汽车零部件用低温烘烤型水性涂料的制备及施工应用
2016-03-17 10:00:20
作者:本网整理来源:=$docheckrep[1]?ReplaceBefrom($ecms_gr[befrom]):$ecms_gr[befrom]?>
一、前言
汽车涂料往往代表着涂料工业的最高技术水平和发展方向。“十一五”期间,随着我国汽车工业的快速发展,汽车用涂料市场也步入了快速发展时期。汽车产销量从2009年的1300多万辆到2013年2200多万辆,仅用了4年时间。其中乘用车产量从2009年的1000万辆左右,2013年增长到1800万辆左右。“十二五”期间,中国汽车年产量将达到2500万辆,我国汽车保有量将达到1.5亿辆,工业总产值将达到4.5万亿元,汽车工业增加值占GDP比例将达到3%,已成为中国经济的引擎,这为涂料涂装工业带来巨大商机。
溶剂型涂料是传统的汽车涂料,是以有机溶剂为主要分散介质;而水性涂料是以水作为主要分散介质的涂料,水性涂料中挥发性有机化合物排放比溶剂型涂料降低了60%~70%。随着环保呼声越来越高,技术创新成为行业发展的主旋律,清洁生产、节能环保、循环经济、高功能性等工艺或产品将成为行业发展的新的增长点。为了达到环保要求,汽车涂料正在向水性化、高固体份、粉末涂料3种主要方向发展,其中水性化技术是有效的途径之一。乘用车涂料主要品种包括:原厂漆、修补漆、零部件漆和PVC抗石击漆,比例分别占约50%,20%,15%,15%。车身原厂漆占乘用车涂料最大份额,其次是修补漆,零部件涂料和PVC抗石击涂料相当。
众所周知,从市场角度来看,汽车原厂漆市场目前基本被外资品牌垄断。汽车修补漆领域,国产品牌也只占市场的部分份额。而对于汽车底盘及零部件用涂料,由于对于涂层的外观及性能要求稍低,国产品牌有很大的市场潜力。实际上,目前很多汽车厂及相关零部件厂商涂装中使用国产的涂料产品。目前市场上的汽车零配件(如传动轴、车桥、水箱、散热片、压缩机等)涂料多以溶剂型为主,这些涂料由于有机溶剂挥发物总量(VOC)较高,对环境的污染比较大,回收利用又有限,造成资源浪费,同时对人们的身体健康造成危害,不符合环保的要求。出于环保法规的要求,与原厂漆及修补漆类似,汽车底盘及零部件涂料也逐步替换为水性涂料。本文重点讨论应用于汽车底盘及零部件的水性涂料。
就涂料的施工性而言,由于许多汽车底盘及零部件涂料或工件较大,或含有塑料件,因此不适合高温烘烤,因此很多工件选择自干涂料或低温(一般低于100℃)烘烤型涂料。目前应用于该领域的涂料主要有以下2个体系:水性醇酸涂料和水性环氧酯涂料。其中水性醇酸树脂是发展较早、产量最大的合成树脂,它价格便宜、施工简单、原料来源丰富、酸值低、对颜填料等有较好的润湿和分散性,用其制成的漆,漆膜光亮,附着力强,耐久性好,柔韧性、光泽和丰满度都非常优良,可与多种合成树脂混合使用。然而,遗憾的是,由于水性醇酸树脂分子链上的酯键在弱碱性条件下较易水解,使涂料贮存稳定性下降,并且涂膜存在易泛黄的缺点,使水性醇酸涂料的应用受到一定限制。水性醇酸涂料在性能上也存在涂膜干燥缓慢,硬度低,耐水性、耐腐蚀性差,户外耐候性不佳等缺点,这都需要通过改性来改善其性能。与水性醇酸涂料相比,水性环氧酯涂料同时具备了环氧体系与干性油的优良特性:其中环氧组分具有较高的耐腐蚀性;植物油脂肪酸组分可以进行氧化交联,进一步提高防护性能。因此,水性环氧酯涂料具有更高的硬度和更优的耐水解性,漆膜在成膜过程中干速也更快,并且具有优良的耐腐蚀性能。
