一、前言
油气管道在设计、施工和运营阶段都有可能遭受来自外部环境干扰和内部操作不规范而造成的管道本体缺陷,从而影响管道的安全运营。同时,随着管道业务的不断深入发展,一系列新的问题使管道的完整性管理也面临着挑战[1],研究应对这些问题的技术方法和策略是解决管道本质安全及管道业务发展瓶颈的关键 [2]。对于投产运营以后的油气管道来说,绝大部分都采用埋地敷设的方式,属于隐蔽工程,管道本体的划伤、焊接缺陷、材料缺陷等在运营期很难通过地面检查来识别,而这些缺陷对油气管道安全运营来说都是潜在的隐患,如 2009 年 12 月 30 日,兰郑长成品油管道渭南支线因第三方施工破坏致使管道在试运投产过程中发生柴油泄漏事故,泄漏的柴油由赤水流入渭河,经渭河流入黄河,对黄河造成了严重的油污染;青岛“11.22”爆燃事故更是暴露出管道本体缺陷给生产运行和社会带来的危害。
近年来随着《管道保护法》、《特种 设 备 安 全 法》 等 国 家 法 律 法 规,《油气输送管道完整性管理规范》(GB32167-2015)、《压力管道定期检验规则 - 长输油气管》(TSG D7003-2010)等相关国家、行业标准规范相继出台,以及逐步成熟和推广应用的管道完整性管理,在控制和监控影响管道完整性的各类威胁中取得了显著的效果。同时,随着内检测技术的发展,识别管道本体缺陷已经成为可能 ,如采用机械原理的几何检测器可以识别管道几何变形,包括凹坑、椭圆变形、屈曲等 ;采用漏磁原理的漏磁检测器可以识别管道金属损失,包括划伤、腐蚀、部分制造缺陷等 ;采用超声原理的裂纹检测器可以识别管道存在的裂纹和类裂纹缺陷,包括 HIC、SCC 等;还有很多种特定的缺陷可以通过特殊的检测工具来识别,如针对输气管道环焊缝裂纹开发的电磁超声检测器(EMAT)等。这些内检测技术的发展,进一步提升了管道完整性管理体系发挥的作用,有效保障了油气管道的本体安全,从而为“事故可防,风险可控”提供了技术保障。
本文将以内检测技术为核心,基于风险控制理论 和“树生”事故致因理论的方法 ,考虑到当前管道大数据的现状 ,探讨一种基于内检测技术的油气管道安全保障体系,实现主动的预防管理模式(见图 1)。

