新款宝马7系推行哪些材料结构?
2016-02-16 11:23:20
作者:本网整理来源:=$docheckrep[1]?ReplaceBefrom($ecms_gr[befrom]):$ecms_gr[befrom]?>
2015年6月发布的新款“7系”,则是新一款实现了多材料化的车辆。其车体骨架中融合了CFRP、铝合金和钢板,采用了新的轻量结构。宝马正在积极推行“多材料”结构,例如为纯电动汽车i3和插电式混合动力车i8采用了CFRP(碳纤维强化树脂)制驾驶室组合铝合金制车体下部的车身。下面就来看看其中的最新技术。
利用CFRP减轻重量、提高刚性
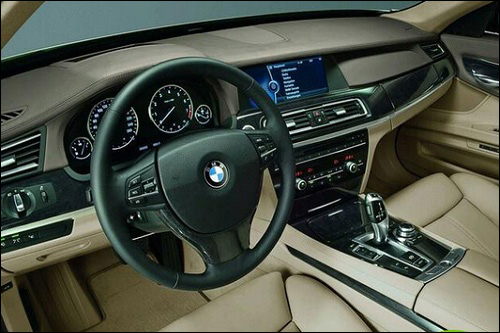
宝马内视图
多材料结构的目的是,通过将各类材料运用在最适合的部位,实现车体的轻量化。为了让以钢板为主的传统车体骨架大幅减轻重量,这项技术从很早以前就被看好。
欧洲的汽车企业顺应这个潮流,在骨架中采用钢板与铝合金相结合的结构的车辆越来越多。而对于CFRP,除了部分高级跑车外,并没有全面推广。
这一次,宝马新开发了车身结构,7系除了钢板和铝合金外,还积极采用CFRP作为骨架的加固件。
基本骨架采用钢材,但A柱的内部等部位使用了CFRP部件,通过提高刚性和强度,减轻了车体重量。使用传统的单体车身,并实现了CFRP等多材料结构的例子非常少见。
宝马将这种采用了CFRP的车体设计技术称作“Carbon Core”。之所以这样命名,是因为在钢板制成的封闭截面的内侧,插入了CFRP制作的芯材,详细情况将在后面介绍。
7系在德国的丁戈尔芬(Dingolfing)工厂生产。这里也为劳斯莱斯(Rolls-Royce)生产铝车体,负责宝马产品的传动系统及底盘部件的制造。CFRP部件也由该厂生产,在细致的品质管理之下,使用机器人组装车体。

宝马内视图
宝马为新款7系提出的技术主题是Efficient Light Weight。7系在充实了安全装备等的同时,整车重量较上一代车型减轻了130kg,车体骨架减轻约40kg。不仅利用CFRP部件实现了轻量化,还以驾驶室部分为中心,强化了抗弯性和抗扭刚性。
据宝马介绍,从原材料的生产到报废时的回收利用,整个生命周期的二氧化碳排放量比上一代减少了约25%。
下面就以车体骨架为中心,逐一看一看采用CFRP部件的具体部位。在车体骨架上,黑色部分采用的是CFRP,银色部分是铝合金,灰色部分是高张力钢板。
CFRP在车顶周围的采用比较突出,这估计是为了减轻驾驶室顶棚的重量并降低重心。宝马在车体中首次采用CFRP,是2003年推出的M3 CSL(E46型)的车顶。
车体采用的CFRP由3种成型方法制成。首先是引人注目的车顶纵梁,将CFRP作为了中空封闭截面结构的芯材。CFRP芯材的长度不到3m,为一体成型,周围覆盖着钢制表皮。通过使该部件贯穿车体上部,为轻量化和刚性强化作出了贡献。
责任编辑:王元
《中国腐蚀与防护网电子期刊》征订启事
投稿联系:编辑部
电话:010-62313558-801
邮箱:ecorr_org@163.com
中国腐蚀与防护网官方 QQ群:140808414
相关文章
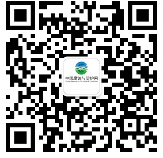
官方微信
《中国腐蚀与防护网电子期刊》征订启事
- 投稿联系:编辑部
- 电话:010-62313558-806
- 邮箱:fsfhzy666@163.com
- 中国腐蚀与防护网官方QQ群:140808414
点击排行
PPT新闻
铝合金LDH自修复自抗菌膜层构建
点击数:466
碳钢及合金钢应用与区别
点击数:393