海洋中蕴藏着巨大的油气资源,随着陆地及近海油气资源的日渐枯竭,深水和超深水的油气资源的勘探开发已经成为世界油气开采的重点领域[1]。随着海上油气田开发的迅速发展,海底油气输送管道已成为广泛用于海洋石油工业的重要运输手段[2]。海底管道由于埋入海底泥土中或浸于海水中,受潮水、暗流、涌动、微生物、腐蚀、海上交通等工况影响,因此对海底管道的可靠性提出了更高要求[3]。腐蚀是海底管线破坏的主要因素之一,严重影响海底管线的使用寿命, 更严重的是造成灾害性事故,引发油气泄漏,造成环境污染和人员伤亡等,导致巨大经济损失[4]。由于钢铁材料韧性大、强度高、价格便宜,因而大量应用于海底管道的建设中,但是苛刻的海洋腐蚀环境对管线钢管的腐蚀不可避免,几乎所有的典型腐蚀类型如:疲劳腐蚀、应力腐蚀、氢致开裂、冲击腐蚀、电化学腐蚀、细菌腐蚀在海底管线中都存在,尤其是主要用在酸性环境下服役的海底管线钢管。因此,研究开发具有耐腐蚀的高强度壁厚管线钢管,对于延长海底管线使用寿命,保证海底管道的安全运行,具有十分重要的意义。
本文针对1500米以上水深用深海油气输送管需求,结合深海高压服役工况对深海油气输送用钢管管线钢及钢管的性能要求,通过从管线钢成分、组织和性能等方面的研究分析,采用低碳微合金设计和高纯净度、超均质冶炼铸坯工艺以及优化的TMCP工艺,开发出具有良好的强韧性、强塑性和耐酸性的X70钢级36.5 mm厚壁管线钢板材,研制出具有抗硫化氢腐蚀的国产X70钢级φ(1016~762)mm×36.5mm高钢级、大壁厚深海油气输送管。
1 海底管线的发展概况
海底管道在国外发展很快,自1954年美国在墨西哥湾覆设世界第一条海底管道以来,北海、黑海、地中海、巴西等海洋油气田被相继发现和开发,全世界海底管道工程得到蓬勃发展[5]。目前世界最长的海底管道是挪威至英国的朗格勒得北海管道,总长度1200 km,管径1016 mm,壁厚34.1 mm,材质X70,最大工作压力25 MPa,最大水深1000 m。目前世界最深海底管道是美国墨西哥湾东部湾的独立管道,水深为2454 m,其管径为610 mm,壁厚34.3 mm,材质X65,最大工作压力25 MPa。目前世界深水管道的典型水深为2500 m,正面临3 000 m及以上深度的挑战[6]。目前世界壁厚最大的海底管道是俄罗斯和欧洲之间穿越波罗的海的输气管道,使用了X70 钢级,管径1219 mm,最大壁厚达到41.0 mm,是目前海底管道工程中应用的最大壁厚钢管。目前,国外海底管道工程中非酸性环境下应用的最高钢级为X70,酸性环境下应用的管材最高钢级为X65[7]。
受装备和技术的限制,我国的海洋管道不仅起步晚,而且海洋管道的设计、施工总体水平与国际先进水平相比存在较大差距。目前世界海底油气管道总量已超过10万千米,最大作业水深已达3000米。我国的海底管道建设始于上世纪八十年代,初期是通过与同国外合作摸索积累经验。经过多年的迅猛发展,我国从1985 年建成第一条海底输油管道开始,在我国海域现已累计已铺设海底管道60多条,总长度超过8000 km。在管道长度方面,从海南岛近海某气田至香港的一条直径为711 mm 的海底输气管道长达800 km,是我国目前最长的一条海底管道[8]。2012 年完工的南海荔湾3-1气田海底管道全长约261 km,钢管外径为762 mm,壁厚为28.6~31.8 mm,钢级为X65MO 和X70MO,设计压力为23.9 MPa,是迄今国内压力最高、壁厚最厚的海底管道开发,同时也开创了我国1500 m 作业水深的管道工程纪录,在海洋开发和海底管线制造领域具有重要战略意义[9]。
2 高强度厚壁管线钢板材的开发
为适应海底管道的安装要求和服役条件,海底管线钢材料除需满足高强度、高韧度以及良好的焊接性能和耐腐蚀性能等一般要求外[10],深海管道用管线钢材料还具有如下特点:①高的形变强化指数和均匀延伸率;②低的屈强比;③优良的纵向拉伸性能;④低的铸坯中心偏析,良好的厚度方向性能,低的断口分离和层状撕裂的几率;⑤优异的夏比冲击、落锤撕裂和CTOD性能;⑥优异的焊接性;⑦严格的尺寸偏差和精度控制[11]。因此,海底管线在成分设计和性能方面要求更为严格,在成分和组织上要求“超高纯、超均质、超细化”。深海管线用X70钢级36.5 mm厚壁管线钢板材采用的是低碳含量、低碳当量、低硫磷含量以低C-低Mn-Nb-Ni-Mo系为基,根据性能要求适当添加Cu和Cr等合金元素的合金化设计,通过TMCP轧制工艺获得以针状铁素体为主体的组织类型。满足管线钢的抗硫化氢腐蚀性能要求,其中要求W[S]<0.001%,W[P]≤0.012%;钢中的夹杂物最大直径D<100 μm,控制氧化物形状,消除条形硫化物夹杂的影响;钢中脆性A12O3 夹杂物和条状MnS夹杂成痕迹,晶粒细化。
