衬套作为航空发动机某部位的重要组成部件,用于壳体内部齿轮和轴承的安装,衬套的材料分为碳钢和钛合金类,为了减轻发动机的重量,以钛合金衬套居多。本文所涉及油管衬套材料为TC4钛合金,由棒材加工而成,内外表面经阳极化处理。TC4合金是一种中等强度的α+β型两相钛合金,该合金具有优异的综合性能,现已广泛用于制造航空发动机风扇和压气机的盘与叶片以及紧固件等。衬套内燃油管材质为不锈钢,燃油管与衬套间套有橡胶管。拆解时发现断裂油管衬套橡胶管已磨损,不锈钢油管与衬套直接接触。
本文对断裂油管衬套进行了宏微观观察、金相检查、硬度检查、能谱分析及残余应力测试,确定了油管衬套的断裂性质,并分析了断裂原因。
1.外观检查送检
衬套导管组件外观形貌如图1所示。断裂油管衬套外观如图2所示,衬套上端为类似花键形状,表层为滚花工艺;下端为螺纹,中间连接处表面光滑,花键端内圆有一小台阶。断裂位置位于近花键端台阶处,断裂方向沿衬套周向分为三段,其中左右两段断口长度接近半圆弧,分别标为1#、2#断口;中间一段断口位于花键两R角中间,收集断口时已丢失。
观察衬套内表面有不同程度的挤压磨损痕迹,周向磨损痕迹明显,在花键端靠近丢失断口一侧磨损痕迹较对侧更深,螺纹端与丢失断口相反的一侧磨损痕迹较深。
