构件发生腐蚀使其正常功能减弱或丧失为腐蚀失效。因此在该构件发生失效时,对腐蚀进行识别同时将腐蚀确定为失效的因素对后续开展失效分析(腐蚀失效分析)极为关键。同时,在开展失效分析不可忽略外部及现场信息变成”盲人摸象”,也不可因现今高科技检测仪器及手段的普遍化或因商业目的需求而盲目使用造成浪费。学习和掌握腐蚀失效的一些重要概念和分析思路也是“可靠性工程师”等技术和管理岗位需要的。
1、失效材料的检测
(1)化学成分分析
包括对失效件金属材料化学成分、环境介质及反应物、生成物(腐蚀产物)、痕迹物、附着物、残留物等化学成分的分析。
(2)性能测试
-
力学性能包括失效件金属材料强度指标、塑性指标、韧性指标、硬度等;
-
化学性能包括金属材料在所处环境介质中的自腐蚀电位、极化曲线、腐蚀速率等;
-
物理性能包括如环境介质在所处工艺条件下的反应热、燃烧热等;
(3)无损检测
针对失效件的现存状态(形状、尺寸等),选择有效的无损检测方法可迅速而可靠地确定构件表面或内部裂纹和其他缺陷的大小、数量和位置。金属构件表面裂纹及缺陷常用渗透法及电磁法检测,内部缺陷则多用放射性检测,声发射常用于动态-无损检测,如探测裂纹扩展情况。(关注公众号,后期将对无损检测的典型方法进行“浓缩介绍”)
(4)组织结构分析
组织结构分析包括金属材料表面和心部的金相组织或缺陷。
常用金相法分析金属的显微组织是否正常、是否存在晶粒粗大、脱碳、过热、偏析等缺陷;夹杂物的类型、大小、数量及分布;晶界上有无析出物,裂纹的数量、分布及其附近组织有无异常,是否存在氧化或腐蚀产物等。
图 20G钢内表面脱碳现象(脱碳层)
(5)应力测试及计算
构件残余应力的测定是在无外加载荷的作用下进行测定,目前多用X射线应力测定法。
2、失效件的取样及处理
(1)失效件的保护
断口保护主要是防止机械损伤或化学损伤。对于机械损伤的防止,应当在断裂事故发生后马上把断口保护起来。在搬运时将断口保护好,在有些情况下还用衬垫材料,尽量使断口表面不要相互摩擦和碰撞。有时断口上可能沾上一些油污或脏物,千万不可用硬刷干刷断口,并避免用手指直接接触断口。对于化学损伤的防止,主要是防止来自空气和水或其他化学药品对断口的腐蚀。一般可采用涂层的方法,即在断口上涂防腐物质,原则是涂层物质不使断口受腐蚀及易于被完全清洗掉。
(2)失效件的取样
在有必要开展全面地的失效分析时,需要制备各种试样,如力学性能试样、化学分析试样、断口分析试祥、电子探针试样、金相试样、表面分析试样和模拟试验用试样等。这些试样要从有代表性的部位上有计划性地截取。在截取的部位,用草图或照相记录,标明是哪种试样,以免弄混而导致错误的分析结果。
通常在开展腐蚀失效分析前,撰写并准备好详细的腐蚀失效分析方案和记录文件样式可提高开展失效分析的逻辑性和准确度。
(3)失效件的清洗
清洗的目的是为了除去保护用的涂层和断口上的腐蚀产物及外来沾污物如灰尘等。
常用以下几种方法:
-
用干燥压缩空气吹断口,清除粘附在上面的灰尘以及其他外来赃物,用柔软的毛刷轻轻擦断口,有利于把灰尘清除干净。
-
对断口上的油污或有机涂层,可以用汽油、石油醚、苯、丙酮等有机溶剂进行清除,清除干净后用无水酒精清洗后吹干。
-
超声波清洗能有效地清除断口表面的沉淀物,且不损坏断口。
-
应用乙酸纤维膜复型剥离。通常对于粘在断口上的灰尘和和疏松的氧化腐蚀产物可采用这种方法,就是用乙酸纤维脂反复覆在断口上2~5次,可以剥离断口上的脏物。该方法操作简单,既可去掉断口上的油污,对断口又无损伤。
-