图1 被动的应对管理与主动的预防管理示意图
二、国内外管道内检测现状
20 世纪 70 年代由于管道检测技术水平较低,无法准确确定管道的运行状况和腐蚀情况,管道的维护维修都采用被动的方式,为了保障生产的连续性,只好建设复线(如庆铁老线和新线,新大老线和复线等)或采取限压措施来确保管道安全生产,有时甚至提前结束服役年限报废。这样,一方面需要昂贵的费用作为代价,另一方面降低管道的输量,造成管输能力的浪费。而且部分管道即使采取了降压措施,因不能了解管道本体的状况,仍然不能确保管道安全。
随着材料、电子信息及计算机技术的发展,检测器探头小型化、缩小探头间距、提高处理器的采样速率以及超大容量存储器的工业应用等得以实现,使得对油气管道无损探伤的精度和置信度也越来越高。同时,在 1999 年华盛顿州 Bellingham 汽油管道爆炸事故、2000年新墨西哥州 Carlsbad 天然气管道爆炸事故等众多油气管道事故的推动下,各个国家完善了管道完整性管理相关的立法和标准规范要求,这些都促进了基于内检测的完整性管理技术和安全保障技术的全面、快速发展,利用超声、漏磁、机械振动、陀螺仪、涡流等原理的管道内检测技术也从无到有,从低精度到高精度,从理论试验研究走向了工业应用,并建立了众多内检测服务公司。
同时,当前基于光学原理的无损检测技术在对管道内表面腐蚀、斑点、裂纹等进行快速定位与测量过程中,具有较高的检测精度且易于实现自动化。相比其他检测方法,该方法在实际应用当中有很大的优势,其中在管道内检测中采用较为普遍的光学检测技术包括 CCTV 摄像技术、工业内窥镜检测技术和激光反射测量技术。
目前,比较有影响力的国际内检测服务公司主要有德国的 Rosen、美国GE PII、BakerHuges、T.D.Williamson、荷兰 PipeSurvey 以及国内的中油管道检测技术有限责任公司等,还有一些新兴的检测公司,如英国的天祥集团、NDTGlobal、Penspen 等,这些公司在不同方面有着各自的独特优势,如 Rosen 在新技术研发方便具有独特的优势,其可以包括设备零件在内的整装设备生产,对于新技术的应用反应速度快,能够及时完成设备的更新换代;GE PII 则形成了比较成熟的技术体系和服务系统,在现场服务、数据分析等方面的优势比较显著,且逐步形成了全球内检测服务网络。在全球内检测市场份额方面,德国的 Rosen 和美国 GE PII 这两家检测服务公司平分了超过 60% 的内检测市场,其次为 BakerHuges、T.D.Williamson 等近 100家内检测公司占据剩余的 40% 的内检测市场。
三、基于数据对齐的风险管理
随 着 管 道 发 展 到 大 数 据 时 代、信息技术的发展和数据管理系统的完善,在实现管道本体属性数据、生命周期运营管理数据、以及周边环境数据对齐并纳入数据库的条件下,形成了管道大数据。所谓管道大数据就是:
以管道内检测数据为基线,实现将内检测信息、外检测数据、设计施工资料数据、历史运维数据、管道环境数据和日常管理数据等的校准、对齐整合,使各类数据均可对应各环焊缝信息,形成统一的数据库或数据表 。从管道大数据的定义可知,管道大数据的核心在于整合管道相关的各类基础数据,其价值在于从大数据中挖掘潜在的安全隐患和提供制定维护维修决策的依据,而实现管道大数据价值的技术基础在于数据对齐。
对于分散、杂乱无章的数据,再多也不能称之为大数据,因为随着数据量的增大,如果不能实现这些数据的价值,那么不仅仅会增加数据管理和维护的成本,而且还会掩盖有价值的数据信息,从而成为管理的负担。
管道内检测是对管道的一次全面的体检,也是管道大数据得以实现其价值,完成数据对齐的关键。管道内检测除了识别管道本体缺陷外,还能识别管道的各类特征,如三通、阀门、环焊缝、套管等。其中,根据内检测报告的焊缝编号与建设施工期的焊接记录中的焊口编号对齐,可以实现内检测数据与建设施工期的数据整合;通过内检测地面定标点和识别的各类典型特征,可以实现内检测数据与外检测数据、日常管理数据、以及其他历史资料数据(如换管、修复等)的对齐。从而实现以内检测数据为核心,将施工焊接记录、管材信息、外检测、地面特征等对齐起来,从而发挥两个方面的作用,一是将大数据进行了有效的整合,更加有效地实现大数据的价值;另一方面是通过数据对齐可以识别一些潜在的危险,如施工记录中缺失的焊口记录、短管的记录、连头口的记录等。
通过数据对齐技术,以内检测环焊缝号为基准,识别建设期和运营期不合规的特征(如某些管道存在的斜接弯头、预载的打孔盗油阀门、凹坑、划伤等)及其位置,建立风险管理台账,从风险专家评估风险转变为数据分析人员分析风险,关注数据相关性,识别潜在的风险 。这种模式可以减少人为的主观性,基于风险的理念合理配置资源,同时也有利于保障管理的连续性,减小政策变化或变更管理给管道运营安全带来的影响。通过这种模式,实现管道大数据的管理和从大数据中挖掘潜在的风险也是构建管道安全保障体系的重要工作。
四、内检测在油气管道生命周期内的作用
管道内检测在管道安全生产全生命周期内都发挥着重要的作用,其中包括:
1.新建管道质量控制
由于长输油气管道基本都是采用埋地的方式敷设,建设施工完成后就成为隐蔽工程,以前对于管道验收都是验收相关的资料、地面标识、路权等资料信息,缺乏对于管道本体完整性情况的验收,质量控制非常困难,以致在新建管道投产初期往往因为面临各类完整性威胁导致事故频发,呈现“浴盆曲线”的初期事故多发期。
通过打压试验,发现了很多缺陷,但是打压对于处于临界状态的缺陷暴露不出来,同时会促使一些处于临界状态下的缺陷的扩展(见图 2),因此为了更好地控制管道建设施工质量,管道内检测是一种非常有效的质量控制手段,在新建管道投产初期就应当开展基线检测,对于基线检测发现的缺陷,分析其原因,并作为新建管道质量控制的一部分 。

