船舶设计的不断进步对舰船材料提出了更高要求
随着船舶设计从静强度设计到动强度设计、寿命设计、损伤容限设计的不断进步,加之轻量化发展的要求,对舰船材料的强度提出了越来越高的要求。此外,恶劣的海洋服役环境,极大增加了材料应力腐蚀开裂的风险。
应力腐蚀
简介:
由拉伸应力和腐蚀介质协同作用导致材料或构件过早开裂的现象。
扩展速率:
一般为10-9~10-6m·s-1,比一般均匀腐蚀的速率要快106倍。
特点:
引发构件失效的主要原因之一,且无明显征兆,往往给工程带来灾难性损失。
现有应力腐蚀评价标准
国际公认标准是BS EN ISO 7539 Corrosion of Metals and Alloys-Stress Corrosion Testing合订本,我国GB/T 15970《金属和合金的腐蚀-应力腐蚀试验》等同采用ISO标准。
标准中给出了多种应力腐蚀评价方法,归纳起来:有3种试样类型,即光滑试样、带缺口试样和预制裂纹试样;加载形式也有3种,即恒位移、恒载荷和慢应变速率。
评价方法和试验参数的选择问题多多
试样类型和加载形式的不同组合就产生了各种应力腐蚀评价方法,各种评价方法均有其侧重点和应用范围,对同一种材料,采用不同的评价方法有时结果并不完全相同,甚至会得到相反的结果,这就给工程设计、使用、选材带来一定困难。
另外,评定的目的是在较短时间内获取材料的性能数据。因此,试验通常会在较高应力、持续应变、预制裂纹、高浓度腐蚀介质、升高温度等条件下进行加速试验。那么,如何科学、合理地选择评价方法和试验参数,就是一个值得思考的问题。
恒位移法
简介:
恒位移法又称恒总应变法,首先通过拉伸或弯曲使试样产生变形,然后借助具有足够刚性的框架或螺栓以维持这种变形,即在整个试验过程中试样变形的总位移量是恒定的。其中,试样的变形包括弹性变形和塑性变形两种。
应用领域:
这种加载方式往往用于模拟工程构件中的加工制造应力状态,属于应力腐蚀最常用的一种评价手段。
优点:
装置简单且易于实现,可在不同高压环境下进行试验,亦可对多个试样同时进行试验。
试样形式:
通常有光滑试样和预制裂纹试样两种。
光滑试样
1评价方法
主要包括各种弯曲(2点、3点和4点)试样、U型、C型环等。
2评价指标
试验结果评价指标为指定暴露周期[通常为30d(天)]内是否发生应力腐蚀开裂,属于通过/失败判断方法。
3应用领域
① U型试样:由于其苛刻的力学条件,常用于应力腐蚀敏感性排序和筛选。此外,也可用于评价材料在服役环境下的适用性,是恒位移法光滑试样中使用较多的一种评价方法。
② 弯曲试样:通常用于石油化工行业的管线钢产品,尤其适合评价焊接产品。
③ C型环试样:对于管件产品,可能会在服役环境中发生沿长度方向的裂纹萌生或扩展时,尤其在环向应力条件下存在长度方向焊缝时,C型环试样就非常合适了。
4优点
试验简单、操作方便、费用较低。
5缺点
