高温合金作为高端设备的主要材料,其产品成分和内部损伤会对设备的使用产生至关主要的影响。目前,国内对高温合金的工艺和原料研究比较多,对检测的研究报道比较少。虽然化学成分分析和无损检测取得了一定的成绩,但是还需要投入更多的时间和精力。
高温合金的化学成分检测
众所周知,航空发动机、超临界燃气机组等高端装备中使用的高温合金化学成分异常复杂,除了基体和主要合金元素外,还存在有意添加、原材料中带入以及冶炼中混杂的各种微量元素,一个牌号的高温合金甚至可以含有 20 多种元素,其典型合金元素的作用如表 1。
事实上,高温合金中各成分含量变化能直接影响材料的各项性能,甚至某些关键微量元素含量的细微变化,将会对材料性能产生非常大的影响,因此需要对此进行有效的利用或严格的控制。这不仅给材料冶炼提出了很高的要求,同时对成分分析技术和分析方法也是严峻的挑战。因此,采用先进的化学成分分析技术或分析方法标准准确测定合金化学成分及夹杂物含量对于改善高温合金的制备冶炼工艺、净化制备过程中混入的夹杂物、提高材料的力学性能及结构材料部件使用寿命,具有重要意义。
高温合金化学成分分析方法主要包括经典化学法和仪器分析法。经典化学法包括容量法(滴定法)、重量法、光度法和电化学分析法,是高温合金化学成分分析技术中使用最早、选择性好,灵敏度和理论准确度较高、且具有中国特色的分析技术。但是随着科学技术的进步、材料研制进程的加快及人们环保意识的提高,使得化学分析方法在使用过程中的缺点逐渐暴露出来,如实验分析步骤较为繁琐、试验周期长、易玷污和损失、污染环境等,无法满足高温合金化学成分快速的分析要求。
为了满足材料研制过程中对检测进度及化学成分控制的严格要求,一些新的测定高温合金化学成分的仪器分析技术应运而生,分析方法呈现多样性,分析方法的灵敏度与选择性也越来越高。高温合金化学成分测定用仪器分析法包括吸收光谱法、发射光谱法、质谱法和红外 / 热导法。
吸收光谱法主要包括石墨炉原子吸收光谱法(GF-AAS)、火焰原子吸收光谱法(FAAS)、电热原子吸收光谱法(ET-AAS)、氢化物发生—原子吸收光谱法(HG-AAS)及流动注射(FI)—原子吸收光谱法等,具有高选择性、高度自动化和智能化、干扰少等特点,目前已广泛用于金属材料中微量、痕量元素的分析中。
发射光谱法主要包括空心阴极原子发射光谱法、电感耦合等离子体原子发射光谱法(ICPAES)、氢化物发生—原子荧光光谱法(HGAFS),X 射线荧光光谱法和火花源光电直读光谱法,因其测定灵敏度高,有较宽的线性动态范围,良好的精密度和重复性,可实现多元素同时分析等特点,非常适合于高温合金中化学成分的分析。
质谱法中最常使用的是电感耦合等离子体质谱法(ICP-MS)和辉光放电质谱法(GDMS),由于其具有谱图简单、灵敏度高、选择性好、检出限低、线性动态范围宽、可多元素同时快速分析等特点,同时可与同位素比例和同位素稀释法、多种分离技术及进样方式相结合,非常适合高温合金复杂体系的超痕量元素分析中,但此方面的研究主要集中在国外,在我国则开展的相对较少。红外吸收光谱法在镍基合金分析中的应用主要是碳和硫的分析测定,测定操作简单,易于掌握,确保结果的快速、准确。
综上所述,高温合金中化学成分的分析方法正在逐渐从经典化学分析法及单一的元素分析不断向仪器分析法及多元素同时分析的方向发展,从而将高温合金中化学元素的分析推进到更新更高的水平。
高温合金的无损检测
作为高端装备的关键部件,高温合金的应用从原材料、坯料到成品的各个阶段,均需要进行无损检测,由于超声检测具有方便、安全、快捷和可靠性的特点,超声检测在高温合金领域得到了广泛使用。高温合金的无损检测在高端设备检测上占有重要的地位,无损检测贯穿着结构件制备的全工程,从原材料到制造过程再到在役检测。常用的无损检测方法有超声检测和荧光检测两种。下面将以涡轮盘为例介绍粉末高温合金的无损检测方法。
粉末高温合金特点为晶粒细小、组织均匀、无宏观偏析、合金化程度高、屈服强度高、疲劳性好是制造高推比新型发动机涡轮盘、篦齿盘最佳材料,我国某型号发动机就用到了粉末材料。涡轮盘是飞机发动机的关键件,在高温工作环境下承受更高的载荷,工作条件十分苛刻,同时粉末盘的特点是导致疲劳断裂的临界缺陷尺寸微小,也就是说微小缺陷也将严重影响零件的使用性能,甚至造成灾难性的后果。因此采用新建的无损检测技术尤为的重要。