本文中选用一种自乳化型水性环氧酯树脂,加入特定的丙烯酸乳液作为成膜物,配合颜料、填料及合适的助剂,制备聚丙烯酸改性环氧酯水性涂料,研究了关键配方参数对涂料性能的影响,将所研制涂料应用于汽车底盘及零部件,研究了该涂料在涂装应用过程中的施工条件参数。
二、实验部分
2.1实验原料实验所用原材料列表如下,包括产品牌号,用途及规格。
表1实验用原材料信息表1实验用原材料信息表1实验用原材料信息2.2涂料制备(1)研磨颜料浆将去离子水加入反应釜中,依次加入pH调节剂、润湿分散剂、消泡剂、颜料、填料进行研磨,研磨至细度40μm以下,出料,得到颜料浆;(2)涂料配制将水性环氧酯乳液(含催干剂)和丙烯酸乳液按比例加入反应釜中,缓缓加入成膜助剂,再搅拌加入步骤(1)得到的颜料浆、依次加入抗闪锈剂、流平剂、基材润湿剂,充分搅拌,缓慢加入增稠剂,调整粘度,得到水性丙烯酸改性环氧酯防腐涂料。参考配方见表2所示。
表2水性丙烯酸改性环氧酯涂料配方表2水性丙烯酸改性环氧酯涂料配方表2水性丙烯酸改性环氧酯涂料配方2.3涂料施工及性能测试将所制备涂料通过兑水调节到施工粘度,喷涂样板或工件。其中实验室标准样板为冷轧钢板,喷涂前进行打磨处理,无脱脂和磷化过程。实验室样板的烘烤条件为80℃烘烤20min。工件按照涂装线上工艺分别进行脱脂和磷化处理后,再进行涂装。对所涂装样板和工件进行性能测试,测试采用相应国标方法检测。
三、结果与讨论
3.1树脂选择水性树脂是成膜的基料,决定了漆膜的主要性能。而高性能的树脂是水性金属防腐漆成功最关键的因素。在水性金属防腐漆的配方中,必须选择有优异附着力和良好阻隔性能的树脂。水性环氧酯树脂由于其优异的机械性能和防锈性能而在金属防护领域有着广泛的应用。环氧酯树脂由环氧树脂与植物油脂肪酸通过酯化反应而制成,因此,环氧酯同时具备了环氧树脂与干性油的许多优良特性:其中环氧组分具有较高的耐腐蚀性;植物油脂肪酸组分可以进行氧化交联,进一步提高防护性能。因此,目前主流的水性环氧酯产品是自乳化制备的产品。乙烯基改性法自乳化法主要技术路线是:将环氧酯树脂与预定酸值的丙烯酸酯类混合单体进行自由基共聚,形成共聚产物,将该共聚产物用有机胺中和后进行水稀释后得到水性环氧酯乳液。该方法制备的水性环氧酯乳液具有很好的储存稳定性,产品性能易于调节、成膜性好、易于施工,并且由于可以空气交联,因此具有较好的耐水和耐盐雾性能。然而,水性环氧酯在应用中也存在一些缺点,例如漆膜干燥速度慢,耐候性较差、耐碱性不足等问题。另一方面,丙烯酸乳液具有干燥速度快、硬度高、耐碱性优异、耐候性好等优点,这些特性正好弥补了水性环氧酯产品性能的不足。
本项目中选用水性环氧酯乳液作为主要成膜物,添加合适用量的丙烯酸乳液提高涂层的硬度和干性,再加入采用分散剂研磨的颜填料浆,制备低温烘烤型水性涂料。由于涂层性能主要取决于水性环氧酯和丙烯酸乳液两种树脂,本文研究了不同比例的树脂配比对涂层干燥速度、硬度、耐碱性、耐水性和耐腐蚀性的影响,实验结果见表3所示。由表3中数据可知,丙烯酸乳液含量小于树脂总量的35wt%时,涂层干燥速度较慢,涂层的耐碱性不满足要求;当丙烯酸乳液含量太高时,涂层中环氧酯相对含量降低,涂层交联程度下降,相应涂层的耐水性和耐盐雾性能均下降。综合考虑涂层性能和综合成本,选用水性环氧酯/丙烯酸乳液质量比为65/35。
