李季,李博文,赵林,郑丽群,韩恩厚
中国科学院金属研究所环境腐蚀中心,沈阳,中国,110016
E-mail:liji09@imr.ac.cn
个人简介
李季,女,四川汉源人,2009年6月毕业于东南大学材料科学与工程学院,获得工学学士学位,现为中国科学院金属研究所在读博士研究生。硕士阶段导师为郑丽群研究员和韩恩厚研究员,研究方向为金属局部腐蚀机理及电化学噪声技术。
局部腐蚀是金属失效的主要方式之一,由于其具有隐蔽性、自发性、破坏性等特点,不仅给工业生产埋下巨大的安全隐患,而且往往造成巨大的经济损失、资源浪费和人员伤亡。因此对生产设备进行实时监控,了解各关键部位的腐蚀状况对于工业生产具有重大意义。电化学噪声技术是目前大家公认的极有潜力应用于局部腐蚀现场监测的手段之一,近年来获得了快速发展。但由于现场情况复杂多变,与实验室相差甚远,目前的应用情况并不乐观,尚有很多问题没有解决。
秉承课题组寓研于用的原则,本课题着眼于目前亟待解决的局部腐蚀在线监测问题,尝试将电化学噪声技术有效应用于复杂的工业生产现场。通过对电化学噪声的实验数据和参数进行合理解析,设法与其它电化学方法进行整合,并在实验理论的基础上对实验仪器进行改进,实现对局部腐蚀的在线监检测,并从软件和硬件两方面提供支持。我们相信,这将极大地推动电化学噪声技术从实验室走向现场应用的进程。
李季
摘要:使用电化学噪声技术研究了N80钢经0. 5mol/L的NaHCO3溶液钝化处理后在0.5mol/LNaCl溶液中的局部腐蚀过程。经过图谱分析发现,在钝化阶段,电流由大变小,电位由小变大,两者最终趋于稳定。噪声电阻Rn在这一过程中不断增大,但增速逐渐放缓。Cl- 加入初期,电位电流峰数量和密度均处于较高水平,电位峰寿命明显大于电流峰;随着点蚀由亚稳态点蚀向稳态点蚀发展,电流峰的寿命逐渐增加,最终达到与电位峰相当的水平。噪声电阻的变化可以明显地分为三个阶段,分别对应于亚稳态点蚀期,稳态点蚀期和稳态点蚀后期。电流噪声和电位噪声标准偏差的散点图亦能明显观察出这个过程,在稳态点蚀后期N80钢出现了均匀腐蚀。
关键词:N80钢,局部腐蚀,电化学噪声,噪声电阻,标准偏差
1 引言
N80钢具有高强度、高韧性的特点,广泛应用于油田的油管、管套等。由于油管常处于CO2、H2S、Cl-等交互作用的环境中,极易导致N80钢发生局部腐蚀。由于腐蚀多发于井下生产作业处,很难及时发现并处理,最终造成穿孔、破裂等严重后果,因此对管道局部腐蚀状况的在线监测显得尤为重要。
电化学噪声(Electrochemical Noise,EN)[1],[2]技术经过三十多年的发展,已经基本被大家认可为一种能有效监测局部腐蚀的手段[3],[4],[5]。对于表面有钝化膜覆盖的金属而言,发生局部腐蚀时,电化学噪声图谱所捕获的信号主要来源于表面钝化膜的破裂和修复过程[6]。N80钢经NaHCO3溶液钝化后,可在表面形成一层FeCO3保护层,由于FeCO3膜呈双层结构,且内层薄而致密,外层疏松,极易出现表面不均匀或局部破损,导致点蚀等局部腐蚀发生[7]。
本文使用电化学噪声技术,研究了N80钢经0.5mol/L的NaHCO3溶液钝化后在0.5mol/L的NaCl溶液中发生局部腐蚀时的腐蚀行为,并尝试通过谱图分析、时域分析等电化学噪声分析技术对它们的点蚀机理做出诠释。
2 实验方法
实验材料为N80油田管线钢板材,其化学成分如表1所示:
表1:N80钢的化学成分(质量分数%)
C | Si | Mn | S | P | Cr | Ni | Fe | |
N80 | 0.24 | 0.22 | 1.19 | 0.004 | 0.013 | 0.036 | 0.028 | Bal. |
将N80钢板材加工成10mm×10mm×3mm的方形试样,在非工作表面上焊接铜导线,并用环氧树脂密封。用水砂纸从300#至1200#逐级打磨并抛光,然后用去离子水、丙酮、酒精逐一擦洗,直至表面干净光亮,最后放入干燥器中备用。
