前言
不论是架空管线还是埋地管线,高质量的内外防腐对于延长管线使用寿命,实现安全运行都是至关重要的。随着 3PE 技术的普遍应用,在外防腐方面我国有了较为完整的体系,包括采用 3PE、环氧粉末涂料、液体涂料(环氧涂料、聚氨酯涂料)及包覆类材料等技术。这些原材料的生产技术、防腐工艺、执行的标准都与国外先进技术相差无几。
而在内防腐方面存在问题就比较复杂,一是介质的复杂性,管线输送介质包括原油、水、含油污水、采出液等,有些介质的腐蚀性远远超出土壤和大气的腐蚀性,二是焊接热影响区的影响,由于内补口技术的滞后,焊接热影响区的存在限制了有机涂层的使用,即使管体防腐层性能再好,补口解决不好也不能从根本上解决问题。三是成本的影响,由于成本控制使得一些耐蚀管材、双金属管的使用受到了限制,四是维护方便性的要求,非金属管材在耐蚀方面有着较大的优势,但在耐压及使用维护方面又存在一些问题。
因此可以认为,不论是埋地管线还是地上管线(尤其是小口径管线),内防腐的质量直接影响了管线的使用寿命及安全运行。以西北某油田一个采油厂为例,该采油厂有各类管道 5576 条,总长 6877.8km,2015 年对 3340 条管线进行摸排,共查出隐患 859 条,其中腐蚀穿孔 724 条,占总隐患数的 84.5%。输送介质的强腐蚀性和内防腐措施薄弱是引起管道腐蚀的主要原因。
而在解决内防腐方面内补口又成为了制约因素,其中小口径管线(DN200 以下)的内补口尤其是难点。本文主要讨论用于埋地小口径管线的内外防腐技术。
内补口技术的探索
防腐业界对管线内补口尤其是小口径管线内补口近年来做了不懈的努力和探索,也包括引进消化了一些国外技术。国内曾经应用的技术如UB滑套、 补口车、焊接不锈钢短节、在线挤涂等,这些技术都有一定的防护效果,但还是存在着成本高、受管径限制、质量不易控制等不足,在一定程度上限制了推广使用。
为了解决这一难题,在大量调研的基础上,我们提出了小口径管线内外一体化工厂预制防腐蚀的理念并进行了深入研究。 经过几年的努力, 研究出了 “堆焊固溶端头处理 + 内外有机防腐层”的小口径管线内外一体化(简称 DGR)防腐蚀技术。利用 DGR 技术生产的防腐管可以现场直接焊接安装,免除了内补口工序且能实现管内防腐层连续完好,能够较好地解决小口径管线的防腐难题。
图1 内补口车
2道O型密封圈内衬套(左) 4道O型密封圈内衬套(右)
图2 O型密封圈内衬套
DGR 内外一体化防腐技术
1、组成、特点及流程
⑴组成
DGR 内外防腐包括三部分:①管端内表面的耐蚀合金堆焊固溶层;②管体内表面的耐蚀环氧粉末防腐层;③管体外表面的环氧粉末或 3PE 防腐层。
⑵特点
DGR 内外防腐技术具有以下特点:
①单根钢管内外涂(覆)层和端头内堆焊均在工厂预制完成,质量可检、可控,②管端堆焊层与管体内表面实现平滑过渡,③钢管内壁除热影响区外,管体及管体与堆焊层的过渡区环氧粉末一次成型(焊接热影响区由耐蚀合金起到防腐作用),④可以根据输送介质选择不锈钢焊材,⑤现场焊接完成后只需要做外补口,不需要内补口。
⑶流程
DGR 内外防腐技术的流程为:端头内表面预处理→端头堆焊固溶处理→内壁喷砂处理→内壁喷涂环氧粉末→外壁抛丸处理→外壁涂敷环氧粉末 ( 或3PE) →端头外处理→质检。
2、端头处理
按照端头热影响区的尺寸,首先对端头内表面进行预处理,之后进行堆焊固溶处理,其流程为:(1) 对管端内表面进行轻喷砂处理,(2) 预热,(3) 选用适当的耐蚀合金做堆焊层,(4) 对堆焊层两端进行固溶处理,(5) 对预补口内孔机械加工。