表3不同乳液比例对涂料性能影响表3不同乳液比例对涂料性能影响注:a乳液比例=m(水性环氧酯)/m(丙烯酸乳液);b表干时间测定按照GB/T1728-79/89,膜厚为25μm,25℃条件下测定。
3.2助剂选择3.2.1分散剂选择在色漆生产中,最重要的步骤之一是固体颜料在液相基料溶液中的均匀分布。分散过程中需要研磨颜料附聚体,从而最大地展现出颜料的颜色性能,满足光学方面的要求,例如色点、色强度、色度和透明度。润湿分散剂润湿颜料表面,避免分散后的颜料颗粒再次附聚。假使颜料研磨步骤不是最佳,那么许多缺陷就会发生,例如絮凝、光泽降低、颜色偏移、浮色/发花、贝纳德漩涡以及沉淀等。
通过研磨过程,聚合物型润湿分散剂通过官能团的吸引作用而锚定于颜料表面。由于它们的空间位阻和静电排斥作用,保持合适的颜料间的距离,这样减少了不受控制的絮凝的倾向,从而保证涂料内部获得足够的稳定性。
本项目中选用嵌段型丙烯酸聚合物作为分散剂,采用NUOSPERSEFX-600和DISPERBYK-190复配使用,制备得到水性涂料。涂料细度满足要求,并且涂料可稳定储存6个月以上,50℃烘箱内储存1个月无硬沉底。实验结果表明,选用该类复合分散剂,可将颜填料研磨至规定细度,制备的涂料储存稳定性优异。
3.2.2流平剂选择涂料施工后,有一个流动及干燥成膜过程,然后逐步形成一个平整、光滑、均匀的涂膜。涂膜能否达到平整光滑的特性,称为流平性。流平不良表现为:刷痕、滚痕、桔皮、缩孔、流挂和针孔等,这些现象的产生降低了涂料的装饰和保护功能。改善涂料的流平性需要考虑加入合适的流平剂,通常需要加入流平剂,可以做到显著降低涂料的表面张力,提高涂料的底材润湿能力和漆膜的流动性、消除Benard旋涡从而防止发花。
本项目中分别选用进口流平剂BYK348和国产流平剂,并与不加流平剂的涂料进行对比,表4可知,加入流平剂后,涂料中发花现象明显改善,国产和进口流平剂流平性均较好,同时,涂层的硬度、耐水性和耐腐蚀性均较优。因此,选用国产流平剂B作为流平剂。
表4不同流平剂流平效果及其对涂膜性能影响表4不同流平剂流平效果及其对涂膜性能影响表4不同流平剂流平效果及其对涂膜性能影响图1不同流平剂流平效果图1不同流平剂流平效果图1不同流平剂流平效果:1#空白样品;2#进口流平剂BYK348;3#国产流平剂B3.2.3增稠剂选择水性涂料中含有大量的颜填料,这些颜填料在分散剂的作用下可以稳定在涂料体系中。然而,在重力作用下,颜料、填料和其他固体物质会有下沉到容器的底部的趋势。考虑到涂料的稳定性和储存周期,降低涂料的沉降速率至关重要。颜料沉降是一个低剪切速率的现象:所涉及的剪切速率小于10-2s-1,所以涂料在这种低剪切速率下的粘度对防止颜料的沉淀至关重要。一般情况下,通过选择增稠剂调高低剪切下的粘度,达到增稠效果,从而延缓颜填料的沉降。另一方面,在施工状态下,特别对于喷涂施工过程,希望涂料的粘度降低,这有利于施工和流平。综合两方面要求,需要涂料有一定的触变性。可以通过加入特定的增稠剂达到触变效果。
表5不同增稠剂增稠效果表5不同增稠剂增稠效果表5不同增稠剂增稠效果流变助剂从性能上可分为高、中、低三种剪切黏度的类型:低剪切黏度的流发助剂能够提供罐内黏度,防止颜料沉降,并有效的控制漆液在立面作业时产生的流挂;提供中高剪黏度的流发助剂能很好的提高水性涂料的丰满度和流平性,而专用提高高剪切黏度的流发助剂则帮助流平、防止飞溅以及提高辊、刷涂施工性能。所以,流发助剂的种类和用量必须根据施工的要求及体系来选定,一般根据施工方法的不同来选定流发助剂类型,往往通过多种剪切黏度的流发助剂来搭配才能达到所需施工效果。