使用化学或电化学方法清洗。这种方法主要用于清洗断口表面的腐蚀产物或氧化层,但可能破坏断口上的一些细节,所以使用时必须十分小心。一般只有在其他方法不能清洗掉的情况下经备用试样试用后才使用。可参考国标GB/T 16545开展。
3、失效分析的基本技能
(1)断口分析
断口上记录了金属断裂的全过程,即裂纹的产生、扩展直至开裂。外部因素对裂纹萌生的影响及材料本身的缺陷对裂纹萌生的促进作用。同时也记录着裂纹扩展的途径、扩展过程及内外因素对裂纹扩展的影响。
断口分析的依据
-
断口的颜色与色泽,观察断口表面光泽与颜色时主要观察有无氧化色、有无腐蚀的痕迹、有无夹杂物的特殊色彩与其他颜色;红锈、黄锈或是其他颜色的锈蚀;是否有深灰色的金属光泽、发蓝颜色(或呈深紫色、紫黑色金属光泽)。根据疲劳断口的光亮程度,可以判断疲劳源的位置。如果不是腐蚀疲劳,则源区最光滑。
-
断口上的花纹,疲劳断裂断口宏观上有时可见沙滩条纹,微观上有疲劳辉纹。脆性断裂有解理特征,断口宏观上有闪闪发光的小刻面或人字、山形条纹,而微观上有河流条纹、舌状花样等。韧性断裂宏观有纤维状断口,微观上则多有韧窝花样等。
-
断口上的粗糙度,断口的表面实际上由许多微小的小断面构成,其大小、高度差决定断口的粗糙度。不同材料、不同断裂方式,其断口粗糙度也不同。一般来说,属于剪切型的韧性断裂的剪切唇比较光滑;而正断型的纤维区则较粗糙。属于脆性断裂的解理断裂形成的结晶状断口较粗糙,而准解理断裂形成的瓷状断口则较光滑。疲劳断口的粗糙度与裂纹扩展有关,扩展速率越快,断口越粗糙。
-
断口与最大正应力的交角,韧性材料的拉伸断口一般呈杯锥状或呈45°切断的外形,其塑性变形是以缩颈的方式表现。即断口与拉伸轴向最大正应力交角是45°。脆性材料的拉伸断口一般与最大拉伸正应力垂直,断口表面平齐,断口边缘通常没有剪切"唇口"。断口附近没有缩颈现象。韧性材料的扭转断口呈切断型。断口与扭转正应力交角也是45°。材料的扭转断口呈麻花状,在纯扭矩的作用下,沿与最大主应力垂直的方向分离。
-
断口上的冶金缺陷,夹杂、分层、晶粒粗大、白点、氧化膜、疏松、气孔、撕裂等,常可在失效件断口上经宏观或微观观察而发现。
断口的观察
-
宏观观察,指用肉眼、放大镜、低倍率的光学显微镜OM或扫描电镜SEM来观察断口的表面形貌。通过宏观观察收集断口上的宏观信息,可初步确定断裂的性质,可以分析裂源的位置和裂纹扩展方向,可以判断冶金质量和热处理质量等。
-
微观观察,用显微镜对断口进行高放大倍率的观察,用金相显微镜及扫描电镜SEM的为多。断口微观观察包括断口表面的直接观察及断口剖面的观察。通过微观观察进一步核实宏观观察收集的信息,确定断裂的性质、裂源的位置及裂纹走向、扩展速度,找出断裂原因及机理等。
-
剖面观察,裁取剖面要求有一定的方向,通常是用与断口表面垂直的平面来截取,垂直于断口表面有两种切法:平行裂纹扩展方向截取,则可研究断裂过程;垂直于裂纹扩展方向截取,在一定位置的断口剖面上,可研究某一特定位置的区域。
(2)裂纹分析
裂纹分析的目的是确定裂纹的位置及裂纹产生的原因。裂纹形成的原因往往很复杂,如选材不当、材质不良、制造工艺不当以及维护和使用不当等均有可能导致裂纹的产生。裂纹分析往往需要从原材料的冶金质量、材料的力学性能、构件成型的工艺流程和工序工艺参数、构件的形状及其工作条件以及裂纹宏观和微观的特征等方向做综合的分析。其中牵涉到多种技术方法和专门知识,如无损探伤、化学成分分析、力学性能试验、金相分析、X射线微区分析等。
金属裂纹的基本形貌特征
-
裂纹两侧凹凸不平,耦合自然。其耦合特征是与主应力性质相关;若主应力属于切应力则裂纹一般呈平滑的大耦合;若主应力属拉应力则裂纹一般呈锯齿状的小耦合。
-
除某些沿晶裂纹外,绝大多数裂纹的尾端是尖锐的。
