砂尘冲蚀是指一定速度和尺度范围、松散的砂尘颗粒流过材料表面时,对材料表面造成的渐近性磨损现象。直升机或运输机在沙漠地带起降,气流诱导砂尘高速吸入发动机,受砂尘颗粒的冲击和磨损作用,压气机叶片外形和结构完整性遭到破坏,导致发动机性能衰减、寿命降低,严重影响作战性能和耐久性。据美国国防部统计:
20世纪60年代的越南战争使美军最早认识到砂尘冲蚀的严重危害。战后,美军与加拿大的公司合作,采用在材料表面制备硬质涂层的方法提高叶片的抗砂尘冲蚀能力。然而,在海湾和阿富汗战争中,硬质涂层并未达到预期的防护效果,带有涂层的压气机叶片依然受损严重。经战后分析:涂层对恶劣的服役环境的适应性、试验考核体系的完备性和有效性不足是导致压气机叶片受损严重的主要原因。
恶劣服役环境的涂层设计、制备技术和工艺的可实现性与稳定性、考核体系的有效性和完备性是抗冲蚀涂层防护系统工程中的关键。本文重点对国内外航空发动机压气机叶片砂尘冲蚀涂层结构设计、制备技术和试验考核三个环节的关键问题进行综述,分析我国在该领域中的不足,展望我国的研究重点和发展前景,对提高武器系统的战备性能、降低后勤保障需求,促进我国高性能、长寿命、高可靠性和易维修性先进航空发动机的研究与发展具有十分重要的指导意义。
1 涂层设计
涂层结构成份和材料体系对冲蚀环境具有一定的适应性,而且“试验—失效—试验”的常用研发模式,周期长、花费高,部分涂层(薄膜)材料的关键参数获得十分困难。因此,在涂层制备和投入使用之前,分析涂层使用的工况环境、自然环境,设计涂层的结构和强韧性,选择材料体系和成份,在冲蚀试验和涂层制备之前,对冲蚀行为进行预测,为涂层的制备和使用提供需求牵引是十分必要的。
1.1 环境适应性
涂层的环境适应性是指涂层对工作环境的自然因素和工况因素的适应程度。自然环境中的温度、湿度和腐蚀性介质以及气动载荷、离心力等工况条件都不同程度影响涂层的抗冲蚀性能和完整性。美军在伊拉克和阿富汗战争中虽然考虑到当地的环境特性,但是,超级种马和海上骑士等多型直升机发动机压气机叶片仍受到严重损伤,部分发动机使用寿命从设计值的3 000小时降为100小时。美国陆军研究实验室在“美国国防特定环境砂粒冲蚀试验方法”报告中指出:恶劣的使用环境是造成美军直升机在沙漠地带受损严重的主要原因之一。
砂尘特性是冲蚀环境中的关键因素。沙漠的高温环境导致砂尘坚硬程度、颗粒外形与尺寸分布与内陆差异较大,这些都直接影响冲蚀损伤程度。美军特别针对伊拉克、阿富汗和科威特等战区环境的砂尘分布特性和微观组织特性开展研究,图1给出了伊拉克和阿富汗Baghram 空军基地等地区,2种不同百分比混合的砂尘颗粒(Golf sand和Yuma dust)、672mph和500mph(1mph=1.609 344km/h)2种冲蚀速度条件下的冲蚀试验试样的质量损失,由此可见砂尘特性的差异对冲蚀损伤的影响。
1.2 材料体系
图2是砂尘对材料表面的冲蚀损伤机理,金属材料表面遭受砂尘小角度冲蚀时,磨损机制以微切削为主,而大角度(接近垂直)冲击时,冲击产生的微裂纹或者损伤成为疲劳源,疲劳破坏成为主要失效机制。