表5列出了不同增稠剂体系对涂料增稠及触变影响。本项目中选用聚氨酯缔合型增稠剂和膨润土组合作为流变助剂。采用CoapurTM830W和膨润土协同使用,可以提供高、中、低的剪切黏度的平衡。所制备涂料既能在低剪切粘度下防止颜料沉降,也能在中高剪切粘度下提高涂料的丰满度和流平性,取得了较好的效果。
3.2.4消泡剂选择涂料制造过程中,颜料和填料的分散、增稠调漆过程中的搅拌、成品涂料在过滤分装过程中产生振动、涂料在调色过程中与色浆混合搅拌,搅拌引入空气,空气在水性涂料中被表面活性剂包裹稳定在涂料中都会产生气泡。存在于漆液中的气泡如不及时消除,漆膜干后,形成不可接受的瑕疵。表6给出了不同消泡剂的消泡表现,可以看出,有机硅类消泡效果较好,相对用量少,但容易产生缩孔;矿物油类消泡剂消泡效果稍差,所以添加量需要增加。综合考虑,消泡效果、涂膜缩孔以及添加量,本项目选择BYK025作为消泡剂。
表6消泡剂种类及性能对照表表6消泡剂种类及性能对照表表6消泡剂种类及性能对照表3.2.5防闪锈剂水性工业漆主要是用水来做稀释剂,是区别于油性工业漆的一种新型环保防锈防腐涂料。因为自干型/低温烘烤型涂料干燥时间较长,水和含铁基材接触很容易出现锈点,一般我们称为“闪锈”。闪锈是由于涂料中的水分与铁表面(如钉头、钢等)的接触产生的。当涂料在一般环境(如潮湿气候环境)施工时,出现这种闪蚀的可能性更大。为了解决闪锈问题需要在配方中添加抗闪锈助剂。
目前市场上抗闪锈剂主要应用两类产品。一类是价格低廉的亚硝酸盐,众所周知,亚硝酸盐有剧烈的生物毒性,过量使用和排放会引起环境生物的急性中毒,而且由于其良好的水溶性,对漆膜耐水性和长期防腐性能也有不利影响。另外一类是有机金属盐和改性锌螯合物或者为二者的复配物,由于这类产品目前在国内没有人生产,产品都是依靠进口,成本较高,制约了这类产品大范围应用。
表7中列出了不同类型抗闪锈剂的效果。本项目中选用一种含有多种缓蚀剂成份的有机螯合物ZT-709,该防闪锈剂能有效抑制水性涂料涂刷在铁质底材上后的干燥过程中出现的闪锈现象。该产品不会对漆膜产生任何不利的影响,而且在干燥过程中由于绝大部分转变成了不溶于水的络合物,相当于使被涂装的金属表面产生钝化膜,从而提高涂层的耐腐蚀性能,形成的络合物在防闪锈的同时可以有效提高涂料干膜的防锈性能和耐盐雾性能。
3.3.1颜料、填料选择颜料和填料是涂料的重要组成部分,颜料和填料不仅能保证涂料具有良好的遮盖力、丰富的色彩,还能赋予涂膜施工各项特殊功效。其中,颜料是涂料色漆不可或缺的成份之一,其作用除了为涂膜提供色彩装饰外,还可以为涂料提供更多的物理和化学性能的改善,如遮盖性、耐光性、耐候性、耐化学品性、光泽和机械强度等。填料在涂料中的主要作用包括两方面:一是填充作用,降低成本;二是通过加入填料改变涂膜或漆料的物理和化学性质。与颜料相比,填料具有成本低、吸油量低和较易分散等优点。
本文中根据客户提供的标准工件进行调色,选用钛白粉、碳黑、铁黄等作为着色颜料,添加沉淀硫酸钡、滑石粉等作为填料,采用分散剂研磨制备颜填料浆,得到与标准工件颜色一致的涂料。
