摘要:
镁合金的比热容和相变潜热均比铝合金低,在压铸时冷却快、流动性差,容易产生欠铸、缺肉等缺陷。通过提高镁合金加热温度和模具温度,增加压射速度能大幅降低废品率。
近年来, 人们对产品轻量化的要求越来越高,尤其对汽车提出了进一步减轻重量,降低燃耗和排放,以及提高驾驶安全性和舒适性要求,而镁合金材料的使用正好迎合了这一发展趋势。镁合金性能的不断改善及压铸技术的显著进步,使得压铸镁合金的用量显著增长。
1.产品概况
汽车转向支架产品3D模型见图1,轮廓尺寸为92mm×94mm×61mm,产品平均壁厚
图1
4.5mm,材料为AZ91D,净质量为114g,是典型镁合金压铸件。该产品结构较为复杂,模具有上、下、左、右4个侧滑块。由于产品功能需要,零件许多部位原先圆角过小,不利于零件成形。
2.废品分析
根据统计数据,该产品废品率为23%。对259373件废品进一步分析发现,欠铸250378件,占96.53%;缺肉8995件,占3.47%。如图2所示,再现了在充型远端部位的欠铸问题。
图2
3.欠铸分析
压铸过程中出现欠铸主要有合金液流动性不良、浇注系统不合理、排气不畅三种情况。产品开发初期对模具浇注系统及排气系统利用CAE作过模拟并在调试阶段进行过优化,浇注系统及排气应该没有大的问题。零件材料为镁合金AZ91D,其比热容和相变潜热均比铝合金低,冷却快。分析认为合金液流动性不良是产品产生欠铸缺陷的主要原因。
下面对合金液流动性不良进一步详细分析。
(1)合金液氧化严重,流动性下降 由于浇注系统及溢流系统的存在,再加上不合格的产品,在连续的压铸生产过程中一般会产生50%以上的回炉料。由于镁合金材料熔炼时的防护性要求非常高,工厂无满足要求的熔化炉,不具备精炼条件,实际生产过程中回炉料被直接加入保温炉,操作者仅对合金液表面的浮渣进行简单清理。相比于精炼的成品合金锭,回炉料氧化严重,流动性差,是产品欠铸的主要原因之一。
(2)合金浇注温度及模具温度过低 温度是压铸过程中的重要工艺参数,为了满足良好的充型条件,保证压铸件的成形质量,必须选用恰当的合金浇注温度和模具温度。本产品采用冷室压铸机生产,要求合金温度在660~680℃,为了方便控制和测量,一般控制和保证炉内合金液的温度。为了保证浇注温度的稳定性,镁合金压铸专用保温炉为长方形,炉膛分为浇注腔和熔化腔,中间连通,合金锭从熔化腔加入后一般不会降低浇注腔内合金温度。保温炉设定温度为670℃,用便携式测温仪测量加料前后浇注腔内合金温度,数值如下:加料前663℃;加料0.5min后662℃;加料3min后648℃,加料后温度明显降低。
在镁合金压铸中,理想的加热方式是用模温机通过热油对模具进行加热,热油不间断地通过模具内的管道,从内部对模具进行加热,使模具达到需要的平衡温度。导热油的功能像热交换器,使模具温度保持在一定范围内。这种加热方式,模具的温度稳定而均匀,能有效地提高产品质量,延长模具寿命,而且使生产节拍稳定。镁合金压铸过程中模具的温度一般在1 8 0 ~ 2 8 0 ℃。转向支架的模温机设定在240℃,用红外测温仪测量连续生产时的模具温度,动模在190~200℃,静模在170~180℃,静模温度明显偏低。以上数据显示,合金液温度及模具温度偏低,压铸过程中容易产生欠铸、冷隔等缺陷。
(3)内浇道流速过低 因生产转向支架的压铸机系统本身未带有显示压射曲线功能,压铸机快压射速度通过流量阀控制,流量阀开启大小在压铸机上按比例显示,无法对应出相应的快压射速度,先用压射曲线测试仪测试出快压射流量与快压射速度对应关系,见表1。从表1可以看出,快压射流量由60%逐步提高到80%的过程中,快压射速度逐步提高,最高速度能达到6m/s。过去生产中,转向支架的快压射流量设定在60%,即压射速度在3m/s左右,此时内浇道合金液流速为72m/s,该速度能满足铝合金零件的压铸要求,但未能达到镁合金零件需要的高速度,这也是产品欠铸的主要原因之一。
