特种耐火材料是以提纯高纯原料或以合成高纯原料为基础,以传统生产工艺和特殊生产工艺相结合的方法加工而成的耐火材料制品。是许多工业部门不可缺少的产品,特别是在很多新技术、新领域中,在关键的部位代替其他产品,大大的提高原有产品的使用寿命。
一、特种耐火材料的分类及特点
特种耐火材料的分类
根据原料及制品的性质不同,大致可将特种耐火材料分为五大类:
1、高熔点氧化物材料及其复合物
举例:氧化铝(Al2O3)、氧化镁(MgO)、氧化铍(BeO)、氧化锆(ZrO)、氧化钙(CaO)、熔融石英(SiO2)、氧化钍(ThO2)、氧化铀(UO2)、镁铝尖晶石(MgO·Al2O3)等。高熔点氧化物是和传统耐火材料“血缘”关系最近的特种耐火材料。
氧化铝坩埚
2、难熔化合物材料(碳化物,氮化物、硼化物、硅化物等)及其复合材料
举例:碳化硅(SiC)、碳化硼(B4C)、氮化硅(SiN)、氮化硼(BN)、氮化铝(AlN)、硼化锆(ZrB)、硼化镧(LaB6)、硅化钼(MOSi2)等。多数由人工合成。
碳化硼喷嘴
3、高熔点氧化物与难熔金属的复合材料(金属陶瓷)
举例:有碳化钨-钴系(WC-Co);氧化铝-铬系(Al2O3-Cr);
氧化铝-铁系(Al2O3-Fe);氧化镁-钼系(MgO-Mo);
碳化钛-钴系(TiC-Co)、碳化钛-镍系(TiC-Ni);碳化钛-镍钼合金系(TiC-Ni-Mo);
碳化铬-镍铬合金系(Cr3C2NiCr)等金属陶瓷。
4、高温不定形材料及无机物层
是一种喷涂或沉积在金属或其他结构材料表面用于抗高温氧化、腐蚀或阻热的陶瓷保护层或表面膜的总称。
5、高温纤维及其增强材料
举例:高熔点氧化物、难熔化合物特种耐火材料制成的纤维或晶须。如碳纤维、碳化硅和氮化硅纤维、晶须和氧化铝纤维及石墨晶须等。它们本质上属于陶瓷。
特种耐火材料的特点
1、更高的熔点。特种耐火材料的熔点大多数在2000℃以上,许多难熔化材料熔点甚至多达4000℃。
2、采用更纯的原料,因为天然矿物存在较多比例的杂质而不能满足特种耐火材料制备的要求,因此多采用提纯原料或者是人工合成原料。
3、原料多为微米级的粉体,甚至是纳米级的粉体,通常采用球磨法或化学制备的方法制备微米级或纳米级的粉体作为原料。
4、制备工艺多样化,可使用注浆法、可塑法成型,等静压、气相沉积、等离子溅射、喷涂、热压、电熔。
5、制品烧成条件更为苛刻。除成型温度要求更高外,在非氧化性烧结时,还需要在真空、惰性或其他特定气氛下进行烧结。
6、制品形状更加多样化。除普通简单形状、还有其他各种更加精致的特定要求产品。
7、性能多样化。除具备较高耐火性能以外,还具有电、热等功能特性。
二、特种耐火材料用途
特种耐火材料可应用在多种特定领域,在于它们所具有的优良的高温力学性能和后来被开发出的功能特性。下文将为大家列举部分应用产品及使用温度。
三、特种耐火材料的生产工艺
可分为原料准备→配料混练→素坯成型→干燥→素坯预烧→粗加工→烧成→烧结后处理→检验等工序,最终获得合格的成品。
原料准备
1、原料的选择
纯度要求:传统的的耐火材料广泛采用天然矿物为原料,而特种耐火材料多选择质量、成分稳定的高纯人工合成粉体为原料,绝大多数纯度在95%以上,特殊要求的在99%以上,更有甚者要求纯度在99.99%以上。