图2 某新投产管道内检测发现的针孔缺陷已经开始渗油(左),采用补丁修复(右)
2.运行期的安全保障
通过周期性的管道内检测,可以在管道本体缺陷导致管道失效前,识别该缺陷尤其在管道内腐蚀比较集中的管道上,这种方式可以准确预测腐蚀速率,从而实施精准的维护维修策略 [19],避免泄漏事故的发生。同时,通过这种方式还可以延长管道的寿命 [20],这也是为什么管道运营商和政府监管部门非常重视管道内检测的原因 [1]。近几年针对老管道开展的内检测工作,及时发现了管道本体的缺陷,进行针对性的修复,避免了大量泄漏事故(见图 3),如马惠线管道内检测报告 70% 以上的缺陷上百处,10% 以上的缺陷几万处,部分70% 以上的缺陷,在修复过程中剥开防腐层后,发现针孔微渗漏,这些缺陷的及时识别与治理,有效确保了管道的安全运营。

图3 历年基于内检测结果进行的管道修复中发现的典型管道腐蚀情况
由于打孔盗油形式呈现多样化,且技术越来越成熟,反侦察能力也急速的提升,往往通过地面巡护、监管等很难100% 防控住打孔盗油,尤其对于一些预埋的盗油阀,采用地道、滴取等方式偷油,现有的防护手段很难排查,管道内检测也成为解决这种难题的有效方法之一,如山东地区某原油管道内检测及时识别了一些极其隐蔽(见图 4)或者打完孔后未曾盗油的阀门 20 余处。

图4 打孔盗油漏磁信号(左)和开挖的打孔盗油阀门(右)
3.管道判废的依据
庆铁新线和老线通过管道内检测发现管道本体存在大量的螺旋焊缝和环焊缝缺陷,在庆铁三线和四线投产前,根据工程适用性评价结果,开展了大量的修复工作,有效降低了泄漏事故率。
同时,基于内检测结果,综合考虑管道物理寿命和经济寿命 ,为庆铁新线和老线的废弃、庆铁三线和四线的规划建设提供了依据,根据类比也为不可内检测管道(见图 5),如任京线,也提供了判废的依据。

图5 因屈曲、弯头曲率半径太小和结蜡太厚等原因不具备内检测条件示意图
五、安全保障体系的构建
当前,保障油气管道的安全技术较多,如泄漏监测技术、安全预警技术、视频监控技术、应变监测技术、高后果区识别技术等,分别从降低失效风险、控制失效后果等多个方面着手构建了相应的安全保障技术体系。尽管这些技术在一定程度上对于保障管道安全运营发挥了积极的作用,但是基本都处于事中和事后处置或维护的阶段,尚未提升到预知维护和风险预控的阶段。管道内检测技术是一种识别管道本体缺陷为主,兼可监测管道状态(如中心线检测(IMU)可监测管道的应力变化情况)的技术,可以有效实现油气管道预知维护和风险预控。
综合上述内容,油气管道安全保障体系就是以管道内检测为中心,以内检测报告的焊缝编号和坐标信息为基准,将所有相关的基础数据实现数据对齐,基于这些数据的统计分析来指导预知性的维护维修、应急管理和风险管理,从而保障油气管道的安全运营。该体系的构架如图 6 所示。

