TC18 钛合金是前苏联于20 世纪70 年代开发的一种综合性能优良的航空结构材料,它具有高强度、高韧性、高淬透性以及良好的焊接性能。目前,国外已经广泛地使用TC18 钛合金制造大型飞机起落架、机身对接框等结构件。将该类钛合金用于飞机起落架结构件来代替高强钢,可使飞机整体减重15%~20%。由于TC18 钛合金拥有一系列优异的性能,其使用将会更加广泛,在起落架上也将会有越来越多的应用。然而起落架在沿海地区长时间服役时会承受严重的海洋性盐雾腐蚀和摩擦磨损,因而需采用表面防护技术提高其表面耐蚀性能。目前已有研究报道各种表面防护技术替代电镀硬铬。经综合评价,HVOF喷涂WC-Co涂层技术被认为最有可能替代电镀硬铬。此外,HVOF喷涂具有相对高的粉末粒子飞行速度和相对低的喷涂温度的优势,因而可以制备出综合性能更优的WC-Co涂层。
本文以TC18 钛合金为基体,采用HVOF 制备WC-12Co 涂层和WC-10Co4Cr 涂层。使用SEM,EDS和XRD分析试样腐蚀前后的微观结构,元素分布和物相组成,通过显微硬度测试和纳米压痕测试分析涂层与基体的显微硬度和塑韧性,采用电化学腐蚀测试和中性盐雾腐蚀测试分析基体及喷涂试样的耐蚀性能。
1 实验方法
选用粒径为15~45 μm 的WC- 12Co 和WC-10Co4Cr 喷涂粉末,基材为TC18 钛合金,其合金元素含量(质量分数,%)为:Al 5.10,Mo 5.14,V 5.06,Cr 0.93,Fe 0.98,C 0.025,H 0.005,N 0.02,O 0.15,余量为Ti。采用国产XM-8000超音速火焰喷涂设备制备WC-12Co和WC-10Co4Cr涂层。喷涂燃料选用航空煤油,氧气作为助燃气,氮气为送载气。采用的工艺参数如下:距离为35 cm,送粉速率为1.5 g/min;燃油流速为25 L/h,压强为12.55 MPa;氧气流速为565 L/h,压强为14.95 MPa;氩气流速为7.5 L/h,压强为0.8 MPa。在喷涂前使用丙酮和酒精对基体表面进行超声震荡清洗,采用60 目的刚玉对基体表面进行喷砂粗化处理,喷涂涂层厚度约为150 μm,喷涂后的试样需使用不同型号金相砂纸依次打磨并使用金刚石研磨膏抛光。并使用表面粗糙度测试仪测量试样表面粗糙度Ra均小于0.2 μm。
超显微硬度计为正四棱锥金刚石压头,测试参数为:加载载荷为300 g,保持时间为15 s,每个试样测量10 个点取算术平均数。为了分析涂层和基材的塑韧性,使用岛津DUH-W201 型超显微硬度计测量其弹性模量,该纳米压痕仪采用金刚石正三角锥压头,测试参数为:载荷500 mN,加载速度3.530394 mN/s,保持时间为10 s。为了分析与评价基体与喷涂试样的耐腐蚀性能,本文采用电化学测试法和中性盐雾腐蚀试验。
使用CHI660D型电化学工作站测试涂层和基体在3.5%(质量分数)NaCl 溶液中的动电位极化曲线,并进行对比分析。使用AB胶封装试样并保留1 cm2的工作面积,封装后使用丙酮、无水乙醇、去离子水进行清洗,再进行电化学腐蚀测试。电化学工作站采用标准三电极体系,工作电极为测试试样,铂电极为辅助电极,参比电极为饱和甘汞电极。极化曲线电位扫描范围为-1~1 V,扫描速率5 mV/s。
采用MC-952C 型盐雾试验机对试样进行中性盐雾腐蚀测试,测试周期为30 d。根据GB6468-86中性盐雾腐蚀标准,实验采用5%(质量分数)的NaCl溶液,测量盐雾箱内溶液pH值为6.9,盐雾箱内温度保持在35 ℃左右。盐雾腐蚀实验参数:喷雾速率为0.025 mL·cm-2·h-1,压力为0.07~0.15 MPa,相对湿度为(94±4)%。试样经盐雾腐蚀不同时间段(3,6,12,18,24 和30 d)后使用去离子水清洗称重,同时由于喷涂涂层经盐雾腐蚀后并不能形成连续致密的保护膜而易于脱落,因此采用腐蚀失重法评定WC-12Co涂层和WC-10Co4Cr 涂层的耐腐蚀性能。盐雾腐蚀后的试样使用自带能谱(EDS,XMS60S)的扫描电镜(SEM,Quanta200)和X射线衍射仪(XRD,BurkerD8-ADVANCE)进行检测与分析。
2 结果与讨论
2.1 WC-Co涂层微观形貌和物相组织