3.3.2防锈颜料涂料保护金属腐蚀最重要的是取决于所用的树脂体系(包括固化剂),同时在很大程度上也取决于所选择的防锈颜料,涂料的防腐性能是树脂体系与防锈颜料相互共同作用的结果。防腐涂料的性能会因添加了防锈颜料而受到明显的正面影响。因此,当我们要用涂料使金属免于腐蚀的时候,根据所采用的树脂体系来选择防锈颜料就成为一个起主导作用的问题。按其作用机理,防锈颜料可分为物理防锈颜料和化学防锈颜料,以及兼具物理和化学机理的综合型防锈颜料。化学防锈颜料基于其本身的化学活性,在金属腐蚀过程中,与金属表面的金属离子反应生成一层致密的钝化膜来抑制腐蚀过程,或依据电化学原理,通过牺牲阳极来达到保护金属的目的。常用的此类防锈颜料有:磷酸盐系、改性磷酸盐系、离子交换型颜料等。磷酸盐系作为含铅、铬颜料的替代品之一,广泛用于涂料中作为化学防锈颜料,是目前用量最大、应用最广的无毒防锈颜料。磷酸盐系防锈颜料的作用机理复杂,正磷酸锌的主要防锈机理为:
正磷酸锌的主要防锈机理正磷酸锌的主要防锈机理该类防锈颜料能与涂料中的羟基、羧基等进行化学结合,也能在金属表面生成颜料-漆料-底材的高分子络合物,阻止锈的形成和扩蚀。本项目选用磷酸锌作为防锈颜料,金属表面形成钝化膜,可以有效地抑制水、氧等物质的侵蚀。为了提高涂料的防腐蚀性,选择三聚磷酸铝APW-Ⅱ与磷酸锌配用。由于三聚磷酸铝的“双重防锈”机理,解聚反应形成三聚磷酸根离子(P3O105-)它比磷化处理的PO43+离子,对Fe3+离子以及各种金属离子有更强的螯合力,在被涂物表面形成卓越的钝化膜,对钢铁等金属物体的腐蚀具有极强的抑制作用。通过两种防锈颜料配合使用,取得了较好的防锈效果。
3.4涂料施工3.4.1施工工艺介绍汽车悬架总成的喷涂工艺包括以下几个步骤:①工件表面处理;②喷涂;③固化。具体的施工步骤包括以下几个部分:脱脂→水洗→表调→磷化→水洗→预烘→喷涂1→流平→喷涂2→烘烤固化→喷修补漆→工件下线,详细见图3所示。
图3汽车平衡悬架总成施工工艺示意图图3汽车平衡悬架总成施工工艺示意图脱脂是指工件在进行化学成膜之前,必须先除去表面的油脂及附着在表面的灰尘、锈迹、金属细铁屑等污物,才能保证转化膜化学反应的顺利进行,使转化膜与金属基体牢固结合,获得质量优良的转化膜。除油的方法包括机械法、化学法两类。本项目生产线中采用化学法(碱液清洗)。
表调就是表面调整,是把工件放入装有表调液的槽子里进行表面调整处理的过程。
表调的作用①除油;②促进零件表层的活力,还能形成大量极细的结晶层,加快磷化膜的形成。使磷化膜更细腻,膜细致均衡。③可以改善磷化性能,能减少磷化一半时间,降低磷化的温度条件;④减少成本,可以降低磷化液的消耗。
磷化是一种化学与电化学反应形成磷酸盐化学转化膜的过程,所形成的磷酸盐转化膜称之为磷化膜。磷化是常用的前处理技术,原理上应属于化学转换膜处理,主要应用于钢铁表面磷化,有色金属(如铝、锌)件也可应用磷化。磷化的目的主要是:给基体金属提供保护,在一定程度上防止金属被腐蚀;用于涂漆前打底,提高漆膜层的附着力与防腐蚀能力;在金属冷加工工艺中起减摩润滑作用。磷化可以增强涂装涂层与工件间结合力,同时可以提高涂装后工件表面涂层的耐蚀性,另一方面也可以显著提高装饰性。
本项目中施工过程中喷涂采用无气喷涂,以喷枪为工具,利用高压将涂料吹散、雾化并喷在被涂饰表面,形成连续完整涂层。其中,喷涂时压力保持在0.35~0.6MPa,压力过小,漆液雾化不良,表面会形成麻点;压力过大易流挂,且漆雾过大,既浪费材料又影响操作者的健康。喷嘴与工件表面的距离一般以300~400mm为宜,喷嘴垂直于工件物面,尽量减少斜向喷涂,喷涂时要下一道覆盖上一道的1/3或1/4,喷涂应均匀无明显漏喷和过喷现象,工件表面无明显流挂现象。喷涂结束后,工件传输进入烘道,烘道实测温度为70~85℃,烘烤时间为18~20min,烘烤固化冷却后工件下线,检查有无漏喷,采用溶剂型涂料修补,最后工件下线。