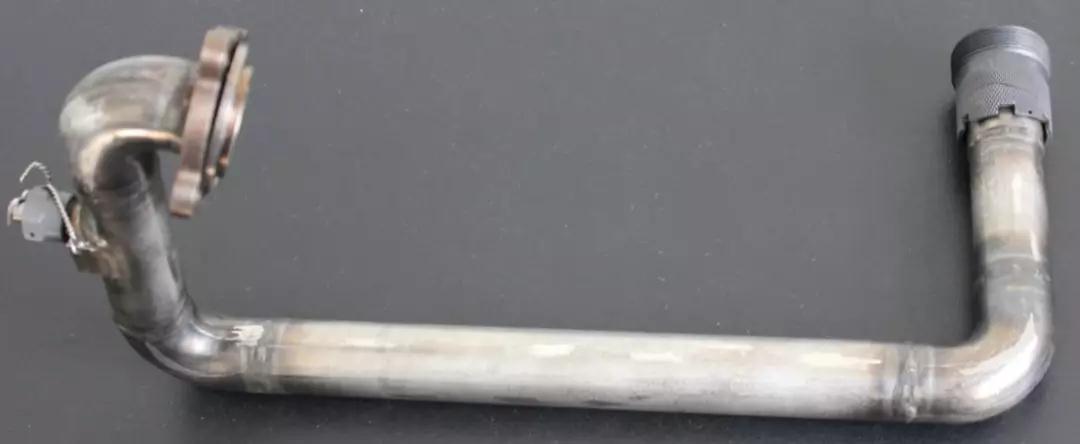
图1 导管组件外观形貌
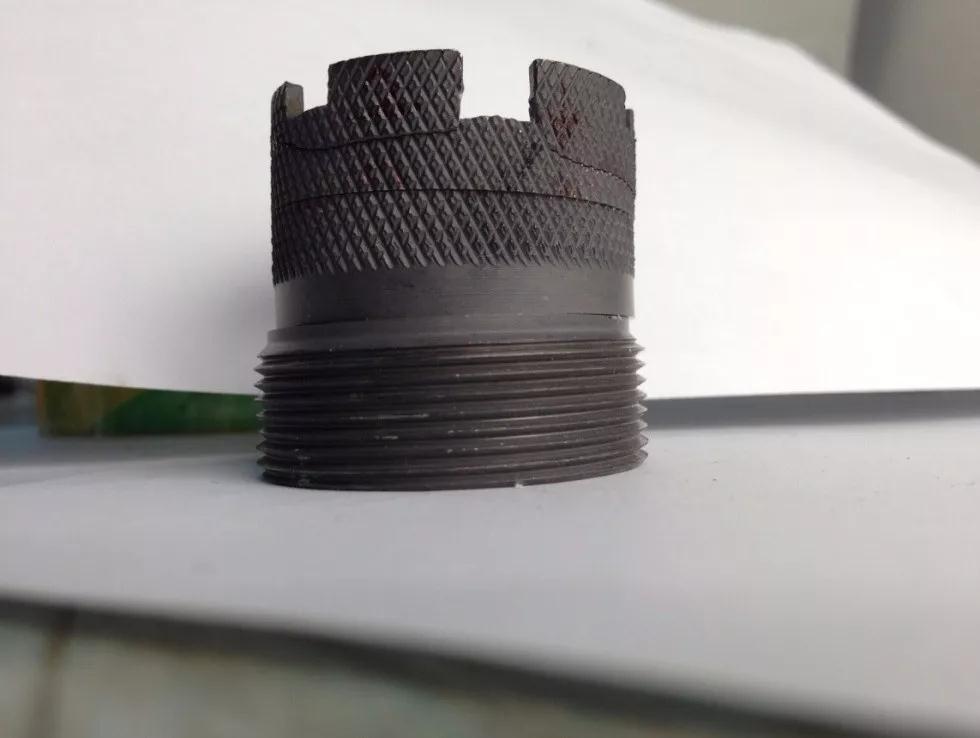
(a)断裂油管衬套整体外观
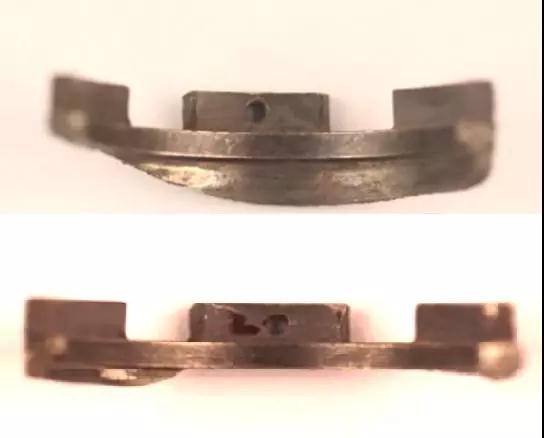
(b)1#、2#断口外观
图2 断裂油管衬套外观
2.宏观、微观观察及能谱分析
(1)宏观观察
将断口置于体视显微镜下观察,图3为1#断口放大观察。螺母掉块断口呈黑灰色,两断口R角处断面均可见由R角处发散的扩展棱线,并伴有疲劳弧线特征,如图3a所示;R角半径较小(见图3b),过渡区加工痕迹较为明显;两断口内表面朝向螺纹一端的台阶面可见清晰磨损痕迹(见图3c),在靠近丢失断口一侧磨痕更为明显。2#断口与1#断口宏观形貌基本一致。
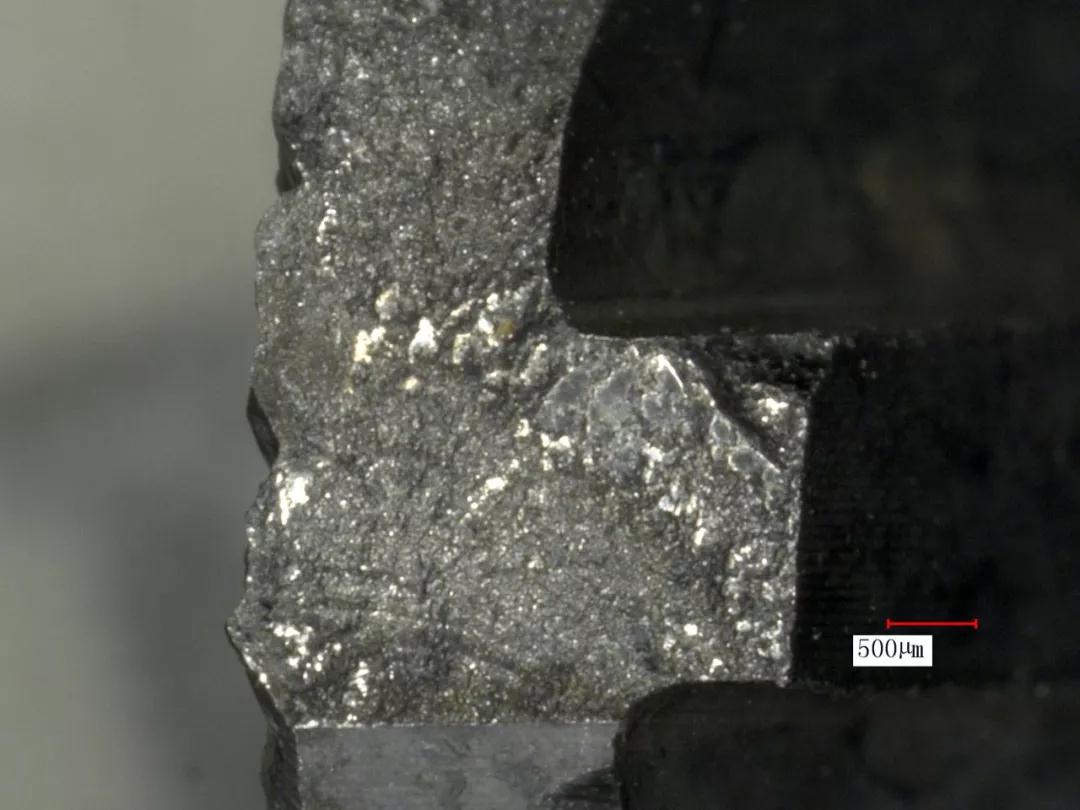
(a)R角处断面
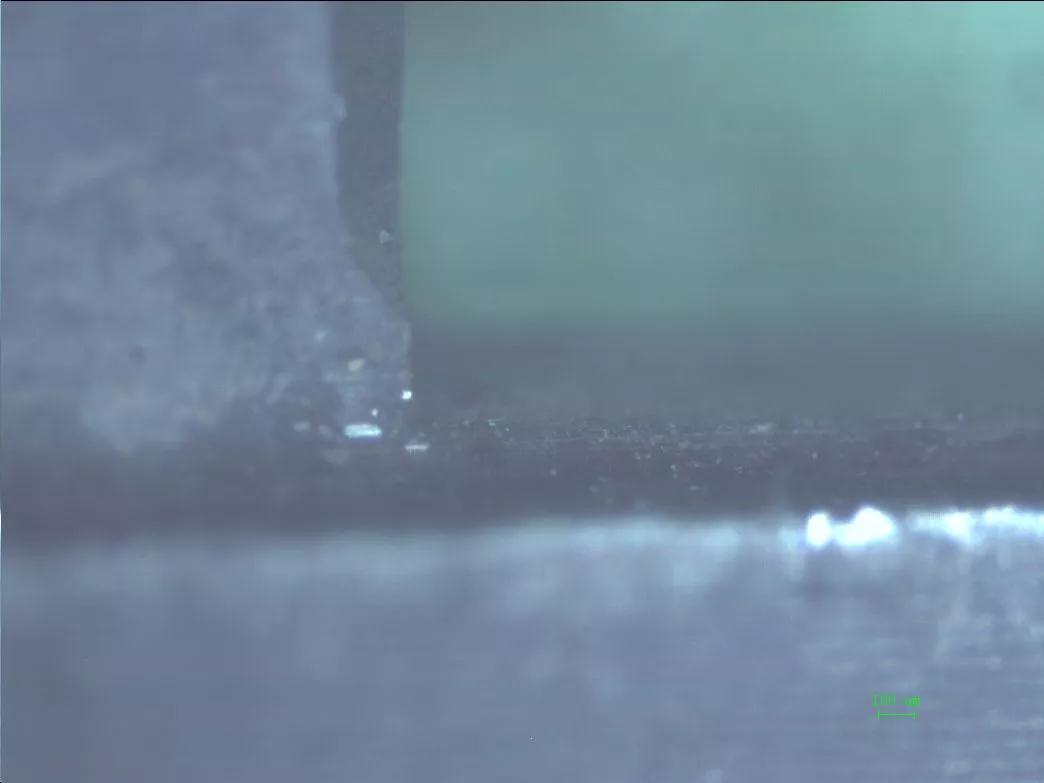
(b)R角侧面
