钛合金因具有重量轻、比强度高、耐蚀性好等优良特性,已广泛应用于航空航天、船舶、机械、化工等领域。但是其表面硬度低,耐磨性差,耐腐蚀性不理想,使钛合金在许多情况下难以满足实际应用的要求,严重阻碍了钛合金的进一步应用。目前,提高钛合金耐磨性的表面处理技术主要有离子注入、化学镀、激光熔覆、等离子喷涂、气相沉积和微弧氧化等。每一种单一表面技术都有其一定的局限性。近年来,采用复合处理技术,对钛合金表面改性,使得其性能逐步提高,解决了钛合金表面强化问题。因此,本文针对目前几种钛合金表面单一及复合强化处理方法进行阐述。
1 钛合金耐磨表面改性和涂层技术
1.1 离子注入离子注入
技术起始于20世纪60年代,该技术通过在真空、低温下将高能带电离子快速射入到金属近表层,使离子与基体发生一系列复杂反应,进而形成新的表面改性合金层,新形成的合金层与基体结合力强,耐磨效果提高显着。该工艺的突出优点在于既能保持金属基体自身性能、不改变材料宏观尺寸、环保无公害,又可以大幅度地改善材料表面的耐腐蚀性和抗氧化性等。离子源既可是非金属离子,如B,C,N等,又可是Zr,Mo,Re等金属离子。就非金属离子注入而言,当将B,C,O等注入钛合金表面后,会形成相应的硬质化合物(TiB,TiC,TiO),使得材料表层硬度和耐磨性得以提高。罗勇等将N3-注入Ti6Al4V基体表面以提高材料力学性能,生成的TiN薄膜使得钛合金表面的显微硬度明显提高,其平均硬度提高了约25%,耐磨性为钛合金基体的2.5倍。
1.2 化学镀
化学镀也被称为无电解镀或自催化镀,即在没有外加电流的前提下,利用金属的自催化作用,同时借助镀液中的还原剂,将游离的金属离子还原成金属,并均匀沉积到待镀零件表层的一种表面镀覆技术。目前,针对钛合金耐磨改性方面,化学镀已由最初的单一化学镀Ni逐步发展到多种金属与合金及复合化学镀的表面处理工艺,如化学镀Cu、Ag、Au及Sn等。复合化学镀是基于原有镀液基础上加入如Al2O3,Cr2O3,SiC等固体硬质颗粒,使其在外力下与金属发生共沉积,从而获得比不加微粒的镀层更好的力学性能。
Zangeneh-Madar等尝试用化学镀技术在钛合金表面制作Ni-P-聚四氟乙烯(PTFE) 复合涂层,并研究了镀液浓度、温度和表面活性剂浓度对镀层形成产生的影响,同时也探究了样品的摩擦磨损特性。结果表明,Ni-P和PTFE的共沉积可以明显降低镀层的摩擦系数,减少磨损量,提高润滑性能。
相对于电镀,化学镀镀层具有均匀致密、无需外加电流供应、操作过程简单、可在塑料等非导体上沉积镀层等优点,且化学镀污染小、成本低。目前,化学镀由于可制备具有良好抗蚀、耐磨的膜层,在航空航天、汽车、机械、化工等领域都得到广泛应用。
1.3 激光熔覆
激光熔覆技术是一种将激光技术与金属热处理技术相结合的表面改性技术。该技术通过预先在基体表面喷涂或粘接粉末材料,或将粉末与激光束同步输送,然后用高能量密度激光束照射材料表面,使得粉末材料熔化,在基体金属上形成良好的冶金结合层。由于激光熔覆时,基材熔化部分很少,对基体性能基本没有影响。目前,已经采用的可改善钛合金耐磨的熔覆材料并不多,常用的有硬质陶瓷 (SiC,TiC,Al2O3,TiN和TiB2等)、镍基自熔合金和陶瓷/合金几类,其中单一硬质陶瓷激光熔覆层由于脆性大,与钛合金热膨胀系数不匹配,产生很高的残余应力,易导致熔覆层产生裂纹甚至脱落。所以常用陶瓷/合金来改善钛合金的耐磨性,其中合金多用自熔NiCrBSi合金。
Weng等在TC4钛合金表面激光熔覆不同含量的SiC,在整个处理过程中,SiC与基体反应生成Si5Si3和TiC,该反应物的生成显着提高了基体钛合金的硬度和耐磨性。实验结果表明,钛合金激光熔覆SiC后的涂层硬度达到1200HV,是基体硬度的3倍多,涂层耐磨性能也提高了18.4~57.4倍;且随着SiC添加含量的增加(低于20%(质量分数)),涂层硬度逐步提高到1300~1600 HV,耐磨性能也进一步提高。
