20世纪80年代汽车防腐蚀技术在国内并未得到足够的重视。随着汽车市场的不断扩大,汽车竞争日益激烈,用户对车身的涂装要求越来越高。为此,生产厂家对车身的防锈、涂料的褪色、调色、光泽度等非常重视,并给予特别的关注。应用创新的防腐蚀技术,不仅可提高汽车的外观质量,更重要的是还可提高汽车的内在质量,延长汽车的使用寿命,提高汽车档次,甚至可成为带动产品销售的一个增长点。
1金属腐蚀及危害
汽车零部件制造所用的材料以金属为主,使用中金属材料的腐蚀是难以避免的。金属零部件在腐蚀性气体或液体环境中,其在表面发生化学腐蚀或电化学腐蚀,生成腐蚀层,摩擦就会使其剥落而导致零件损坏,此现象即为腐蚀磨损。
汽车发动机的磨损程度,除燃料中硫含量外,主要取决于汽缸的冷却程度。发动机温度越低,酸性物质越易在缸壁生成,腐蚀作用强烈;当温度升高时,这些酸性物质呈蒸气状态随废气排出,腐蚀要小得多;但温度过高时,润滑油黏度变低,油膜不易形成,抵抗腐蚀的作用减小,使磨损加剧。
车辆金属零件的腐蚀,不仅会降低其品质和寿命,而且因其腐蚀异常损坏的零件极易引发交通事故,甚至造成车毁人亡的惨剧。随着车辆使用年限或行使里程的增长,各部位机件的腐蚀逐渐加剧,常见腐蚀比较严重的部位是板金件部分,如驾驶室、车大箱、客车壳体、车底板、挡泥板、车头(翼子板、面罩)等。这些部位常与泥沙、碎石和水接触,如车轮飞溅碎石、泥沙撞击汽车表面的防护层,极易划伤漆层,破坏其完整性、连续性,使金属裸露在外,当接触到水和空气中的氧,就会起化学作用而产生锈蚀。
2影响车辆腐蚀的主要因素
引起车辆腐蚀的主要因素有使用环境因素和其自身结构因素。汽车使用环境比较恶劣且多变,造成汽车零部件腐蚀损坏。①湿气的影响:在车身下部积存的泥沙、污垢和水分会加速腐蚀。②湿度的影响:在相对湿度高的地区(如沿海地区),腐蚀将加速,而在气温持续冰点以上,有大气污染的地区腐蚀更为严重。③温度的影响:温度升高,处于通风不良处的零件会加速腐蚀。
含有湿气的污垢或碎屑物积留在车身板部分、空间或其他部位;汽车内部产生的腐蚀环境如发动机产生的高温和含硫、氯离子等的燃烧废气,蓄电池产生的酸雾、漏液;工作中振动、冲击产生的应力,摩擦、碰撞引起的局部破损等也是引起汽车零部件腐蚀损坏的主要原因。
3金属腐蚀的机理
金属腐蚀变化过程通常是从表面开始的,然后逐步向内层侵蚀,最终造成难以挽救的损失。其表现先是外表失去光泽,使光滑表面变得粗糙不平,并盖满一层金属氧化物,也就是金属腐蚀产物。如铁由于腐蚀而盖满一层褐色锈,就是由铁的氧化物构成的铁锈。金属腐蚀的主要机理是原金属转化成金属氧化物,造成结构件或元件生锈、损坏甚至不能修复而报废。而油漆、橡胶、玻璃钢纤维等非金属材料的老化,主要是受环境综合作用后,材料的高分子结构发生裂解、降解、溶解等物理和化学变化,导致外观和性能下降。当金属零件摩擦表面之间存在着氧和酸性物质时,就会出现化学腐蚀,使表面局部腐蚀,并不断地扩大延伸,导致颗粒状剥落,使零件表面形状变化造成早期磨损。可见汽车本身的设计结构、应用的材料、工艺及防护措施直接决定其耐蚀能力。
电化学腐蚀是当不同电位金属相接触,由于电位差的不同而出现电流,这时失去正电荷离子的金属被锈蚀,在锈蚀中伴有电流的产生。
