1.化学转化
镁合金与转化液发生化学反应生成一层保护性钝化膜的处理技术称为化学转化法。化学转化是一种比较成熟的表面处理工艺,国内航天航空、军工企业在20世纪60 年代就已应用。按照转化液的不同,生成的化学转化膜分为:铬酸盐转化膜、磷酸盐转化膜、锡酸盐转化膜、高锰酸盐转化膜、植酸盐化学转化膜、稀土金属盐转化膜、钨酸盐转化膜、氟锆酸盐转化膜、钼酸盐转化膜等。化学转化方法的主要特点是设备简单、成本低,适应于构复杂件及大件的处理,但是化学转化膜层薄(0.5~3μm)且为多孔结构,对镁基体保护有限,现多用于零件制备过程中的工序间防护和涂装前处理。由于部分转化液有毒会对环境造成污染,国际上已经开始禁止使用相应的化学转化工艺,因此,其未来的发展方向是绿色环保的化学转化技术。
2.阳极氧化
利用电解作用在金属表面成膜的过程称为阳极氧化,阳极氧化膜为多孔双层结构,较厚的多孔层为外层,较薄的致密层为内层,膜层的成分由合金元素的氧化物和沉积的氧化物共同组成。氧化膜的厚度为10~40μm左右。阳极氧化膜空隙大、无规则、分布不均匀,如果不进行封闭,耐蚀性非常差,因此,需进行后续的封孔处理,使其既美观又耐蚀。
早期的阳极氧化处理是含铬的有毒化合物处理液,代表性的工艺有Dow17。后逐渐发展了以磷酸盐、高锰酸盐、可溶性硅酸盐、硫酸盐、氢氧化物和氟化物为电解液的阳极氧化工艺,如较有名的HAE工艺。传统的HAE工艺获得膜层的耐腐蚀等级为8级。戎志丹等,研究了一种新型无铬环保型镁合金阳极氧化配方及工艺,其研究结果表明,氧化膜主要由MgO和MgAl O 组成,阳极氧化新工艺所获得的膜层的耐腐蚀等级为9级。
阳极氧化膜的厚度、强度、耐蚀性及耐磨性都比化学转化膜好,因此,经封闭处理后可以作为中等腐蚀环境条件下的防护层。但由于膜层孔隙较大、分布不均匀,一般也作为涂装底层。
3.微弧氧化
微弧氧化又叫等离子体微弧氧化,是在阳极氧化的基础上发展起来的,在金属表面原位生长陶瓷层的一种表面处理技术。微弧氧化的生成陶瓷膜层的过程一般为:将Al、Mg、Ti及Zr等轻金属或其合金置于电解质溶液中,当施加在电极两端的电压达到临界值时,工作电极表面会出现电晕、辉光、火花放电及弧放电等现象,这种微区放电现象在工作电极表面不同的位置不断间歇重复出现,表金属面生成的氧化膜被击穿,瞬间温度可达2000℃,氧化膜在高温高压作用下熔融,等离子弧消失以后,熔融物急速冷却形成陶瓷层。微弧氧化膜层的生长是一个“成膜—击穿—熔化—烧结—再成膜”的多次循环过程。微弧氧化装置的基本构成如下图所示。
镁合金微弧氧化形成的膜层主要分为过渡层、致密层、疏松层。疏松层是由很硬的、孔隙较大的物质组成,表面疏松且粗糙,易打磨掉。致密层是微弧氧化层的主体,约占氧化层总厚度的60% ~70%,该层致密、孔隙小,每个孔隙的直径约为几微米,孔隙率在5%以下,主要是镁的氧化物,硬度高且耐磨。过渡层为界面层,是微弧氧化膜层与基体的交界处。过渡层凹凸不平,与基体相互渗透,使微弧氧化膜层与基体结合牢固,属典型的冶金结合。
当微弧氧化基体材料选定时,微弧氧化膜层的厚度与形貌主要受到电解液体系、电源类型、工作模式、电参数等的影响。与化学转化、阳极氧化技术相比,镁合金微弧氧化制备的膜层厚度可控,耐蚀性和耐磨性也更优异,该方法已被证明是提高镁合金的耐蚀和耐磨性能的有效途径,但微弧氧化膜层表面的微孔隙是限制耐蚀性提高的主要因素,需采用有效的封孔技术才能大幅度提高镁合金的耐蚀性能。