1.4 热喷涂
热喷涂是使用某种热源对喷料加热,待喷涂材料呈现可流动状态后被焰流加速,再喷溅到经前处理过的基体表面上,沉积得到具有特定功能涂层的加工方法。钛合金耐磨改性常用的喷料一般为非金属材料镍包石墨,单质金属材料Al、Ni及合金材料TiN,NiCrAl,MCrAlY等。热喷涂处理后,涂层与基体界面处平直,结合较好,并在随后的高温氧化过程中,喷涂材料与基体发生相互扩散,形成冶金结合的扩散层,使耐磨性能大大提高。Huang等曾介绍,在钛合金表面进行热喷涂铝涂层,可在基体表面沉积一层保护层,但该保护层在低温下坚硬且具有脆性,由于热膨胀系数的不匹配性,易发生剥落。
1.5 物理气相沉积
物理气相沉积技术是在真空条件下,采用物理方法,将材料源-固体或液体表面气化成气态原子、分子或部分电离成离子,并输运至基体表面形成固相薄膜的技术。物理气相沉积技术主要包括蒸发、溅射和离子镀等,既可制备金属膜,也可制备化合物膜。
溅射和离子镀是两种常见的物理气相沉积技术,各具优势。离子镀具有韧性好、离子能量高、结合强度大等优点,然而制备的薄膜容易含有熔滴等缺陷。溅射的优点包括:操作温度低、膜层成分可控、材料变形较小、可镀靶材选择范围广等;但是膜层沉积速率较慢。奚运涛等采用磁控溅射和离子镀的方法在TC4钛合金表面制备了TiN膜,比较其摩擦磨损性能。结果表明,多弧离子镀和磁控溅射TiN膜层均提高了TC4钛合金表面的耐磨性能,多弧离子镀方法得到的膜层性能更好。
综上所述,单一钛合金表面耐磨改性技术虽可显着提高钛合金的显微硬度和耐磨性能,但是一些缺点不可避免,例如离子注入技术注入层的厚度过浅,仅在微米级别范围内,使用受限,同时试样尺寸也有一定的限制。化学镀层与基体结合强度不高,镀层薄,易产生氢脆。激光熔覆技术工艺参数控制较繁琐,且熔覆层中容易产生裂纹和气孔。热喷涂技术不适合处理不耐高温基体,且喷得的涂层结合力低、孔隙率大、均匀性差等。以下介绍的一些复合技术,可以对上述缺陷进行进一步的完善。
2 钛合金耐磨复合处理技术
当前,在日益发展的工业需求的驱使下,复合涂层技术将逐渐替代单一涂层技术。微弧氧化又称微等离子体氧化,该技术可在轻金属Al、Mg、Ti以及相应的合金表面,借助高电压、高电流及瞬时高温的作用,制备出具有良好冶金性能的陶瓷层。陶瓷层主要成分是基体原位生长的氧化物,同时电解液成分也会参与到微弧氧化膜层中。微弧氧化过程中的电参数 (如溶液配方、电压电流、占空比、脉冲频率等),都对微弧氧化膜的制备和微观结构有很大的影响。该方法工艺安全、操作简易、溶液环保,同时也具有其他处理技术无法比拟的工艺简单、膜层均匀致密、对工件尺寸限制较少等优点。
钛合金微弧氧化膜具有硬度高、膜基结合强度高、耐蚀、耐磨等优点,但其膜层表面较为粗糙,且疏松多孔,摩擦系数较大,从而降低了膜层的耐磨性,缩短了氧化膜的使用寿命,不利于钛合金在磨损环境下的应用。目前,针对改善钛合金微弧氧化膜这一缺陷,俄罗斯科学院的一些研究院所开展了很多工作,而国内对于这一问题的关注才刚刚起步。本文主要介绍在微弧氧化技术的基础上,结合封孔法、镀铝法、脉冲电子束法、水热法和电泳沉积法等进行复合处理的相关技术。
2.1 微弧氧化+封孔法
由于钛合金微弧氧化膜表面疏松多孔,一些研究者们设法通过物理、化学或者电化学方法,将润滑物质填充到微弧氧化膜的孔隙中,以达到自润滑的效果。其中聚四氟乙烯 (PTFE) 热稳定性好,在各种环境中具有优良的化学稳定性,是一种理想的自润滑材料。