粒度要求:原料粉体的粒度将影响后续耐火材料的制备过程,一些特种耐火材料要求毫米级甚至是更大尺寸的颗粒,而更多的特种耐火材料需要的粒度为微米级,更有甚者需要纳米级粉体原料。
2、原料热处理
根据加热温度的不同,可以将特种耐火材料生产领域内对原料的热处理分为煅烧和电熔两种。
煅烧热处理过程中对原料的加热温度通常低于制品烧结温度。意在分解原料中有机物、除去易挥发组分及物理吸附,化学吸附水分,以提高原料纯度。
通过煅烧可以使原料粉体颗粒的晶粒长大,致密度提高,以控制制品收缩率。或者使其转变为更稳定的晶型。
3、粉碎
根据工艺要求,使用适当的球磨设备或粉碎设备制取原料粉体。原料的粒度分布将直接影响到成型后坯体的致密度,从而影响制品的耐热及强度等相关品质。
如果粉体有合适的粒度分布,就可以有效的提高坯体的密度。其他条件相同时,坯体致密度高时,在烧成过程中,需要排出的气孔体积就相对较少,烧成后制品的致密度就会因此得到提高。
4、合成
当通过热处理或粉碎等原料准备工序,依然无法获取某些特种耐火材料所需粒度或者纯度要求时,需要用合成的方式来获取原料。根据反应物状态的不同,其合成方法可分为固相法、液相法及气相法。
5、净化
在电熔化的粉碎以及粉碎操作过程中,极易引入铁屑等杂质,根据混入杂质的不同性质,可选用的净化方法包括水洗、酸洗、溶剂洗和磁洗。
6、配料混炼
经原料准备工序获得了纯度、粒度分布等均符合要求的粉体原料后,接下来就需要进行配料和混练。照既定的配方来称量原料,利用混练设备将称量好的原料及适量的各种添加剂混合均匀,得到可塑性良好的坯料,为随后的成型工序做好准备。
各类添加剂的添加原则是尽量不引入影响品质的杂质元素。
成 型
成型就是将混练得到的坯料加工成规定尺寸及形状坯体的操作过程。在特种耐火材料的工业生产中,使用得比较普遍且成熟的成型方法为模压法、注浆法、热压注法、等静压法、挤压法。
流延法、等离子喷涂法及化学气相沉积法则主要是用于特种耐火材料陶瓷材料功能特性成型和制备方面。
1、模压法
将混练后通过特殊造粒工艺获得的粒度合适、流动性好的粉体团聚体加入到金属模具中,在压力作用下进行成型。加压的方式有单向加压法和双向加压法。
模压成型的主要特点是工艺简便、周期短、工效高,宜于批量生产和实现机械化。坯体的密度高、尺寸精确。但由于加压方式所限,这种成型方法仅适合于圆柱、薄片状等简单形状制品的成型,不适合于复杂形状制品的成型。
2、注浆法
在原料粉体中加入适量的水或有机液体及电解质,通过混练制成具有良好的稳定性、流动性、脱模性且气泡含量少的料浆,然后将料浆注入石膏模中成型的方法,因此也被称为石膏模注浆法。
因混练浆料制备过程中需加入大量的水或有机溶剂,因此注浆法得到的坯体往往密度较低。烧成过程中,制品不容易达到较高的致密度,因而机械强度也较差。这种方法只适于生产一些形状复杂、不规则,对外观尺寸要求不严格、薄壁及大型厚胎的制品。
3、热压注法
热压注法成型法也被称为注射成型法。其原理与注浆成型法类似,但料浆的制备过程与注浆法有很大的区别。热压注法是将经过粉碎、热处理等原料准备工序处理好且充分干燥的原料粉体与熔化的石蜡混合均匀,然后再注入金属模具腔体中进行冷却、脱模得到坯体;然后经排蜡和烧成制成所需形状制品的方法。
4、挤压法
挤压法指可塑性坯料在挤泥机中,在压力作用下从挤出口中的具有一定形状的模具中挤出成型的方法。特种耐火材料原料多为瘠性物料,不具有可塑性,因此在挤压成型之前必须进行塑化。塑化是利用塑化剂使原本没有可塑性的物料转变为可塑性物料的过程。该法可实现连续化生产,生产效率高,特别适用于生产管状、棒状产品。