为提高材料表面的抗冲蚀性能,一般采用硬质涂层材料,且硬质涂层材料的断裂韧性逐渐受到关注,涂层材料的硬度和断裂韧性都是涂层十分重要的机械性能。陶瓷-陶瓷、金属-陶瓷等5种不同基体-涂层材料的断裂韧性和硬度如图3所示,图中横坐标为材料断裂韧性,纵坐标为硬度,α为材料抗冲蚀行为表现优秀的冲蚀角度,阴影1~5分别表示包括陶瓷及金属的5种具有脆性和塑性的材料,可见材料1具有较低的断裂韧性和较高的硬度,对小角度(小于30°)冲蚀较有效,而材料5具有较好的断裂韧性和较低的硬度,对大角度(大于60°)的冲击有效。而相比材料1和5,材料2、3和4同时具有较好的断裂韧性和硬度,对全角度防护冲蚀有效。
世界各国对抗冲蚀涂层的研究主要集中在陶瓷涂层、WC/Co涂层、ZrN等。近年来,尤其在TiAlN、高分子涂层、超弹性硬质涂层和SiC/SiC涂层深入发展。目前抗冲蚀涂层已经在国外的发动机上得到广泛应用,美国在MDS-PRAD、GE公司等单位的协助下,20世纪80年代美军就已经将抗冲刷涂层技术应用在直升机、运输机发动机上。近20年来,应用最多的主要是ER7和BlackGold涂层。ER7涂层的主要成份为TiN,BlackGold涂层的主要成分为TiAlN。
1.3 结构与强韧性
涂层是提高叶片抗砂尘冲蚀的有效措施。但是,复杂的冲蚀损伤机理导致结构简单、性能单一的涂层无法满足防护要求。涂层的抗冲蚀性能与涂层结构、强韧性和砂尘特性等密切相关。抗冲蚀涂层发展初期,涂层硬度被普遍认为是提高材料抗冲蚀性能的关键因素,高硬度的陶瓷涂层可降低砂尘冲击时塑性变形导致的磨损,从而提高叶片抗冲蚀性能。然而,在伊拉克和阿富汗战争中,超硬涂层并未达到期望的防护效果,带有陶瓷涂层(TiN 和CrN)的叶片仍然受砂尘冲蚀。虽然陶瓷涂层具有较高的硬度,但是脆性大、断裂韧性低,导致涂层在受到恶劣环境砂尘粒子冲击时极易出现裂纹。
为提高涂层韧性,可在硬质涂层中增加延性金属,形成复合涂层,也可以将硬质涂层和延性金属交替排列,形成多层陶瓷-金属涂层。由于多层陶瓷-金属涂层具有良好的韧性和硬度,且结构形式和种类多样,成为抗冲蚀涂层的研究趋势。
美军成功应用于装备的ER7涂层微观结构示意如图4所示,该涂层由软/硬(Soft layers/Hard layers)交替排列而组成,并通过渡层(Transition)使涂层与机体相互结合。相比单层涂层,该涂层结构具有较好的断裂韧性和抗冲击能力,交替的多层结构和梯度过渡区域有利于降低涂层内应力,提高涂层的耐久性。目前,已在多型号涡轴、涡扇发动机上大规模使用。
1.4 结构设计方法
加拿大的研究人员采用三维数值仿真的方法,模拟局部外形尖、尺寸不同的砂尘对材料表面的损伤,重点分析复杂外形砂尘对材料表面的冲蚀损伤机制。采用有限元方法对砂尘以V0=84m/s的速度单次冲击情况进行模拟,如图5所示,以多层涂层的拉应力最小化为目标,分析了涂层表面应力的动力学响应,如图6所示。
美国宾夕法尼亚大学的科研人员开展了多层涂层结构设计优化研究,2层和32层结构的涂层分别对氧化铝颗粒和玻璃颗粒的冲击具有较好的防护效果,进一步说明某种涂层材料和结构仅可以在特定的或一定条件范围内满足冲蚀防护要求,为多层涂层系统优化设计奠定了较好的研究基础。文献以多层TiN涂层发展过程中存在的问题为研究背景,针对Ti0.75X0.25C材料,发展了一种新的断裂韧性估算方法(Density FunctionTheory,DFT),该方法计算出的弹性模量、表面能和断裂韧性与试验数据和其他理论方法计算结果具有较高的一致性,计算结果表明,钽和钨在提高ER-7陶瓷涂层断裂韧性方面是十分有效的。