磨削主要适用于外圆、内圆、平面以及各种成形表面(齿轮、螺纹、花键等)的精加工。它可以用于加工难加工热喷涂涂层,但比起磨削加工其他难加工的金属材料,其生产效率较低。一般磨削精度可达IT6~IT5级,表面粗糙度Ra值可达0.80~0.20。
一、影响砂轮切削性能的因素及其选用
磨削加工所用的刀具是砂轮,目前可用于磨削难加工热喷涂涂层的砂轮种类不多,只有绿色碳化硅、金刚石和立方碳化硼砂轮。
1.磨料
磨料在磨轮中担负切削的材料,它和车刀材料一样应具备高的硬度、高的耐磨性、足够的抗弯强度与冲击韧性、高的耐热性等。目前,用于高硬度热喷涂涂层磨削加工的磨料有绿色碳化硅、人造金刚石和立方碳化硼。大量的实验表明人造金刚石砂轮的性能远远优于绿色碳化硅与白刚玉砂轮。
表1是不同砂轮的磨削效率对比。
立方氮化硼砂轮,从许多实际加工的例子以及一些与人造金刚石砂轮的磨削对比情况说明,它有更高的磨削效率和更好的磨削性能。例如,用立方氮化硼砂轮磨削镍基喷熔层(粉102+50%WC)外圆,硬度HRC76~78。又如磨削镍基喷熔层(粉102+35%WC)外圆,硬度HRC65,不但磨削效率高。且加工质量亦优于金刚石砂轮。因此,立方氮化硼砂轮是磨削加工高硬度热喷涂涂层比较理想的砂轮。
表1 喷涂层的磨削效率(g/min)对比
2.粒度
粒度表示磨料颗粒的大小,一般用号数来表示。粒度主要依据表面粗糙度来选择,在保证一定表面粗糙度的条件下,尽可能选用小粒度号数的粒度即磨料颗粒尺寸较大,这样不但保证了加工表面质量,而且可以采用较大的切削用量,从而提高了生产效率。
(1)绿色碳化硅砂轮的粒度选用范围是:36#~80#。
(2)人造金刚石砂轮的粒度选用范围是:
表面粗糙度为Ra1.25~2.5,粒度为46#~60#;
表面粗糙度为Ra0.63~1.25,粒度为80#~100#;
表面粗糙度为Ra0.32~0.63,粒度为120#~150#;
表面粗糙度为Ra0.16~0.32,粒度为150#~240#。
(3)立方氮化硼砂轮的粒度选用范围是:
表面粗糙度为Ra0.32~1.25,粒度为80#一100#;
表面粗糙度为Ra0.16~0.63,粒度为100#~150#;
表面粗糙度为Ra0.32~0.08,粒度为150#~240#;
表面粗糙度为Ra0.16~0.02,粒度为280#~W40。
3.砂轮硬度
硬度是指磨粒受力后从砂轮脱落的难易程度。砂轮硬度影响砂轮的“自砺性”,这对于磨削热喷涂涂层是很重要的。砂轮硬度的一般选用原则是,被加工材料硬度越高,砂轮硬度的级别越软。这一原则也适合热喷涂涂层的磨削。
绿色碳化硅砂轮的硬度选用范围是ZR—R(中软一软)。软1(R1)、软3(R3)有较高的磨削效率。
人造金刚石砂轮的硬度级别有ZR、Z、ZY、Y,只有树脂结合剂的人造金刚石砂轮才有硬度级别。一般选用ZR与Z级。
4.浓度
浓度是金刚石与立方氮化硼砂轮的一个性能指标,它是指在砂轮的工作层内单位体积金刚石或立方氮化硼的含量。规定lcm3体积中金刚石或立方氮化硼含有4.4克拉(0.88g)的砂轮,称其浓度为100%。
浓度共分5种,见表2。
浓度的选用。粗磨时应选浓度高的砂轮,因单位面积上有较多的磨粒,切削能力较强。半精和精磨,一般选用中等浓度(75%左右)的砂轮。
表2 金刚石砂轮浓度
5.砂轮宽度
砂轮宽度对磨削的径向分力影响较大,径向分力Fy容易引起振动,这对于加工质量与砂轮的耐用度都是不利的。所以,在磨削难加工热喷涂涂层时,应尽量选用窄的砂轮(在砂轮强度允许的条件下),其宽度约为砂轮直径的10%左右为宜。
