在金属学中,把高于金属再结晶温度的加工叫热加工,热加工可分为金属铸造、热轧、锻造、焊接和金属热处理等工艺。近十年来,热加工在机械制造行业普遍得到重视,推动了产品质量的改进和制造效率的提升。在现代航空制造业中,热工艺水平是技术最密集、最能代表航空制造水平的高技术领域之一。随着技术的进步,热加工零件要求越来越高,加工方法和工艺设计在不断进步,热加工技术正经历着深刻的变革。
金属铸造
铸造是人类掌握比较早的一种金属热加工工艺,已有约6000年的历史。中国约在公元前1700~前1000年之间已进入青铜铸件的全盛期,工艺上已达到相当高的水平。中国商朝的重875公斤的司母戊方鼎,战国时期的曾侯乙尊盘,西汉的透光镜,都是古代铸造的代表产品。
古代铸造青铜器
18世纪的工业革命以后,蒸汽机、纺织机和铁路等工业兴起,铸件进入为大工业服务的新时期,铸造技术开始有了大的发展。进入20世纪,铸造的发展速度很快,其重要因素之一是产品技术的进步,要求铸件各种机械物理性能更好,同时仍具有良好的机械加工性能;另一个原因是机械工业本身和其他工业如化工、仪表等的发展,给铸造业创造了有利的物质条件。
在这一时期内开发出大量性能优越,品种丰富的新铸造金属材料,如球墨铸铁,能焊接的可锻铸铁,超低碳不锈钢,铝铜、铝硅、铝镁合金,钛基、镍基合金等,并发明了对灰铸铁进行孕育处理的新工艺,使铸件的适应性更为广泛。
现在铸造技术已成为航空制造技术中关键技术之一,因此铸造的技术进步对加速航空产品的更新换代,提高新机种的性能,缩短产品的制造周期,大幅度减轻重量,以及减少能源消耗和成本上都具有非常重要的意义。特别是在航空发动机的制造上,铸造技术更有其重要的意义。
如燃气涡轮发动机从第二次世界大战以来其最大推力提高了50倍,推动比已达到10,涡轮叶片的工作温度也提高了几百度,而燃油消耗却降低为原来的一半。为此,涡轮叶片从材质到结构都改变了,要生产出这些性能更好的涡轮叶片就要求铸造技术的进步。
上图是1960年以来涡轮叶片材质及工艺发展情况。涡轮叶片的材质从IN100、B1900到MM200、MM247,再发展到PWA1480、PWA1484、CMSX-11。同时因凝固技术的发展和应用,生产涡轮叶片的工艺,则从传统的普通铸造到定向凝固铸造,再发展到单晶铸造叶片,另外,为了降低涡轮叶片工作温度、叶片结构从实心向空心发展。如果没有铸造技术的进步就很难生产出新型的涡轮叶片空气的型芯。就难以保证发动机性能的提高,因此说铸造技术是航空工业的关键技术之一。铸件在航空飞行器中,尤其是航空发动机中所占的比重也逐年增加。如美国GE公司制造的航空发动机1985年时铸件只占发动机重量的18%,而到1994年已到44%。
航空工业中使用的发动机零件、结构件、附件有相当数量的铸件。这些铸件材料种类繁多,所用铸造方法也很多。主要材料有高温合金、不锈钢、钛合金和铝合金等有色合金,以及复合材料等。随着航空工业的发展,新材料研制和使用在不断前进,品种也在不断增加。所使用的铸造方法有熔模铸造、石膏型铸造、金属型铸造、压力铸造、低压铸造、离心铸造等。
随着发动机叶片的越来越复杂和精密,对于空心复杂叶片,熔模铸造已经成为其生产的独一无二的工艺技术。另外,为了减轻飞机重量、降低油耗、减少制造和维修周期,近年来很多结构件开始用大型复杂薄壁整体件代替组装件,在生产此类铸件上熔模铸造业具有优势。因此,在航空工业中使用的众多铸造技术中,熔模铸造技术是应更加被关注的铸造技术。
焊接技术
焊接技术是热加工技术的一种重要技术,是通过加热、加压,或两者并用,使同性或异性两工件产生原子间结合的加工工艺和联接方式,焊接既可用于金属,也可以用于非金属。
焊接技术是随着金属的应用而出现的,古代的焊接方法主要是铸焊、钎焊和锻焊。中国商朝制造的铁刃铜钺,就是铁与铜的铸焊件,其表面铜与铁的熔合线婉蜒曲折,接合良好。古代焊接技术长期停留在铸焊、锻焊和钎焊的水平上,使用的热源都是炉火,温度低、能量不集中,无法用于大截面、长焊缝工件的焊接,只能用以制作装饰品、简单的工具和武器。