文献采用DEM 分析法,对不同角度、不同速度和粒子密度情况下,粒子冲击平板情况进行模拟,将单个粒子冲击与多个粒子冲击结果进行比较,主要目的是对DEM 方法的有效性进行估算,相比较得到结论:切向冲击能量和冲蚀率最大值出现在20°~30°,正向冲蚀能量出现在冲蚀角度80°,计算结果与试验结果有较强的一致性。
2 涂层制备
涂层制备技术是实现涂层应用的核心。目前,涂层制备技术繁多,然而,选择涂层制备技术,除需获得涂层本身的基本性能外,制备方法对基体材料疲劳性能的影响,制备技术本身的稳定性与可实现性也十分关键。
2.1 物理气相沉积
近年来,随着高能真空等离子体技术的飞速发展,气相沉积逐渐成为制备涂层的主要技术手段。气相沉积技术是通过使材料气相化后沉积于固体材料表面的一种薄膜制备方法,该方法主要包括物理气相沉积(Physical Vapor Deposition,PVD)和化学气相沉积(Chemical VaporDeposition,CVD)2大类方法。物理气相沉积、化学气相沉积、热喷涂以及堆焊等制备涂层厚度和处理温度如图7所示。可见,化学气相沉积和堆焊方法涂层制备的温度过高,尤其对于钛合金压气机叶片,具有较强的腐蚀性。热喷涂方法可将涂层制备控制在较低的温度,涂层制备厚度超过1 000μm,但是热喷涂方法涂层与基体的结合强度不能满足要求。
物理气相沉积方法是用物理的方法,将镀膜材料气相化,再沉积在叶片表面的过程。物理气相沉积包括溅射镀和离子镀等,以及目前飞速发展且应用最多的磁控溅射离子镀技术。
制备方法对材料疲劳性能的影响。虽然在燃气轮机部件表面使用抗冲蚀和腐蚀涂层,疲劳极限降低10%~15%是允许的,但是理论和实践经验表明,直升机疲劳极限最多不能下降超过10%。美军针对ER7涂层对3种压气机叶片材料在不同测试环境温度下(800F,600F,400F即426.7,315.6,204.4℃)的疲劳性能开展实验研究如图8所示,ER7涂层对3种压气机材料的疲劳强度影响不大,在可接受的范围内,其中,钛合金叶片对疲劳性能比较敏感,疲劳强度下降了约10%,可采用在叶片根部的疲劳敏感区域不制备涂层的方法保证材料的疲劳强度。
2.2 制备技术中的关键问题
材料表面制备硬质涂层,增加了裂纹萌生的倾向,尤其是钛合金对表面十分敏感,硬质涂层脆性较大,一旦表面出现缺陷就会降低疲劳性能。材料的疲劳性能与制备方法和工艺的选择有很大关系,一直是亟待解决的难题。
此外,对于外形复杂、遮挡严重部件的制备问题仍是制约制备技术应用于实际装备的关键问题。物理气相沉积方法中的磁控溅射离子镀技术,在实现对镀膜材料大面积稳定溅射的同时,利用特殊配置的电磁场技术控制溅射电子在真空腔内的运行轨迹,提高原子离化率,同时在薄膜物质沉积的过程中伴有离子的轰击过程,实现镀膜材料的物质沉积和能量沉积,因此,具有膜基结合强度高、薄膜致密、温升低等优势。离子轰击物理过程,对涂层内部形成压应力以及提高基体疲劳性能等方面都存在一定优势,而且,由于电磁场的控制具有一定的绕性,有利于遮挡部位的涂层制备。因此,磁控溅射离子镀目前已成为工业领域制备硬质涂层的常用手段。