4汽车耐蚀性及防腐技术的应用状况
国内汽车的防护设计、防腐技术的应用和工艺水平相对偏低。一些国产汽车油漆层的丰满度、平整度和光泽度及附着力偏低&镀层、转化膜的质量欠佳,尤其是重腐蚀环境(酸雾、高温等)中零件的耐蚀能力差。直接表现在使用一段时间后出现锈渍,油漆层起泡、剥落、变色、失光,油箱清洁度降低,非金属件变形等。与国外或国内合资企业制造的品牌汽车相比,国产汽车的造型、使用的材料及工艺直接影响了产品的档次。目前占据国内汽车市场较大份额、且技术上国内领先的是东风、解放等品牌汽车,其外观质量近几年有明显提高,所采取的防腐技术和应用现状具有一定的代表性。由此可见,提高汽车的防腐性能需从结构设计、制造工艺的各个环节采取综合措施才能取得最好的效果。
4.1从汽车结构设计上避免腐蚀
在汽车整体布置上考虑要防止腐蚀介质的积聚,尽量避免封闭区域,或保持封闭系统通风和排水良好,如考虑整车的通风、散热;发动机产生的尾气排放或通过净化、降温等;在外形设计上注意防护、避免积存水汽和尘土。国外先进汽车非常注重造型设计,如一些品牌汽车,造型流畅,既体现美感和功能设计,又不易积水和积垢,十分值得借鉴。注意外露件的保护,电器件与接头布置在内侧,或加防护罩壳。整车外露易腐蚀和易进水的部位设防尘罩。零部件设计时考虑其均匀腐蚀,选择一种或几种组合防腐方式。汽车常用的防护方式有涂层、电镀、转化膜和涂防锈油脂等。不同的工艺,具有不同的耐腐蚀性能。通过完善表面处理要求,提高零件设计的合理性,以及有效规范表面处理工艺,促进了产品外观质量和耐蚀性的提高。
4.2明确油漆涂层的特性和质量指标
如车身结构件涂层强调装饰性和耐蚀性;前后桥等的涂层强调保护性;蓄电池箱的涂层强调耐酸性;排气管等的涂层强调耐热性等。注意避免缝隙腐蚀、电化学腐蚀、应力腐蚀开裂。对不可避免的缝隙结构如发动机罩拼焊缝隙用密封胶封闭。不同金属连接时应尽量选取电位接近的金属,或采取绝缘措施避免电化学腐蚀。零件的结构要便于防护工艺的实施,必要时开设工艺孔。例如,油箱上开孔的位置要有利于喷枪嘴覆盖全部表面进行喷丸处理。对化学前处理的工件要开设工艺孔,防止积液。考虑选用性能优良的耐腐蚀材料,如镀锌板、彩卷板、复合材料和工程塑料等。玻璃钢具有工艺性好、强度高、成本低的特点,配合隔热垫可以起到一定的隔热和降低噪声的效果,已广泛应用于汽车发动机罩、蓄电池箱盖和普通护罩等。目前应用的玻璃钢零件普遍是以不饱和聚酯树脂和无碱玻璃纤维为主要原材料,配合钢板加强筋叠压制作而成,可获得良好的外观质量,无焊接造成的焊棱和油漆难以掩饰的点焊疤痕,但耐久性差,易老化,适合试制小批量产品。对批量大的罩壳类定型零件,选用工程塑料(ABS工程塑料)取代玻璃钢,可获得更好的装饰性和耐久性。发动机罩受环境影响较大,采用薄钢板或镀锌板配合涂层防护更为合理,汽车将更多地应用新型材料。
4.3应用投入少、见效快的防腐新工艺和新材料
