如何提高发动机叶片的服役寿命,如何评价或预测高强紧固件的服役安全等,是目前国内工业界急需解决的关键工程问题。上述问题的解决,迫切依赖相关基础理论的逐步突破。
金属材料的弹性变形是可恢复的,因此不会引入损伤。对于金属材料的塑性变形,其主要涉及位错的滑移,变形孪生,相变,蠕变等。上述变形机理的交互作用,必然会导致晶体材料内点缺陷,线缺陷,及面缺陷的增殖。这些缺陷随着塑性变形的累积和分布,决定了材料的损伤行为。上述问题的复杂性在于弹性变形和塑性变形存在非线性交互作用。目前,学术上仍缺乏有效的理论或数值手段对金属材料的变形损伤做出定量的表征和预测。
北京科技大学的解清阁副研究员,王沿东教授团队,杨平教授团队,联合广东材料研究所的闫星辰副研究员,爱尔兰圣三一大学的Yin Shuo教授,美国橡树岭国家实验室的An Ke首席科学家和Yu Dunji研究员,芬兰阿尔托大学的Lian Junhe教授,匈牙利罗兰大学的Sidor Jurij教授,上海大学的陈超越副教授,重庆大学的孙丰伟副教授等,通过原位中子衍射表征,微观组织表征,和理论计算,确认了常见工程材料:铝合金和含锰钢的变形损伤机理。相关结论有助于对工程材料的疲劳损伤和缩颈损伤提供损伤判据和定量表征,为疲劳寿命预测提供理论基础。上述成果分别于2020和2022年发表在Acta Materialia上。
铝合金的缩颈失效机理
铝合金近乎弹性各向同性,在与塑性变形的相互竞争中,非常容易产生缩颈现象。而缩颈和塑性变形的位错滑移行为密切关联。通过大量实验,发现缩颈的扩展主要发生在拉伸-压缩疲劳的拉伸卸载阶段,从而最终失效,如图1所示。注意,这里的点阵应变是弹性点阵应变,其可以通过中子衍射来原位测量。而不同点阵应变对应不同的晶粒群(特定<hkl>方向平行于加载轴或垂直于加载轴)。从图1可以发现<111>点阵应变垂直于加载轴对应的缩颈损伤最明显。而该晶粒群是铝合金中损伤最严重的晶粒。
图1 铝合金不同损伤阶段的点阵应变表现:黄色箭头指示缩颈损伤行为
同时,试样缩颈失效后,表面看不到任何孔隙。通过CT测量表明,微孔隙都在材料的内部。如果以试样中心建立笛卡尔坐标系,把孔隙在三维空间的分布按极图的方式投影,发现孔隙的三维空间分布和残余点阵应变分布非常类似,如图2所示。这里,残余点阵应变也表达在极图中。可以看到心部对应沿着轴向的压缩残余应变,而其它孔隙对应拉伸残余点阵应变。该规律的详细机理解释见参考文献1。
图2 缩颈失效导致内部孔隙和残余点阵应变的分布规律
通过介观-宏观尺度的数字孪生仿真(图3),可以看到:铝合金的损伤在介观尺度表现为带状组织形貌,而该形貌主要是由材料内部析出和第二相硬颗粒导致的。图6给出变形微观组织对应的实验测量和计算结果对比。计算表明,第二相颗粒会增加介观尺度的变形非均匀性,从而产生带状组织。
图3 铝合金变形的数字孪生仿真
含锰钢 (Fe-18Mn) 的疲劳损伤机理
钢有强的弹性各向异性,使得其在拉伸时不容易产生缩颈。同时,拉伸/压缩变形时,自由表面与试样心部相比,对应更强的棘轮效应。因此,钢的拉/压疲劳失效位置主要在自由表面。不论是塑性变形还是弹性变形,拉伸都会导致侧向收缩(反泊松比现象除外)。对于含锰钢,在变形的时会发生大量变形孪晶,并且变形孪晶对应针状形貌。该形变孪生行为在拉伸-压缩疲劳过程中有拉压不对称现象(拉伸过程积累的塑性变形组织在压缩时没有完全回复,或反之),其会导致自由表面内,形变孪晶处的缺陷累积。而表面缺陷是疲劳裂纹形核的优先位置。图4右侧,微区1给出典型的变形孪晶导致的表面缺陷。
图4 含锰钢拉/压疲劳的表面缺陷表征
同时,疲劳损伤和晶粒的晶体学取向密切关联。通过大量实验对比,发现在加载轴和垂直于加载轴方向,某些特定取向的晶粒信息可以反映疲劳损伤。如图5所示,拉伸时,在垂直于加载轴的方向,111和422点阵应变可以表征和反映材料的损伤程度。压缩时,沿着加载方向,111,422, 311,220点阵应变可以反映疲劳损伤。但是由于拉伸和压缩过程中,裂纹扩展在前者是有利的,而在后者会被抑制。因此,对于拉/压疲劳的不同阶段,表征疲劳损伤程度,需要沿不同方向,采用不同的点阵应变来表征。详细规律见参考文献2。