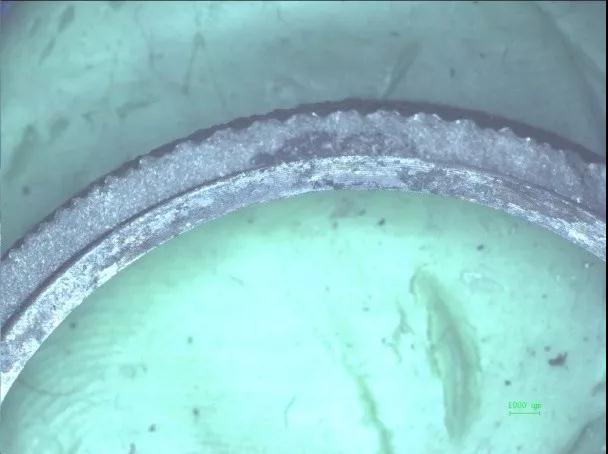
(c)内表面台阶磨损痕迹图
3 1#断口体视放大观察
(2)微观观察及能谱分析
将1#断口用丙酮超声波清洗后放入扫描电镜下进行微观观察。图4为1#断口显微形貌,裂纹从R角处起源,呈线源,可见扩展棱线从源区约45°方向向衬套内表面扩展;次源区为外表面滚花尖角处,棱线由外表面向内表面扩展(见图4a)。主源区放大形貌如图4b所示,断口表面存在附着物,经能谱测试主要含C、O元素,断面可见大量清晰小刻面,呈准解理特征。对断口进行整体观察,可见所有外表面滚花尖角处均存在清晰棱线,由外表面向内表面扩展,如图4c、4d所示,扩展区也为准解理断裂特征。2#断口微观形貌与1#断口特征一致。
取断口附近滚花表面试样沿周向进行人工打断,人工打断断口显微形貌如图5所示,为典型韧窝特征。
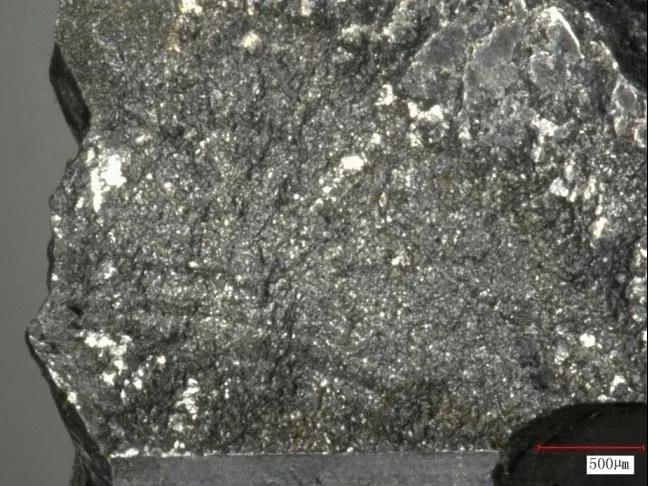
(a)源区低倍形貌
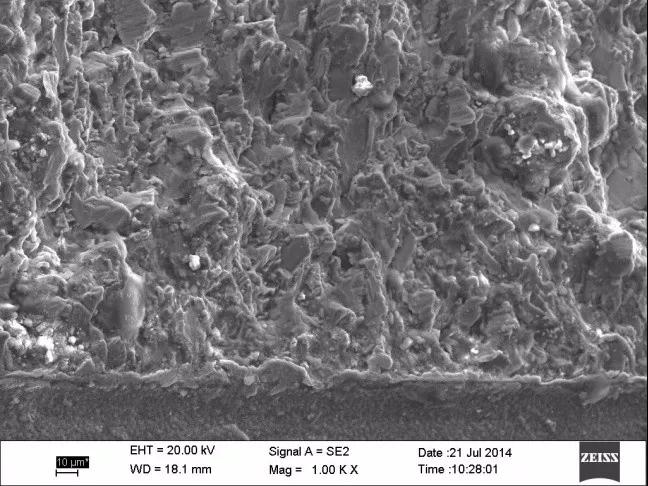
(b)主源区高倍形貌
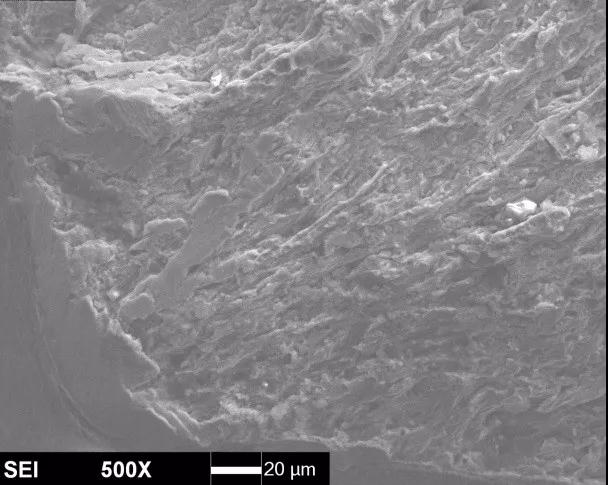
(c)疲劳扩展区低倍形貌