3.4.2温度和湿度影响水性漆中水的含量超过了60%,由于含水量高,水性漆中稀释剂的主体是水,水的挥发与喷漆室的温度、湿度有较大关系。当湿度一定时,随着温度的升高,水的挥发度增加;当温度一定时,则湿度增加,水的挥发受阻;当相对湿度过大时,水份挥发很慢,施工过程中易产生流挂等漆膜缺陷。温度和湿度是喷房内所需控制的最重要的工艺参数。
关于温度对涂料成膜及性能的影响如下:与溶剂型涂料类似,施工环境温度偏高时,水的挥发速率快,涂料喷涂到基材表面未得到充分的润湿,涂膜未来得及流平即干燥成膜,从而造成涂膜外观不良;温度偏低时,水的挥发速率慢,涂膜易出现流挂。因此,与溶剂型涂料相比,水性涂料的施工温度范围比较窄,严格控制水性涂料的施工温度是保证良好涂膜外观的必要条件。需要特别指出的是,喷涂施工前工件需要进行前处理,脱脂和磷化后会对工件进行加热预烘,因此工件在喷涂时温度一般大于室内温度,经过测定工件温度大约为25~35℃之间。通过实验证实,喷房温度在10~30℃均可,前处理水洗后预烘烤温度为80~100℃,喷涂前工件温度约为20~35℃之间较为适宜。当室温较低时,提高预烘温度,可以防止涂料流挂;当室温过高时,可适当降低预烘温度,防止涂料干燥过快,流平不好,造成漆膜外观不好。
表8环境温度及工件温度对漆膜外观影响表8环境温度及工件温度对漆膜外观影响同样,若空气中的相对湿度偏大,水的挥发速率慢,不利于水性涂膜的干燥,时间延长会影响涂膜的性能指标(如盐雾老化等);相对湿度偏小,水的挥发速率快,不利于水性涂料的流平,降低涂膜的外观效果。因此,要严格控制水性涂料喷涂时的相对湿度。通过实验证实,相对湿度控制在30%~75%比较适宜。
3.4.3施工黏度涂料在储存过程中,为了防止涂料体系中颜填料的沉降,一般原漆的黏度要比实际施工黏度大。在涂料施工过程中,再通过兑水稀释达到合适的施工黏度再进行喷涂。施工时黏度太低,涂膜容易流挂,涂膜厚度很难达到要求,涂层不丰满;黏度太高,对涂膜流平性不利,涂层不平整。此外,黏度交大,喷涂困难,涂膜成膜质量不好。本项目中的涂料施工黏度和施工性及涂料流平性关系见表9所示。由表9中数据可知,施工黏度控制在50~100s较为合适,喷涂容易,涂层流平性好,涂层丰满度高。
表9施工黏度与施工性及涂层流平性关系表9施工黏度与施工性及涂层流平性关系3.4.4性能测试采用制备的涂料分别喷涂标准样板和汽车悬架工件,分别测试性能,性能见表10,图4为喷涂施工现场图,图5为喷涂施工后平衡悬架示意图。由表10中数据可知,涂层平整光滑,无泡,外观良好。涂层光泽在45~55之间。涂料对底材附着力较好,硬度达到H。特别地,喷涂后的样板和工件具有较好的耐水和耐盐雾性能。根据实验数据可知,本项目涂料综合了水性环氧酯涂料和水性丙烯酸涂料的优点。产品可常温干燥,具有良好漆膜附着力、耐腐蚀性能优异、存放稳定性好,可代替传统溶剂型涂料,可广泛应用于汽车零部件涂料领域。
表10标准样板及工件涂层性能表10标准样板及工件涂层性能*工件性能特指从工件上取下的部位,材料为钢材。