在炼钢工艺上采用了超低S、Ca处理等纯净钢冶炼技术,在热轧方面采用控制轧制和控制冷却技术,以得到钢质纯净、组织均匀的针状铁素体组织。在钢板生产中,主要从板坯加热温度、变形量、轧制温度和轧后冷却等方面对X70管线钢的轧制工艺进行控制。为获得细小、均匀的显微组织,采用较大的单道次变形量、较高的累积压下率和冷却速率。将钢锭在电炉中加热至1200 ℃,均匀化60 min后,经过再结晶温度区变形50% 和非再结晶温度区变形20% 的两阶段控轧,采用TMCP工艺轧成36.5 mm 厚钢板,终轧后钢板先弛豫一定时间再进行加速冷却,终轧温度控制在820°C,终冷温度为430°C,最终获得细小、均匀的针状铁素体组织。通过调整精轧温度、变形量和冷却模式及温度的均匀性控制等,降低了钢板的横纵向性能差异,改善了钢板的表面质量以及钢板的组织和性能的均匀性,钢板的屈服强度、抗拉强度、冲击韧性及DWTT性能均满足深海管线用管线钢的性能要求。
开发出的X70 36.5 mm厚壁管线钢钢板的微观组织见图1,化学成分和力学性能分别见表1和表2。
图1 X70 36.5 mm钢板微观金相组织
Fig.1 Microstructure of 36.5 mm X70 steel plate
表1 X70 36.5mm厚壁管线钢的化学成分设计(质量分数,%)
Table 1 Chemical Composition Design of X70 pipeline steel plate with 36.5 mm(Wt.%)
C |
Si |
Mn |
P |
S |
Ni |
Cr |
Cu |
Nb |
V |
Ti |
Mo |
B |
N |
Alt |
Pcm |
0.04 |
0.24 |
1.51 |
0.011 |
0.001 |
0.26 |
0.25 |
0.18 |
0.06 |
0.006 |
0.014 |
0.15 |
0.0003 |
0.004 |
0.030 |
0.15 |
表2 X70 36.5mm管线钢板材力学性能
Table 2 Chemical Composition Design of X70 pipeline steel plate with 36.5 mm(Wt.%)
方向 |
屈服强度 Rt0.5/MPa |
抗拉强度Rm/MPa |
断后伸长率 A50/% |
屈强比Rt0.5/Rm |
冲击吸收能量Akv(-30℃)/J |
落锤 SA(-10℃)/% |
硬度 (HV10) |
晶粒度 级别 |
带状组织 级别 |
0℃ CTOD/mm |
横向 |
523 |
615 |
65.4 |
0.85 |
480 |
96 |
185-211 |
11-11.5 |
0-0.5 |
1.19 |
纵向 |
503 |
593 |
63.8 |
0.85 |
495 |
96 |
1.34 |
从X70 36.5 mm高强度厚壁管线钢板材的组织、化学成分和力学性能结果可看出,开发的X70 36.5 mm管线钢板材组织均匀、钢质纯净,性能优良,断裂韧性优异,严格控制了S,P,N和O等有害元素含量,板材的低温韧性、焊接性能和耐酸性腐蚀性能得到明显改善。
3 高强度厚壁抗H2S腐蚀海洋管的开发
采用开发出X70 36.5 mm高强度厚壁管线钢板材,通过JCOE直缝埋弧焊接钢管的小径厚比(D/t)钢管成型、厚壁管线钢多丝埋弧焊接、钢管全管体扩径等工艺技术研究,在宝鸡钢管公司下属秦皇岛钢管公司JCOE制管生产线试制出X70 φ(1016~762) mm×36.5 mm的高钢级、大壁厚深海油气输送管,从管体及焊接接头的力学性能、硬度及抗H2S耐腐蚀试验等方面对试制钢管进行了性能分析。
3.1 力学性能
在距焊缝180°处取管体横、纵向全壁厚板状拉伸试样,在焊接接头处取横向焊缝全壁厚板状拉伸试样,依据ASTM A370-14标准在UTM5305、SHT 4106材料试验机上进行拉伸性能试验,表3 为钢管的拉伸性能试验结果。
表3 拉伸性能试验结果
Table 3 Tensile properties test results of steel pipe
管体拉伸性能 |
焊缝拉伸性能 |
|||||