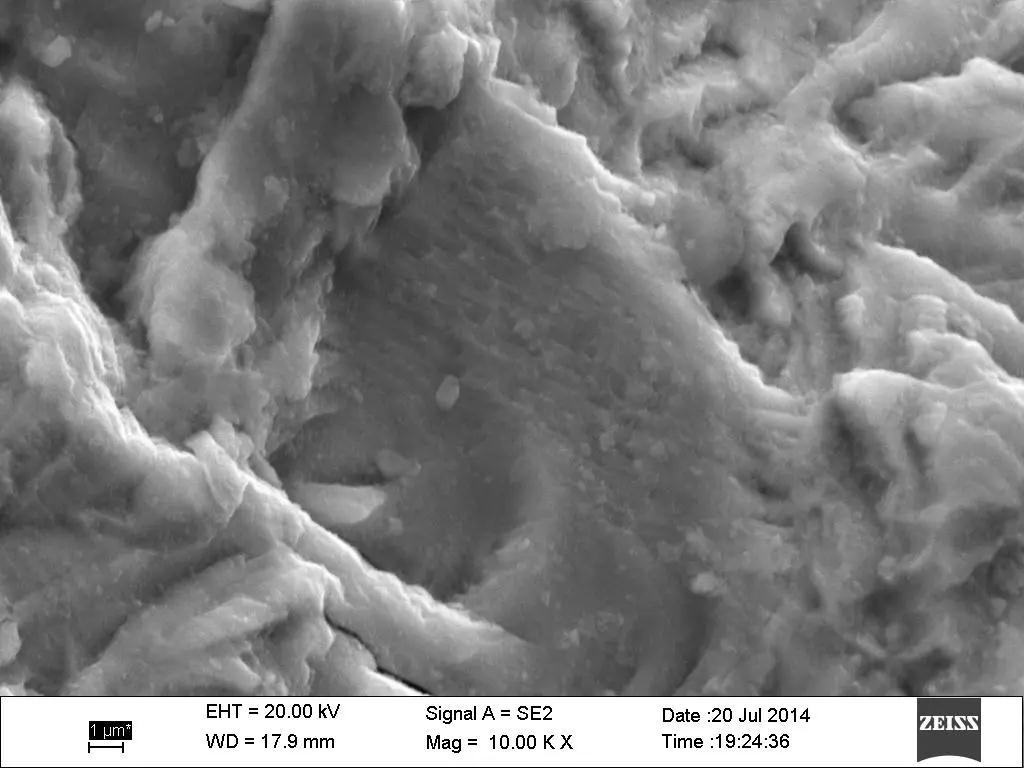
(d)疲劳扩展区疲劳条带形貌
图4 1#断口显微形貌
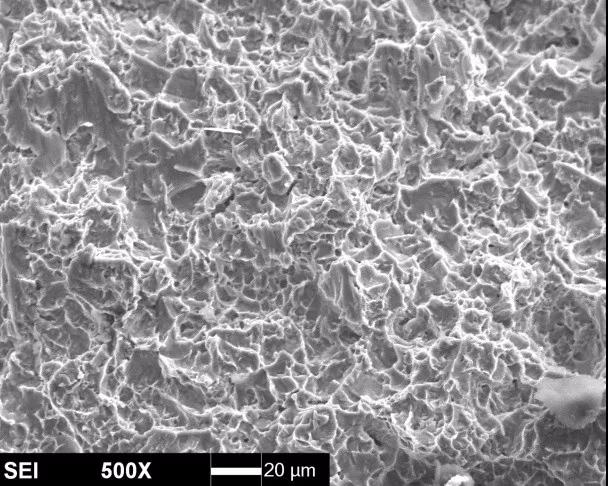
图5 人工打断断口显微形貌
3.残余应力测试
对衬套滚花表面及滚花与螺纹连接的光滑表面进行残余应力测试,结果如表1所示,可见周向残余应力较小。
表1 残余应力测试数据 (N·mm-2)
位置 |
滚花表面位置1 |
滚花表面位置2 |
光滑表面 |
周向 |
3.4±16.4 |
6.1±6.3 |
-10.3±13.2 |
轴向 |
112.1±7.6 |
96.0±11.4 |
81.5±8.1 |
4.金相检查
在断口附近垂直于衬套轴向和周向分别取横截面和纵截面制金相试样,显微组织分别如图6a、6b所示。油管衬套金相检查为双态组织,滚花表面可见明显塑性变形,金相组织为等轴α+β两相组织,参照GJB1538《飞机结构件用TC4钛合金棒材规范》标准评级,其组织状态符合图A1-A2。螺母金相组织未见异常。
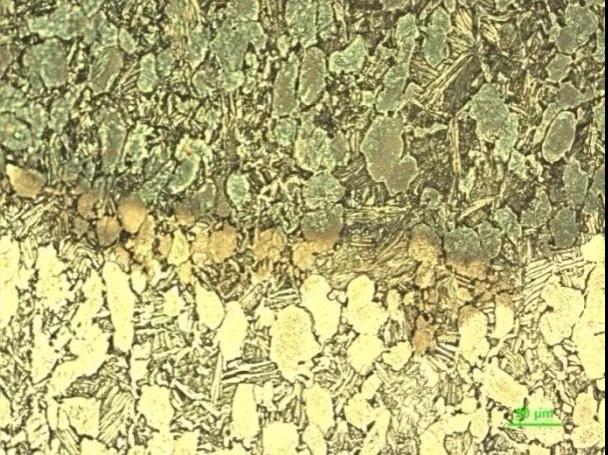
