据报道,金属腐蚀导致全世界每年每辆汽车平均损失为150~250美元, 可以估算出2013年我国因汽车腐蚀造成的经济损失达1700多亿元,造成材料、能源浪费,导致巨大的经济损失,同时还带来环境污染、交通事故。
文/ 朱春东、严威、邓广新·武汉理工大学
中国汽车工业协会发布的数据显示中国汽车销售加速增长,2013年,汽车产销2211.68万辆和2198.41万辆,同比增长14.76%和13.87%,比上年分别提高10.2和9.6个百分点。中国已超过美国,成为全球第一大汽车市场。
在汽车工业高速发展的同时,延长汽车服役寿命是各国追求的目标之一。事故损坏、摩擦损坏、腐蚀损坏分别是汽车损坏的三种主要形式,其中最为普遍和严重的是腐蚀损坏,尤其是在沿海地区以及工业发达地区腐蚀损坏已经成为影响汽车使用寿命的主要原因。
据报道,金属腐蚀导致全世界每年每辆汽车平均损失为150~250美元,可以估算出2013年我国因汽车腐蚀造成的经济损失达1700多亿元,造成材料、能源浪费, 导致巨大的经济损失,同时还带来环境污染、交通事故。在1985~1991年间对瑞典和我国汽车腐蚀调查表明,除意外交通事故损坏及部分零部件磨损外,汽车腐蚀是汽车损坏报废的重要原因。近些年来,由于汽车零部件腐蚀而导致的汽车召回事件不在少数。加强对汽车的腐蚀防护,正确使用、合理维护与保养汽车, 对于安全运行、延长其使用寿命具有重要意义,同时这也是汽车厂家和消费者的共同愿望。图1所示的为一些汽车腐蚀案例。
图1 汽车腐蚀案例
汽车常见的腐蚀类型
汽车由各种金属材料零件和非金属材料零件组成,在汽车使用的各种环境中无论是金属材料还是非金属材料都会有腐蚀问题。这些腐蚀发生在汽车的各个零部件上,轻则影响汽车外观,重则造成功能损伤,导致交通事故,危及人的生命财产安全。汽车的腐蚀形态有很多,影响因素也是多种多样的。
汽车腐蚀试验
随着汽车腐蚀问题慢慢进入公众的视野,汽车腐蚀所带来的危害也开始引起人们的关注。汽车防腐越来越被重视,相关法规的颁布则加速了这种趋势,汽车的抗腐蚀性能已成为生产厂家对汽车性能的主要考核项目之一。
腐蚀测试能检验产品的防腐能力, 甄别产品的质量,提高产品的竞争能力, 因而许多汽车厂家相继展开了相关试验。汽车零部件的腐蚀测试主要有以下几种: 1、盐雾测试(中性盐雾、乙酸盐雾、铜加速乙酸盐雾、交变盐雾 );2、冷凝水 \水雾试验;3、气体腐蚀试验;4、循环腐蚀试验(CCT);5、腐蚀膏试验;6、耐溶剂试验(耐酸碱、汽油等各种溶剂)。其中,中性盐雾、冷凝水\水雾、气体腐蚀和循环腐蚀试验是最常用的加速腐蚀试验, 在汽车零部件的防腐测试中被广泛使用。
中性盐雾试验(NSS)与实际的自然腐蚀试验相关性很低,甚至有研究结论认为毫无相关性,但是NSS目前应用非常广泛,被普遍认可并一直被认为是腐蚀试验的基础试验。循环腐蚀试验(CCT)在恒定盐雾试验基础上引入了高温、湿度、低温、干燥等参量,还有部分加入紫外、氙光等老化因素,尽可能考虑了自然环境中的诸多条件因素,目的是取得了和自然环境相关性更高的试验结构。相对于NSS而言,CCT拥有更贴近于实际腐蚀状态,周期短,能模拟实际环境中的温度和湿度变化,能够更大程度上反映出镀层或涂层的缺陷点,对工件的抗腐蚀性能要求更高等优点。正是因为这些优点,越来越多的整车厂采用新的加速循环腐蚀试验来取代原有的中性盐雾试验。