为确保涂层对压气机叶片表面的实时防护,涂层与基体之间需有较高的结合强度,使涂层受到砂尘冲击仍保持一定完整性。物理气相沉积方法,通过制备过程中涂层材料物质和注入能量的双重沉积,提高涂层与基体之间的结合强度,物理气相沉积在较低的温度制备涂层,可有效降低涂层的内应力,降低涂层遇冲击开裂的可能性。此外,对涂层制备表面进行预处理,获得一定的清洁度和粗糙度,改善表面机械性能,去除表面氧化膜,使基体显露出“新鲜金属”,与其他表面处理方法结合,复合强化的方法也是提高结合强度的有效方法。ER7涂层的制备过程如图9所示,叶片先后经过酸洗、超声清洗、涂层PVD 制备、特殊振动处理、视觉检测、金相检测,最后投入使用。
3 试验体系
冲蚀试验体系是评价涂层设计的有效性、制备技术可控性、稳定性以及涂层抗冲蚀性能最为直观和有效的措施,试验体系的完备性和有效性直接影响涂层在实际使用中的防护能力。
3.1 美军标中冲蚀试验规范
美军2010年发布的军标3033号为飞机发动机叶片常用材料的耐砂蚀(颗粒侵蚀)性能测试提供标准。测试方法用于检测飞机发动机叶片抗侵蚀系统常用材料的耐砂蚀(颗粒侵蚀)性能。包括合成橡胶、强化塑胶和复合材料、金属、陶瓷及涂层。军标中针对静态样本,开展在高速气流不断带入的砂粒作用下的材料遭受冲蚀试验测试,如图10所示。
标准规定:颗粒直径大约为240~550μm,颗粒密度为30 g/cm3,颗粒速度为(222.5±10.7)m/s,撞击角度为20°~90°之间,测试温度应为(23.9±2.8)℃,相对湿度(RH)为50%。
3.2 试验体系的完备性
美军的军用标准中已针对预处理试样的温度、湿度、测试温度和湿度、侵蚀物尺寸、成份、冲蚀速度和角度、砂尘颗粒负载量等进行了详细的规定。然而,军用标准中的试验条件与实际使用中仍存在较大差异,因此仍需建立完善的冲蚀试验体系,且加强试验的有效性验证。为考核冲蚀涂层的防护效果,美军的冲蚀试验体系包括了实验室原理性验证、吞砂试验、疲劳试验、外场小规模验证试验等。
首先在实验室条件下开展了涂层砂尘防护效果的原理性验证实验,使用粒径为10~100μm,速度达到213。4m/s的二氧化硅沙粒冲蚀试样,冲蚀设备运行时间与试样质量损失的关系如图11所示,由图可知随着磨蚀砂尘量的增加,压气机叶片的弦长损失量逐渐增加,当损失量到达设定的门限值时,压气机叶片到寿、报废。两条曲线的对比表明涂层能够大幅提高压气机叶片的使用寿命达2倍以上,初步验证了涂层的砂尘防护效果。
考虑到实验室条件下难以模拟发动机整机的吞砂情况,因此后续开展了涂层在发动机整机(T64)上应用的试验研究。试验结果如图12所示,表明涂层的防护效果明显。
涂层性能的考核主要包括:涂层基本力学性能、摩擦学性能指标、静止试样的冲蚀试验、转动试样冲蚀试验、试样疲劳性能测试、叶片冲蚀和疲劳性能测试试验、发动机吞砂试验及外场小规模验证试验。此外,针对特定环境应包括:雨水、沙石和雨水的共同作用、水解作用、阳光辐射、空气氧化、极端天气、温度骤变、盐雾、电磁兼容性、热传导等,开展涂层环境适应性研究。
4 国内研究现状与差距
我国的全天候和全疆域作战需求要求直升机和运输机需具备复杂地域和恶劣气候下的作战能力。然而,我国现役航空器其发动机仍未采用砂尘防护措施,发动机容砂能力差极大地限制了作战使用要求。