图6 基于内检测的油气管道安全保障体系示意图
其中,基于内检测构建的安全保障体系主要有以下几个方面的优点:
1.提高管理者的认知,梳理管理的重点
基于内检测的油气管道安全保障体系可以让管理者明白管道存在什么问题、哪些区域不能发生泄漏、如何预防泄漏的发生、发生泄漏后可能造成多大的影响、以及发生泄漏后如何应对等。其中,安全保障体系的关键在于解决如何维护维修和应急,投入多少、投入什么、以及投在什么地方能发挥有限资源的最大价值方面的问题。
基于内检测的油气管道安全保障体系虽然基本实现预知的维护维修 ,但由于认知、技术发展等方面的局限性,不等于不需要应急,而是提高应急的针对性和降低应急的成本。
2.实现应急保障目标化,优化应急物资储备
通过内检测可以清晰了解管道本体的状况,预测管道发生泄漏的可能性有多大、发生泄漏后的泄漏量有多大、发生泄漏后的影响范围有多大、需要采取什么样的应急技术(如焊接套筒、换管或者封堵)等,从而可以有效地识别在应急过程中可能遇到的风险,制定针对性的应急策略,如针对腐蚀缺陷,在应急方面考虑渗漏、小泄漏的维抢修措施,应急物资储备方面只需要考虑管道卡具、套筒等的维抢修物资;针对焊缝缺陷,在应急方面就需要考虑破裂的维抢修措施,应急物资储备方面也需要考虑不停输封堵、换管等维抢修措施和储备管子、封堵头等维抢修物资。
同时,结合数据对齐的成果,还可以帮助管理者识别应急的重点部位,对高后果区管段中存在的缺陷修复优先,并在修复之前作为应急的重点监控对象。
3.促进技术发展,保障安全运营
根据数据对齐识别的建设期预留的潜在风险和运营期内检测识别的管道本体缺陷,可以预测近期和远期管道可能发生失效的类型和趋势,并预测可能发生失效的区域。对于这些预测的失效类型可以开展针对性的技术研究,从而完善安全保障的技术体系,如当前需求的高强钢在役焊接、非开孔封堵的换管技术、凹坑缺陷的修复技术等方面的研究。
同时,内检测技术也存在一定的局限性,如输油气管道焊缝裂纹、针孔腐蚀等缺陷检测技术还有待进一步的研究。
六、总结与展望
在油气管道运行全寿命周期过程中,管道内检测能有效识别管道在运行过程中影响管道本体运行安全的威胁 [21],从而针对这些威胁,采取有针对性的运行管理和维护措施,将有限的资源投入到最需要关注的管段上,明晰管理的重点方向,达到预防式管理的目的,确保管道安全运行,降低运行与维护成本。同时,基于当前内检测技术存在的局限性,如焊缝缺陷、裂纹、针孔类缺陷等在检出率和识别率等检测指标方面还不能达到预定的目标,因此,在构建油气管道安全保障体系时还需要着手开展电磁超声内检测技术、电磁涡流内检测技术、超声裂纹内检测技术等方面的研究工作,提高对于裂纹、焊接缺陷、针孔缺陷等识别能力,并完善数据对齐技术,提高大数据的应用价值,使其能够更好地揭示风险。
作者简介

戴联双,1983 年,高级工程师,现在中国石油管道公司从事管道完整性管理、管道风险评价及管道内检测等相关工作。
免责声明:本网站所转载的文字、图片与视频资料版权归原创作者所有,如果涉及侵权,请第一时间联系本网删除。
相关文章
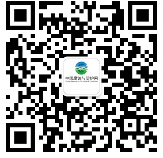
官方微信
《腐蚀与防护网电子期刊》征订启事
- 投稿联系:编辑部
- 电话:010-62316606-806
- 邮箱:fsfhzy666@163.com
- 腐蚀与防护网官方QQ群:140808414
点击排行
PPT新闻
“海洋金属”——钛合金在舰船的
点击数:8135
腐蚀与“海上丝绸之路”
点击数:6475