耐蚀合金可根据输送介质的成分和腐蚀性,选择镍基合金、双相不锈钢和奥氏体不锈钢等耐蚀合金材料。
由于采用了变电流堆焊工艺,并采用 TIG 焊接专用机,保证了堆焊层的平整度。堆焊层厚度 1.5 ~ 2.0mm,堆焊层长度可按经验或实际测量确定,一般不小于 50mm。
通过对预补口内孔的车削加工,可实现不同钢管管端内径的一致,保证了管道内组对精度,从而保证了内焊道质量。
图 3 小口径钢管DGR内外防腐示意图
1-环氧粉末涂层;2-搭接覆盖区;3-堆焊预补口区;4-钢管母材
图4 小口径钢管内壁“堆焊+涂层”防腐示意图
3、内防腐粉末涂敷
内防腐粉末的性能首先要满足 SY/T0442-2010《钢质管道熔结环氧粉末内防腐层技术标准》的要求,在此基础上,如果介质有特殊性就应该增加相应性能指标。如对于单井管线和污水管线,如果H 2 S、CO 2 含量较高或温度较高,在选择粉末涂料时就要相应增加耐 H 2 S、CO 2 或者耐温试验,以确保满足使用要求。标准中关于涂层厚度分为了普通级和加强级,普通级≥ 300μm,加强级≥ 500μm。除消防管线外,只要是腐蚀较严重的介质建议采用加强级,适当增加涂层厚度对于提高防腐质量是很有好处的,内防腐环氧粉末涂料及涂层性能指标要求详见表 1。
为了确保环氧粉末固化完全,本工艺采用固化炉进行后固化,固化时间为30min,固化温度为 200℃~ 230℃。
内环氧粉末涂敷流程为:
喷砂处理 (Sa2.5级) →吹扫除尘 (2级)→中频加热→粉末喷涂→后固化→质检
喷砂处理:除锈等级 Sa2.5 级,粗糙度 50 ~ 100μm
中 频 加 热: 钢 管 加 热 温 度200 ~ 260℃
粉末喷涂:正压喷粉
固化温度:200 ~ 230℃
质检:外观、厚度、漏点等
4、外防腐技术
外防腐材料可选择的余地较大,3PE、环氧粉末涂料、液体涂料(环氧涂料、聚氨酯涂料)及缠带包覆类材料都可用于外防腐,选择时可考虑以下因素:(1)土壤的腐蚀性(2)安装过程机械损伤的可能性,(3)外补口的可靠性,(4)经济性。
比较干燥且土壤条件较好,安装回填不会造成机械损伤的建议采用环氧粉末涂料,土壤条件较差不能保证细土回填的建议采用 3PE 等。DGR 内外防腐技术由于是工厂预制,且针对的是小口径管线, 仅采用环氧粉末或3PE两种方式,液体涂料及缠带包覆类材料不在本文讨论范围之内。
采用环氧粉末时,其流程为:
抛丸处理→中频预热→静电喷涂→固化→水冷→检验。
抛丸处理:Sa2.5 级
锚纹深度:40 ~ 100μm
中频加热:180 ~ 230C
质量控制依据:SY/T0315-2013 《钢质管道熔结环氧粉末外涂层技术规范》 ,详见表 2。
表2 外防腐环氧粉末涂料及涂层性能指标
采用 3PE 时,其流程为:
抛丸处理→中频预热→静电喷涂→固化→涂胶→包覆 PE →水冷→防腐层端头处理→检测。
质量控制依据 GB/T 23257-2009《埋地钢质管道聚乙烯防腐层》,详见表 3。
表3 3PE外防腐层的性能指标
焊接工艺评定
由于 DGR 管道端头的特殊结构,为保证焊接质量,需要采取特殊的焊接方式,即:采用免充氩药皮耐蚀合金焊丝TIG打底焊接, 然后采用手工电弧焊工艺填充盖面。由于采用了耐蚀合金,使焊缝区域与堆焊层、内防腐层形成连续的防腐层,因此无需进行内补口防腐作业,施工简单快速。
