酸性硫酸盐镀锡后出现一些情况如锡镀层光亮细致,存放时变色。
(1)可能原因:镀后处理不当,清洗不净
原因分析:对于光亮镀锡而言,镀后处理十分重要,若镀层表面残留的镀液清洗不净或锡镀层在存放和转运过程中遭受氧化和污染,都将直接影响其可焊性
处理方法:a.按下列工艺进行镀后处理:镀锡工件→水洗→专用清洗剂(或5%磷酸三钠)清洗→水洗→钝化(Cr03:50g/L;H2S04:1~2g/L;常温;10~20s)→水洗→热纯水洗(60℃以上)→甩干→60~70℃烘干;(钝化工艺也可采用专用钝化剂进行钝化。)
b.严格清洗操作,加强清洗水和化学槽液的维护保养。
(2)可能原因:有机杂质积累过多
原因分析:有机分解产物或光亮剂中的某些组分积累过多,使镀层内夹杂物增多,以致工件在空气中极易变色泛黄。
处理方法:定期用3~5g/L活性炭吸附有机杂质。
(3)可能原因:光亮剂过多
原因分析:若光亮剂过多,镀层内夹杂的光亮剂太多,镀层内应力大,出现发黄、变脆、脱落,有时甚至镀不上镀层,严重影响镀层的结合力和可焊性。
处理方法:a.电解除去多余的光亮剂;b.用活性炭吸附,除去多余的光亮剂。
(4)可能原因:温度过高
原因分析:光亮镀锡温度一般在10~20℃下进行,如果温度超过25℃,就会影响镀层的光亮度,超过30℃,不利于光亮剂吸附,而且载体光亮剂析出,使其他光亮剂失效。亚锡盐的氧化水解和光亮剂消耗均随温度升高而加快,若温度过高(超过35℃),Sn2+氧化速度加快,镀液浑浊,镀层粗糙,光亮剂消耗增加,光亮区变窄,严重时镀层变暗,出现花斑,可焊性降低。低温有利于整体光亮及良好的均镀性,但温度过低,工作电流密度范围缩小,镀层易烧焦。加入稳定剂能提高使用温度的上限值。
处理方法:采用制冷或停镀,降低镀液温度至标准值。
(5)可能原因:电流密度过大
原因分析:光亮镀锡电流密度一般控制在1~4A/dm2。电流密度过大,镀层疏松、粗糙、多孔、边缘易烧焦,脆性增加;电流密度过小,沉积速度过低,镀层光亮度低,不能获得全光亮的镀层。对于滚镀电子元器件,电流密度一般控制在工艺范围的下限。
处理方法:准确测量受镀工件面积,合理设定电流值。
(6)可能原因:镀液浑浊
原因分析:镀液中的胶状物与Sn2+共沉积到镀层中,使镀层变色,对锡镀层的可焊性将有一定的影响。
处理方法:详见酸性硫酸盐镀锡故障分析:镀锡液浑浊的处理方法。
责任编辑:王元
《中国腐蚀与防护网电子期刊》征订启事
投稿联系:编辑部
电话:010-82387968
邮箱:ecorr_org@163.com
中国腐蚀与防护网官方 QQ群:140808414
注:本稿为中国腐蚀与防护网版权所有,未经允许, 严禁用于商业用途。转载时请务必以超链接形式标明文章原始出处和作者信息及本版权声明。
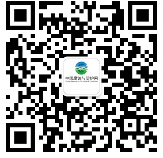
官方微信
《中国腐蚀与防护网电子期刊》征订启事
- 投稿联系:编辑部
- 电话:010-62313558-806
- 邮箱:fsfhzy666@163.com
- 中国腐蚀与防护网官方QQ群:140808414