Rt0.5/MPa |
Rm/MPa |
Rt0.5/Rm |
A50/% |
UEL/% |
Rm/MPa |
断裂位置 |
495~512 |
645~648 |
0.77~0.79 |
55~58 |
7.5~8.2 |
665~668 |
母材 |
一般而言,在满足强度要求下,其屈强比越低、伸长率越高、维氏硬度越小,就更适合在具有腐蚀性、对钢管变形能力要求较高的环境中使用[12]。从表3 中可以看出,试验的X70 36.5 mm厚壁直缝埋弧焊管的管体屈服强度为495~512 MPa,抗拉强度为645~648 MPa,屈强比为0.77~0.79,伸长率为55%~58%,这些性能指标均能满足DNV-OS-F101-2013《海底管线系统规范》要求。同时,从表3可以看出,钢管焊接接头的抗拉强度略高于母材抗拉强度20 MPa,断裂位置都在母材处,表明在焊接过程中热影响区未出现软化现象。由此可见,试验钢管具有高塑性的特点,可适用于具有腐蚀性的环境中。
3.2 硬度
依照ASTM E 384-11e1标准,采用KB 30BVZ-FA硬度计对焊接接头进行硬度测试,表4为试验钢管焊接接头维氏硬度试验结果,图2为焊接接头测试位置示意图。
图2 焊接接头维氏硬度试验压痕位置示意图
Fig.2 Schematic diagram of the indentation position of the Vickers hardness test of the welded joint
表4 焊接接头维氏硬度试验结果(HV10)
Table 4 Vickers hardness test results of weld joint
压痕位置 |
1 |
2 |
3 |
4 |
5 |
6 |
7 |
8 |
9 |
10 |
11 |
12 |
13 |
14 |
15 |
16 |
17 |
18 |
硬度值 |
189 |
190 |
193 |
189 |
190 |
190 |
198 |
227 |
226 |
225 |
226 |
221 |
201 |
179 |
204 |
196 |
201 |
208 |
压痕位置 |
19 |
20 |
21 |
22 |
23 |
24 |
25 |
26 |
27 |
28 |
29 |
30 |
31 |
32 |
33 |
34 |
35 |
36 |
硬度值 |
201 |
200 |
198 |
196 |
191 |
194 |
212 |
225 |
223 |
226 |
226 |
200 |
215 |
192 |
209 |
204 |
207 |
209 |
压痕位置 |
37 |
38 |
39 |
40 |
41 |
42 |
43 |
44 |
45 |
46 |
47 |
48 |
49 |
50 |
51 |
52 |
53 |
54 |
硬度值 |
207 |
202 |
197 |
198 |
192 |
202 |
222 |
231 |
232 |
231 |
243 |
239 |
203 |
196 |
182 |
198 |
207 |
209 |
硬度与强度密切相关,早期的研究发现,硫化氢应力腐蚀敏感性与钢材的硬度有关,硬度愈高,敏感性愈大, 所以NACE MR0175 推荐在酸性介质中,管线钢的硬度极限为248HV10 或22HRC[13]。从表4中可以看到,管体母材及焊接接头的平均硬度为207 HV10,最大硬度值为243HV10。管体及焊接接头的硬度试验结果表明,钢管可适用于在硫化氢腐蚀环境中应具有的低硬度特点。
3.3 氢致裂纹(HIC)试验
在管体母材及焊缝处的壁厚上、中、下部位取抗氢致裂纹试样,试样规格为20 mm×20 mm×100 mm,依据美国腐蚀工程师协会NACE TM0284-2011(A溶液) 标准进行HIC试验。管体母材及焊缝试样在H2S饱和溶液(A溶液)中浸泡96小时。试验后,经过对试样进行宏观检查,试样表面未发现氢鼓泡(见图3~图4)。经对试样截面的金相剖面在100倍显微镜下进行观察,管体及焊缝剖面无裂纹(见表5)。试验结果表明试验钢管在该试验条件下对HIC不敏感。
表5 HIC试样内部剖面裂纹率测量分析结果
Table 5 Measurement and analysis results of internal cross section crack rate of HIC specimen
位置 |
剖面编号 |
平均值 |
