一、研究的背景与问题
腐蚀导致零部件精度丧失、性能退化甚至发生突然灾难。对滚动轴承而言,腐蚀加速了疲劳和磨损,显著降低轴承寿命与可靠性。为此航空航天、海洋舰船以及医疗设备大力提倡使用不锈钢轴承,以保障丝杠及轴承等基础件的使役性能与安全性。传统不锈轴承钢主要是高碳高铬马氏体钢440C(国内牌号9Cr18(Mo))和高温不锈轴承钢BG42(Cr14Mo4),含有50-70um大颗粒碳化物,成为腐蚀与疲劳源头,严重降低耐蚀性能和抗疲劳性能,远不能满足航空航天高端装备用长寿命化轴承及丝杠副需求,亟需开展高耐蚀和长寿命的高氮高强马氏体不锈钢30Cr15Mo1N的国产化研制与应用研究。
高氮高强马氏体不锈钢30Cr15Mo1N的氮合金化,不仅抑制了大颗粒碳化物出现,还大幅提升了抗点蚀能力以及表面钝化膜稳定性,从而显著提升了耐蚀性能和抗疲劳性能。加压电渣熔炼的高氮高强马氏体不锈钢N含量可达0.40%以上,典型钢种如德国FAG公司Cronidur30,通过碳含量进一步降低和氮含量进一步提高,实现了轴承钢的基体组织和碳化物更加均匀细小(最大碳氮化物尺寸≤10μm)。目前加压电渣冶炼已成为高氮高强马氏体不锈钢产品主流生产工艺。据报道加压电渣冶炼30Cr15Mo1N的耐腐蚀性比440C提高100倍,疲劳寿命比M50和GCr15提高了5倍以上。鉴于30Cr15Mo1N在冶金质量上具有纯净度高和组织细密特点,在性能上具备优异的低温性能,优异的耐蚀性能、耐磨性能以及长的接触疲劳寿命,因而被成功应用于航空航天、医疗器械、海洋船舶及高速精密机床为代表的高端装备领域。但高氮高强马氏体不锈钢国产化研究滞后,导致高氮高强马氏体不锈钢严重依赖进口。
近10年来,钢铁研究总院轴承钢研究团队立足于高氮高强马氏体不锈钢30Cr15Mo1N重大需求,开展了超过极限氮含量高氮高强马氏体不锈钢研制工作。天马和抚钢也分别在2016年和2018年相继从奥地利和德国引进了加压电渣冶炼装备。这为高氮高强马氏体钢Cronidur30国产化奠定了技术储备与装备基础。本项目在国家“十一五”到“十四五”多个项目支持下,开展并完成了高氮高强马氏体不锈钢的加压电渣冶炼研制和推广应用工作,解决了大型飞机用高氮高强马氏体不锈钢国产化及零部件制造与应用等关键问题。
二、解决问题的思路与技术方案
高氮高强马氏体钢30Cr15Mo1N是高硬度和高耐蚀材料的王牌钢种,国外已应用于航空航天、海洋设施、医疗卫生等丝杠副、轴承等零部件。与传统钢铁材料冶炼技术不同,高氮高强马氏体不锈钢30Cr15Mo1N制备需向钢中加入超过溶解度极限的N元素并实现稳定均匀控制,这涉及到高氮高强马氏体不锈钢棒线材的合金化优化设计、电极母坯冶炼、电渣坯冶炼、热变形与热处理等材料工业化技术和飞机用丝杠副及轴承等零部件加工制造与考核验证等技术的系统研究。基于大型飞机等,本项目制定了如图1所示的棒线材研制路线图,具体材料研制与推广应用等研究内容如下:
1. 高氮高强马氏体钢棒线材工业研制:(1)开展以30Cr15Mo1N为主的高氮高强马氏体不锈钢原型钢设计与验证,(2)开展真空感应与炉外精炼等两种电极制备工艺技术研究;(3)开展加压电渣冶炼用增氮剂Si3N4与保护渣的系统研究;(4)开展加压电渣炉的加压电渣冶炼工艺研究;(5)开展高氮高强马氏体不锈钢的热变形工艺技术研究,(6)打通30Cr15Mo1N电极坯制备、电渣坯冶炼和热变形及热处理工业化制备技术,(7)开展了高氮高强马氏体钢线材拉拔工艺研究;(8)制定高氮高强马氏体钢产品技术条件。