20世纪初,碳极电弧焊和气焊得到应用,同时还出现了薄药皮焊条电弧焊,电弧比较稳定,焊接熔池受到熔渣保护,焊接质量得到提高,使手工电弧焊进入实用阶段,电弧焊从20年代起成为一种重要的焊接方法。1957年美国的盖奇发明等离子弧焊;40年代德国和法国发明的电子束焊,也在50年代得到实用和进一步发展;60年代又出现激光焊等离子、电子束和激光焊接方法的出现,标志着高能量密度熔焊的新发展,大大改善了材料的焊接性,使许多难以用其他方法焊接的材料和结构得以焊接。此外在1956年,美国的琼斯发明超声波焊;苏联的丘季科夫发明摩擦焊;50年代末苏联又制成真空扩散焊设备。
下面就简单地介绍几个热门的焊接工艺:
电子束焊
电子束焊是在真空环境下利用会聚的高速电子流轰击工件接缝,将电子动能转变为热能,使被焊金属熔合的一种焊接方法。作为高能束流加工技术的重要组成部分,电子束焊具有能量密度高、焊接深宽比大、焊接变形小、可控精度高、焊接质量稳定和易实现自动控制等突出优点。也正是这些特点,电子焊接技术在航空、航天等领域已得到广泛应用。
在航空制造业中,电子束焊接技术的应用,大大提高了飞机发动机的制造水平,使发动机中的许多减重设计及异种材料的焊接成为现实,同时为许多整体加工难以实现的零件制造提供一种加工途径。
搅拌摩擦焊
搅拌摩擦焊技术是英国焊接研究所在1991年发明的新型固相连接技术。它是利用一种非耗损的搅拌头、高速旋转着压入待焊界面,摩擦加热被焊金属界面使其产生热塑性、在压力、推力和挤压力的综合作用下实现材料扩散连接,形成致密的金属间固相连接。它具有无飞溅,无需焊接材料,不需要保护气体,被焊材料损伤小,焊缝热影响区小,焊缝强度高等特点。
美国Eolipse公司在Eolipse N500型商务飞机制造中首次大规模成功运用可FSW技术,包括飞机蒙皮、翼肋、弦状支撑、飞机地板以及结构件的装配等基本上全部利用搅拌摩擦焊技术制造,70%的铆接被焊缝替代,不仅极大地提高了十倍,生产成本大大降低。波音公司将搅拌摩擦焊技术用于C-17和C-130运输机地板的制造,利用搅拌摩擦焊代替紧固件连接,简化了地板设计并提高了构件的生产效率。
扩散焊
扩散焊又称扩散连接,是把两个或两个以上的固相材料紧压在一起,置于真空或保护气氛中加热至母材熔点以下温度,对其施加压力使连接界面微观塑性变形达到紧密接触,再经保温、原子相互扩散而形成牢固结合的一种连接方法。它具有接头质量好,焊后无需机加工,焊件变形量小,一次可焊接多个接头等优点。扩散焊已在直升机上钛合金旋翼桨毂、飞机大梁、发动机机匣以及整体涡轮等方面试用,涡轮叶片、钛合金宽叶弦蜂窝夹层风扇叶片等的扩散焊已应用于生产。
锻造技术
锻造技术早在几千年前就被人们所掌握。到了近代,随着工业革命的进行,锻造技术才真正有了长足的发展。1842年,内史密斯发明了双作用锤,1860年,哈斯韦尔发明了第一台自由锻水压机。这些设备的出现标志着锻压技术成为一门具有影响力的科学的开始,之后学者又更系统的论述了压力加工原理,从而有了如今的锻造技术。
随着航空产业的不断发展,对航空装备极端轻质化与可靠化的追求越来越急迫,对材料和材料和锻件的性能要求也越来越高。钛合金、高温合金等材料的应用日益广泛,以航空工业为例,F-22和F-33飞机钛合金用量已分别高达39%和27%,先进航空发动机中高温合金和钛合金重量占发动机总结构重量的55%和65%。而高温合金、钛合金属于难变形材料,即加工参数范围狭窄、变形抗力大、组织性能对加工过程十分敏感。所以锻造技术在航空制造领域的应用相比其他工业领域难度较大。
精密锻造技术
精密锻造是指零件锻造成形后,只需少量加工或不再加工即符合零件尺寸精度要求的成形技术。实现精锻成形的途径主要有精化毛坯、即直接锻造出满足精密机加工要求的毛坯。精锻件,整个或零件一些部分直接采用精锻工艺加工而成,从而减少机加量。目前应用于生产的精密锻造工艺很多,按成形温度不同可以分为热精锻、冷精锻、温精锻、复合精锻等。
等温锻造技术
等温锻造技术是一种先进的近净成型技术。它是指在整个模锻过程中,模具和坯料的温度保持相同或者相近的恒定值,并以较慢的变形速度完成变形的一种模锻技术。
目前等温锻造技术已经在工业的各个领域特别是航空工业领域得到了广泛的应用,涉及的材料有钛合金、高温合金、铝合金、镁合金、金属间化合物、金属复合材料等,研制的等温锻件种类有盘类、轴类、叶片类以复杂结构件等。美国、俄国在等温铸造技术领域一直处于国际领先。利用等温铸造技术,美国铝业公司、NASA等制造了飞机水平安定面连杆、TAZ-8A高温合金的涡轮叶片、Ti6Al4V2Sn钛合金起落架前轮、TC4钛合金框架加强板、隔舱及轴承支座等零件。目前有国外研究者在探索使用其他新型材料用作模具材料,如陶瓷材料、碳纤维复合材料等,这是目前等温铸造技术研究的一个热点。
