X射线断层成像(X-Ray Computed Tomography)是一种影像诊断学的检查。这一技术曾被称为电脑轴切面断层影像(Computed Axial Tomography)。 X射线断层成像是一种利用数位几何处理後重建的三维放射线影像。
近几年来,断层摄影也到了微米的等级,而如今,国外将这一技术用到了金属3D打印产品的检测中。接下来,让我们一起去看看那些关于金属打印质量检测与监测的那些事儿,并领略国际上最前沿的检测技术是怎么样的。
3D打印制品在制备和使用过程中,某些缺陷的产生和扩展是无法避免的。根据3D打印材料中缺陷形成的不同特征,根据《无损检测》杂志,上海材料研究所助理工程师凌松归纳出3D打印中产生缺陷的主要原因有两方面:
① 材料特性导致的缺陷,它由材料特性导致的无法通过优化3D打印特征参数予以解决的缺陷,主要为气孔;
② 特征参量导致的缺陷,即在3D打印中,由于工艺参数或设备等原因导致的缺陷,可以称之为特征参量导致的缺陷,主要有孔洞、翘曲变形、球化、存在未熔颗粒等。
根据研究,在金属融化过程中,每个激光点创建了一个微型熔池,从粉末融化到冷却成为固体结构,光斑的大小以及功率带来的热量的大小决定了这个微型熔池的大小,从而影响着零件的微晶结构。
为了融化粉末,必须有充足的激光能量被转移到材料中,以熔化中心区的粉末,从而创建完全致密的部分,但同时热量的传导超出了激光光斑周长,影响到周围的粉末。当激光后的区域温度下降,由于热传导的作用,微型熔池周围出现软化但不液化的粉粒。
根据上海材料所凌松,无损检测的方法不仅仅局限于材料内部缺陷的检测与表征,还可实现材料的密度、弹性参数、孔隙率、残余应力分布以及其内部各种非连续性等方面的无损测试与表征;整个过程可实现快速、无损、原位的结果,对缩短材料的研发与生产周期和成本有积极意义。凌松对3D打印制品无损检测的展望如下:
(1)3D打印的原材料检测
3D打印的原材料为粉体或丝材,其形态与传统板材、棒材、锻件等有较大区别;因此,其理化特性的测试检验项目与传统减材加工技术的原材料有很大的不同,诸如力学性能、金相组织等项目无法进行。除化学成分分析外,粉体材料应着重关注其粒度、粒度分布、形貌及颗粒中的空隙等参量。
(2)3D打印制品的超声检测
例如在制备过程中使用超声检测来实时监控3D打印制品中残余应力的分布,防止其翘曲和开裂;在产品的研发阶段,使用超声检测结合数字计算机技术可以为制品提供其相应的密度、弹性参数、孔隙率,指导产品研发工艺的提高与升级,为制备出样品出更高质量的3D打印制品发挥出“灯塔”作用。
由于3D打印材料晶界组织的微小化,必须对超声检测的相关条件进行提高和拓展,超声检测走向高频化和定量化的趋势将更加明显。
(3)3D打印制品的射线检测
射线检测对于复杂构件的检测有着天然的优势,基于这一点上,射线在3D打印制品的检测上必将承担更加重要的角色,未来,配合高分辨率的工业CT和DR技术,射线检测在3D打印的发展中将发挥更大的作用。
在检测工艺上,需要充分结合样品的制造工艺,针对其特殊性构建出一套与之匹配的检测方法和体系。在使用和验收等级方面,需要考虑到其微观组织的特殊性,调整各个方面的验收参数。
(4)3D打印材料微区的无损评估
为了确保3D打印制品的可靠性,研究和制备过程中需要充分地分析3D打印制品的材料性能以及进一步了解材料微区的结构和性能、微区再结晶、Kirkendall空穴、成形过程内应力演化行为规律、内部组织形成规律、内部缺陷和损伤形成机理。因此,发展分辨率优于微米量级的微米、纳米尺度上的无损评估技术,进行材料微区的力学、电学、磁学和热学等特性的三维成像和评估,是声学和其它学科共同的任务。
(5)3D打印制品的早期损伤评估
3D打印制品的早期损伤评估也将是无损检测技术发展的一个方向,作为制造过程和状态预测的一部分,损伤评估技术直接影响到整个装备系统的安全运行。这就要求我们在现有的基础上开发出稳定性和灵敏度更高的仪器与设备,并实现远程评价。
对于上述凌松提到的第5条中的早期损伤评估,即金属打印过程中质量控制。无疑,最好的质量控制是过程中控制,但是对于打印结果的检测仍是必不可少的。而令人头疼的问题是,现今的无损探伤检测技术对于金属3D打印结果来说,并不是万能的,一个显著的问题是对于比较简单的产品设计,现在的NDE方法是没问题的,但是随着产品的复杂化,现在的NDE方法遇到了极大的挑战。
概括来说,当前NDE的局限性体现在
- 难以检测复杂设计
- 缺乏对关键缺陷类型和大小的定义
- 物理检测参考标准缺乏
- 缺乏书面检查程序
- 缺乏检测数据的概率统计
根据研究,对于金属增材制造的复杂性可以区分为五个层面:1 简单的零件、2 优化的零件、3 带有嵌入式设计的零件、4 为增材制造设计的零件、5 复杂的胞元结构零件。
在这方面,宾州大学将现今的检测方式针对这五个层面的检测有效程度做了分析。我们可以看到在第5个层级上只有X射线显微CT(X-ray Micro CT)是有效的检测手段。
为了达到对复杂零件的检测,宾州大学采取了计算机X射线断层成像(X-Ray Computed Tomography)检测技术,该技术不仅被用于打印零件的检测,还被用于后处理零件的检测。
这其中,GE也将计算机X射线断层成像技术用于其著名的喷油嘴的检测中,从图片上我们可以看到经过热等静压的后处理工艺,GE改进了产品的内部晶体结构,并提高了产品的抗疲劳性能。
通过实现对复杂零件的检测,当前的增材制造行业有望将过程中加工参数与模型结构以及零件机械性能建立有效的相关性分析,随着材料特征数据库的建立,以及对加工过程中几何形状特征与重要的工艺变量之间关系的理解,未来我们将有望建立增材制造领域的知识专家系统,从而将金属增材制造推向另一个高度。
免责声明:本网站所转载的文字、图片与视频资料版权归原创作者所有,如果涉及侵权,请第一时间联系本网删除。
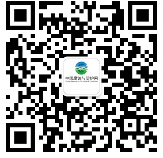
官方微信
《中国腐蚀与防护网电子期刊》征订启事
- 投稿联系:编辑部
- 电话:010-62316606-806
- 邮箱:fsfhzy666@163.com
- 中国腐蚀与防护网官方QQ群:140808414