改进涂装生产工艺,提高汽车外观质量和耐蚀性。常见国产汽车的涂装采用可低温烘干的自干型油漆,目前所用面漆正由低固体分溶剂型向高固体分溶剂型及粉末涂料过渡,由丙烯酸工程磁漆过渡到装饰性强、耐蚀性好的聚氨酯或丙烯酸聚氨酯磁漆;底漆和中间层良莠不齐,有些仍在使用醇酸底漆和过氯乙烯铁红底漆及过氯乙烯腻子、二道漆等,而有些已在使用耐蚀性较好的磷化底漆及铁红环氧酯底漆、不饱和聚酯腻子(原子灰)。因大批量生产的需要,汽车涂装已由地摊式改为流水线生产,将装配、调试后再整车涂面漆的生产工序改为分部涂装,即零部件完成涂装后再装配、调试、精整入库,用进口的空气辅助式喷枪或高压无气喷枪取代普通的空气喷枪进行喷涂,提高油漆材料的利用率和涂装效率,将漆膜自然干燥改为烘干,提高涂膜的附着力和硬度,加快了生产速度。既满足大批量生产的需要,又避免了整机涂装所造成的车身内污染、漆膜不全、附着力和硬度低等弊病。
4.4改进前处理工艺
国内汽车零件的前处理主要是喷丸处理和化学前处理。目前喷丸处理主要应用于厚板结构件和铸件,以除锈、除氧化皮为主要目的,材质的表面并没有形成保护膜,零件的耐蚀性取决于表面涂层。化学前处理主要应用干氧化皮较少的薄板结构件‘如发动机罩、仪表架等。目前主要应用的较成熟的中温磷化技术是“脱脂除油→除锈→水洗→中温磷化→水洗→中温钝化→烘干→涂装”。经磷化和钝化后处理的零件,表面形成的磷化膜在大气中有较好的耐蚀性,能有效提高涂层的附着力。
5汽车制造中的金属机件防腐措施
5.1金属表面处理和表面除油
金属分为黑色金属和有色金属两大类。由于材料种类不同故表面处理方法也有一定差别,金属表面处理可分为:除锈、除油、磷化、纯化等几种。汽车零部件在制造加工、保管和使用中,常常接触到各种润滑油而形成油污或因保管不当而锈蚀。在车身涂装前,须经过除油、除锈等表面处理。最常用的方法有溶剂除油法、碱液清洗法和表面除锈法。
5.2使用防腐装饰涂料
现实生活中有70%以上的钢铁制品暴露在易于腐蚀的环境中,如桥梁、交通工具、各种机械设备等,长期受到风吹雨淋,酸、碱、盐和微生物的腐蚀,使设备的机械性能下降、使用价值降低,甚至造成提前报废。防腐涂料涂膜有很强的附着力,起着隔离水分、烟雾以及外来腐蚀物质侵蚀的作用,使被涂物体表面受到保护。因此防腐涂料作为金属防腐最广泛的应用方法。
底漆的作用是防止金属表面的氧化腐蚀、增强金属表面与腻子、腻子与面漆之间的附着力。由于附着力和耐腐蚀性能主要依靠底漆层,因此车用底漆具备的特性有:①对经过表面处理的车身表面有良好的附着力;②所形成的漆膜应具极好的机械强度(耐冲击强度、硬度、弹性);③漆膜必须具有极好的耐腐蚀性、耐水性和抗化学腐蚀性;④必须有合理的配套作用;⑤有良好的施工性能,能适应先进的汽车涂装工艺。底漆的附着力和漆膜的强度除了与成膜物质有关,还与涂膜的厚度、均匀度、干燥程度、稀释剂的正确使用及施工环境、表面清洁处理(如除锈、去油)等有关。常用底漆有:国产客车钢铁表面用F06-1铁红酚醛底漆,铝及铝合金等轻金属用F06-1锌黄酚醛底漆;中高级或进口轿车可用进口防护底漆。具体可根据制造商提供的产品说明书选用。施工以喷涂为主,要求喷涂均匀、无漏涂、无流痕。
沥青是一种热塑材料,是历史悠久的涂料品种。由于其具有材料来源丰富、价格低廉、施工方便的特点,得到了广泛应用。主要品种有纯沥青漆、加油沥青涂料、加树脂沥青涂料。其主要特点:优异的耐水性,良好的耐化学性能和绝缘耐热性,是一种很好的防腐装饰涂料。常用于化工、机械、船舶、地下管道、轻工制品、小五金等。
5.3纳米涂料