① 应力状态不明确,仅能定性反映材料的应力腐蚀敏感性,而不能反映裂纹扩展速率;② 试验数据分散性较大,数据分析比较困难;③ 应力松弛,试验过程中一旦裂纹萌生,试样加载时所储存的弹性应变能会部分或全部转变为塑性变形得以释放,导致已有裂纹扩展缓慢或者停止,对试验结果有显着影响。
缺口和预制裂纹试样
为了避免光滑试样裂纹萌生多源性、随机性的问题,开发了缺口和预制裂纹试样。预制裂纹试样是在人工缺口试样的基础上,经疲劳处理使其产生裂纹。典型的有改进后的楔型张开加载(WOL)和双悬臂梁(DCB)两种试样。
1应用领域
缺口试样:主要用于模拟材料宏观裂纹以及各种机加工缺口对SCC的敏感性;预制裂纹试样:与缺口试样相比,预制裂纹试样的裂纹前沿更加尖锐,可用于断裂力学中临界应力腐蚀门槛值KISCC和裂纹扩展速率da/dt等动力学参数研究,在工程设计、安全评估和寿命预测等方面都有极为重要的应用。
2优点
① 试验周期短、数据稳定性好,便于结果比较和分析;② 缺口和预制裂纹能真实反映实际工程构件的损伤状态,试验结果与实际情况较为吻合;③ 可以定量研究应力腐蚀门槛值KISCC以及裂纹扩展速率da/dt等动力学参数。
3局限性
① 该试验基于线弹性断裂力学理论,要求试样处于平面应变状态,即满足小范围屈服的条件,对于大多数中低强度金属材料而言,无法在现有设备能力范围内满足试样尺寸要求。
② 试验过程中,裂纹容易分叉,且会因蠕变而使得裂纹尖端应力场强度下降,所测得的KISCC明显偏高,导致对材料性能的过高评估。
恒载荷法
简介:
恒载荷法是试验过程中试样加载载荷保持不变的一种评价方法与光滑试样相同,亦属于通过/失败类评价方法,可用于材料的合格性验收。将试样的一端固定,另一端加上恒定的拉伸静载荷,然后将试样浸泡在腐蚀介质中,记录SCC发生的时间。
应用领域:
由于其初始应力明确,试验结果可定量描述材料应力腐蚀敏感性。与恒位移法相比,恒载荷法特别适用于初始应力明确,试验过程中应力保持恒定的情况。
例如,在实际工程中,大型构件在加工、制造或随后的使用过程中不可避免地会产生各种缺陷,即所谓的“带缺陷服役”。在这种情况下,构件承受的外部载荷不会随各种缺陷程度的加深而改变。
另外,依据断裂力学理论,构件发生断裂失效是由裂纹萌生、裂纹扩展、裂纹失稳撕裂几个过程组成。其中,裂纹萌生过程用时最长,约占全过程的90%左右。从这点上讲,恒载荷试验所得结果比恒位移试验所得结果更能代表裂纹萌生时间。因此,恒载荷试验有很强的工程应用价值。
优点:
应力状态明确、试验方法简单、试验周期相对较短,试验没有试样类型和尺寸限制。
缺点:
由于裂纹萌生后,应力水平不断增加,裂纹加速扩展,因此无法获得裂纹扩展速率等信息;此外,如果在高压环境下进行多种材料或研究多种变量对应力腐蚀敏感性试验时,费用会比较高。
慢应变速率法
简介:
慢应变速率(SSRT)法是以相当缓慢的应变速率给处于腐蚀介质中的试样施加载荷,以考察材料应力腐蚀敏感性大小。缓慢加载的目的是让腐蚀介质与金属表面有充分的反应时间。因此,应变速率是试验过程中的一个关键参数,太快或太慢均不合适。对于大多数材料-环境体系,最为敏感的应变速率为10-6~10-7s-1。