4.离子注入
离子注入是在高真空状态下,在十至数百千伏电压的静电场作用下,经加速的高能离子以高速冲击镁材表面,离子被嵌入并在基体的间隙位置被中和形成固溶体,从而改变基体的表面性能(硬度、抗疲劳性、耐蚀性)。注入的元素主要有N、O、Ti、Al 和Zn 等。耐蚀性的提高与注入离子的种类、注入的离子量以及“注入影响区”范围有关。离子注入使镁合金表面的组织和成分发生变化,相当于生成一种新的合金表面,保证了与基体的整体性,解决了其他方法生成的膜层与基体结合力的问题。但离子注入改性层的厚度一般较薄(50~500nm),往往无法满足所需要的表面性能。离子注入工艺过程中为高温环境,会影响基体的力学性能,注入过程要气体保护,成本高。
5.激光表面改性
激光表面改性技术是通过激光等高能束流使基体表面预先涂覆的膜层和部分基体熔化,或者在表面熔化的同时注入某些粉末,膜层或表面在熔池中液态混合后发生快速凝固,从而在表面形成耐蚀性较好的合金薄层。按照激光与基体作用时的功率密度、作用时间及方式不同,激光表面改性一般可分为:激光表面熔凝处理、激光表面合金化和激光表面熔覆。相关研究表明,激光表面改性能够提高镁合金表面的耐蚀性。
激光熔覆装置构成
激光表面改性技术的特点为:激光作用在基体表面能量集中,加热快,冷速大,对基体的热影响小,工件处理后的变形小,容易实现自动控制。受激光束作用于工件的方式限制,激光不一定覆盖工件所有表面,所以该方法不适用处理复杂形状的零件。由于所需设备昂贵,该技术不宜进行大面积处理。镁合金激光表面改性技术还不成熟,工业应用较少。陈长军等采用激光多层熔敷的方法为相关军工厂修复了ZM2、ZM5和ZM6镁合金成品件上的腐蚀坑、疏松等缺陷。
6.有机涂装
该方法是通过在镁合金表面喷涂有机涂层将基体与腐蚀介质隔绝已达到耐腐蚀的目的。喷涂有机涂层可以直接用于镁合金表面防护,但更多是与其他表面处理方法联合使用,作为最外层的防护层来提高工件的耐蚀性。
常用的有机涂层材料为:环氧树脂、乙烯树脂、聚氨酯等。工业部门常常采用在工件表面涂油、涂漆的方式进行防腐。有机涂层具有品种和颜色多样、适应性广、成本低及工艺简单的优点。
有机涂层还有一类粉末型的,其具有无溶剂、污染、厚度均匀及较好的耐蚀性等特点,近年来在汽车和电脑外壳等镁合金零部件上的广泛应用。但是,粉末型涂层要求加热固化成膜温度较高,会影响到基体性能。
7.金属及化合物涂层
金属涂层主要是采用电镀和化学镀的方法在镁合金基体表面涂覆一层金属涂层。镁合金具有高的反应活性,属于难电镀材料,虽然镁合金电镀方法在不断发展完善,但是工业界的应用很少。化学镀工艺较为成熟,镁合金化学镀应用最广的为化学镀镍,其是通过自催化还原反应沉积Ni-P或Ni-B合金镀层的工艺。镁合金化学镀镍分为沉锌法和直接化学镀镍。镁合金化学镀镍工艺目前已用于实际生产。经过化学镀镍得到镀层为规则、均匀、致密的球形结点结构,且胞体具有明显的界限,镀层厚度均匀,具有较高的硬度和耐磨性,耐蚀性能优良。镁合金电镀、化学镀的缺点是前处理中的Cr、F 及镀液对环境污染严重;镀层中含有重金属元素,增加了回收的难度与成本。
除电镀、化学镀方法外,还有学者研究热扩散和热喷涂铝的方法,在镁合金表面形成镁铝化合物的扩散层,从而提高工件表面的耐蚀性和耐磨性。但是,热扩散和热喷涂工艺中均存在高温保温过程,因此有可能会影响基体力学性能以及导致零件变形。冷喷涂是相对较新的一种喷涂技术,它是利用高速压缩气体将金属或者陶瓷粉末加速后喷涂到基材表面,通过金属粉末塑性变形形成致密的涂层。与传统的热喷涂相比,冷喷涂工艺过程温度低,非常适合镁合金等易氧化或对热较敏感的基材,冷喷涂铝合金等在镁合金耐蚀防护领域展现出良好的应用前景。