2.针对高氮高强马氏体钢棒线材推广应用,开展以下6方面研究:(1)开展高氮高强马氏体钢的耐蚀性能和疲劳性能研究;(2)开展30Cr15Mo1N钢一材四状态的热处理调控技术研究;(3)开展表面脱碳脱氮控制、表面超硬化热处理技术和30Cr15Mo1N全面性能评价等应用技术研究;(4)开展丝杠副和多种机体轴承等零部件的批量制造、台架考核验证和装机应用研究;(5)开展高氮高强不锈钢两大海域的使役性能研究,为未来高氮高强马氏体不锈钢在不同海域应用积累了数据;(6)初步开展直径220mm和270mm更大规格高氮高强马氏体钢棒材试制,为大型飞机丝杠副研制奠定了超大规格棒材基础。
图1 高氮高强马氏体不锈钢棒线材研制及应用项目的理论、制造和应用研究路线图
通过本项目研究,打通了加压电渣生产工艺流程,形成了直径φ3.5-φ170的高氮高强马氏体不锈钢棒材和线材产品,实现了国产30Cr15Mo1N的产品的批量稳定供货,产品质量达到甚至超过了国外Cronidur30同类产品。棒线材产品的高强韧性(抗拉强度Rm≥2000MPa)、高接触疲劳性能(4.0GPa下L10≥1.67x107次)、高耐蚀性能(耐蚀性能超过440钢100倍以上,中性盐雾腐蚀超过192小时)以及超细尺寸碳化物(大颗粒碳化物≤10微米)等质量性能水平。通过本项目研究,完成了大型飞机用大型丝杠副、机体轴承、航发动力轴承等零部件设计、加工制造和装机验证,满足了零部件的高耐蚀和长寿命需求并实现了批量装机应用,填补了国内空白,为大飞机多个型号研制与生产做出了重要贡献。
三、主要创新性成果
1.研制出X30N、X60N和X90N等系列化高氮高强马氏体不锈钢原型钢,阐明了高氮高强马氏体不锈钢中氮元素存在形式与控制机理,奠定了本项目材料研制和推广应用的理论与实验基础。
项目团队通过系列化成分设计和真空感应加压冶炼,制备了如表1所示的原型钢,验证了高硬度、高耐蚀以及优异耐蚀性能。通过系列化回火温度对微观组织结构和耐蚀性能影响,发现了低温回火状态下,N主要以固溶形式存在,而在超过450℃后N以M2N形式析出的高氮高强马氏体钢的耐蚀与疲劳与机制。主要包括以下技术与理论成果。
表1 X30、X60、X90及440C钢化学成分(感应加压冶炼,440C双真空冶炼)
(1) 发明了高硬度、高耐蚀和抗疲劳X30N、X60N和X90N等高氮高强马氏体不锈钢原型钢,获得了高硬度、耐腐蚀和优异抗疲劳性能。从图2a可以看出,X30、X6N和X90在180℃回火可获得58HRC的硬度,随回火温度升高,硬度略微降低。但当回火温度提高480℃后,三种钢硬度均达到60HRC以上,X90N钢更是达到了65HRC。从图2(b)和(c)可以看出,经过180℃低温回火,X30、X60和X90均匀腐蚀速率均在1.0×10-5m/s水平,与进口钢相当。但在500℃高温回火后,X30钢均匀腐蚀速率为10-3m/s,X60和X90钢的均匀腐蚀速率更是降低到10-2m/s水平。从图2(d)可以看出,经过180℃低温回火,440C在4.0GPa的赫兹应力下,接触疲劳寿命仅为L10=0.45x107次,远低于X30的L10=1.0×107次、X60的L10=4.0×107次和X90的L10=7.0×107次。