||||||||||
Ⅰ |
Ⅱ |
Ⅲ |
||||||||||
CLR(%) |
CTR(%) |
CSR(%) |
CLR(%) |
CTR(%) |
CSR(%) |
CLR(%) |
CTR(%) |
CSR(%) |
CLR(%) |
CTR(%) |
CSR(%) |
|
管体上部 |
0 |
0 |
0 |
0 |
0 |
0 |
0 |
0 |
0 |
0 |
0 |
0 |
管体中部 |
0 |
0 |
0 |
0 |
0 |
0 |
0 |
0 |
0 |
0 |
0 |
0 |
管体下部 |
0 |
0 |
0 |
0 |
0 |
0 |
0 |
0 |
0 |
0 |
0 |
0 |
焊缝 |
0 |
0 |
0 |
0 |
0 |
0 |
0 |
0 |
0 |
0 |
0 |
0 |
3.4 硫化物应力腐蚀(SSCC)试验
在管体母材及焊缝位置取抗硫化物应力腐蚀试样,试样规格为5 mm×15 mm×120 mm。依据美国腐蚀工程师协会NACE TM0177-2005(A溶液)标准进行抗硫化物应力腐蚀(SSCC)试验,试验设备为四点弯曲试验装置,应力加载量为413MPa(85%SMYS),经过720小时H2S饱和溶液(A溶液)浸泡,试样未断裂,放大10倍观察无裂纹(见图5~图6),试验结果表明试验钢管具有良好的抗应力腐蚀能力。
3.5 腐蚀速率试验
在管体母材及焊缝位置取腐蚀速率试验挂片试样,试样尺寸为3 mm×15 mm×25 mm,每个位置各取3个平行试样。腐蚀速率浸泡试验依据JB/T 7901—2001《金属材料实验室均匀腐蚀全浸试验方法》,在常温常压条件下进行,试验介质为3.5% (质量分数)NaCl水溶液(pH为6.5~7.2),试样在腐蚀试验介质中连续浸泡30天。
Tab.6 Corrosion rate of X70 steel pipe in 3.5%NaCl solution at room temperature and pressure
试验位置 |
试样编号 |
试验前重量/g |
试验后重量/g |
腐蚀速率(mm/a) |
平均腐蚀速率(mm/a) |
管体母材 |
-1 |
8.46250 |
8.40785 |
0.08684 |
0.08518 |
-2 |
8.13680 |
8.08345 |
0.08572 |
||
-3 |
8.08369 |
8.03205 |
0.08299 |
||
焊缝 |
-1 |
8.10541 |
8.04988 |
0.08926 |
0.08687 |
-2 |
8.04242 |
7.98953 |
0.08541 |
||
-3 |
8.17120 |
8.11746 |
0.08592 |
从表6的腐蚀速率试验结果可以看出,试验管材在焊缝和管体母材的腐蚀速率均小于0.09 mm/a,焊缝的平均腐蚀速率比管体的略高一点。根据SY/T0087.1-2006以及NACE标准RP-0775-2005对腐蚀程度的规定,管体和焊缝的腐蚀均属轻微腐蚀,即表明该X70试验钢管具有良好的耐腐蚀性能。
4 结 论
(1)采用低碳微合金设计和高纯净度、超均质冶炼铸坯工艺以及优化的TMCP工艺,开发出具有良好的强韧性、强塑性和耐腐蚀的深海用X70 36.5 mm高强度厚壁管线钢钢板。
(2)开发出具有抗硫化氢腐蚀的国产X70钢级φ(1016~762)mm×36.5 mm高钢级、大壁厚深海油气输送管。通过对试制钢管管体及焊接接头的力学性能、硬度、氢致裂纹(HIC)、硫化物应力腐蚀开裂(SSCC)等试验分析,试验结果表明开发的X70 36.5 mm高强度厚壁钢管具有良好的耐硫化氢腐蚀性能。
更多关于材料方面、材料腐蚀控制、材料科普等方面的国内外最新动态,我们网站会不断更新。希望大家一直关注中国腐蚀与防护网http://www.ecorr.org
责任编辑:王元
投稿联系:编辑部
电话:010-62313558-806
中国腐蚀与防护网官方 QQ群:140808414
免责声明:本网站所转载的文字、图片与视频资料版权归原创作者所有,如果涉及侵权,请第一时间联系本网删除。
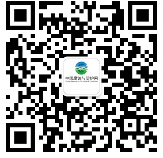
官方微信
《中国腐蚀与防护网电子期刊》征订启事
- 投稿联系:编辑部
- 电话:010-62316606-806
- 邮箱:fsfhzy666@163.com
- 中国腐蚀与防护网官方QQ群:140808414