图4喷涂施工现场展示图4喷涂施工现场展示图5涂装后平衡悬架工件图5涂装后平衡悬架工件3.5产品VOC数据2015年1月26日,国家财政部与国家税务总局联合发布了“关于对涂料征收消费税的通知”(以下简称“通知”),引起行业广泛关注。“通知”要求自2015年2月1日起对涂料征收消费税,在生产、委托加工和进口环节征收,适用税率均为4%。“通知”特别指出,对施工状态下挥发性有机物(VOC)含量低于420克/升(含)的涂料免征消费税。在涂料行业整体利润率已经相当微薄的情况下征收4%的消费税,对于涂料行业及企业而言,无疑带来了巨大的冲击。为了推动行业转型,提升企业环保产品的比重,规避或减轻被征税带来的冲击,采用水性涂料替代溶剂型涂料是一个有效的解决方案。根据GB/T23986-2009《色漆和清漆挥发性有机化合物(VOC)含量的测定-气相色谱法》(等同采用ISO11890-2:2006,该方法适用于VOC含量在0.1%和15%之间(质量分数)的样品),对本项目的水性涂料产品测试VOC含量,结果如表11所示。
表11产品VOC含量测试结果表11产品VOC含量测试结果由表1中实验结果可知,本项目中水性涂料产品施工状态下挥发性有机物(VOC)含量低于420克/升,可免征消费税。
四、结论
本文中选用一种自乳化型水性环氧酯树脂,添加特定的丙烯酸乳液作为成膜物,采用分散剂将颜料、填料研磨成为颜料浆,添加合适的涂料助剂,制备丙烯酸改性环氧酯水性涂料,将所制备涂料应用于汽车底盘及零部件,研究了涂料配方及相应产品的施工工艺条件,得出如下结论:
1、采用水性环氧酯和水性丙烯酸乳液作为成膜树脂,所制备产品既保持了水性环氧酯可以空气交联,耐水和耐盐雾性能优异的特性,同时具有丙烯酸乳液快干、耐碱性好、耐候性好等优点,综合性能优异。
2、涂料配方中采用丙烯酸聚合物作为分散剂研磨颜填料,选用环保的磷酸锌作为防锈颜料,在配漆过程中加入聚醚改性有机硅作为流平剂,选用聚氨酯缔合型增稠剂作为流变助剂,同时加入有机螯合物作为防闪锈剂,得到细度小于40μm,储存稳定性优异的水性涂料。
3、涂料施工过程中,喷房内的温度和湿度需要调整在合适范围。相对湿度控制在30%~75%比较适宜,喷房温度在10~30℃,控制前处理后水洗预烘后工件温度在20~35℃,所得涂料外观较好。
4、施工采用无气喷涂,喷涂时涂料黏度控制在50~100s喷涂容易,涂层流平性好,涂层丰满度高。
5、采用本项目产品施工的工件涂层外观良好。涂料对底材附着力较好,硬度达到H。喷涂后的样板和工件具有较好的耐水和耐盐雾性能,可代替传统溶剂型涂料,在汽车零部件领域具有广泛的应用前景。
6、本项目的水性涂料产品安全环保,VOC含量仅为182g/L,保护环境,符合绿色环保要求。
更多关于材料方面、材料腐蚀控制、材料科普等方面的国内外最新动态,我们网站会不断更新。希望大家一直关注中国腐蚀与防护网http://www.ecorr.org
责任编辑:班英飞
《中国腐蚀与防护网电子期刊》征订启事
投稿联系:编辑部
电话:010-62313558-801
邮箱:ecorr_org@163.com
中国腐蚀与防护网官方 QQ群:140808414
相关文章
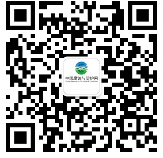
官方微信
《中国腐蚀与防护网电子期刊》征订启事
- 投稿联系:编辑部
- 电话:010-62313558-806
- 邮箱:fsfhzy666@163.com
- 中国腐蚀与防护网官方QQ群:140808414
点击排行
PPT新闻
铝合金LDH自修复自抗菌膜层构建
点击数:466
碳钢及合金钢应用与区别
点击数:393