塑化剂由黏结剂和相应的溶剂组成。对于特殊要求的产品,可以采用坯料主要成分来做粘结剂。
例如:氧化钇稳定氧化锆制品生产中,可以先将以氧氯锆和醋酸盐为原料制备醋酸氧锆;将醋酸氧锆白色粉末和硝酸钇溶于甲醇中制成溶胶,并使得最后产物中Zr与Y比与原料中相同。将该溶胶在80℃进行适当的脱水后,就制成所需黏结剂。
5、轧膜法
轧膜法是先将粉料可塑化,然后通过粗轧和精轧,将坯料轧成一定厚度的膜片后,再通过冲片成型的方法。先粗压,再精压即可对膜片进行切割和冲片制成所需形状的坯体。
该法工艺简单,生产效率高,膜片厚度均匀,但干燥和烧成过程中收缩较大。适用于批量生产厚度在1mm以下的薄片状特种耐火材料制品。
6、流延法
将陶瓷原料粉体与一定比例的黏结剂、抗凝剂、除泡剂和溶剂混合形成料浆;以倾倒或浇注等方式将料浆铺展在平面基体上;随着溶剂的逐渐挥发,铺展开来的料浆慢慢固化,最终形成一定厚度的膜片,静置或烘干一段时间后,对膜片进行必要的切割、冲片或打孔后,即得到需要制备的制品的坯体。
流延法的每个步骤都有严格要求:使用原料需要经过细磨,浆料均匀性要高,料浆不允许有气泡,气泡可以通过过滤或消泡剂等方法消除。
7、等静压法
等静压成型亦称为静水压成型,它是将需要成型的粉料(有时需要与一定的黏结剂预先混合均匀)放入由塑料或橡胶制成的弹性模具中,再将模具放入装满刚性液体介质的高压容器中,然后对液体介质施加压力。
刚性液体介质具有的不可压缩性和均匀传递压力的特性,压力通过包裹在弹性模具周围液体介质均匀地传递至弹性模型,对填充于其中的坯料进行加压,最终获得一定形状的制品。坯体四周均匀受力,因此这种成型方法特别适合于制备其他成型方法无法制备的形状复杂的制品,所得制品收缩小,缺点是采用弹性模具尺寸精确度差。
在最初的等静压成型的基础上,又衍生出热等静压,干等静压等成型方法,其基本原理相似。
等静压原料粉举例-氧化铝造粒粉
8、热压法
热压法在模压法的基础上发展而来。原料粉体置于由石墨或氧化铝特种耐火材料制成的模具中,在通过电阻或感应加热方式,直接或间接对模具及其中的粉体原料加热的方式,进行加热的同时,施加压力,使坯料在成型的同时被烧结成瓷。
9、熔铸法
熔铸法是将原料在电弧炉中熔融后,把熔体直接浇注入铸模中,经冷却、退火及切割等工序制成所需形状制品的一种成型方法。
采用熔铸法生产特种耐火材料制品时,原料既可以采用粒径较细的粉体原料,也可以采用粒径稍粗的颗粒原料。用颗粒原料投料,可有效减少粉尘污染。此外,熔铸法在适当的退火条件下,可以制得性质优良的坯体,具有晶粒大、致密度高耐腐蚀的特点。
10、等离子喷涂
通过高频压缩电弧放电使流经电弧的气体分子部分电离,产生高温等离子体射流;然后用高温等离子体射流喷入其中的原料粉体熔融、喷吹到工件表面进行冷却、凝固、获得陶瓷涂层的方法。喷涂后无需额外的烧成工序,因此这种方法既是一种成型方法,同时也是一种特殊的陶瓷材料烧成方法。
由于等离子射流的温度可以达到上万度,足以将任何特种耐火材料粉体颗粒熔化,因此在理论上可以利用这种方法生产任何特种耐火材料材料的涂层。但利用该方法进行成型所需设备及运行成本昂贵。
11、化学气相沉积法