汽车涂层除要求高装饰性外,还要求有优良的耐久性,包括抵抗大气紫外线、水分、化学物质及酸雨的侵蚀和抗石击性能。在影响汽车使用寿命的各项性能中,最为重要的莫过于耐候性了。汽车外部零件如保险杠、挡泥板以及车门的镶边等所选择的涂料其耐候性是最突出的要求,另外也要求能够有较好的耐介质性和耐磨性。因此汽车上那些经常受到外界因素摩擦、冲击的部位,最好采用具有防护作用的涂料。纳米材料的特性为其广泛的应用奠定了基础,开发纳米材料的应用领域正是纳米科学研究的主要方向。利用纳米材料特殊的抗紫外线、抗老化、高强度和韧性、良好的静电屏蔽效应、色泽变换效应及抗菌消臭功能等,开发和制备性能优异的新型汽车涂料,具有广阔的应用和发展前景。
利用纳米粉体材料较强的紫外光反射特性,将纳米粉体按一定比例加入到涂料中,可以有效地遮蔽紫外线,免受紫外光损害。
利用纳米SiO2、MgO等的透明性和对紫外光的吸收特性,在制备某些防护材料或产品时添加少量(一般不超过总量的2%)这样的纳米材料,就大大减弱紫外线对这些防护材料或产品的损伤作用,使之更具有耐久性和透明性。这种涂料可以用于汽车有机玻璃的涂层材料,防止有机玻璃老化、透明度下降。用纳米TiO2或SiO2改性的塑料膜,贴在汽车玻璃上具有保温效果,可以降低空调的能耗。汽车车体最贴近地面的部分,往往受到各种溅石、瓦砾的冲击,这就需要性能良好的抗石击涂料。在汽车窗导槽等经常摩擦磨损部位,应该用具有低摩擦系数的涂料,从而减少对汽车的伤损。在涂料中添加纳米Al2O3、纳米SiO2等可提高涂层的表面强度和耐磨性。由于静电的作用会引起诸多麻烦,因此汽车内饰件涂料及塑料部件用防静电涂料的开发和应用日益广泛。美国用纳米材料可作为静电屏蔽涂层,日本利用纳米氧化物制成多颜色的静电屏蔽涂料,还研发了汽车塑料部件用无裂纹抗静电透明涂料。
6汽车车身表面防护处理措施
(1)采用镀锌钢板。为了防止钢板件锈蚀,所有的外部冲压件都是采用镀锌钢板,镀锌层厚度10?m。镀锌钢板置于自然环境下,每年镀锌层自然减薄2?m,基本可以维持车身寿命5年。
(2)磷酸处理。磷酸处理亦称涂装前的预处理。在对车身钢板进行脱脂清洗之后,应给车身涂上一层磷酸锌,涂了这层磷酸锌(很薄的一层,仅3?m)既能起到第一次保护的作用,也有利于下一道涂料的黏附。
(3)阴极电泳处理。阴极电泳处理亦称为上底漆,电泳涂层较厚(30~50?m)该涂料为水溶性涂料,实施过程中应采用电解方式对所有暴露在外的钢板表面和车身底部进行处理。也即是将车身的一头接正极,并浸泡在电解槽内进行电解沉积处理。电泳底漆的主要步骤为-入槽浸泡(至少2min);F溶液(亦称超滤液)冲洗4道,其中浸泡清洗一次,目的是使夹缝、封闭梁内部清洗干净;用去离子水冲洗2道;烘干[(180±5)℃]。烘干过程中也可使车身焊装时采用的点焊密封胶固化。
(4)密封——涂抗石击涂料。这道工序的操作必须仔细、耐心和认真,其主要目的是防止水、灰尘、气味进入车厢内,车厢底部的涂料能保证车厢底部不锈蚀和不致被碎石块撞坏,这种涂料弹性好,可以吸收和缓冲碎石的撞击能量,涂料以喷涂方式覆盖于轮罩内部、底板外表面,车身侧面下裙部。在所有外部可见的钢板搭接处用喷涂或挤涂的方式涂密封胶6,必要时用刷子对缝隙进行密封,此外对发动机罩盖和骨架间采用这种胶,按工艺要求进行逐点填充式挤涂。