6.组织
砂轮的组织反映容纳切屑空间的大小,它可分为紧密、中等、疏松三类,号数为0~12。一般采用中等组织的砂轮。磨削难加工热喷涂涂层时,为了避免砂轮被“塞实”,特别在磨内圆时,可采用疏松组织(10~12号)的砂轮或采用大气孔砂轮。
二、 磨削用量的选择
图1 磨削运动
磨时的运动如图1所示,其磨削用量有:砂轮速度v、轴向进给量fa、工件速度vo、径向进给量fr。
1.砂轮速度v
试验表明,砂轮速度过低,砂轮的磨耗会增大,加工表面粗糙度变差。但砂轮的速度过高,砂轮的磨耗也会增大,对加工表面粗糙度的改善并不明显。因此,砂轮速度在一定的加工条件下,有一合理的数值。一般,绿色碳化硅砂轮速度v=20~25m/s;
人造金刚石砂轮速度v=15~25m/s;
立方氮化硼砂轮速度v=25~35m/s。
2.轴向进给量fa
轴向进给量增加,生产率随之增大,但砂轮的磨耗亦增大,加工表面粗糙度变差。一般内、外圆磨削fa=0.5~lm/min;平面磨削fa=10~15m/min。
3.工件速度vo
工件速度过高,容易产生振动。一般工件速度vo=10~20m/min。
4.径向进给量fr
径向进给量亦称磨削深度,它对磨削表面的尺寸精度、表面租糙度,砂轮耐用度以及磨削效率等影响较大。用绿色碳化硅砂轮磨削Ni04喷涂层内孔,当径向进给量等于0.006mm/双行程时,磨削效率、砂轮耐用度均已大大下降,并且产生明显的振动,表面粗糙度变差。所以,磨削难加工喷涂层内孔的径向进给量比磨削淬火钢要小得多。
径向进给量的选用原则是:当加工要求越高、工艺系统刚性越小、热喷涂涂层的硬度越高等,则径向进给量fr应越小。
一般,外圆磨fr=0.005~0.015mm/dst(mm/双行程)
内圆磨fr=0.002~0.01mm/dst
平面磨fr=0.005~0.02mm/d3t
磨削加工方法,在保证尺寸精度和表面粗糙度的高要求是好的,但存在的主要问题是生产率低。特别是磨削难加工热喷涂涂层,其径向进给量是很小的,若要完成一定厚度余量的磨削,其生产率自然是不能令人满意的。
另外,热喷涂层内孔的磨削要比磨外圆困难,但内孔表面用等离子喷涂修复更具有特殊意义。因为内孔表面多是薄壁盘类零件上的一部分,采用等离子喷涂修复,除了获得高耐磨性的表面外,不致引起整个零件的热变形,这是用传统堆焊修复方法所做不到的。因而,它对扩大零件的修复范围是很重要的,根据对某一工程机械要修复的零件表面进行统计,内孔表面占70%左右。内孔磨削加工的问题显得突出。
因此,提高磨削热喷涂涂层的生产率,特别是提高磨削喷涂层内孔的生产率是一个需要解决的重要问题。
更多关于材料方面、材料腐蚀控制、材料科普等方面的国内外最新动态,我们网站会不断更新。希望大家一直关注中国腐蚀与防护网http://www.ecorr.org
责任编辑:庞雪洁
投稿联系:编辑部
电话:010-62313558-806
中国腐蚀与防护网官方 QQ群:140808414
免责声明:本网站所转载的文字、图片与视频资料版权归原创作者所有,如果涉及侵权,请第一时间联系本网删除。
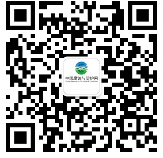
官方微信
《中国腐蚀与防护网电子期刊》征订启事
- 投稿联系:编辑部
- 电话:010-62316606-806
- 邮箱:fsfhzy666@163.com
- 中国腐蚀与防护网官方QQ群:140808414