0 引言
随着对易挥发有机物(VOC)控制日益严格,国内外对水性涂料原材料、成品及应用领域的研究力度得到空前提高。水性环氧涂料因为其施工适应性好、对很多种类的基材有较高的附着力、可以在常温以及潮湿的环境中固化等优点而被大量使用。但水性环氧涂料本身也存在缺陷:首先,由于水的表面张力较大,水性环氧涂料对于钢材的润湿性较差,容易出现缩孔、附着力差的问题;其次,在乳液制备的过程中,通常会在树脂链段上引入大量的亲水性基团,会大大降低水性环氧涂层的交联密度,从而影响了涂层的粘结强度;同时,大量亲水性基团的引入和交联密度的降低会导致涂层耐腐蚀性能降低。本研究从水性环氧乳液、水性环氧固化剂、颜填料等方面进行研究,通过耐腐蚀性能测试试验,开发出防腐性能良好的双组分水性环氧涂料配方。
1 试验部分
1.1 主要原材料和设备
水性环氧乳液A、B、C;水性环氧固化剂D(高活性聚胺)、E(改性脂肪加成物),某树脂公司;乙二醇丁醚、湿法绢云母粉、硫酸钡、滑石粉、气相二氧化硅,天津市江天化工技术有限公司;三聚磷酸铝、磷酸锌,北京之途化工有限公司;石墨烯,深圳天元羲王材料科技;消泡剂、润湿剂、分散剂、流平剂、防闪锈剂、增稠剂、杀菌剂,德国BYK。
QXD涂料细度计、FED115烘箱、FA2004N电子天平、高速分散机等。
1.2 涂料的制备
按照表1配方中的量,首先加入去离子水、分散剂、消泡剂和润湿剂,高速搅拌均匀,随后加入湿法绢云母、硫酸钡、滑石粉、气相二氧化硅和石墨烯,搅拌均匀后,进行研磨,直至磨出的水浆细度低于60 μm。随后向磨好的水浆中加入防闪锈剂、杀菌剂和环氧树脂乳液(转速小于1 000 r/min,温度低于60 ℃),边搅拌边加入增稠剂调节体系黏度。最后用200目滤网过滤,得到A组分。将水性环氧固化剂和丙二醇甲醚混合均匀,200目滤网过滤制备得到B组分。
表1 水性环氧涂料配方
原材料 质量分比/% 原材料 质量分比/% A组分 硫酸钡 15.0-20.0 去离子水 20.0~25.0 滑石粉 15.0~20.0 分散剂 0.5~1.0 气相二氧化硅 0.2~0.3 润湿剂 0.1~0.5 石墨烯 0.3~1.0 消泡剂 0.1~0.5 三聚磷酸铝 1.0~5.0 流平剂 0.1~0.5 磷酸锌 3.0~8.0 防闪锈剂 0.3~0.5 环氧树脂乳液 30.0~40.0 杀菌剂 0.3~0.5 B组分 增稠剂 0.3~0.5 水性环氧固化剂 60.0~80.0 湿法绢云母 10.0~20.0 乙二醇丁醚 20.0~40.0
1.3样板的制备
按照标准要求,准备马口铁片、喷砂钢板和试棒。将1.2中制备得到的A、B组分按照一定比例混合均匀后,静置20 min消除气泡,随后进行施工作业。用于测试力学性能的涂膜厚度为25 μm,用于测试耐腐蚀性能的涂膜厚度为200 μm以上(3 ~ 4道)。将样板放置在室温情况下养护7 d,随后进行性能测试。
2 结果与分析
2.1 水性环氧乳液与水性环氧固化剂的确定
将水性环氧乳液A、B、C与固化剂D、E分别按照环氧基与活泼氢物质的量比为1∶1进行试验,通过对比清漆的综合性能,筛选综合性能最优的树脂固化剂体系,试验结果见表2。
表2 清漆的综合性能对比
从表2结果可以看出:固化剂D活性较高,表干速度较快,涂层上强度较快,但涂层较脆,柔韧性和耐冲击性较差;水性环氧树脂乳液B、C的分子量较大,同时在链段中含有大量极性基团和甲基,能赋予涂层良好的附着力和柔韧性。但C的分子量过大,导致其耐腐蚀性能差;水性环氧树脂A的分子量较小,柔韧性相对较差。因此,本文选择水性环氧树脂乳液B和固化剂E作为树脂固化剂体系。
随后将水性环氧乳液B和水性环氧固化剂E按照环氧基与活泼氢的物质的量比在(0.8 ~ 1.2)∶1.0范围进行试验,测试清漆的综合性能,试验结果见表3。
表3 清漆的综合性
表3 清漆的综合性能
测试项目 |
n(环氧基)∶n(活泼氢) |
|||
0.8∶1.0 |
1.0∶1.0 |
1.1∶1.0 |
1.2∶1.0 |
|
耐冲击性/cm |
40 |
50 |
50 |
40 |
弯曲性能/mm |
2 |
1 |
1 |
2 |
划格试验/级 |
2 |
1 |
1 |
2 |
耐50 g/L NaCl(常温,240 h) |
起泡 |
无变化 |