图2的结果表明本项目研发的系列化高氮高强马氏体不锈钢450℃以下回火后可以获得高硬度、高耐蚀和优异的接触疲劳寿命,为本项目高氮高强马氏体不锈钢研制与推广应用奠定了合金化基础。
图2 系列化高氮高强马氏体不锈钢的性能验证 (a)回火温度对硬度影响, (b)180℃回火耐蚀性能比较,(c)500℃回火耐蚀性能比较和(d)180℃回火接触疲劳性能比较
(2) 发现了回火温度对微观组织结构和耐蚀性能影响规律,首次揭示了高氮高强马氏体不锈钢中N的存在形式及其对耐蚀性能影机制。图3给出了X30在160-620℃等不同温度回火对钝化膜成分影响结果,提出了低温与高温回火腐蚀机制示意图。相对于180℃低温回火处理,500℃高温回火X30、X60和X90耐蚀能力严重恶化。回火温度及氮含量变化对耐蚀性能影响表明,耐蚀性能主要取决于固溶Cr和N的元素含量。随着钢中Cr和N含量降低,耐蚀性能显著下降。图3a表明,随回火温度提升,钝化膜中Cr氧化物与Cr水化物比值降低,O-2/OH-1比值降低,表明回火温度提升导致了钝化能力的降低。图3b表明NH4+与NH3总量变化与回火温度基本线性下降,进一步揭示了钝化能力随回火温度升高而降低的电化学机制,表明了高氮高强马氏体不锈钢的耐蚀行为主要归因于回火温度改变了N存在形式。图3c给出了低温到高温回火的高氮高强马氏体不锈钢耐蚀行为演变机理示意图。该研究成果为本项目高耐蚀热处理技术研究奠定了理论基础。
图3 高氮马氏体不锈钢的电化学腐蚀研究及腐蚀机制(a)回火温度对钝化膜成分影响, (b)回火温度对钝化膜稳定性影响和(c)高氮马氏体钢耐蚀行为与回火温度关系的耐蚀机制示意图
2.开发了高氮高强马氏体不锈钢的加压冶炼PESR增碳控氮技术,打通了VIM+PESR和EAF+LF+VD+PESR两条冶炼工艺流程,开发了“高温慢锻”、“低温快轧”的热加工工艺,实现了高氮高强马氏体不锈钢的批量稳定工业生产。
项目团队在系统研究加压电渣装备与技术基础上,形成了高氮高强马氏体不锈钢加压冶炼用保护渣和增氮剂技术,提出了电极和电渣锭制备等双步冶炼技术思路,完成了电极冶炼和电渣锭冶炼关键技术研究;打通了VIM+PESR和EAF+LF+VD+PESR两条冶炼工艺流程,开发了“高温慢锻”和“低温快轧”的热加工工艺。主要包括加压电渣冶炼和高成材率热变形等两大关键核心技术。
(1) 发明了VIM+PESR和EAF+LF+VD+PESR两条冶炼工艺流程,解决了电极冶炼问题、突破了保护渣、增氮剂和加压电渣冶炼选材与优化,打通了高氮高强马氏体不锈钢冶炼流程。本项目在对高氮高强马氏体钢的加压电渣冶炼保护渣、增氮剂和加压电渣关键参数研究基础上,开展了高氮高强马氏体钢的电极制备与电渣冶炼的双阶段工业流程,提出了真空感应VIM冶炼+加压电渣和炉外精炼EAF+LF+VD两种冶炼工艺流程,如图4所示。在电极制备技术基础上,通过JmatePro 软件和Meltflow-ESR专用电渣重熔软件等模拟,计算出了X30钢加压电渣凝固控制参数,探索出了加氮炉内压力与钢中含氮量定量关系,发明了高氮马氏体不锈钢PESR工艺。通过VIM和EAF+LF+RH的两种电极制备和加压电渣PESR冶炼的冶炼全流程工艺技术研究,突破了高氮高强马氏体钢冶炼工序的氮含量协同控制难题,形成了超纯净丝杠棒材VIM+PESR和低成本轴承钢棒材EAF+LF+VD+PESR的高氮高强马氏体不锈钢冶炼技术。