粉末锻造技术
粉末锻造是将传统的粉末冶金和精密锻造相结合的一种近净成形工艺。粉末锻造以粉末为原料,利用粉末冶金方法先制取具有一定形状和尺寸的多孔顶成形坯,简称预型件,在保护气氛下烧结和锻前加热结合为一个工序,然后很快转移到闭式锻模中一次锻压成型,其工艺如下图。
粉末锻造工艺
粉末锻造技术保持了粉末冶金近净成型的优点,具有材料利用率高,尺寸精度高,机械加工量少等特点。烧结后的预形件一次锻压后的致密度可达到98%以上,内部均匀致密,晶粒尺寸小,具有相当于传统铸件甚至超过传统铸件的力学性能。由于粉末锻造温度低,无氧化皮,模具表面磨损小,且锻造单位压力远低于普通模锻,与普通模锻相比,其模具寿命可提高10-20倍以上。此外,粉末锻造技术采用粉末作为原料,可以根据零件的实际工况和性能要求,在大范围内调整材料成分,以获得最佳性价比。
热处理技术
在从石器时代进展到铜器时代和铁器时代的过程中,热处理的作用逐渐为人们所认识。早在公元前770至前222年,中国人在生产实践中就已发现,钢铁的性能会因温度和加压变形的影响而变化。公元前六世纪,钢铁兵器逐渐被采用,为了提高钢的硬度,淬火工艺遂得到迅速发展。
1863年,英国金相学家和地质学家展示了钢铁在显微镜下的六种不同的金相组织,证明了钢在加热和冷却时,内部会发生组织改变,钢中高温时的相在急冷时转变为一种较硬的相。法国人奥斯蒙德确立的铁的同素异构理论,以及英国人奥斯汀最早制定的铁碳相图,为现代热处理工艺初步奠定了理论基础。
二十世纪以来,金属物理的发展和其他新技术的移植应用,使金属热处理工艺得到更大发展。一个显着的进展是1901~1925年,在工业生产中应用转筒炉进行气体渗碳;30年代出现露点电位差计,使炉内气氛的碳势达到可控,以后又研究出用二氧化碳红外仪、氧探头等进一步控制炉内气氛碳势的方法;60年代,热处理技术运用了等离子场的作用,发展了离子渗氮、渗碳工艺 ;激光、电子束技术的应用,又使金属获得了新的表面热处理和化学热处理方法。
在航空航天工业发展的过程中,工作人员在极力地减轻设备的重量,在此过程中,还需要确保航空工程进行的安全性。航空热处理的特点比较明显,其中质量控制的全面性是比较典型的特点之一。航空热处理的对象包括钢铁材料、金属合金以及各种高温合金等。
近年来,热处理技术发展很快,热处理技术的发展与物理冶金、新材料、新科学技术的发展密切联系,以物理冶金理论研究为先导,发展了等温淬火、分级淬火、亚温淬火,形变热处理、磁场热处理等新工艺。在钢铁材料广泛应用的基础上,发展应用于铝、镁、钛、铜等合金和精密合金,使热处理从Fe-C平衡范围走出来,发展了有色金属热处理。
陶瓷材料、复合材料等新型材料的发展又给热处理提出许多课题。热处理技术的发展充分利用了新的科学技,如在制氮技术发展基术础上发展了氦基可控气氛热处理;在真空技术基础上发展了真空热处理和离子化热处理;
在激光技术基础上发展了激光热处理及表面合金化;在计算机技术基础了发展了微机控制热处理技术等,其目的的是提高热处理质量和效率,节约能源,减少公害和污染,降低成本,提高经济技术效益。
更多关于材料方面、材料腐蚀控制、材料科普等等方面的国内外最新动态,我们网站会不断更新。希望大家一直关注中国腐蚀与防护网http://www.ecorr.org
责任编辑:王元
《中国腐蚀与防护网电子期刊》征订启事
投稿联系:编辑部
电话:010-62313558-806
邮箱:ecorr_org@163.com
中国腐蚀与防护网官方 QQ群:140808414
免责声明:本网站所转载的文字、图片与视频资料版权归原创作者所有,如果涉及侵权,请第一时间联系本网删除。
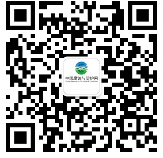
官方微信
《中国腐蚀与防护网电子期刊》征订启事
- 投稿联系:编辑部
- 电话:010-62316606-806
- 邮箱:fsfhzy666@163.com
- 中国腐蚀与防护网官方QQ群:140808414