(a)横截面(500×)

(b)纵截面(500×)
图6 金相组织检查
5.硬度检查
对油管衬套金相检查所取的横截面与纵截面试样进行维氏硬度测试,测试结果如表2所示,符合正常TC4钛合金硬度范围。
表2 油管衬套硬度测试结果(HV0.5)
位置 |
1 |
2 |
3 |
平均值 |
|
横截面 |
靠近滚花处 |
309.2 |
320.9 |
317.1 |
315.7 |
基体 |
314.2 |
292.6 |
294.5 |
300.4 |
|
纵截面 |
基体 |
304.6 |
303.2 |
337.7 |
315.2 |
6.分析与讨论
(1)油管衬套的断裂性质分析
断口的宏微观观察结果表明,油管衬套裂纹首先从花键端一凹槽两R角处线性起源,宏观可见疲劳弧线特征,源区附近宏观可见明显扩展棱线,而后断口在整个圆周方向由外表面内表面扩展,在所有外表面滚花尖角处均可见清晰扩展棱线,为多点次疲劳源,扩展区为准解理特征,与人工打断断口的典型韧窝特征不同。由以上特征可判断油管衬套的断裂性质为疲劳断裂。
(2)油管衬套的断裂原因分析
油管衬套金相组织正常,未见明显冶金缺陷,硬度正常,表明该衬套开裂与材质无关。