图4 开发了高氮高强马氏体不锈钢的VIM+PESR和EAF+LF+VD+PESR两条冶炼工艺流程与工艺(a)IIM+PESR流程和(b)EAF+LF+VD+PESR流程
(2) 发明了高氮马氏体钢的高温慢锻和低温快轧的双阶段热变形技术,解决了表面开裂和碳化物网带问题,形成了高成材率的热变形与热处理关键核心技术。通过热变形模拟构建了热加工图,提出了高温低速变形和低温高速变形的技术思路,如图5所示,建立了丝杠用超纯净棒材和低成本轴承钢棒材的高氮马氏体钢棒材生产线,实现了包括最大直径270mm的棒材产品稳定生产和批量供货。
图5 不同应变量下轴承钢Cronidur30钢热加工图工艺谱(a)0.1,(b)0.2,(c)0.4和(d)0.6 (高温1100-1250℃的低速变形(10-5-10-2/s)和低温1000-1100℃的高速变形(10-1-10+2/s))
3.首次发现了高氮高强马氏体不锈钢中马氏体孪晶为疲劳起裂源和纳米析出的抗疲劳现象及机制,阐明了表面脱碳脱氮自由能控制机制,开发了纳米析出第二相的抗疲劳组织调控技术和丝材拉拔工业生产技术。
项目团队系统开展了高氮高强马氏体不锈钢的组织性能调控与热处理技术研究,发现了基体组织严重影响疲劳性能。开展了真空热处理与氧化气氛热处理对高氮高强马氏体不锈钢表面脱氮脱碳行为及机制的研究。主要包括抗疲劳的纳米析出调控热处理和高氮高强马氏体不锈钢丝材质量性能控制等两大关键核心技术。
(1)开发出高氮高强马氏体不锈钢的纳米析出抗疲劳组织调控技术,大幅提升疲劳强度与寿命。项目团队首次发现并揭示了孪晶马氏体疲劳源机制。通过180℃回火旋弯疲劳试样及断口疲劳源特征分析,揭示了马氏体孪晶和夹杂物的两种疲劳源现象,提出了马氏体孪晶形成疲劳源的缺陷形成模型。通过对碳化物定量分析,揭示了纳米碳氮化物抗疲劳机制。180℃回火X30和500℃回火X30的Rm为2000MPa,但疲劳强度s-1从715MPa提升到1020MPa,L10=1.67×107提升到L10=3.99×107。通过构建抗疲劳组织结构单元,揭示了纳米析出可同时提升疲劳强度与疲劳寿命的机制,为新型抗疲劳材料研制提供了思路。
(2)开发出高氮高强马氏体不锈钢的丝材拉拔工业化生产工艺技术,揭示了脱碳脱氮机制。针对高氮高强马氏体不锈钢丝材的表面无脱碳脱氮要求,开展了不同热处理条件下的脱碳脱氮行为与规律研究,如图6所示。实现了直径5mm线材的产品稳定生产和批量供货。
图6 奥氏体化温度及气氛对高氮高强马氏体钢C/N分布规律影响(a)氧化气氛下基体组织与析出物,(b) EPMA表征C/N分布,(c)氧化气氛下C/N沿分布结果和(d)真空热处理C/N分布
4. 完成了高氮高强马氏体钢的热处理、零部件加工制造与考核验证等应用适应性技术研究,开发出一材四状态处理和表面超硬化处理技术,满足了丝杠副等零部件制造需求,实现了零部件制造与应用。