1-不锈钢焊口;2-不锈钢预补口区;3-固溶区;4-内熔结环氧防腐涂层;5-外熔结环氧防腐层;6-钢管。
图5 DGR一体化防腐钢管示意图
为验证焊缝的焊接质量,委托中油一建焊接培训中心和中国石油集团工程技术研究院焊接实验室对 DGR 焊缝进行了焊评测试,测试标准采用石油行标 SY/T0452-2012《石油天然气金属管道焊接工艺评定》。具体的焊接工艺参数如下:
钢管管径:φ60
钢管厚度:5.5mm
钢管材质:20# 钢
打底焊焊材:ER2209 2.4mm
填充及盖面焊材:E309L-16 2.0mm
焊接方法:SMAW
焊接电流:70~90A
评定主要技术指标及测试结果见表 4。
从上表可以看出, 采用上述方式焊接的DGR管道端口焊接质量完全满足标准要求。
图6 焊评试验照片
室内耐蚀性能评价
为测试 DGR 管道内防腐层的实际防腐性能,开展了室内耐蚀性性能评价,包括管道端口的堆焊层和管体的环氧粉末防腐层。
1、堆焊层耐蚀性评价
试 验 采 用 SY/T0029-2012《 埋 地钢质检查片应用技术规范》中的失重法测试堆焊层的平均腐蚀速率,即把带堆焊层的试片用环氧涂层封底封边后,分别放置在常温常压下的两种化学介质溶液(3% NaCl 溶液和 10% NaOH溶液)中,浸泡时间为 32d。试验堆焊 材 质 为 不 锈 钢 2209, 试 件 尺 寸 为50mm×80mm×25mm,具体尺寸如图 7所示。
图7 堆焊试件实物图及试验暴露面积示意图
试验结束后观察发现,堆焊层表面光滑平整,没有发现蚀坑,在两种介质溶液中浸泡后的失重重量及腐蚀速率计算结果见表 5。
表5 堆焊层在不同介质中腐蚀速率测试结果
从表 5 中可以分析得出,耐蚀合金堆焊层耐 10%NaOH 溶液介质、3%NaCl 溶液腐蚀性能较好,浸泡 32d 后,腐蚀速率< 0.01mm/a。
2、环氧粉末内防腐层耐蚀性评价
作为保护管道内壁的主要防腐体系,环氧粉末内防腐层的耐蚀性能也是非常重要的,除按照标准 SY/T0442-2010《钢质管道熔结环氧粉末内防腐层技术标准》要求的规定进行常规检测外,还特别进行了防腐层在碳钢及耐蚀合金基材的拉拔附着力和高温高压加速耐蚀性试验,拉拔附着力的测试方法为 GB/T 5210,具体测试结果见表 6。
表6 环氧粉末内防腐层耐蚀性测试结果
从表 6 中可以看出,环氧粉末内防腐层与碳钢及耐蚀合金基材均有良好的粘结性,在盐雾试验后附着力也没有明显下降,在加速耐蚀性试验后,防腐层在耐蚀合金基材和碳钢基材上均具有良好的防腐性能。
从上述试验结果可以得知,内防腐体系中的耐蚀合金堆焊层和环氧粉末内防腐层均具有良好的防腐性能,且两者之间的配套性良好。
现场试验
DGR 防腐管于 2016 年 7 月和 2016 年 11 月,分别在长庆油田采油三厂五里湾第一采油作业区的柳 101-252 井组、柳 91-39 井组进行了现场试验,输送压力0.3 ~ 0.5MPa,输送温度为 20~35℃。
1、柳 101-252 井组试验管段
DGR 试验管道尺寸为 φ60×4mm,共 3 根,试验管段长度分别为 1.5m、4m、1.5m。将上述三根 DGR 防腐试验管段对接焊连成一整根试验管,对接焊后试验管段总长度为 7m,其中试验管包含 2 道焊口(焊口距离管端各 1.5m 处),将长度为7m 的 DGR 防腐试验管接入柳 101-252 井组原油管线。