(5)中涂。中涂油漆覆盖于车身所有外表面。涂层较厚,一般为40?m,在迎风面还要厚一些,中涂油漆物理性能与底漆、面漆不同,它的弹性较强,底漆与面漆则比较脆硬。中涂层油漆的功能主要是吸收灰、砂等对面漆的冲击力;加强底漆与面漆之间的附着力;使面漆丰满,起填补的效果。中涂后需进行烘干,烘烤温度为(140±5)℃,中涂后的烘烤也同时使抗石击涂料和密封胶得以固化。
(6)面漆。面漆物理化学性能稳定,除了使汽车外观更美观漂亮以外,同时也能承受自然环境对汽车的侵蚀,如潮湿、氧化、雨水、含盐物质、含酸物质、阳光辐射、砂石撞击等。
(7)存放防护涂层。对于长期(3个月以上)露天存放的车身其外表面应喷涂一层水溶性防护蜡。该防护蜡加有紫外线吸收剂,使用前用皂类洗涤剂和清水冲洗掉防护蜡使油漆重现光彩。
7汽车应用中金属机件的防腐措施
(1)应用防锈剂对车身进行处理。购到新车后要尽快防锈)一旦铁锈已经开始产生,过了微细粉末状阶段,再防锈就费事了+,在易附着水分及泥土较多的地方,密封或半密封的部位,如面板底部、底板下面、车门内侧、护板衬垫内、挡泥板的接合部、灯类装设处等容易生锈的地方,喷涂一层含蜡的自行封闭的防锈剂。,专业的防锈工作,包括在正确的位置钻孔,通过所钻的孔喷漆防锈。孔的具体位置在不同车型上是不尽相同的,应根据具体车型的详细说明进行。喷漆后要用橡胶或塑料塞子,将钻的孔塞住。
(2)平时及时作好除锈工作,在换季维护时,做有计划的防锈处理。
(3)经常刷洗汽车,定期打蜡,以保护喷漆层并保持涂膜光亮。
(4)经常用水管对车身进行冲洗,冲洗车身底板下面、翼子板下面和易于生锈的其他部位,同时要清洗掉车门槛上的污垢。不要使用较高水压的水喷洗,以防淋到车身各处,特别是车窗、发动机罩盖及行李箱盖接合之处引起锈蚀。
(5)如果车门底部和后挡板有排水孔,应保持其畅通,以避免积水并引起腐蚀。
(6)雨天和行驶泥泞道路后,要及时擦拭车辆,除去泥污。清洗时,应尽量少用地下水,洗后用干布擦拭。
(7)喷漆的部件如果缺漆,应及时补漆和打蜡7没有喷漆的部件,应经常检查,发现缺油,及时维护。车辆在二级维护时,应分解除锈、以免锈死。
(8)汽车封存防腐,选择和改善停放环境,注意通风、除尘、保温等。经常检查车辆是否有较小的损伤,如有损伤应及时进行修理。金属部件表面尽可能做保护处理,如采用电镀、喷镀等金属覆盖层,法兰和磷化(即金属件表面形成一层氧化膜),非金属覆盖层(如油漆、橡胶沥青等),暂时覆盖层(如涂抹润滑油脂等)。
8汽车应用防腐技术的发展方向
8.1应用阴极电泳底漆
在目前的各种油漆施工工艺中,阴极电泳底漆防腐能力最强,这一点在瑞典腐蚀研究所所做的调查中得到证明。阴极电泳涂装生产可实现全自动化,施工安全、效率高,以水为溶剂,可做到无排放和几乎无污染;漆膜均匀并具有优良的抗蚀性,在磷化处理后电泳,耐盐雾能力强;漆膜结合力与韧性及硬度指标皆具有优势,此项防腐技术已经在汽车产品上得到广泛应用并日益成熟。国产汽车上应用只需对现有工艺进行完善。“基材前处理(包括磷化)→清洗→去离子水洗→阴极电泳底漆→去离子水洗→清洗→固化→面漆涂装”,在现有的磷化前处理生产线上增设电泳涂装设备就能实现。阴极电泳漆目前较多采用丙烯酸树脂、环氧树脂和聚氨酯等,与汽车所用面漆(丙烯酸或聚氨酯磁漆)具有良好的配套性。
