率,但是镀液的稳定性下降,很容易造成镀液的分解。
为了避免这种情况的发生,应做到在施镀过程的情况下,要采取小量连续的方法用1:1NH3·H20来调整,控制在pH4.0~4.5,经常用pH试纸和pH计来对照测试结果。而降温后,镀液倒槽再生的过程中用10%的NaOH来调整,调整后应做升温前的加热试验,将镀液加热到95℃以上或到沸腾,持续不一段时间又发生浑浊即可,否则要用稀H2S04反调(乳酸、醋酸也可以)。
提高促进剂含曼
新配镀液在开始(最初的)2~3个周期,没有其他杂质毒物和副产物含量十分低,反应物质有效浓度较高,镀速较快,为防止镀速过高,容易引起镀液分解,前期一般都加一定量的稳定剂,降低还原反应的活性,随着使用周期的延长,原料中有毒物、副产物以及结合剂、稳定剂在镀液中的富集,镀液中有效成分浓度及活性相对降低,从而镀速也相应地下降,所以后期要停止加稳定剂,而是应要相应提高促进剂的含量。
加强工件表面的前处理
在施镀前,应对工件表面进行前处理,如除油、除锈、活化,特别是活化后热水清洗要加强,防止工件将其它杂质及污染物带入镀槽,并在活化后热的清水槽中加入少量的NH3·H2O
,使工件表面带有少量的微碱性溶液,这样工件入镀槽后,会加速起镀反应,对工件表面快速覆盖一层镀层起到促进作用,有利于用形成(后期)均匀较密的镀层,降低孔隙率。加强施镀过程中的循环过滤。
循环过滤一是防止镀液中过多的杂质微粒,作为反应的活化中心,导致镀液的分解,同时也防止其沉淀在镀层上,使镀层表面粗糙,导致孔隙率提高;二是有利于均衡槽内反应条件;三是防止加热盘管附近镀液局部过热,造成盘管上沉积镀层或引起镀液分解;四是有利于反应过程中产生的氢气快速逸逃工件表面,使工件表面的反应均匀快速。
免责声明:本网站所转载的文字、图片与视频资料版权归原创作者所有,如果涉及侵权,请第一时间联系本网删除。
-
标签: 维护化学镀液多周期
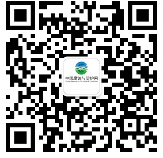
官方微信
《腐蚀与防护网电子期刊》征订启事
- 投稿联系:编辑部
- 电话:010-62316606-806
- 邮箱:fsfhzy666@163.com
- 腐蚀与防护网官方QQ群:140808414