内防腐层:熔结环氧粉末防腐层,厚度 500 ~ 600μm。
外防腐层:熔结环氧粉末防腐层,厚度 300 ~ 400μm。
内补口:耐蚀合金堆焊层,厚度1.5mm,长度 65mm。
外补口 : 矿脂油防腐带+外护带结构。
图8 现场试验照片
2、柳91-39井组试验管段
试验管道尺寸为 φ60×4mm,每根试验管段长度为 1m,一共 20 根。
污水管线:20 根总长度为 20m,分别接入和原油管线各 10m,即每种管线各有焊口 11 处。
内防腐层:熔结环氧粉末防腐层,厚度 500 ~ 600μm。
外防腐层:熔结环氧粉末防腐层,厚度 300 ~ 400μm。
内补口:耐蚀合金堆焊层,厚度1.5mm,长度 65mm。
外补口:矿脂油防腐带 + 外护带结构。
图9 现场试验照片
柳 91-39 井组水样主要化学成分:
总矿化度:29269mg/L
pH 值:7.62
HCO3- 含量:396mg/L
Cl- 含量:12053mg/L
SO42- 含量:6243mg/L
目前试验正在进行中,试验管段运行正常,未出现腐蚀穿孔渗漏现象。
结论
利用 DGR 技术生产防腐管可以实现工厂化预制,质量可检可控,现场直接焊接安装,免除了内补口工序且能实现管内防腐层连续完好,也可以根据介质变化选取不同的耐蚀合金和防腐涂料,能够较好地解决小口径管线的防腐难题。
(本项目的研究与现场试验得到了李广华、魏国两位同志的指导与帮助,也得到了山东胜利长龙管道科技有限公司的支持,在此一并致谢)
参考文献
1、SY/T0029-2012《埋地钢质检查片应用技术规范》
2、SY/T0452-2012《石油天然气金属管道焊接工艺评定》
3、SY/T0442-2010《钢质管道熔结环氧粉末内防腐层技术标准》
4、SY/ T0315-2013《钢质管道熔结环氧粉末外涂层技术规范》
作者简介
韩文礼,生于 1961 年。1982 年毕业于北京钢铁学院,现任中国石油集团工程技术研究院院长助理,防腐保温研究所所长,教授级高工,中国石油集团高级技术专家。主要从事石油行业储罐、管线防腐蚀技术研究开发与应用。
工作三十多年来,先后主持和组织完成了国家、中石油集团公司 20 余项重点课题的研究工作,多项技术成果填补国内和集团公司空白。近年来获得省部级科技进步三等奖以上 5 项、中国腐蚀与防护学会科技进步一等奖 1 项、二等奖 2 项、局级科技进步创新奖 5 项。获得授权发明专利 6 项。主编 SY/T 0320-2010钢质储罐外防腐层技术标准等行业标准 3 项,中石油集团企标 1 项。发表论文多篇。
2015 年被中国工程院环境与轻纺工程学部聘为“我国腐蚀状况及控制战略研究”项目组专家。中国腐蚀与防护学会第九届理事会理事、 中国腐蚀与防护学会防腐蚀施工与技术专业委员会第五届副主任委员、 《石油石化管线与技术》杂志编委、天津市防腐应用技术协会理事、 《石油工程建设》杂志编委、 《管线与技术》杂志编委副主任。
免责声明:本网站所转载的文字、图片与视频资料版权归原创作者所有,如果涉及侵权,请第一时间联系本网删除。
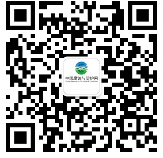
官方微信
《腐蚀与防护网电子期刊》征订启事
- 投稿联系:编辑部
- 电话:010-62316606-806
- 邮箱:fsfhzy666@163.com
- 腐蚀与防护网官方QQ群:140808414