化学气相沉积法是一种典型的在材料基体表面制备薄膜的方法,是将含有构成薄膜元素的反应气体引入被加热至特定温度的反应室,通过在基体或衬底材料表面发生化学反应,并将反应生成的固体产物沉积在衬底表面生成薄膜的方法。
与等离子喷涂方法一样,沉积产物是陶瓷薄膜,因此既可以被看成是一种成型方法,也可以被看成是一种特殊的烧成方法。同时该法仅在材料表面生成薄膜,不改变基材性质,因此可以看做是一种材料表面改性方法。
通过化学气相反应沉积在衬底材料表面生成陶瓷薄膜的速度非常低,大约为0.25mm/h。然而与其他陶瓷制备技术相比,以这种方式形成的陶瓷薄膜往往具有更高致密度,因此其硬度和耐磨性也较高。另外陶瓷晶粒在衬底表面形成时,如果反应条件控制得当,可以使多数晶粒按某一垂直于衬底表面的晶轴优先生长,从而形成具有各向异性的结构陶瓷薄膜。
干燥与排塑
除热等静压、热压、熔铸、等离子喷涂和化学气相沉积这几种成型方法以外,其他成型方法均不能直接获得陶瓷制品,而仅能得到一个具有一定形状和致密度的坯体,通常称之为生坯。
其中,热压注法采用石蜡作塑化剂,因此生坯中不含有水分。剩余的其他几种成型方法,通常均采用水基黏结剂、塑化剂等有机添加剂。对这样的生坯通常不直接进行烧成,而需要先进行干燥与排塑。
1、干燥
干燥指借助热能使生坯中的水分汽化进入生坯周围流动的介质中被带走而使生坯含水量下降的过程。
生坯中水存在的方式分为三种,分别是:化学结合水、吸附水和机械结合水。化学结合水原料中的结晶水或结构水。吸附水是由于原料表面的不饱和键吸附了水分而产生。机械结合水为坯料原料间的缝隙水分,这种形式存在的水分与原料粉体的结合强度最低,是干燥过程的主要除去对象。除去水分后,坯体会形成一定量的气孔。
根据热量供给方式的不同,可将干燥的方式分成热空气干燥、电热干燥、辐射干燥和微波干燥等。
2、排塑
干燥后,成型时所加的黏结剂、塑化剂、消泡剂等有机添加剂仍然存在于生坯中。排塑就是将生坯加热到制品烧成温度之下的某个温度、保温,使生坯中的有机添加剂熔化、分解并挥发出坯体的处理过程。
在一些特种耐火材料制品生产过程中,为提高生产效率、降低成本,可将干燥和排塑合并进行。
烧 结
采用模压法、注浆法、挤压法、轧膜法、流延法及热压注法制备的生坯,经过干燥和排塑工序后,粉料颗粒间形成了一定的键合,晶粒也有了一些成长,因此也具备了一定的强度,但它的强度等性能指标还远远达不到我们对一件特种耐火材料制品的要求。需通过后序烧结来提高制品强度。
烧结是一个通过加热使素坯经过一系列物理化学变化成为致密制品的工艺过程;其次,烧结还可以指被加热至高温的素坯体中发生的晶粒长大和致密化这两个基本现象。
烧结后处理及品质控制
制品经过如上工序加工后,可制取一定形状及致密度的陶瓷制品。部分制品经检查合格后可以投入使用环节。另外一部分烧结后尺寸、表面光洁度及缺陷类型达不到用户要求的,需要进行后续的加工,其工艺包含:冷加工、上釉或导电化处理(金属化处理)及缺陷检验等。
免责声明:本网站所转载的文字、图片与视频资料版权归原创作者所有,如果涉及侵权,请第一时间联系本网删除。
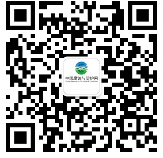
官方微信
《中国腐蚀与防护网电子期刊》征订启事
- 投稿联系:编辑部
- 电话:010-62316606-806
- 邮箱:fsfhzy666@163.com
- 中国腐蚀与防护网官方QQ群:140808414