无变化 |
无变化 |
耐50g/L H2SO4 (常温,24 h) |
起泡 |
无变化 |
无变化 |
无变化 |
耐50g/L NaOH (常温,168 h) |
起泡 |
无变化 |
无变化 |
起泡 |
耐盐雾(300 h) |
起泡 |
无变化 |
无变化 |
无变化 |
根据表3可以看出:n(环氧基)∶n(活泼氢)为0.8∶1.0时,涂膜的耐介质性能不理想,这是因为固化剂过量,氨基含量过剩,从而导致耐介质性能下降,同时,固化剂过量也会影响涂膜的机械性能下降。n(环氧基)∶n(活泼氢)为1.2∶1.0时,环氧基团过量的较多,降低了涂膜的交联密度,从而影响涂膜的防腐性能。综合考虑,成膜物体系选择n(环氧基)∶n(活泼氢)为1.0∶1.0。
2.2 颜填料体系的选择
水性环氧防腐涂料体系应该选用吸油量低、化学稳定性及耐水性好的颜填料体系。石墨烯有热稳定性好、耐化学介质、导热性好、硬度高等优点,将石墨烯加入到涂料中可以提高涂料的耐热性、耐冲击性以及耐磨性。同时,片状的石墨烯在涂料干燥过程中会定向排列,相互交叠覆盖,有效屏蔽H2O、CO2、Cl-1等,使其不能直接透过鳞片,被迫迂回渗透,减慢了离子的渗透速度,起到“迷宫效应”,并截断了涂层中的毛细管微观通道,降低透过率,提高涂层的防腐蚀能力。三聚磷酸铝具有“双重防锈”机理,解聚后得到的三聚磷酸根离子(P3O105-)对Fe3+具有很强的鳌合力,在基材表面形成防腐蚀性能优异的钝化膜,阻止金属基材的进一步腐蚀。磷酸锌在金属受到腐蚀的时候,可以与Fe3+形成络合物沉淀层,同时锌离子与阴极OH-反应,得到Zn(OH)2,从而起到阴极极化作用,同时还能够与涂料中的极性基团络合,提高了涂层与基材之间的附着力和涂层的防腐蚀能力。本研究使用上述3种填料进行复配试验(见表4),通过机械性能和耐腐蚀性能综合考虑,得出最佳添加配方(见表5)。从表5结果可以看出,三聚磷酸铝、磷酸锌和石墨烯添加量过大会导致填料在涂层中形成团聚,影响涂层性能。本研究采用方案4。
表4 填料添加正交试验 %
试验编号 |
填料 |
||
三聚磷酸铝 |
磷酸锌 |
石墨烯 |
|
1 |
1 |
3 |
0.3 |
2 |
1 |
5 |
0.5 |
3 |
1 |
8 |
1.0 |
4 |
3 |
3 |
0.5 |
5 |
3 |
5 |
1.0 |
6 |
3 |
8 |
0.3 |
7 |
5 |
3 |
1.0 |
8 |
5 |
5 |
0.3 |
9 |
5 |
8 |
0.5 |
表5 颜填料对涂层防腐性能影响
项目 |
试验编号 |
||||||||
1 |
2 |
3 |
4 |
5 |
6 |
7 |
8 |
9 |
|
耐冲击性/cm |
50 |
50 |
40 |
50 |
40 |
40 |
40 |
40 |
40 |
弯曲性能/mm |
1 |
1 |
2 |
1 |
2 |
2 |
2 |
2 |
2 |
附着力/MPa |
13 |
11 |
5 |
12 |
4 |
8 |
5 |
6 |
7 |
耐50 g/L NaCl (常温,720 h) |
无变化 |
无变化 |
起泡 |
无变化 |
起泡 |
起泡 |
起泡 |
无变化 |
起泡 |
耐50g/L H2SO4 (常温,360 h) |
起泡 |
起泡 |
起泡 |
无变化 |
起泡 |
起泡 |
起泡 |
无变化 |
起泡 |
耐50g/L NaOH (常温,360 h) |
无变化 |
无变化 |
起泡 |
无变化 |
起泡 |
无变化 |
起泡 |
无变化 |
起泡 |
耐盐雾(1 000 h) |
无变化 |
无变化 |
起泡 |
无变化 |
起泡 |
无变化 |
起泡 |
无变化 |
起泡 |
2.3 助剂的选择
制备水性涂料过程中需要添加较多种类的助剂来起到提高贮存稳定性、减少针孔缩孔的产生以及提高表观效果的作用,筛选出合理的水性涂料助剂十分重要。水性涂料常用助剂包括:分散剂、润湿剂、消泡剂、成膜助剂、增稠剂、杀菌剂等。本研究选用的分散剂是一种含颜料亲和基团的高分子量嵌段共聚物溶液,该款分散剂通过空间位阻稳定作用使得颜料解絮凝,添加量为A料质量的0.5%时可以得到理想效果。本研究的防沉触变剂选择的是气相SiO2,添加量为0.2% ~ 0.3%时,可以使涂料有一定的触变性,起到防沉和防流挂的作用。本文采用的杀菌剂是40%的BIT杀菌剂,可以起到长效杀菌防霉的作用。