电化学噪声的测试由PARSTAT2273电化学工作站的电化学噪声模块(ZRA)来完成。在开路电位下测量两个相同的工作电极之间的电流噪声,以及工作电极1与参比电极之间的电位噪声。采用三电极体系,其中两个工作电极为面积相同的N80试样,参比电极为饱和甘汞电极(SCE)。整个电化学实验装置至于法拉第笼中进行电磁屏蔽。
本文根据N80钢的性质和特点,采用了0.5mol/L NaHCO3为钝化介质,钝化时间为5小时;0.5mol/L NaCl为腐蚀介质,腐蚀时间为160小时。配置所需的NaCl、NaHCO3等试剂均为分析纯,溶液用去离子水配置。电化学噪声的测试在工作电极浸到溶液的同时立即开始。所有的电化学实验均在15±2°C温度下进行。
3 实验结果及讨论
3.1 谱图分析
3.1.1 钝化过程
N80钢为低碳钢,其表面无法在空气中自动形成钝化膜,在点蚀实验开始前需要先用0.5mol/L的NaHCO3进行钝化,待其表面形成稳定的保护膜。其钝化过程可以用下面(1)~(3)式表示[8],[9]。
Fe+OH--2e->FeOH+ (1)
FeOH+ +OH- <->Fe(OH)2 (2)
FeOH+ +HCO3-->FeCO3+H2O (3)
经过5小时的钝化,N80试样表面即可形成一层相对均匀致密的FeCO3膜,充当保护作用。钝化过程的电化学噪声图谱如图1所示。
从图1可以看出, N80钢侵入NaHCO3溶液后电位即开始持续上升,电流不断下降。此时由于N80钢表面发生着钝化膜的形成过程,电荷转移较为频繁,电流噪声峰数量略高,但峰值较小,最大仅为几个纳安。经过4小时以后,两者均趋于稳定,电位强度逐渐维持在约-0.16V左右,表明试样表面的钝化膜已逐渐形成。
图1. N80钢在0.5mol/L NaHCO3溶液中做钝化处理的电化学噪声特征图谱#p#副标题#e#
3.1.2 点蚀过程
随着N80钢的电位噪声逐渐趋于稳定,表面的钝化过程基本趋于结束。在盛有NaHCO3溶液中加入4mol/L的NaCl,使Cl-离子浓度保持在0.5mol/L。
图2. N80钢处于亚稳态点蚀期的电化学噪声图谱
从图2中可以发现:对于N80钢,在加入NaCl溶液后,随即出现电流和电位噪声的漂移,该过程可能与N80表面的FeCO3膜部分溶解相关。经过约500s后图谱开始出现电流和电位的成对暂态峰,但是峰的数量和强度均维持在较小的范围内。电位值在-0.16~-0.30之间变化,电位峰呈现出快速下降,缓慢恢复的特点,恢复过程呈指数增长,最强的峰大约有90mv,持续时间最大可达100s以上。而电流峰寿命明显短于电位峰,仅为几秒到几十秒,强度约几百纳安。由于N80钢表面的FeCO3膜极易受到Cl-的侵蚀发生局部破裂,诱发以点蚀为主的局部腐蚀。在本实验中,NaCl溶液与N80钢接触约500s后即告别钝化态,表现出亚稳态点蚀的特征,但由于溶液中同时存在的HCO3- 离子起到了再钝化的作用,因此试样表面进行着激烈的点蚀与再钝化的竞争过程,属于亚稳态点蚀阶段。
随着浸泡时间达到约50h,电位和电流噪声峰的强度逐渐增强,电流峰寿命也明显增加,最大值达到接近200s,如图3所示。此时的电流和电位噪声峰持续时间相当,处于稳态点蚀阶段。
图3. N80钢处于稳态点蚀期的电化学噪声图谱
在图谱上,除了有明显的暂态峰外,还存在着大量的高频小幅波动。图3中的小图为400s-800s的局部特征图,通过局部分析这些小幅波动的峰可以发现,它们均呈现出快速上升,缓慢恢复的特点,噪声峰寿命、强度长短不等。因此可以判断,虽然在电极的某些部位已经发生点蚀,但在电极表面还存在着大量的点蚀与再钝化的竞争过程。
当浸泡时间到100小时左右时,幅值较大的电流和电位暂态峰的数量逐渐减少,但此时电流噪声暂态峰的寿命明显增长,在没有暂态峰出现的其它位置表现出更明显的高频小幅波动,如图4所示。
图4. N80钢处于稳态点蚀后期的电化学噪声图谱