赵晖等将PTFE粒子填充到钛合金微弧氧化膜层孔隙中进行固化处理,制备PTFE复合自润滑膜。在封孔处理后,扫描电镜 (SEM) 观察结果显示复合膜孔洞明显减少,表面形貌更为平整;在随后的摩擦磨损实验中,微弧氧化膜的摩擦系数约为0.4,而经封孔处理的复合膜的摩擦系数仅为0.15。杜楠等在微弧氧化电解液中添加微量Cr2O3粒子,通过封孔法,也使钛合金微弧氧化复合膜的耐磨性得以提高。目前,封孔法使用的封孔剂多为绝缘有机化合物,因此在导电材料的应用上限制较多。同时,封孔法处理结构复杂、尺寸较大的零件时,耗时较长,也很难涂覆到位。
2.2 微弧氧化+水热法
水热法是在密闭的容器里盛有反应介质,利用热源对容器进行连续加热,使容器内部达到高温和高压的状态,在高温高压作用下,难溶或不溶的物质会发生溶解并进一步重结晶。
Vangolu等探究了TC4钛合金经微弧氧化与水热技术复合改性膜的耐磨性能。与微弧氧化处理的Ti6Al4V相比,复合膜为含有羟基磷灰石的TiO2层。在载荷为1 N、速度为6.5 cm/s的情况下进行摩擦时,复合处理使膜层摩擦系数由0.6降到0.4,磨损率也由0.25降低到0.18,明显提高了膜层的耐磨性。但该复合膜层在高载荷下耐磨性能减弱,不适用于在高负荷状态下应用。
2.3 微弧氧化+脉冲电子束
脉冲电子束 (HCPEB) 表面处理技术以高速电子作为载体,在非常短的时间内将入射能量作用于材料的表面,并导致一系列现象,包括熔化、冷凝、汽化、增强、扩散等,从而获得其他热处理难以实现的物理、化学和力学性能。利用HCPEB法在钛合金微弧氧化膜上制备复合改性层,属于涂层重熔范畴,即预先制备出微弧氧化涂层,然后对氧化膜施加HCPEB,进行电子束重熔,从而可以提高膜层的均匀致密性、晶粒细化程度、膜基结合强度、耐磨、耐蚀等特性。
杜春燕采用HCPEB法处理钛合金微弧氧化膜,SEM观察显示处理过的微弧氧化膜孔洞、颗粒特征明显消失,硬度最大可达到1695 HV,且磨粒磨损迹象减轻。但是,复合膜表面、截面都存在一定的裂纹,进而导致膜层结合强度降低。同时,HCPEB法对微弧氧化膜粗糙度要求较高。目前,将HCPEB与MAO结合的例子不多,相关的研究也较少。
2.4 微弧氧化+镀铝
铝合金较钛合金而言,有很多相似的性能,如它们均属于阀金属,应用领域相似,密度低,比强度高,在阀金属领域也是应用较广的两种金属。但钛合金和铝合金经微弧氧化处理以后的氧化物性能差异很大。钛合金微弧氧化后形成氧化膜的主要组成是TiO2 (金红石和锐钛矿);铝合金微弧氧化的主要产物为Al2O3 (α-Al2O3和γ-Al2O3[43])。Al2O3的硬度值在1200~1800 HV之间,明显高于TiO2的硬度值(550~1050 HV);与此同时,TiO2韧性不足,γ-Al2O3则具有高结构性和韧性。因此,在硬度和耐磨性方面,钛合金微弧氧化膜都不如铝合金微弧氧化膜。若能将镀铝技术与微弧氧化技术以适当的方法相结合制备出复合涂层,充分发挥两种技术的优点,则可显着改善微弧氧化后钛合金的耐磨、耐腐蚀等性能。同时,拓宽钛合金在航空航天领域的进一步应用。
镀铝层因性能优良,制备方式多样,经济效益可观,原材料Al的资源储量丰富,所以一直是涂层改性技术研究的热点。当前应用于钛合金微弧氧化膜表面镀铝的方法多种多样,常见的与微弧氧化结合的镀铝技术主要有:热浸镀、多弧离子镀和磁控溅射镀铝等。
2.4.1 微弧氧化+磁控溅射镀铝 欧阳小琴等先在TC4钛合金表面进行溅射镀铝,溅射时间为2.5 h,然后对镀层进行微弧氧化30 min,电流密度为5 A/dm2,TC4基体微弧氧化膜及溅射镀铝微弧氧化膜的力学性能对比显示:TC4钛合金的硬度一般约为360HV,微弧氧化后的钛合金硬度达到了基体的1.69倍,而经微弧氧化处理的复合镀层,其硬度达到1700 HV以上,摩擦系数也由0.38降到了0.25。除此之外,附着力分析显示,MSD/MAO复合处理过的镀层结合力要优于单一钛合金微弧氧化层的。