-
裂纹具有一定的深度,深度与宽度不等,深度大于宽度,是连续性的缺陷。
-
裂纹有各种形状,直线状、分支状、龟裂状、辐射状、环形状、弧形状,各种形状往往与形成的原因密切相关。
金属裂纹的检查
-
裂纹的宏观检查的主要目的是确定检查对象是否存在裂纹。裂纹的宏观检查,除通过肉眼进行直接外观检查和采取建议的敲击测音法外,通常采用无损探伤法,如X射线、磁力渗透着色、超声波、荧光等物理探伤法检测裂纹。
-
裂纹的微观检查是指检查裂纹形态特征,确定裂纹的分布是穿晶的,还是沿晶的,主裂纹附近有无微裂纹和分支。裂纹处及附近的晶粒度有无显著粗大或细化或大小极不均匀的现象,晶粒是否变形,裂纹与晶粒变形的方向相平行或相垂直。
-
裂纹附近是否存在碳化物或非金属夹杂物,其形态、大小、数量及分布情况,裂纹源是否产生于碳化物或非金属夹杂物周围,裂纹扩展与夹杂物之间有无联系。
-
裂纹两侧是否存在氧化和脱碳现象,有无氧化物或脱碳组织;产生裂纹的表面是否存在加工硬化层或回火层;裂纹萌生处及扩展路径周围是否有过热组织、魏氏组织、带状组织以及其他形式的组织缺陷。
裂纹产生部位分析
-
构件结构形状引起的裂纹,由于构件结构上的需要或由于设计上的不合理,或加工制造过程中没有按设计要求进行,或在运输过程中碰撞而导致在构件上往往有尖锐的凹角、凸边或缺口,截面尺寸突变或台阶等"结构上的缺陷" ,这些结构上的缺陷在构件制造和使用过程中将产生很大的应力集中并可能导致裂纹。所以,要注意裂纹所在部位与构件结构形状之间的关系分析。
-
材料缺陷引起的裂纹,金属材料本身的缺陷,特别是表面缺陷,如夹杂、斑疤、划痕、折叠、氧化、脱碳、粗晶以及气泡、疏松、偏析、白点、过热、过烧等,不仅其本身直接破坏了材料的连续性,降低了材料的强度与塑性,而且往住在这些缺陷的尖部,造成应力集中使得材料在很低的平均应力下产生裂纹并扩展,最后导致断裂。
-
受力状况引起的裂纹,在金属材料质量合格、构件形状设计合理的情况下,裂纹将在应力最大处形成或有随机分布的特点。在这种情况下,为判别裂纹起裂的真实原因要特别侧重对应力状态的分析。尤其是非正常操作工况下构件的应力状态, 如超载、超温等。
主裂纹的判别方法
-
T形法,将散落碎片按相匹配的断口合并在一起,其裂纹成T形。在一般情况下横贯裂纹首先开裂,主裂纹一般阻止二次裂纹扩展。
-
分枝法,将散落碎片按相匹配断口合并在一起,其裂纹成“树枝”形:在断裂失效中,往往出现一个裂纹后,产生很多分叉或分枝裂纹。裂纹的分叉或分枝方向通常为裂纹的局部扩展方向,其相反方向指向裂源,即分枝裂纹为二次裂纹,汇合裂纹为主裂纹。
-
变形法,将散落碎片按相匹配断口合并在一起,构成原来构件的几何外形,测量其几何形状的变化情况,变形量较大的部位为主裂纹,其他部位为二次裂纹。
-
氧化法,在受环境因素影响较大的断裂失效中,检验断口各个部位的氧化程度,其中氧化程度最严重为最先断裂即主裂纹所形成的断口,因氧化严重说明断裂的时间较长。
金属裂纹走向分析
-
应力原则,在金属脆性断裂、疲劳断裂、应力腐蚀断裂时,裂纹的扩展方向一般都垂直于主应力的方向,当韧性金属承受扭转载荷或金属在平面应力的情况下,其裂纹的扩展方向一般平行于切应力的方向,如韧性材料切断断口。
-
强度原则,指裂纹总是倾向沿着最小阻力路线,即材料的薄弱环节或缺陷处扩展的情况。有时按应力原则扩展的裂纹,途中突然发生转折,显然这种转折的原因是由于材料内部的缺陷。在这种情况下, 在转折处常常能够找到缺陷的痕迹或者证据。