在浸泡的最后阶段,电位噪声大幅随机漂移,没有暂态峰,如图5所示,表现出均匀腐蚀的特征。但在局部出现了脉冲波动,对2400s-2800s时间段局部脉冲波放大的分析如图5中小图所示。曹楚南等人早期的电化学噪声研究中也观察到类似的脉冲噪声电压谱[6],其特点为多段间歇性密波。他们认为这种类型的噪声波是电极表面特性不稳定的一个信号,很有可能发生局部腐蚀。
图5. N80钢处于稳态点蚀后期的电化学噪声图谱
3.2 时域统计分析
3.2.1 噪声电阻Rn
噪声电阻(Noise Resistance,Rn)的定义为电位噪声和电流噪声的标准偏差之商,是目前广泛采用的表征局部腐蚀的一个重要参数。前人已经从理论上证明在某些情形下可以将噪声电阻与极化电阻等价。因此,在钝化阶段,噪声电阻的变化可以反映出N80钢表面钝化膜的生长过程[10],[11],而在整个点蚀过程中,均可用1/Rn近似表达局部腐蚀速率[11]。
对图1中的数据作统计分析发现,钝化前期,N80钢表面的噪声电阻持续增加,且在初始阶段,噪声电阻的增加速度较快,但是随着钝化时间延长,增长速度有所减缓,如图6所示。这一变化过程表明:经钝化处理后,N80钢表面已经形成了一层较为致密的钝化膜。
图6. N80钢钝化处理初期阶段的噪声电阻变化曲线#p#副标题#e#
在点蚀过程中,点蚀实验的时间约为160小时,按每2小时取一组数据进行统计分析,统计结果以散点图的形式如图7所示。统计结果表明,在点蚀实验开始2小时后所测得的噪声电阻就已明显小于钝态期(见图8),这一结果与噪声图谱上N80钢在接触Cl- 溶液约500s之后迅速出现暂态峰的特点相一致。可见,FeCO3膜的耐蚀性较差,容易受到侵蚀性离子的侵蚀发生阳极溶解。在整个监测过程中噪声电阻逐渐递减,按照图谱分析中各阶段的起止时间,可以将其分为3个阶段,见表2。
图7. N80钢在浸泡160小时过程中的噪声电阻变化曲线
表2:N80钢噪声电阻的3个阶段
阶段编号 | 阶段名称 | 噪声电阻范围 | 时间范围 |
第一阶段 | 亚稳态点蚀期 | >10000Ω | 0~50小时 |
第二阶段 | 稳态点蚀期 | 10000Ω~5000Ω | 50~100小时 |
第三阶段 | 稳态点蚀后期 | <5000Ω | >100小时 |
从噪声电阻的变化可以较为直观地看出,N80钢在含Cl- 溶液中的耐蚀性随着浸泡时间的增长而变差。在第一阶段,钢表面的状态较为复杂,噪声电阻变化的幅度比较大,此时为点蚀和再钝化的竞争阶段。随着浸泡时间增长,Cl- 在N80钢表面的吸附越来越多,使得点蚀倾向逐渐变大。第二、第三阶段噪声电阻均保持在一定区间内稳定变化,腐蚀速率1/Rn逐渐变大。
3.2.2 电流标准偏差Si和电位标准偏差Sv
电流标准偏差(Standard Deviation of Current,Si)和电位标准偏差(Standard Deviation of Potential, Sv)[12]是噪声分析钟爱的参数。研究表明:电流噪声的标准偏差越大,发生局部腐蚀的可能性越大,而电位噪声则刚好呈现出相反的规则[13]。但是在实验中,仅用一个参数并不能客观地对电极的腐蚀状态进行描述,如图8、9所示。
图8. N80钢在0.5mol/L NaCl溶液中浸泡期间电位标准偏差的变化情况
图9. N80钢在0.5mol/L NaCl溶液中浸泡期间电流标准偏差的变化情况
标准偏差数值很小,且初始状态与结束状态差别约为3个数量级,在统计图中大量数据点均集中在0附近,不利于分析。H.A.A. Al-Mazeedi和R.A. Cottis[14]等人尝试了一种新的分析方法,以数量级为单位长度同时用Si和Sv作统计分析,此时两个参数的变化表现出一定的规律性,更有利于数据分析。
图10. N80钢在0.5mol/L NaCl溶液中浸泡期间电位和电流标准偏差的变化情况#p#副标题#e#
如图10所示,上图给出了电位偏差和电流偏差的分布情况。从图中可以发现,本实验的电流噪声分布在8.49E-09~9.1E-06的范围内,电位噪声分布在6.42E-05~0. 015的范围内,该区间具有典型的局部腐蚀和均匀腐蚀的特征。
