“目前,钢管行业推进颠覆性工艺创新、绿色发展面临管坯芯部质量差、内壁质量差、缺少在线组织调控手段三大难题,需要重点解决。针对此三大难题,提出连铸坯凝固组织调控、铸坯直接穿孔高温再结晶控轧组织调控和热轧后控制冷却组织调控3个绿色化的系统解决方案。”在3月20日举办的2024第二届中国钢管产业创新发展大会上,中国工程院院士、东北大学教授王国栋在做《追求未来的钢管行业探索未知的钢管行业》主题报告时,如是指出了钢管行业面临的瓶颈问题与解决方案,并提出通过数字化转型赋能钢管行业绿色化、高质化和强链化发展。
图为王国栋
三大难题对应三大突破口
王国栋表示,目前钢管行业推进颠覆性工艺创新、绿色发展面临三大难题。
一是管坯芯部质量差。连铸坯凝固及冷却至室温后形成严重缩孔和中心疏松,芯部集中杂质和合金元素,严重影响最终钢管的质量。
二是内壁质量差。因冷却后再加热的连铸坯心部存在疏松、偏析等质量缺陷,在顶头到达之前钢管内部即已开裂,造成内壁折叠和裂纹等缺陷,降低了内壁质量,并严重影响钢管的整体使用性能和承载能力。同时,连铸坯冷却后重新加热穿孔、轧制,需要额外的能源供给。
三是钢材组织性能调控完全依靠合金与离线热处理,缺少组织调控手段。轧制和冷却过程组织调控手段缺失或落后,组织性能调控完全依靠高度合金化+离线热处理,成本高、消耗大、质量差、效率低。
王国栋提出,面对三大难题,钢管行业可以从三方面进行颠覆性创新,寻求突破口。
一是连铸坯凝固组织调控。“这也包括三方面的技术内容。”王国栋介绍,可以采用电磁搅拌、连铸坯凝固末端重压下、电磁旋流水口等技术,消除管坯中心缩孔、疏松等缺陷和宏观偏析,提高铸坯芯部质量。
二是连铸坯直接穿轧大变形控轧。王国栋介绍,在实际生产过程中,管坯芯部的严重疏松和杂质偏析等缺陷,是在其由高温冷却的室温过程中形成的。它们是穿孔时造成内壁缺陷的根源。如果采用铸坯免加热直接穿孔,在芯部疏松和杂质偏析形成之前,对高温的芯部金属进行穿孔和碾压变形,实现高温动态再结晶控制轧制,并避免了顶头前铸坯芯部开裂,故可以获得细晶、均匀、无缺陷的内壁组织。铸坯直接穿孔轧制,利用了高温再结晶技术从根本上改变了钢管内部的组织和性能。为了在铸坯穿孔过程中使铸坯的表面和芯部都获得必要的温度,建议综合采用反射式保温罩、提高拉速、合理选择铸坯火切位置等措施,控制铸坯在切断点的芯部温度在1300摄氏度左右,表面温度在1000摄氏度左右。由于温度较高、材料可塑性强,再加上大变形锻压过程,钢管内壁及整个断面的质量都会大幅提升。
三是轧后在线控制冷却进行组织调控。王国栋介绍,东北大学和宝钢合作,借鉴板材控轧控冷技术的经验,依托宝钢鲁宝PQF460机组,在国际上率先研发成功热轧无缝钢管控制冷却技术,在工艺减量化、合金减量化以及性能高质化等方面体现出显著成效。这标志着热轧无缝钢管组织性能调控进入新阶段。该技术作为热轧无缝钢管颠覆性的组织调控手段,突破了传统钢管生产工艺的技术瓶颈,开辟了热轧无缝钢管高效组织调控、实现高质量发展的新路径。
夯实基础设施底座,推进数字换脑、模型换代
王国栋表示,钢铁工业为大型复杂流程工业,巨大的不确定性是钢铁生产过程面临的重大挑战。在此背景下,数字化转型成为钢铁行业解决上述问题的关键。钢铁行业要按照习近平总书记指示,夯实数字底座,实行“人工智能+”,建设智能化综合性数字信息基础设施,智改数转,推动数字换脑、模型换代,建成生成式AI(人工智能)大模型,低成本、高效率、零风险地实现数字化转型,用数字化赋能绿色化、高质化、强链化。
钢管是钢铁行业重要产品,为了突破钢管行业的三大技术瓶颈、实现钢管行业的高质量发展,钢管企业必须尽快建立自己的企业数字化创新基础设施,即数字化转型的底座。他介绍,钢铁企业创新基础设施包括:一网,即工业互联网;三平台,即底层实体设备平台(端)、边缘数字化核心平台(边)、资源配置与管理云平台(云);四功能,即绿色化转型、数字化转型、高质化发展、强链化运行。该创新基础设施让数据在整个系统中闭环自动流动,通过状态感知、实时分析、科学决策、精准执行实现钢铁生产过程的自组织、自适应、自学习、高度自治的智能化控制,并对资源进行优化配置和管理。大量蕴含在物理空间中的隐性数据经过状态感知被转化为显性数据,进而能够在信息空间进行计算分析,将显性数据转化为有价值的信息。不同系统的信息经过集中处理形成对外部变化的科学决策,将信息进一步转化为知识,通过最优化设计应用于物理空间,形成一个闭环赋能循环系统,使得物理空间生产过程更加智能、资源调度和设备运维更加合理顺畅,各环节智能协同效果更加优化。
最后,王国栋为包括钢管行业在内的钢铁企业推进数字换脑、模型换代、开发工控大模型、实现新型工业化提出4点建议。
一是夯实数字底座。他建议,一方面组织企业建设钢铁企业新型信息基础设施,扩大工业感知网络覆盖面,打造海量物联接入能力;另一方面聚焦数字化转型、智能化发展、工业控制大模型系统等重点环节,增强源头技术供给。
二是强化应用牵引。王国栋建议,利用钢铁行业数据资源、应用场景和反馈赋能的优势,智改数转、数字换脑、模型换代,建立并应用钢铁行业大模型系统,制订项目目标、树立标杆、建立评价标准,推进数字化、智能化技术全方位、深层次赋能钢铁行业新型工业化。
三是加强技术服务。“通过产学研深度融合、联合组队等方式,推动装备、软件、网络等成组连线创新突破,提出系统解决方案;开展技术交流和推广工作,促进先进钢铁企业数字化推广应用。”他说。
四是营造良好生态。他建议,加快钢铁企业数字人才培训和关键标准研制推广,建设数字化转型开源生态,同时深化工业互联网安全管理。
“未来5年,建成15条~20条全流程一体化企业数字化转型生产线,完成钢铁产业数字化转型标准与规范的制定。未来10年,基本完成数字化转型,建成钢铁行业管理控制优化大模型,形成国家钢铁企业创新基础设施体系,实现行业高质量发展。”他最后说。
免责声明:本网站所转载的文字、图片与视频资料版权归原创作者所有,如果涉及侵权,请第一时间联系本网删除。
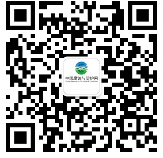
官方微信
《腐蚀与防护网电子期刊》征订启事
- 投稿联系:编辑部
- 电话:010-62316606
- 邮箱:fsfhzy666@163.com
- 腐蚀与防护网官方QQ群:140808414