图5 含锰钢拉/压疲劳损伤的点阵应变特征:点阵应变按绿色箭头方向演化就代表损伤。
疲劳寿命预测
综上,塑性变形导致的位错等缺陷的累积是变形损伤的本质。上述两种材料的损伤行为都可以通过晶粒的Taylor Factor大小来定量表征。这里Taylor Factor等于给定晶粒内部,所有滑移系或孪生系的剪切和(sum of plastic shears)。
但是,由于损伤的演变涉及裂纹的形核与扩展,由于后者在拉伸和压缩变形时的行为差异,导致变形损伤的表现也不同。实际多尺度模拟损伤时,既要考虑裂纹扩展行为的差异,也要考虑微裂纹导致局域有效弹性模量的降低。当前晶体塑性模型对疲劳寿命的预测仍然依赖一些经验参量,从而限制了模型的工业应用:疲劳寿命预测。目前,课题组正在开发考虑(1)裂纹形核与扩展,(2)等效弹性模量由于微裂纹的累积而降低,而导致的拉伸压缩损伤行为的差异,从而真正达到基于介观组织的疲劳寿命定量计算。
文章第一作者简介
解清阁,目前第一作者的文章有:4篇Acta Materialia,1篇PNAS (Proceedings of the National Academy of Sciences of the United States of America), 1篇 Acta Materialia Corrigendum, 2篇 Scripta Materialia, 3篇Materials Science and Engineering A, 及数篇其它期刊。博士毕业于比利时鲁汶大学。曾在美国橡树岭国家实验室做两年博士后,之后在新加坡科技局高性能计算中心担任Scientist (岗位Scientist II, Stage III) 。2018年末,辞去新加坡工作,全职在北京科技大学钢铁共性技术协同创新中心工作。目前为副研究员。主要从事金属加工和服役的介观-宏观尺度的表征和数字孪生(见图6), 兼顾基础理论和工程应用:高强金属组织/应力控制,增材制造的组织/应力控制,高速冲击的断裂行为等研究。欢迎感兴趣的老师/同学联系和交流。
图6 微观组织数字孪生实例
参考文献
Q.Xie, J. Lian, J. Sidor, F. Sun, X. Yan, C. Chen, T. Liu, W. Chen, P. Yang, K. An, Y. Wang, Crystallographic orientation and spatially resolved damage in a dispersion hardened Al alloy, Acta Materialia 193(2020) 138-150.
Q.Xie, Z. Yan, D. Yu, K. An, X. Yan, S. Yin, B. Gillham, X. Wu, P. Yang, Z. Zhao, Y. Wang, Crystallographic orientation and spatially resolved damage for polycrystalline deformation of a high manganese steel, Acta Materialia 226(2022) 117628.
免责声明:本网站所转载的文字、图片与视频资料版权归原创作者所有,如果涉及侵权,请第一时间联系本网删除。
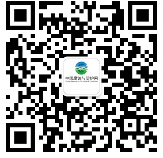
官方微信
《腐蚀与防护网电子期刊》征订启事
- 投稿联系:编辑部
- 电话:010-62316606-806
- 邮箱:fsfhzy666@163.com
- 腐蚀与防护网官方QQ群:140808414