图11和12用三维模式给出了本实验中电流噪声和电位噪声的标准偏差随时间的变化情况。根据H.A.A. Al-Mazeedi和R.A. Cottis等人对电位偏差和电流偏差的大小与腐蚀过程对应关系的总结[14],图11、12的散点分布图可以提供N80钢表面腐蚀状态的变化过程。
在实验开始初期,电位标准偏差的数量级主要集中在-5左右,而电流噪声则在-9左右,均处于较低水平,表明此时的电流和电位波动均较小,工作电极表面实际上是处于钝化态。随着实验进行,电流噪声标准偏差的数量级逐渐向-8,-7转移电位噪声先向-3,-4处集中,该过程表明电极表面的活性增加,点蚀倾向明显增大,表现出明显的局部腐蚀。反应末期,数量级分别达到-8和-5,此时为均匀腐蚀。
图11. N80钢在0.5mol/L NaCl溶液中浸泡期间电位和电流标准偏差变化情况的三维图
图12. N80钢在0.5mol/L NaCl溶液中浸泡期间电位和电流标准偏差变化情况的三维图
结论:
1、N80钢的钝化过程是其表面FeCO3膜的生长过程,在这一过程中,电位、电流持续增加后逐渐回落并保持稳定。钝化过程使得碳钢的耐蚀性增加,表现为Rn持续增加,且增速从快逐渐变慢。
2、噪声图谱上噪声峰寿命是判断点蚀发展过程的一个重要指标,在点蚀初期,电流噪声峰明显短于电位噪声峰;进入稳态点蚀后,两者基本相当;而在稳态点蚀后期,几乎没有噪声峰。
3、对Rn进行大量统计分析可以较为直观地反映点蚀过程中腐蚀速率的变化,Rn的三个阶段分别为亚稳态点蚀,稳态点蚀和均匀腐蚀。
4、电流噪声标准偏差和电位噪声标准偏差的散点图可以判断点蚀所处阶段,时间轴上的三维统计图能直观地反映出点蚀的发展阶段,对于现场监测具有较大的指导意义。
References(参考文献)
[1] Bertocci U, Huet F. Noise analysis applied to electrochemical system [J]. Corrosion, 1995, 51(2):131-144
[2] Iverson W P. Transient voltage changes produced in corroding metals and alloys [J]. J.Electrochem.Soc., 1968,115:617-618
[3] Hladky K, Dawson J L. The measurement of localized corrosion using electrochemical noise [J]. Corrosion Science, 1981, 21: 317-322
[4] Cheng Y F, Wilmott M, Luo J L. Analysis of the role of electrode capacitance on the initiation of pits for A516 carbon steel by electrochemical noise measurements [J]. Corrosion Science, 1999, 41: 1245-1256
[5] Helmuth Sarmiento Klapper, Joachim Goellner, Andreas Heyn. The influence of the cathodic process on the interpretation of electrochemical noise signals arising from pitting corrosion of stainless steels [J]. Corrosion Science 52(2010) 1362-1372
