晶格/点阵结构由于重量轻、高强度比,逐渐成为航空航天产品设计的宠儿。丹麦公司Adimant利用3D金属打印技术制作了据说是迄今为止最大的金属晶格结构,重1.7公斤,体积134×28×500毫米,用在欧洲最大的卫星制造商Thales Alenia Space的卫星上。
而近期,由中国空间技术研究院采用微单元包络体(即点阵结构)结构进行轻量化设计的飞行器结构件,通过金属3D打印技术研制成功,尺寸超过了Thales Alenia Space的卫星所采用的金属晶格结构。这标志着国内金属选区熔化3D打印在成形尺寸极限、薄壁结构、微单元包络结构等关键技术方面取得重大突破。今天,我们不但为大家揭晓此飞行器结构件的真面目,还将揭秘其背后的技术难题。
图1:飞行器框形状
据悉,此飞行器结构件是采用钛合金研发制造、包络尺寸为长短轴在550至700mm的十字连接椭圆形结构件(外形如图1所示)。如果采用传统制造工艺制造,零件内部只能为实体结构,重量将高达3公斤,无法满足减重设计要求。
为达到减重的目的,设计人员在零件设计优化过程中创造性地采用轻量化设计,用微单元包络体结构代替原有的实体结构,这种结构的理论重量远低于实体结构的重量,最终这样一个大家伙成形零件的质量仅为600余克!让人不得不惊叹于点阵结构的神奇魅力(内部结构如图2所示)。
图2:飞行器框结构
由于传统制造工艺无法实现这种微单元包络体结构的制造,最终,通过采取金属3D打印技术成功研制出该飞行器结构件。零件的质量仅为600余克,相比传统制造工艺减重80%左右。该钛合金零件体密度仅为1g/cm3,与水密度相当,减重效果极为明显,是尺寸获得重大突破的点阵轻量化飞行器结构件。众所周知,飞行器通常由众多复杂零部件构成,而这仅仅只是其中之一。如果能在更多的零部件尤其是大型结构件上实现晶格结构及金属3D打印,发射中的燃料成本将可以大大节约!这对于金属3D打印在航天航空领域的应用无疑具有里程碑式的重要意义。
据了解,此飞行器结构件成形采用的金属3D打印技术为激光选区熔化成形技术。激光选区熔化成型技术成形的零件致密性好,能够成形高精度复杂异型金属零件。因其具有组织致密、综合性能优良的特点,在国内外已得到了普遍重视,并具有一定程度商业化应用。
据项目相关专家介绍,采用激光选区熔化成形技术成形此结构件的背后,存在以下技术难题:
1、该飞行器结构件尺寸大,包络体蒙皮壁厚较薄,厚度不足0.5mm,且内部为微单元结构,结构尺寸精度要求严格;
2、激光选区熔化成形过程中,温度梯度产生的热应力存在使零件变形的风险;
3、包络体完全包络微单元结构,无法通过添加支撑来确保悬空的包络体蒙皮的成形。
4、零件整体尺寸较大,超出国际金属3D打印厂家一般设备成形尺寸极限。
5、重量要求严格,实物重量不得超过模型理论重量的3%。
据悉,为了获得性能优良、致密性高的轻量化飞行器结构件,中国空间技术研究院经过大量的工艺研究实验,在大型薄壁微单元包络体设计方面积累了丰富的经验。而鑫精合团队作为承制方,经过层层技术攻关,通过金属3D打印技术成功研制出这一大尺寸3D打印轻量化飞行器结构件产品,一举解决该结构件的减重制造难题。
更多关于材料方面、材料腐蚀控制、材料科普等方面的国内外最新动态,我们网站会不断更新。希望大家一直关注中国腐蚀与防护网http://www.ecorr.org
责任编辑:刘洋
投稿联系:编辑部
电话:010-62313558-806
邮箱:fsfhzy666@163.com
中国腐蚀与防护网官方 QQ群:140808414
免责声明:本网站所转载的文字、图片与视频资料版权归原创作者所有,如果涉及侵权,请第一时间联系本网删除。
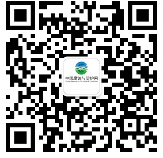
官方微信
《中国腐蚀与防护网电子期刊》征订启事
- 投稿联系:编辑部
- 电话:010-62316606-806
- 邮箱:fsfhzy666@163.com
- 中国腐蚀与防护网官方QQ群:140808414