阴极电泳涂装工艺经30年的不断完善,现已成为汽车涂装中最成熟的涂底漆(或底面合一涂层)的先进技术之一。
8.2水性涂料的静电涂装工艺
汽车涂装中的VOC排放量要达到环保法规的要求,主攻方向是中涂和面漆,因底漆几乎实现了水性化。据资料介绍,中涂层涂料的VOC释放比率约占汽车涂料VOC总排放量的25%,汽车面漆的VOC释放比率约占60%(其中金属闪光底色漆占40%,罩光清漆占20%)。为适应环保的要求,进入20世纪90年代以来,欧美等国汽车车身涂装线都采用水性中涂和水性底色漆,日本也都采用水性中涂、面漆。我国现今采用的汽车中涂面漆仍是传统的有机溶剂型涂料。为保护环境,汽车中涂和面漆实现高固体分化、水性化和粉末涂装无害化是势在必行的。高固体分涂料还可采用常规的涂装方法及设备进行涂装。可是水性涂料和粉末涂料无法采用常规的涂装方法及设备进行涂装。采用水性涂料可望大大减少中涂和面漆的VOC,但因水性涂料本身是导电的,因此要求开发一种在涂装线上使用水性中涂和面漆的静电喷涂生产技术,并仍能保持常规高速杯式自动静电喷涂的质量和涂着效率。
8.3应用达克罗技术
达克罗即片状锌基铬酸盐防护涂层,亦称锌铬膜,是当今国际表面处理的高新技术。经达克罗处理的金属制品性能优异,耐蚀性强,一般涂层厚6~8?m就可保证在盐雾试验中480~1000h不出红锈,是电镀锌5~7倍。高耐热性(可耐热至300℃),表面涂膜即使长时间置于高温条件下也不会被腐蚀,而电镀锌法(有色铬酸盐处理),在100℃左右,表面的铬酸盐涂膜就开始变化,抗腐蚀性急剧下降;无氢脆性,适用于高强度受力件。在汽车及配件上开始大量使用,并获得了极高的评价。随着国内达克罗技术的发展,生产成本的降低,国产汽车亦有可能对重蚀环境(高温、高腐蚀性环境)中的零件应用锌铬膜防护。
9结语
汽车表面需要涂料的保护和装饰,涂层质量是对汽车质量的直观评价,它将直接影响汽车的市场竞争力。对于现代汽车尤其是轿车,人们不仅追求线条流畅的外形,而且对汽车的外观质量、汽车的装饰和使用寿命也提出很高的要求。这尤其表现在要求汽车满足人们在视觉、嗅觉和听觉等方面的追求。汽车业的发展变化对涂料提出高品质、低消耗和环保技术等要求。这些都对现代汽车涂层材料和工艺提出挑战。提高汽车的耐蚀性和外观质量,着重是提高设计的合理性及应用先进的防腐工艺和材料。
更多关于材料方面、材料腐蚀控制、材料科普等方面的国内外最新动态,我们网站会不断更新。希望大家一直关注中国腐蚀与防护网http://www.ecorr.org
责任编辑:王元
投稿联系:编辑部
电话:010-62313558-806
中国腐蚀与防护网官方 QQ群:140808414
免责声明:本网站所转载的文字、图片与视频资料版权归原创作者所有,如果涉及侵权,请第一时间联系本网删除。
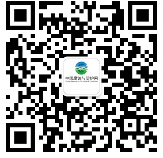
官方微信
《中国腐蚀与防护网电子期刊》征订启事
- 投稿联系:编辑部
- 电话:010-62316606-806
- 邮箱:fsfhzy666@163.com
- 中国腐蚀与防护网官方QQ群:140808414