整车的防腐测试现阶段则主要是道路强化腐蚀试验,模拟沿海地区盐雾沉降、北方冬季冰雪路面撒盐的腐蚀环境,通过高温高湿、高低温交变、盐雾喷射、盐水路、碎石路、强化坏路行驶和高速行驶等多种试验工况,暴露汽车产品在结构设计、材料选用和防护工艺等方面的腐蚀问题,以此来考核及评价汽车在极其恶劣的使用条件下的抗腐蚀性能,为提高产品抗腐蚀能力提供依据。海南汽车试验研究所自1998年起,开始进行汽车腐蚀试验的摸索,制定了《海南汽车试验场汽车道路强化腐蚀试验》进行发布,该方法于2005年7 月已作为汽车行业标准《乘用车强化腐蚀试验方法》进行发布,得到了广泛认可。
尽管不少车企做了相关的汽车腐蚀测试的研究,但是各大厂家进行腐蚀测试实验的周期各不相同,如中性盐雾试验,ISO 9227-2006推荐的试验周期从2h到1000h不等,这些推荐时间,没有针对性指出何种产品适用,生产厂家很难选择。同时,大量的试验数据处于分散的状态,数据资源没有共享,也没有统一的平台对这些数据进行整合。这些不仅导致大量重复试验的进行,造成了资源浪费,还给汽车腐蚀测试的发展带来了无形的阻力,进而也影响到了国内汽车防腐技术的发展。
国内汽车防腐现状
我国汽车工业发展水平与世界先进水平相差较大,投入使用的汽车1~2年后就出现腐蚀,3~4年就有部件腐蚀穿孔。国内对于腐蚀防护的研究也非常落后,国外从六十年代就开始了整车道路强化腐蚀试验,这项试验对于汽车腐蚀防护能力的提高有着极其重要的作用,而我国在这一方面起步则相当的晚。海南汽车试验研究所自1998年起,开始进行汽车腐蚀试验的摸索,并于1999年正式开始汽车道路腐蚀试验,至今,已完成百种车型的试验任务, 积累了大量的试验数据。其试验结果显示,部分自主品牌与合资品牌仍存在有一定的差距。
国内汽车的防护设计、防腐技术的应用和工艺水平相对偏低。一些国产汽车油漆层的丰满度、平整度和光泽度及附着力偏低;镀层、转化膜的质量欠佳,尤其是重腐蚀环境(酸雾、高温等)中零件的耐蚀能力差。直接表现在使用一段时间后出现锈渍,油漆层起泡、剥落、变色、失光,油箱清洁度降低,非金属件变形等。与国外或国内合资企业制造的品牌汽车相比,国产汽车的造型、使用的材料及工艺直接影响了产品的档次。
2014年,第二届中国汽车防腐蚀与老化技术论坛召开,众多整车企业积极参与。各企业交流汽车腐蚀与防护的经验与想法,这对于促进汽车防腐的发展有着非常积极的作用,同时也反映出国内大环境对于汽车防腐蚀越来越重视。
汽车腐蚀防护
整车防腐性能的基本需求主要是从两个方面出发,一是美观,二是保证汽车的功能性。在保证美观和功能的同时也应该尽量降低成本。做好防腐工作应从以下几个方面入手:1、从结构设计上避免腐蚀; 2、汽车零部件合理选材;3、在使用保养上防腐;4、从制作工艺上防腐。