4.对策及验证
(1)回炉料与成品合金锭分别作原料生产比较 因为镁元素化学特性较活泼,很容易被氧化,在无特殊除渣和精炼工艺的条件下,压铸中使用回炉料作原材料时镁合金液流动性比成品镁合金锭差。为了验证原材料流动性对镁合金转向支架欠铸缺陷的影响,在不同批次分别用回炉料(50%)与成品合金锭生产,其余工艺参数保持不变,统计欠铸废品率分别为:回炉料23.3%,成品合金锭19.1%。可以发现,采用成品合金锭作原料时,合金流动性比回炉料要好,欠铸比例明显下降。
(2)提高合金液温度 为验证合金液温度对镁合金支架废品率的影响,稳定合金液温度为690℃,其余工艺参数保持不变进行生产,原材料分别采用回炉料及合金锭各生产一批。统计欠铸废品率分别为:回炉料生产造成的废品率为16.3%;成品合金锭13.5%。对比先前合金液温度为660℃时统计的欠铸废品率不难发现,合金液温度升高,不管是采用回炉料还是成品合金锭,欠铸废品率都明显下降。其中采用成品合金锭生产批次的工件质量最好,废品率最低。
(3)提高模具温度 由于模具温度受合金液温度的影响很大,模温机分别设定为240℃、280℃,合金液温度分别设定为660℃、690℃,分四批次分别对模具实际温度进行现场监控,其结果见表2。
由表2可看出,合金液温度提高30℃后,模具温度也相应地提高了20℃左右,但是把模温机温度提高40℃后模具温度只提高了5℃左右。分析认为模具加热流道设计存在一定问题,提高模温机设定温度未能达到提高模具温度的目标。
(4)提高快压射速度为进
进一步验证快压射速度对废品率的影响,将快压射流量由原生产时的68%提高到78%,即快压射速度由3.6m/s提高到5.3m/s左右,采用不同的原材料,分别用不同的合金液温度进行生产,其余工艺参数保持不变,分8批次进行欠铸废品率统计,结果见表3。
表3显示,随着合金液温度提高,欠铸废品率降低,同时适当提高快压射速度也能大幅降低欠铸废品率。在提高合金液温度和快压射速度的条件下,可以克服回炉料流动性差的问题,采用成品合金锭生产对降低废品率有一定好处,但降低幅度不大。提高快压射速度后,由于内压增大,零件飞边较大,增加了后续清理难度,这可以适当降低增压压力及增压速度来解决。
5.结语
合金液温度和模具温度提高后,合金液流动性增加,充型能力大大提高,欠铸废品率明显降低。同时,适当提高快压射速度也能大幅降低欠铸废品率。采用成品合金锭生产能降低一定废品率,但降低幅度不大。改善压铸工艺条件后,解决了回炉料流动性差、废品率高的问题,废品率由过去的23.30%下降到现在的3.70%,给企业带来了可观的经济效益。
更多关于材料方面、材料腐蚀控制、材料科普等方面的国内外最新动态,我们网站会不断更新。希望大家一直关注中国腐蚀与防护网http://www.ecorr.org
责任编辑:庞雪洁
投稿联系:编辑部
电话:010-62313558-806
中国腐蚀与防护网官方 QQ群:140808414
免责声明:本网站所转载的文字、图片与视频资料版权归原创作者所有,如果涉及侵权,请第一时间联系本网删除。
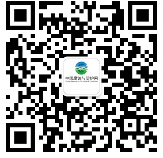
官方微信
《中国腐蚀与防护网电子期刊》征订启事
- 投稿联系:编辑部
- 电话:010-62316606-806
- 邮箱:fsfhzy666@163.com
- 中国腐蚀与防护网官方QQ群:140808414