1)机理研究不够深入。砂尘环境下,基体与涂层的冲蚀损伤与防护是砂尘粒子与涂层相互作用的结果。砂尘冲击条件下的多层涂层动态响应规律和损伤机理,这一问题直接影响涂层的抗冲蚀性能和基体的防护效果。然而,目前国内外在这方面报道极少,尤其对于交替排列的多层涂层,已有的研究对冲击应力波在多层涂层内部以及涂层多个界面反射、折射传播过程的描述仍不多见,无法获知多层涂层防护下,基体和涂层材料的冲击动态响应以及冲击最终形成的复杂应力、应变场状态。同时,对于陶瓷和金属交替排列的多层涂层结构,其损伤模式和机理既有别于金属的塑性变形,也不同于陶瓷的脆性断裂。而这些问题都严重影响着涂层的抗冲蚀性能。因此,急需开展多层涂层结构强韧性和损伤机理的研究,为建立涂层设计体系奠定理论基础。
2)涂层结构与性能设计研究亟待加强。抗冲蚀涂层研究应包括涂层设计、制备方法和技术以及性能考核3个主要环节。针对涂层使用环境的自然因素和工况因素对涂层结构和性能进行设计,对涂层制备具有十分重要的引领作用。然而,我国现有的研究中忽视了这个环节,导致涂层性能需求不明确,制备方法的工艺选择十分盲目。
3)考核手段仍不完备、有效性亟待验证。我国现有的试验一方面集中在涂层的基本性能测试,主要包括硬度、断裂韧性以及膜基结合强度等基本性能指标对涂层抗冲蚀性能存在重要影响。
4)研究系统性不强。我国多年的研究成果仍不能在武器装备上广泛应用,涂层设计环节的指导性、涂层制备的可实现、可控和稳定性以及涂层考核体系的完备和有效性等重点环节不能形成系统的研究体系是主要原因。涂层需求论证不准确,制备方法选择的不恰当、工艺可靠性低,再加上考核体系无法贴近工况,最终导致涂层的防护能力不能满足实际需求。
5 结 论
对国内外航空发动机压气机叶片砂尘冲蚀问题进行综述,分析美军防护涂层的发展过程,重点阐述环境适应性、结构强韧性设计、制备技术和试验体系等制约涂层发展的关键问题。经过20多年的研究与应用,目前,国际上在抗冲蚀涂层领域的发展正朝着材料体系不断创新、涂层结构强韧性匹配更加合理、设计手段不断丰富、制备技术更加成熟、试验条件更为有效的方向发展。我国在抗冲蚀涂层领域存在机理研究不深入、缺少涂层设计以及考核体系不完善等关键问题,这些都是我国抗冲蚀涂层领域的发展方向和研究重点,加强抗冲蚀涂层研究对提高我国航空发动机容砂能力与作战性能具有重要的战略意义。
更多关于材料方面、材料腐蚀控制、材料科普等方面的国内外最新动态,我们网站会不断更新。希望大家一直关注中国腐蚀与防护网
责任编辑:王元
《中国腐蚀与防护网电子期刊》征订启事
投稿联系:编辑部
电话:010-62313558-806
邮箱:fsfhzy666@163.com
中国腐蚀与防护网官方 QQ群:140808414
免责声明:本网站所转载的文字、图片与视频资料版权归原创作者所有,如果涉及侵权,请第一时间联系本网删除。
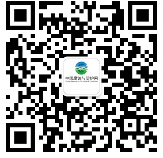
官方微信
《中国腐蚀与防护网电子期刊》征订启事
- 投稿联系:编辑部
- 电话:010-62313558-806
- 邮箱:fsfhzy666@163.com
- 中国腐蚀与防护网官方QQ群:140808414