2.3.1 消泡剂体系的选择
在涂料制备、生产及施工过程中,容易混入大量的气泡,会导致涂层表面出现缩孔或者针孔,影响到涂膜性能。水具有大的表面张力,更容易产生气泡并且难以消除,因此选择合适的消泡剂体系对于水性涂料来说十分重要。本研究选择市面上常见的3款不同类型的消泡剂进行对比试验,结果见表6。从试验可以看出,有机硅类消泡剂消泡效果最差。矿物油类消泡剂与体系相容性好,可以起到快速破泡的作用,但是对于消除微泡效果较差。聚合物类消泡剂消除气泡效果好,但是破泡速度慢,现场施工容易出现问题。综合考虑消泡效果和破泡速度两方面,本研究采用0.3t% 消泡剂B+0.5%消泡剂C作为消泡剂体系。
表6 消泡剂添加量对涂料体系的影响
消泡剂 |
添加量/% |
消泡效果 |
涂膜效果 |
A(有机硅类) |
0.1 |
破泡慢,大量气泡 |
表面大量针孔 |
0.3 |
破泡慢,大量气泡 |
表面大量针孔 |
|
0.5 |
破泡慢,大量气泡 |
缩孔 |
|
0.7 |
破泡慢,微泡 |
缩孔严重 |
|
B(矿物油类) |
0.1 |
破泡快,微泡 |
表面有针孔 |
0.3 |
破泡快,微泡 |
表面有针孔 |
|
0.5 |
破泡快,微泡 |
表面有针孔 |
|
0.7 |
破泡快,微泡 |
表面有针孔和轻微缩孔 |
|
C(聚合物类) |
0.1 |
破泡慢,微泡 |
表面有针孔 |
0.3 |
破泡慢,少量微泡 |
表面有针孔 |
|
0.5 |
破泡慢,无气泡 |
表面无针孔 |
|
0.7 |
破泡慢,无气泡 |
缩孔严重 |
2.3.2 成膜助剂的选择
涂料成膜助剂可以降低树脂的最低成膜温度,从而有利于固化剂分子扩散,帮助最优化涂膜的性能。同时,成膜助剂的存在可以提高涂膜的开放时间,有利于防止痱子、针孔等问题,因此选择合适的成膜助剂对于水性涂料来说至关重要。水性环氧涂料常用的成膜助剂有:丙二醇甲醚、丙二醇苯醚、乙二醇丁醚等。本研究从试验效果和环保两方面考虑,选择丙二醇甲醚、丙二醇苯醚、乙二醇丁醚按照5%添加量进行性能测试,试验结果见表7。从表7可以看出,丙二醇甲醚挥发速度快,涂膜表干快,容易导致涂膜表观粗糙、附着力下降等问题。丙二醇苯醚沸点高,挥发慢,导致涂膜表干时间过长,会影响现场施工进度。添加乙二醇丁醚的涂膜表干时间适中,涂膜表观平滑且不影响涂层的附着力,因此本课题选择乙二醇丁醚作为成膜助剂。
表7 成膜助剂对涂层性能的影响
成膜助剂类型 沸点/℃ 表干时间/min 涂膜外观 附着力/级 丙二醇甲醚 120 10 粗糙 2 丙二醇苯醚 243 100 平滑 1 乙二醇丁醚 151 40 平滑 1
3 结语
本研究通过对水性环氧树脂乳液体系、固化剂体系、n(环氧基)∶n(活泼氢)、颜填料体系、助剂体系的筛选对比试验,得出双组分水性环氧涂料的基本配方。其中,分散剂、消泡剂、成膜助剂和防沉触变剂气相二氧化硅的选择和添加量的优化,使得涂层具有良好的表观和贮存稳定性。对防锈填料三聚磷酸铝、磷酸锌和石墨烯进行复配,赋予了涂层优良的防腐性能。
表2 清漆的综合性能对比
性能 |
AD |
BD |
CD |
AE |
BE |
CE |
表干时间/min |
5 |
10 |
12 |
30 |
40 |
80 |
耐冲击性/cm |
40 |
40 |
40 |
40 |
50 |
50 |
弯曲/mm |
2 |
2 |
2 |
2 |
1 |
1 |
附着力/级 |
2 |
2 |
2 |
1 |
1 |
1 |
耐50 g/L NaCl (常温) |
3 d后起泡 |
3 d后起泡 |
5 d后起泡 |
8 d后起泡 |
12 d后起泡 |
5 d后起泡 |
免责声明:本网站所转载的文字、图片与视频资料版权归原创作者所有,如果涉及侵权,请第一时间联系本网删除。
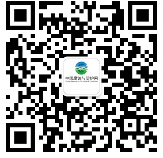
官方微信
《中国腐蚀与防护网电子期刊》征订启事
- 投稿联系:编辑部
- 电话:010-62313558-806
- 邮箱:fsfhzy666@163.com
- 中国腐蚀与防护网官方QQ群:140808414