结构设计不仅要考虑金属零部件的力学性能和加工性能,还要考虑金属腐蚀原理和腐蚀形态。各种防腐设计的应用和效果受如下因素的影响:温度、排水孔的位置、空气流通能力、气流飞溅引起的泥土与道路盐的沉积、不正确的搭接和缝隙处无法覆盖电泳涂层。合理的结构设计可以使汽车的腐蚀大大减轻,并控制腐蚀的发生。在设计时应避免尖端、空腔、缝隙和容易引起雨水的沉积区域的形成等,电位差差异较大的两种金属的接触容易发生电化学反应,需要在两种材料之间增加相容的材料。
汽车使用的金属材料有很多种,每种材料的耐腐蚀性能都不一样。合理选材是提高汽车耐腐蚀能力的有效方法,再与适当的防护措施相结合,可以保证汽车外观和使用寿命的要求,如车身钢板采用了镀锌钢板或锌合金钢板,大大提高了车身的耐腐蚀能力,近年来铝合金也应用于车身钢板。宝山钢铁有限公司的研究发现,Zn 基镀层热冲压用钢和裸板及AISi镀层热冲压用钢相比具有更好的防腐保护作用。非金属材料一般不会发生腐蚀,用塑料代替金属材料也是一种提高零部件防腐能力的有效方法,如使用塑料油箱和油箱口盖, 如图3所示。
图3 车用塑料油箱
合理保养。经常对汽车进行清洗保养,也能起到很好的防腐作用。目前国内汽车虽有多级保养制度,但并不涉及防锈处理,可以建立定期清锈和防锈处理制度。
从制作工艺上防腐则主要是指汽车防腐表面处理,目前汽车常用的表面处理方式有电化学处理(电镀和阳极氧化)、涂装(喷涂和电泳)、化学处理(磷化、钝化、发黑等)、热处(热浸镀、热喷涂、热烫印、化学热处理等)、真空法(蒸发镀、溅射镀、离子镀等)。合理的表面处理是提高零部件防腐能力最有效的方法, 根据零部件的结构、材料、性能和所服役的环境决定其表面处理方式,如高强度标准件采用达克罗处理,内部区域的标准件采用镀锌处理。下面简单介绍几种常用的汽车防腐表面处理方式:
汽车常用表面处理工艺-电镀锌
电镀锌,行业内又称冷镀锌,就是利用电解,在制件表面形成均匀、致密、结合良好的金属或合金沉积层的过程。电镀锌的工艺:上夹具-前处理-水洗-钝化-水洗-干燥。其中钝化处理是为了提高镀锌零部件的抗蚀性和装饰性。按照电镀工艺中使用原材料可以将电镀锌分为碱性镀锌和酸性镀锌。
(一)碱性镀锌
(1)氰化物镀锌。包括高氰、中氰、低氰和微氰镀锌。其优点是氰化镀锌对于金属杂质不太敏感,镀液分散能力和深镀能力好,镀层结晶细致,纯度高,结合力和耐蚀性性能好,能得到厚镀层。合适复杂零件的电镀。但是氰化物有剧毒,对环境影响大,以后的发展趋势是发展无氰碱锌。
(2)锌酸盐镀锌。主要成分有氢氧化钠、氧化锌和相应的添加剂。优点是镀液分散能力和深镀能力接近氰化镀液,镀层结晶细致,光泽性好,槽液稳定,对设备无腐蚀。缺点是温度范围窄,镀层厚度超过15μm有脆性。
(二)酸性镀锌
(1)氯化物镀锌。包括氯化铵镀锌、氯化钾镀锌和氯化钠镀锌。优点是镀锌电流效率高,镀速快,镀液简单。镀液分散能力和深镀能力好,氢脆性较小,镀层结晶细致,光泽性好。缺点是镀层杂量大, 纯度低,对设备有腐蚀。
(2)硫酸盐镀锌。其优点是配方简单,技术成熟,电流效率高,沉积速度快,导电性好,价格低廉等。缺点是分散能力差、极化能力小、镀层结晶粗糙、镀层外观发暗,表面光洁度差。