从图1a 和c 可以看出,两种WC-Co 涂层与TC18 钛合金基体结合良好,WC-12Co 涂层厚度约为150 μm,WC-10Co4Cr 涂层厚度约为170 μm。能谱分析结果(图1b 和d)显示两种涂层中各元素质量分数与其喷涂粉末中各元素质量分数基本一致,且不存在其他杂质元素,说明喷涂粉末纯净,在喷涂过程中实验条件良好而未被其他杂质元素污染。从低倍横截面显微结构SEM图可以看出,两种涂层组织均匀致密,没有明显的分层现象。在高倍放大的显微组织中,灰白色大小不一的多边形颗粒为WC颗粒,四周包裹着颜色较深的粘结相金属。硬质WC颗粒均匀地镶嵌在粘结相中,从而确保涂层较高的硬度,Co和CoCr作为粘接相将WC颗粒粘结在一起,使得两种涂层具有良好的韧性。
2.2 TC18基体和WC-Co涂层力学性能
图2a 和b 分别为WC-12Co 和WC-10Co4Cr 涂层的XRD图谱。从图中可以看出,硬质相WC为两种涂层的主要相,且其峰位基本一致,同时该硬质相的存在使得涂层拥有较高的硬度和耐磨性。在WC-10Co4Cr 涂层XRD图谱中出现了较弱的CoCr 相衍射峰,表明在热喷涂过程中Cr 和Co 形成了固溶体。两种涂层均存在W2C相,在WC-12Co涂层中还出现脆性η相(Co6W6C),说明在HVOF 喷涂过程中WC存在一定的脱碳现象,在相同的热喷涂工艺参数下,WC-10Co4Cr 粉末较WC-12Co 粉末熔化更充分、脱碳程度更低。
图3a 为基体与涂层表面平均硬度值矩形图,TC18 基体平均显微硬度为HV0.3336.4,两种涂层的平均显微硬度都明显高于基体,其中WC-12Co涂层为HV0.31177.2,WC- 10Co4Cr 涂层为HV0.31258.8。
WC-Co 涂层的高硬度主要是由于涂层中大量分布的硬质WC相,HVOF 具有相对低的喷涂速率和相对高的喷涂温度的特点,可以有效地降低WC在喷涂过程中脱碳分解和氧化,因而涂层中WC颗粒的组织和形态基本得到保留而显示出高的硬度,高的表面硬度意味着两种WC-Co 涂层拥有良好的耐磨性。
纳米压入测试结果如图3b 所示,可以看出,WC-12Co 和WC-10Co4Cr 涂层的加载-卸载曲线与横坐标轴所围成的面积均小于TC18 钛合金基体的,说明两种涂层的形变功均小于基体的形变功,即WC-Co涂层较TC18 基体更难发生塑性变形。弹性模量通常可以用来表征涂层的弹性变形行为,测得WC-12Co 涂层的弹性模量值为355 GPa,WC-10Co4Cr 涂层的弹性模量值为391 GPa,基体的弹性模量值则为102 GPa,这表明WC-Co 涂层抵抗弹性变形的能力远大于TC18钛合金,即刚度更大。
2.3 电化学腐蚀性能
图4 所示为WC-Co涂层和TC18 基体在3.5%的NaCl 溶液中的电化学极化曲线。两种涂层的电化学极化曲线变化相类似,但与基体存在明显不同,WC-Co 涂层极化曲线随着测试电位的增加呈现指数增长趋势,然后趋于平缓并基本保持不变。这个过程中涂层首先受到腐蚀溶液的腐蚀,然后在其表面形成钝化膜,因而腐蚀电流密度基本保持不变[13]。电化学测试结果表明,TC18 钛合金基体、WC-12Co 涂层和WC-10Co4Cr 涂层的自腐蚀电位及腐蚀电流密度分别为-0.167 V,7.136×10-9 A/cm2;-0.621 V,5.257×10- 7 A/cm2;-0.495 V,1.573×10- 7 A/cm2。WC-12Co涂层和WC-10Co4Cr 涂层与TC18 基体相比,自腐蚀电位分别降低了0.454 和0.328 V。自腐蚀电位是电化学腐蚀热力学参数,表征材料在溶液中失电子难易程度,由此表明两种涂层热力学稳定性低于基体,而且两种WC-Co 涂层的腐蚀电流密度高于基体腐蚀电流密度两个数量级。这都说明涂层相对于基体更容易被腐蚀,然而由于两种WC-Co涂层均匀致密并紧密的覆盖在TC18 钛合金基体表面,因而对基体具有一定的物理保护作用。同时在电化学腐蚀过程中WC-Co涂层最先受到腐蚀,并且在涂层表面形成致密的氧化膜,因此能有效地阻止进一步的腐蚀而保护TC18 钛合金基体。与WC-12Co 涂层相比,WC-10Co4Cr 涂层具有相对高的自腐蚀电位和低的腐蚀电流密度,因而拥有更好的耐蚀性能而能够更好地保护基体。