项目团队针对系列大型飞机的高安全、高强韧、优异耐蚀和抗疲劳等性能要求,开展了材料应用适应性评价、零部件制造和验证,实现了装机应用,解决了我国大型飞机等用高氮高强马氏体不锈钢及零部件保供问题,保障了国产大型飞机的生产与研制进程。
(1) 发明了适用于航空丝杠副制造的一种材料四种状态热处理工艺。如图7所示,完成了热处理工艺对高氮高强马氏体钢X30影响研究,研发出了适用于丝杠副制造的一种材料四种状态热处理工艺。如图7a,针对丝杠对不同硬度、强度与韧性要求,研发出一种材料四种状态热处理工艺,满足了丝杠螺母对高硬度、高耐磨性以及抗疲劳性能要求;如图7b,通过一材四状态热处理,形成了四个不同状态的拉伸曲线,表明高氮高强马氏体钢抗拉强度可以达到2380MPa。如图7c,通过对X30钢旋弯疲劳测试,获得了1020MPa旋弯疲劳强度。如图7d所示,四状态下的高氮高强马氏体不锈钢表现出优异的疲劳强度与抗拉强度比值。其中第四状态和第三状态s-1/Rm=0.55,而第二状态为s-1/Rm=0.50,第一状态s-1/Rm=0.43,揭示了回火状态组织对抗疲劳性能重要影响,为高氮马氏体不锈钢的心部强韧化工艺制定提供了理论与技术基础。
图7 高氮高强马氏体不锈钢基体与表面热处理对性能影响研究.(a)X30一材四状态工艺性能图,(b)X30一材四状态的拉伸曲线,(c)X30一材四状态旋弯疲劳性能和(d)X30钢表面渗氮硬度和耐温性能
(2) 发明了适用于航空丝杠副和航空轴承的表面超硬化工艺。研究发现表面硬化技术应用大幅提升高氮高强马氏体钢的表面硬度与耐温性能,显著提升疲劳性能,如图8所示。
完成了高氮高强马氏体不锈钢的表面感应淬火和表面渗氮热处理研究。如图8所示,通过表面感应淬火实现了表面硬度720Hv和感应深度1mm,通过表面渗氮实现了表面硬度提升到1100Hv和表面渗氮层深度达到0.1mm以上。同时通过表面渗氮大幅提高表面硬度和耐温性能,实现650℃回火达到表面硬度60HRC,为高氮高强马氏体不锈钢的表面抗疲劳工艺制定提供了技术基础。
图8 高氮高强马氏体不锈钢表面超硬化技术研究结果。(a)表面感应淬火硬度分布,(b)表面渗氮热处理硬度分布,(c)表面渗氮层深度可达0.1mm以上和(d)表面渗氮大幅提高耐温性能。
四、应用情况与效果
本项目研制的高氮高强马氏体不锈钢,形成了批量制造与稳定供货能力,实现了在大型运输机等的机体轴承、航发轴承以及高强韧丝杠副的批量装机应用,保障了国产大型飞机的生产与研制进程。同时高氮高强马氏体不锈钢产品已进入C919等大飞机用材目录,奠定了大型宽体客机用丝杠与机体轴承的材料基础。本项目成果多个指标达到甚至超过国外产品,钢材产品实物质量性能达到甚至超过了国外水平,实现申报发明专利14件(获批9件发明专利),发表论文20余篇(SCI收录文章6篇和EI收录14篇)。经中国金属学会组织的科技评价认为研发成果总体达到世界领先水平。
信息来源:钢铁研究总院有限公司
免责声明:本网站所转载的文字、图片与视频资料版权归原创作者所有,如果涉及侵权,请第一时间联系本网删除。
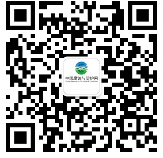
官方微信
《腐蚀与防护网电子期刊》征订启事
- 投稿联系:编辑部
- 电话:010-62316606
- 邮箱:fsfhzy666@163.com
- 腐蚀与防护网官方QQ群:140808414