[6] Lin HC.Cao C N.Astudy of electrochemical noise during pitting corrosion of iron in neutral solutions [J].Journal Chinese Society of Corrosion and Protection,1986,6(2):141
林海潮,曹楚南。孔蚀过程的电化学噪声研究[J].中国腐蚀与防护学报,1986,6(2):141-148
[7] REN Chengqiang. A study of the electrochemical corrosion behavior of N80 steel in CO2 and H2S environment [D]. Northwestern polytechnical university, 2003
任呈强。 N80油管钢在含CO2/H2S高温高压两相介质中的电化学腐蚀行为及缓蚀机理研究 [D].硕士学位论文,西北工业大学,2003.
[8] Linter B R,Burstein G T. Reaction of pipeline steels in carbon dioxide solutions[J].Corrosion Science,1999,42(2):117
[9] Nesic S, Postlethwaite J, OIsen S. An electrochemical model for prediction of corrosion of mild steel in aqueous carbon dioxide solutions [J]. Corrosion,1996,52(4):280
[10] Gusmano G, Montesperelli G, Pacetti S, et al. Electrochemical noise resistance as a tool for corrosion rate prediction[J]. Corrosion, 1997, 53(11): 860-868
[11] J. F Chen, W. F Bogaerts. The physical meaning of noise resistance [J]. Corrosion Science, 1995, 37:1839-1842
[12] Cheng Y F, Luo J L. Passivity and pitting of carbon steel in chromate solution [J]. Electrochimica Acta, 1999,44:4795-4804
[13] ZHANG Jianqing, ZHANG Zhao, WANG Jianming, CHENG Shaoan, CAO Chunan. Analysis and application of electrochemical noise -Ⅰ·Theory of electrochemical noise analysis [J]. Journal Chinese Society of Corrosion and Protection, 2001,21(5):310~320
张鉴清,张昭,王建明,曹楚南。 电化学噪声的分析与应用-Ⅰ。电化学噪声的分析原理 [J]。中国腐蚀与防护学报, 2001, 21(5): 310-320
[14] H.A.A. Al-Mazeedi, R.A. Cottis. Parameter maps for the assessment of corrosion type from electrochemical noise data [A]. Corrosion, 2004, Paper 460.
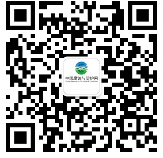
官方微信
《中国腐蚀与防护网电子期刊》征订启事
- 投稿联系:编辑部
- 电话:010-62313558-806
- 邮箱:fsfhzy666@163.com
- 中国腐蚀与防护网官方QQ群:140808414