一般情况下, 当材质比较均匀时,应力原则起主导作用,裂纹按应力原则进行扩展,而当材质存在着明显不均匀时,强度原则将起主导作用,裂纹将按强度原则进行扩展。裂纹扩展方向到底是沿晶的还是穿晶的, 取决于在某种具体条件下, 晶内强度和晶界强度的相对比值。应力腐蚀裂纹、氢脆裂纹、回火脆性、磨削裂纹、焊接热裂纹、冷热疲劳裂纹、过烧引起的锻造裂纹、铸造热裂纹、蠕变裂纹、热脆等晶界是薄弱环节,因此这些裂纹是沿晶界扩展的;而疲劳裂纹、解理断裂裂纹、淬火裂纹,焊接裂纹及其他韧性断裂的情况下,晶界强度一般大于晶内强度,因此它们的裂纹为穿晶型,这时裂纹遇到亚晶界、晶界、硬质点或其他组织和性能的不均匀区时,往往会改变扩展方向。因此认为晶界能够阻碍疲劳裂纹的扩展, 这就是常常用细化晶粒的方法来提高金属材料的疲劳寿命的原因之一。
(3)痕迹分析
构件失效时,由于力学、化学、热学、电学等环境因素单独或协同地作用,并在构件表面或表面层留下了某种标记,称为痕迹。
痕迹分类
-
机械接触痕迹,构件之间接触的痕迹,包括压入、撞击、滑动、滚压、微动等单独作用或联合作用,这种痕迹称为机械接触痕迹,其特点是塑性变形或材料转移、断裂等,集中发生于接触部位,并且塑性变形极不均匀。
-
腐蚀痕迹,由于构件材料与周围的环境介质发生化学或电化学作用而在构件表面留下的腐蚀产物及构件材料表面损伤的标记,称为腐蚀痕迹。
图 点腐蚀穿孔
-
电侵蚀痕迹,由于电能的作用,在与电接触或放电的构件部位留下的痕迹称为电侵蚀痕迹。
-
热损伤痕迹,由于接触部位在热能作用下发生局部不均匀的温度变化而留下的痕迹。金属表面层局部过热、过烧、熔化、直至烧穿、表面保护层的烧焦都会留下热损伤痕迹。不同的温度有不同的热损伤颜色(如,不同温度下的回火着色),且构件材料表面层成分结构会发生变化,表面性能有所改变。
-
加工痕迹,对失效分析有帮助的主要是非正常加工痕迹,即留在构件表面的各种加工缺陷,如刀痕、划痕、烧伤、变形约束等。
-
污染痕迹,各种外来污染物附着在构件表面而留下的痕迹是污染痕迹(如附着物、残留物)。
痕迹分析主要内容
-
痕迹的形貌,特别是塑性变形、反应产物、变色区、分离物和污染物的具体形状、尺寸、数量及分布;
-
痕迹区以及污染物、反应产物的化学成分;
-
痕迹颜色的种类、色度和分布、反光性等;
-
痕迹区材料的组织和结构;
-
痕迹区的表面性能(耐磨性、耐蚀性、显微硬度、表面电阻、涂镀层的结合力等)
-
痕迹区的残余应力分布;
-
从痕迹区散发出来的各种气味;
-
痕迹区的电荷分布和磁性等。
4、失效现场信息的重要性
除了以上几个部分提到的内容,腐蚀失效分析需要关注失效件现场信息,包括失效件所属设备和/或作业点的信息收集和分析、失效件失效时的运行数据收集和分析、失效件使用工况历史数据收集和分析等。在重点关注失效实物件分析的同时,进一步更多地关注失效现场信息的收集和分析将有助于失效分析的开展,对识别某一类型的失效分析、提供有效的预防措施、避免此类失效事故的再次发生有重要帮助。
5、失效分析参考标准
开展腐蚀失效分析的参考标准文件有:GB/T 16545、HB 7739、GB/T 38803、ASTM G161、SY/T 6945-2013、DB51/T 1723-2014、ASTM G1、JB/T 7901等。
免责声明:本网站所转载的文字、图片与视频资料版权归原创作者所有,如果涉及侵权,请第一时间联系本网删除。
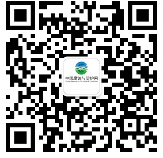
官方微信
《腐蚀与防护网电子期刊》征订启事
- 投稿联系:编辑部
- 电话:010-62316606
- 邮箱:fsfhzy666@163.com
- 腐蚀与防护网官方QQ群:140808414