从油管衬套的受力方面进行分析:首先,油管衬套内表面可见清晰周向磨损痕迹,在花键端裂纹起源一侧磨损痕迹较对侧更深,螺纹端与裂纹起源相反的一侧磨损痕迹较深(见图7),此磨损痕迹应为不锈钢油管在衬套内的相对运动所致,两钢管在衬套内对接的同轴度差,伴随发动机工作过程中的振动,极易引起对衬套的不均匀磨损。失效油管衬套在拆卸过程中,油管与衬套间所垫橡皮圈已完全磨透,证明了油管与衬套之间磨损严重。此外,在花键端内部面向螺纹的台阶表面也存在磨损痕迹(见图3c、图4c),说明油管台阶与衬套台阶相接触且存在相互作用力。此外,花键端凹槽R角较为尖锐,存在应力集中,促进了疲劳裂纹的起源。
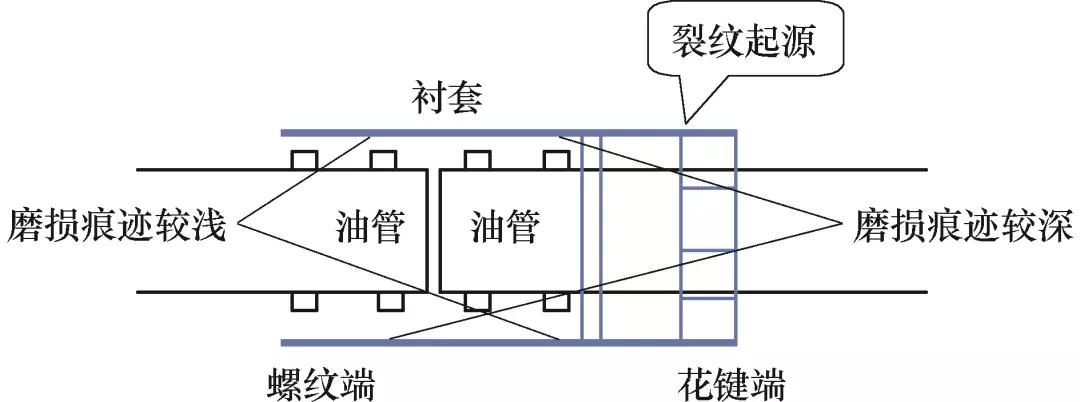
图7 衬套与油管配合示意
综上所述,油管衬套的断裂性质为疲劳断裂。其断裂主要原因为衬套与油管配合不良所带来的不均匀振动与挤压产生的附加应力,同时,结构上的应力集中促进了疲劳裂纹的萌生与扩展,最终导致衬套发生疲劳断裂。
7.结语
(1)油管衬套的断裂性质为疲劳断裂,疲劳源区未见缺陷。
(2)油管衬套断裂主要原因为衬套与油管配合不良所带来的不均匀振动与挤压产生的附加应力,结构上的应力集中促进了疲劳裂纹的萌生。
(3)花键端凹槽R角较为尖锐,存在明显加工痕迹,建议对R角进行圆滑处理。
更多关于材料方面、材料腐蚀控制、材料科普等方面的国内外最新动态,我们网站会不断更新。希望大家一直关注中国腐蚀与防护网http://www.ecorr.org
责任编辑:韩鑫
《中国腐蚀与防护网电子期刊》征订启事
投稿联系:编辑部
电话:010-62313558-806
邮箱:fsfhzy666@163.com
中国腐蚀与防护网官方 QQ群:140808414
免责声明:本网站所转载的文字、图片与视频资料版权归原创作者所有,如果涉及侵权,请第一时间联系本网删除。
相关文章
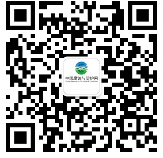
官方微信
《中国腐蚀与防护网电子期刊》征订启事
- 投稿联系:编辑部
- 电话:010-62313558-806
- 邮箱:fsfhzy666@163.com
- 中国腐蚀与防护网官方QQ群:140808414
点击排行
PPT新闻
“海洋金属”——钛合金在舰船的
点击数:5768
腐蚀与“海上丝绸之路”
点击数:4763