电镀锌的后处理涉及到除氢处理、钝化处理、镀锌层着色和膜层封闭。钝化处理过去一直使用六价铬,由于六价铬具有很强的光敏性和致敏性,可导致临床明显的接触性湿疹,并且六价铬属于致癌物质,故各国相继开始对六价铬实行禁令。使用三价铬或者其他材料替代六价铬也是镀锌的一个发展趋势。
汽车常用表面处理工艺-达克罗
达克罗,国内命名锌铬涂层,是一种以锌粉、铝粉、铬酸和去离子水为主要成分的新型的防腐涂料。达克罗层外观为均匀的银白色,涂层中80%为锌、铝, 其余是铬酸盐。工艺流程为:有机溶剂除油--机械抛光--喷涂--烘烤--二次喷涂--烘烤--干燥。图4所示的为经达克罗处理的零件。
图4 达克罗件
达克罗是一种新型的表面处理技术, 与传统的电镀工艺相比,达克罗是一种“绿色电镀”。其优势有以下几点:1,优异的防腐性能;2,无氢脆性;3,耐高温强;4,对油漆的着附力强;5,生产工艺全程闭路循环,对环境无污染。达克罗涂层虽然有很多优点,但它也有一些不足之处,如部分达克罗层中含有对人体有害的六价铬。达克罗件常用于重载汽车上的各种高强度底盘中小支架、连接件、外露件及紧固件、发动机周围等高热环境金属制件、各种弹性零件以及各种形状复杂的管类、腔类零部件的防腐。
汽车内腔喷蜡工艺
资料报道显示,乘用车内腔是频发腐蚀部位之一,瑞典和中国防腐专家对市场乘用车腐蚀损坏的调查结论之一:内腔采用防锈蜡保护的车型,使用7年后,避免了腐蚀的发生。内腔没用采用防锈蜡保护的车型,使用三年后,50%发生了严重腐蚀。
汽车内腔用蜡主要有两大类:一种是溶剂型防锈蜡,另一种是固体蜡。空腔喷蜡分为:室温、加温注蜡和灌蜡三种方式。内腔室温注蜡工艺说明:1、注蜡前处理,运输链将车身吊至适宜工位,用专门的橡胶或塑料帽堵上底板处的进漆孔。2、高工位进行底板横梁、纵梁等的喷涂,低工位进行前盖、立柱、车门、后盖内腔等的喷涂。3、室温晾干,用溶剂润湿过的白纱布或无纺布擦去多余的蜡,堵上底板处的注蜡孔,检查合格后送往内饰。
结语
随着汽车行驶里程和使用年限的增加,汽车各部位的腐蚀现象将逐渐加剧。汽车腐蚀现象不仅会破坏汽车的外观,还直接影响到整车的质量和使用寿命。因此, 汽车防腐是汽车制造及使用中的一个重要部分,汽车防腐技术的发展对于车辆的使用具有重要意义。
国内的大部分汽车厂还没有成立专业的部门对汽车的防腐进行统一负责,使得防腐工作过于分散,缺乏系统性。应组建专业防腐部门统一负责防腐,建立起防腐体系,来提高整车的防腐水平。而且,随着汽车工业的发展,汽车行业应该建立一套针对于国内汽车的防腐标准。
汽车腐蚀的试验数据处于分散的状态,数据资源没有共享,导致大量重复试验的进行,造成了资源浪费,影响国内汽车防腐技术的发展,因此,建立统一的平台对这些数据进行整合势在必行。
免责声明:本网站所转载的文字、图片与视频资料版权归原创作者所有,如果涉及侵权,请第一时间联系本网删除。
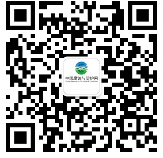
官方微信
《腐蚀与防护网电子期刊》征订启事
- 投稿联系:编辑部
- 电话:010-62316606-806
- 邮箱:fsfhzy666@163.com
- 腐蚀与防护网官方QQ群:140808414