试验注意点:
需要注意的是,如果一次试验没有应力腐蚀敏感性,并不能说明该材料没有应力腐蚀敏感性,试验还应该在更宽泛的应变速率下进行试验,包括更低的应变速率,如10-8s-1。
评价指标:
试验结果评价是与在惰性环境中所得数据进行比较,评价指标包含:塑性损伤、断裂强度、吸收能量、断裂时间等,并结合断口形貌和二次裂纹等信息综合评估材料应力腐蚀敏感性大小。
优点:
试验周期短,效率高;评价结果具有多维度、多指标性,不局限于断裂时间一种。
缺点:
设备相对复杂,不便于进行高温高压环境试验,且费用较高;不能从试验曲线中区分裂纹萌生期和扩展期相关信息。
应用领域:
如果仅用于材料筛选的目的,慢应变速率试验无疑是第一选择。然而,由于没有可接受的验收准则,慢应变速率试验并不能用于材料验收评价,即仅用做选材,这与前两种评价方法有本质区别。
鉴于各种应力腐蚀评价方法具有不同的特点及应用范围,为便于在实际工作中选择科学合理的评价方法,笔者对上述3类评价方法进行了对比,详见表1。
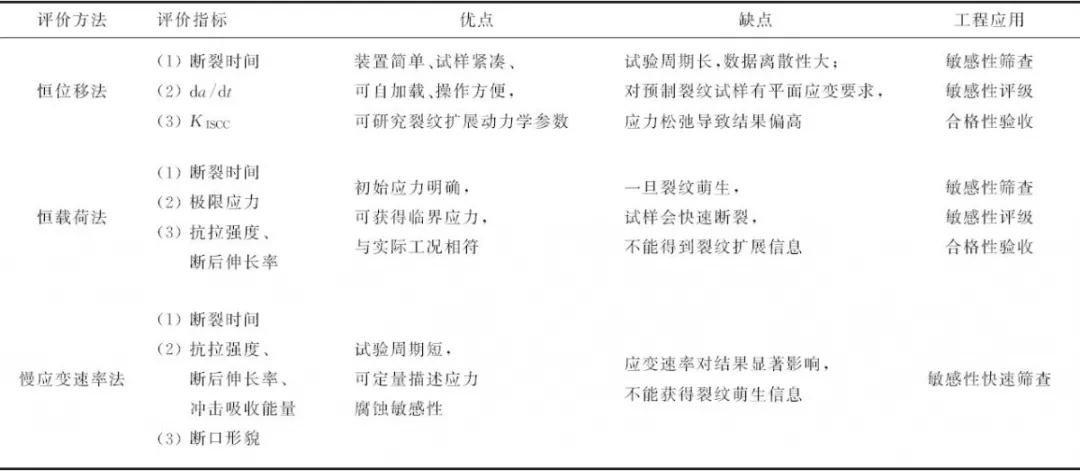
表1 应力腐蚀评价方法对比
结束语
金属材料的应力腐蚀性能与应力状态、腐蚀介质以及材料组织特性密切关系,对于金属材料应力腐蚀评价,多数还是遵照ISO标准执行,不同应力腐蚀评价方法均有其独特的应用和特点。
对于某一特定材料-介质体系,恒位移法、恒载荷法、慢应变速率法所得结果并不一定完全相同。
从应力腐蚀机理来讲,对于以阳极溶解为主的应力腐蚀敏感性评价,3种方法均适用;而当以氢脆为主时,慢应变速率法较为适用,原因在于动态应力过程更有利于氢的扩散和聚集。在具体选取时,应对试验的目的、应用、费用及预期结果等因素进行综合考虑。
总之,如何科学、合理地评价材料应力腐蚀敏感性,既保证工程构件的安全运行,又充分发挥材料性能,仍然需要广大科研工作者不断努力探索。
更多关于材料方面、材料腐蚀控制、材料科普等方面的国内外最新动态,我们网站会不断更新。希望大家一直关注中国腐蚀与防护网http://www.ecorr.org
责任编辑:韩鑫
《中国腐蚀与防护网电子期刊》征订启事
投稿联系:编辑部
电话:010-62313558-806
邮箱:fsfhzy666@163.com
中国腐蚀与防护网官方 QQ群:140808414
免责声明:本网站所转载的文字、图片与视频资料版权归原创作者所有,如果涉及侵权,请第一时间联系本网删除。
相关文章
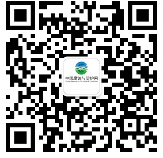
官方微信
《中国腐蚀与防护网电子期刊》征订启事
- 投稿联系:编辑部
- 电话:010-62313558-806
- 邮箱:fsfhzy666@163.com
- 中国腐蚀与防护网官方QQ群:140808414
点击排行
PPT新闻
“海洋金属”——钛合金在舰船的
点击数:5768
腐蚀与“海上丝绸之路”
点击数:4763