粉末高温合金中的缺陷有三种,原始颗粒边界、热诱导孔洞和非金属夹杂物,其中原始颗粒边界和热诱导孔洞可通过改进工艺得到解决,但夹杂物通过现有的粉末制造和处理工艺不能完全消除,因此需要采用无损检测方法进行控制,即要求无损检测技术将验收标准规定的缺陷可靠地检测出来。验收标准是建立在损伤容限理论基础上,损伤容限理论认为任何结构都存在缺陷,只要这些缺陷不超过某一容许尺寸,结构就是安全的。
超声检测
超声检测是无损检测的常规方法之一,具有穿透能力强,灵敏度和分辨率高是利用超声波穿透材料时的变化检测、可定位和定量检测等优点。
超声检测方法按照原理分主要有:脉冲反射法、衍射时差法、穿透法和共振法等,应用最广泛的是脉冲反射法。脉冲发射法通过探头产生脉冲到工件,根据来自工件的反射波情况来检测缺陷。
超声波探伤仪是超声检测的主要设备,通过发射电路产生高压电脉冲,激励晶片产生振动,藕合到工件中产生发射超声波动,接收来自工件的反射波,经过放大、检波等处理后进行显示。显示方式有 A,B,C,D 等,A 型显示是一种波形显示,横坐标一般代表的是声波的传播时间 ( 或距离 ),纵坐标代表反射波的幅度。根据波形的形状来确定材料中是否有缺陷,缺陷的大小及形状。B, C,D 显示都是表示的某一截面的灰度图。
对待检工件进行扫查时,如工件内有界面或者存在缺陷时,在始波和底波之间便会存在界面波或者缺陷波,如图就是对巴氏合金的 A 扫波形图,在始波和底波之间的就是复合层界面波。
粉末零件缺陷特点是尺寸小。为了检测粉末零件中的微小缺陷,关键是提高小缺陷超声反射信号幅度和信噪比。如何实现既能提高小缺陷反射幅度,同时又能提高信噪比?采用水浸聚焦探头、高的检测频率是途径之一。这是因为聚焦声束在焦区能量高度集中,声压明显提高,因而小缺陷反射幅度高;声束穿过的基体材料体积较小,相应引起的散射噪声也较小,使得信噪比较好。但不同聚焦探头参数不同,为了保证零件全厚度范围的检测灵敏度,超声检测工艺参数的制订至关重要。
传统高温合金超声波检测采用的是单个水浸聚焦探头,将探头焦点落在零件表面或某一深度区域,而粉末盘的超声检测采用的是多个探头分区检测,即使每一个探头焦柱区落在零件的不同深度,这样零件全厚度范围超声检测均具有较高的检测灵敏度。
荧光检测
低周疲劳试验数据表明,粉末零件裂纹起始于表面缺陷的约占 25%,起始于近表面缺陷的约占30%,其余起始于内部,但近表面缺陷的危害更大。
荧光检测是检测零件的表面开口缺陷,针对粉末零件产生的缺陷小的特点,荧光检测的关键是确定发现微小缺陷的工艺参数。
荧光渗透液:
1:水洗型荧光渗透液1)成份:
溶剂:油基溶剂溶质:油溶性荧光染料2)灵敏度低灵敏度:适用于表面粗糙零件,用于轻合金铸件中灵敏度:较难从粗糙表面去除,适用于精密铸钢件、焊接件、精密铸铝件、轻合金铸件及机加工表面高灵敏度:难于从粗糙表面上去除,适用于良好加工面,用于精密铸造涡轮叶片等关键工件2: 后乳化型荧光渗透液1)成份:
溶剂:油基溶剂溶质:油溶性荧光染料添加:互溶剂、润湿剂等2)灵敏度标准灵敏度:适用于变形材料机加工件高灵敏度:适用于要求较高的变形材料机加工件 超高灵敏度:适用于特殊构件,如航空涡轮盘3)分类:亲水性、亲油性3:溶剂去除型荧光渗透液1)成份:与后乳化型荧光渗透液的成份基本相同2)灵敏度等级:低、中、高、超高灵敏度。
超高灵敏度后乳化荧光渗透方法对小缺陷具有最高的检测灵敏度,因此荧光检测方案确定采用超高灵敏度后乳化荧光渗透工艺。
要保证粉末盘中 0.2mm 的缺陷采用荧光方法能够可靠地检测出来,后乳化荧光渗透液的选择及工艺参数至关重要。具体选用的荧光渗透剂需要根据结构件的具体材质和损伤情况而定。
依据选择的荧光渗透剂的类型,选择合适的显像方法,依据渗透探伤的标准进行探伤测试,然后依据荧光检测的显示,采用 20 倍的双目放大镜进行观察。
虽然高温合金的无损检测很重要,但是关于高温合金的无损检测研究报道非常少,关于高温合金的研究大多集中在制造工艺阶段和原材料的研究,无损检测相对滞后。虽然,超声检测和荧光检测也取得了一定的结果,但是由于种种原因,检测步骤繁琐,和检测准确度相对不高,无损检测仍需要研究。
我们还需要投入更多的时间和精力在高温合金的检测方面。
免责声明:本网站所转载的文字、图片与视频资料版权归原创作者所有,如果涉及侵权,请第一时间联系本网删除。
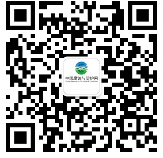
官方微信
《腐蚀与防护网电子期刊》征订启事
- 投稿联系:编辑部
- 电话:010-62316606-806
- 邮箱:fsfhzy666@163.com
- 腐蚀与防护网官方QQ群:140808414