2.4.2 微弧氧化+热浸镀铝 钛合金表面热浸镀铝,在熔融铝剂中,钛合金基体表面会发生一系列反应,包括液态Al向钛合金基体的扩散和相互作用。高温热扩散处理后,金属表面可获得高硬度、耐高温的钛铝合金层。如果结合微弧氧化技术,在钛合金表面制备出多层结构的复合膜,过渡区的存在将大大提高膜层结合性能,涂层的综合性能也会显着增强。
Hu等把热浸镀铝2 min后的纯Ti进行微弧氧化处理,电流密度分别为:正向10 A/dm2,负向5 A/dm2,处理时间分别为10,20,30和40 min,所得膜层呈现清晰的分层结构,外层疏松多孔,内层紧凑致密。随微弧氧化时间的延长,氧化层厚度不断增加,涂层粗糙度始终在1.0~1.2之间;在30 min时,复合涂层粗糙度约为1.1,表面显微硬度达到750 HV,摩擦系数约为0.2,磨损率为0.39;在40 min获得最高的涂层硬度和最佳耐磨性能,平均硬度值达到820 HV,摩擦系数约为0.3,磨损率仅为0.29×10-4。武媛通过热浸镀铝技术在TC4钛合金表面得到钛铝金属间化合物层之后,再进行微弧氧化处理,生成基体/TiAl3合金/TiAl2O5陶瓷膜的梯度复合层;经微弧氧化处理40 min后,表面显微硬度达到980 HV,约为基体硬度的4倍;在载荷50 N,转速60 r/min的条件下,复合膜磨损量仅为基体磨损量的1/4,平均摩擦系数也由基体的0.45降低到0.25。
目前热浸镀铝工艺已经成熟,但仍存在成本高、污染环境等缺点。同时,由于镀液流动性差,难以有效地渗入复杂工件。随着渗铝技术的发展,一些新的渗铝法如电泳扩散喷涂法、真空液相渗铝、热喷涂扩散渗铝、真空蒸镀法等逐渐开始替代热浸镀铝并得到应用。
2.4.3 微弧氧化+多弧离子镀铝 多弧离子镀是离子镀技术的一种,在切削刀具中应用较多,也较为成功。该方法膜层沉积速率快,膜层致密度高,膜基结合强度大。将微弧氧化与多弧离子镀两种技术结合,可大大提高涂层的结合强度,使复合膜层的耐磨性得以增强。
卜彤等在TC4钛合金表面多弧离子镀铝后进行微弧氧化,并探究不同镀铝工艺对复合氧化膜耐磨及耐蚀性能的影响,工艺主要围绕处理温度 (25和250 ℃) 和基体偏压 (-200和-300 V) 展开。其中,多弧离子镀时间为20 min,微弧氧化处理时间为30 min,电流密度为6 A/dm2。研究结果表明,负向偏压的增大和处理温度的升高,均能提高涂层性能,因而在250 ℃、-300 V的条件下,微弧氧化膜获得了最优的耐磨和耐蚀性能,摩擦系数达到了0.801,摩擦磨损体积仅为0.042 m3;点滴实验中,34.47 min时才发生变色效应。目前多弧离子镀铝与微弧氧化复合改性技术还不算成熟,但在耐磨改性方面具有一定的技术优势。随着复合处理工艺的不断优化,钛合金表面耐磨性能将会不断提高。
3 总结与展望
(1) 提高钛合金耐磨性的表面处理技术中,微弧氧化技术因具有制备温度低、设备简单、溶液环保、膜层均匀致密、对工件尺寸形状限制较少等优点,具有明显的技术优势。
(2) 将微弧氧化与其他技术复合,可改善单一微弧氧化技术制备的膜层性能,无论在耐磨、耐腐蚀性能方面。因此,复合技术是未来钛合金耐磨技术的发展方向。
免责声明:本网站所转载的文字、图片与视频资料版权归原创作者所有,如果涉及侵权,请第一时间联系本网删除。
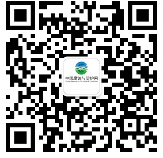
官方微信
《中国腐蚀与防护网电子期刊》征订启事
- 投稿联系:编辑部
- 电话:010-62313558-806
- 邮箱:fsfhzy666@163.com
- 中国腐蚀与防护网官方QQ群:140808414