2.4 盐雾腐蚀性能
图5 所示为两种WC-Co 涂层在NaCl 中性盐雾中腐蚀失重随时间变化的情况。从腐蚀失重曲线分析可以看出WC-12Co 涂层的失重量明显大于WC-10Co4Cr 涂层,同时两种涂层在5%NaCl盐雾中腐蚀速度较为平均,失重变化曲线大致呈线性变化。
根据失重试验数据计算得出,WC-12Co 和WC-10Co4Cr 涂层的单位面积平均腐蚀速率分别为0.2 mg·cm-2·h-1和0.033 mg·cm-2·h-1。这表明在NaCl腐蚀介质中,WC-10Co4Cr 涂层的耐蚀性高于WC-12Co涂层。
2.5 WC-Co涂层盐雾腐蚀物相组织及形貌
图6a 和b 是WC-12Co 涂层和WC-10Co4Cr 涂层盐雾腐蚀30 d 后的XRD图谱。从图6a 可以看出,WC-12Co涂层腐蚀层主要含WC相和Co相,而在腐蚀过程中生成的CoO、WO3氧化膜已不存在,这是由于这两种生成的氧化膜耐蚀性能不强,在盐雾腐蚀过程中易出现点蚀而逐渐破坏脱落。WC-10Co4Cr涂层经盐雾腐蚀后的物相组织如图6b 所示,涂层主要含有WC相、CoCr2O4和Cr2O3相,但在腐蚀过程中形成的稳定Cr2O3氧化物并不能完整的覆盖于涂层表面,裸露的Co 粘结相和WC会发生腐蚀,生成的CoO和WO3并不稳定而会很快破裂脱落。
WC-Co 涂层经30 d 中性盐雾腐蚀后的截面微观形貌如图7a 和c 所示,可以看出,两种涂层中腐蚀介质并没有进一步向内扩散,涂层的内部保持均匀致密而并未受到腐蚀,同时WC-12Co涂层的腐蚀层厚度明显大于WC-10Co4Cr 涂层腐蚀层厚度。从图7a 可以看出WC-12Co涂层腐蚀层形貌非常粗糙,存在着大量的裂纹、孔洞等缺陷。结合腐蚀区域EDS分析(图7b)和物相组成分析(图6a),这是由于当腐蚀介质接触到涂层时,优先腐蚀自腐蚀电位更高的Co 粘结相,而且涂层中的Co6W6C 相也易于腐蚀而形成CoO 和WO3 腐蚀产物,伴随着粘结相不断腐蚀,最终导致WC颗粒和CoO、WO3腐蚀产物大量的脱落,形成裂纹、孔洞等缺陷。图7c 所示为WC-10Co4Cr 涂层截面腐蚀形貌,与WC-12Co 涂层相比,腐蚀层厚度更小、孔洞裂纹等缺陷较少、形貌更为平整。结合腐蚀区域EDS分析(图7d) 和XRD物相分析(图6b),这是由于在腐蚀过程中形成了稳定的Cr2O3陶瓷钝化相,从而提高了WC-10Co4Cr 涂层中粘结相的自腐蚀电位,延缓了腐蚀介质向内部扩散。因此,两种WC-Co 涂层都能有效地提高TC18 钛合金在NaCl 盐雾中的耐蚀性能,其中WC-10Co4Cr涂层显示出更好的耐盐雾性能。
3 结论
(1) 使用HVOF技术在TC18 钛合金上制备了组织致密、缺陷较少的WC-12Co 涂层和WC-10Co4Cr涂层,涂层与基体结合良好。两种涂层的显微硬度和弹性模量均明显高于基体,其中WC-10Co4Cr 涂层拥有更高的显微硬度和弹性模量。
(2) 两种WC-Co涂层在电化学腐蚀测试过程中表面均能形成氧化膜而阻止腐蚀溶液向内部腐蚀,有效地提高了基体耐蚀性,且WC-10Co4Cr 涂层显示出更优的耐蚀性能。
(3) WC-12Co 涂层的腐蚀失重、平均腐蚀速率和截面腐蚀层深度均明显大于WC-10Co4Cr 涂层,WC-Co涂层的腐蚀机理是腐蚀介质不断腐蚀涂层中的粘结相并向其内部扩散,其耐蚀性能主要取决于粘结相,添加少量的Cr能有效提高WC-Co涂层的耐蚀性,因而WC-10Co4Cr涂层抗盐雾腐蚀性能更好。
免责声明:本网站所转载的文字、图片与视频资料版权归原创作者所有,如果涉及侵权,请第一时间联系本网删除。
-
标签: TC18钛合金, 超音速火焰, 喷涂WC-Co-Cr涂层, 微观结构, 耐蚀性能
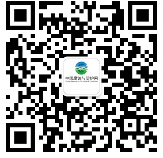
官方微信
《中国腐蚀与防护网电子期刊》征订启事
- 投稿联系:编辑部
- 电话:010-62313558-806
- 邮箱:fsfhzy666@163.com
- 中国腐蚀与防护网官方QQ群:140808414