利用气相沉积方法也可获得一定耐蚀性的金属及化合物膜层。气相沉积分为物理气相沉积(PVD)和化学气相沉积(CVD)。气相沉积膜层是在等离子体条件下获得的,沉积层被电离、激发为活性粒子,使得沉积层的组织细密、结合良好。目前已通过PVD等技术在镁合金表面制备出TiN、AlN、CrN以及Al O 等化合物涂层。但制备的化合物涂层的致密度不够,存在空隙,因此PVD方法制备化合物涂层的耐蚀性还需进一步解决。德国学者采用CVD技术在镁合金表面沉积铝膜,所获得的膜层具有良好的耐蚀性。
气相沉积原理图
8.溶胶-凝胶法
溶胶-凝胶法制备涂层过程主要是以金属有机/无机化合物或两者混合物的液体化学试剂(或固体粉末溶于溶剂形成的溶液)为前躯体,在液相下均匀混合,经过水解、缩聚等化学反应过程,反应生成物聚集成1~9 nm 左右的粒子并逐步形成稳定的溶胶体系。以溶胶为原料对镁合金基材进行涂覆处理,溶胶膜逐渐凝胶化形成以前躯体为骨架的三维或颗粒空间网络结构,经过干燥处理后脱去吸附水及化学结合水等溶剂而成为多孔结构的干凝胶膜,最后在一定温度下进行烧结热处理消除干凝胶中存在的气孔即得到所需的涂层。
二氧化硅溶胶
溶胶-凝胶法具有设备简单,工艺过程温度低,可以大面积在不同形状、不同组分的镁基底上制备薄膜,并且能有效控制薄膜的成分和微观结构。目前,国内外学者在利用溶胶-凝胶技术实现对镁合金防护方面取得了一定的进展,研究和开发了多种有机/无机杂化涂层、还有缓释因子的杂化涂层、杂化涂层与化学转化、电化学氧化、微弧氧化相结合的复合涂层等一系列防护涂层,有效提高了镁合金的耐蚀性。这些涂层体系中与其他表面处理方法相结合的涂层对基体的附着能力表现优异,含缓蚀因子的杂化涂层具备自修复能力,而单一的溶胶-凝胶涂层更容易出现溶胀和破坏,不具备长期抗蚀性。另外,除了开发长效耐腐蚀涂层外,还应充分考虑环境、工艺成本、操作工艺等问题。
结束语
经过上面的介绍,相信大家对镁合金表面处理技术有了一个比较初步的了解。化学转化、阳极氧化、微弧氧化、化学镀镍、有机涂装相对来说技术成熟,已经在实际生产中应用。激光表面改性、气相沉积、溶胶-凝胶法等应用在镁合金防腐还处在研究阶段,进一步实现工业应用还有若干问题需要解决。在众多的表面处理方法中,似乎没有那个方法是“完美”的,都或多或少的存在一定的问题。在实际应用中,设计师往往根据镁合金零件的使用环境和要求,采用多种表面防护方法相结合。相信随着镁合金应用的增多,镁合金表面处理方法会继续得到发展,但不论是那种方法,要想实现真正的工业应用,除了具备优良的防腐性能外,还应考虑生产效率、工艺成本、设备工艺的复杂程度、操作工艺性、对基体性能的影响以及对环境的影响等因素。
免责声明:本网站所转载的文字、图片与视频资料版权归原创作者所有,如果涉及侵权,请第一时间联系本网删除。
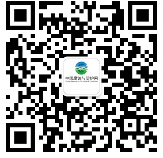
官方微信
《腐蚀与防护网电子期刊》征订启事
- 投稿联系:编辑部
- 电话:010-62316606-806
- 邮箱:fsfhzy666@163.com
- 腐蚀与防护网官方QQ群:140808414