近年来高速列车的快速发展对车体轻量化提出了更高的要求,高速铁路车辆采用铝合金中空结构比钢结构减轻自重35% ~ 66%,同时可增效和节能10% 以上。 5、6、7 系铝合金由于各自的优异性能,已被应用于制造高速列车车体各主要部件,对车体的安全运行起着至关重要的作用。
工业废气和汽车尾气形成NO -3和SO - 42以及来源于海洋的Cl - ,容易对车辆用铝合金造成腐蚀破坏。 特别是7 系高强度铝合金对应力腐蚀SCC( stress corrosion cracking) 开裂非常敏感,在服役过程中,应力腐蚀是导致铝合金构件失效的主要原因。 陈小明等认为影响7000 系铝合金的SCC敏感性因素很多,如热处理工艺、外部环境、电化学效应等。
本文对车体用5、6、7 系铝合金按两种不同加载方式进行应力腐蚀试验,探讨其抵抗应力腐蚀开裂性能,对高速列车车体制造及运行过程中车体铝合金应力腐蚀行为进行评价。
1 试验原理
应力腐蚀试验( SCC) 方法分为恒载荷试验和恒位移试验。 本文试验中全部使用机械预制裂纹试样。 对试样进行机械切口并预制疲劳裂纹,通过在施力点施加恒定载荷或恒位移,在化学侵蚀性介质中进行试验,通过观察其表面和断口形貌来判断其应力腐蚀敏感性。 恒位移应力腐蚀试验中采用三点加载的方式,最大应力出现在凸形表面的中部,并线性下降至外支点处为0. 根据GB /T 15970. 2—2000《弯梁试样的制备和应用》可知,三点弯凸形表面中点弹性应力为式中:
σ 为最大张应力; E 为弹性模量; B 为试样厚度; y 为三点弯凸形最大挠度; H 为外支点间距。
恒载荷试验中采用悬臂梁试样,如图1 所示。
通过引伸计采集数据曲线和试样断口形貌判断是否发生应力腐蚀开裂。
根据弹塑性力学原理可知,试样所受弯矩为
其中: M0为夹具自重产生弯矩; F 为可调加载载荷; L 为加载载荷力臂。
根据GB /T 15970. 6—2007《预裂纹试样的制备和应用》可知,计算初始应力强度因子为
其中: α = 1 - ( a /W) ; a 为断口裂纹长度; W 为试样宽度。
2 试验内容
针对高速列车常用5083P-H111、6005A-T6、7N01P-T4 铝合金,采用恒位移和恒载荷两种加载方式对比其应力腐蚀性能,3 种铝合金材料化学成分、力学性能如表1和表2 所示。
试验按照ISO7539-2003《金属和合金的腐蚀应力腐蚀试验》进行。 恒位移应力腐蚀试验时,每组材料试件数量为2,试样B = 6 mm,W = 12 mm,三点弯跨距为60 mm. 为了使试验具有可比性,取加载到3 种材料上最大应力都接近于材料屈服强度值,试样加载情况见表3 所示。 放入周期腐蚀试验箱内进行腐蚀,温度为室温25 ℃,腐蚀液为质量分数3. 5%的NaCl 溶液,箱内相对湿度为70 ± 5%,腐蚀时间为80 d.
恒载荷应力腐蚀试验时,采用线切割切口试样,切割用钼丝直径Φ≤0. 2 mm,B = 6 mm,W =12 mm,切口长为2 mm,预制疲劳裂纹在YK-1 型音叉式疲劳开缝机上进行。 预制疲劳裂纹后,在试样缺口两侧贴好刀口,在CFW-150 型悬臂梁应力腐蚀持久试验机上加载,将裂纹区域浸入质量分数3. 5%的NaCl 溶液中。 试验中利用引伸计监测刀口张开位移δ,观察采集的δ-t 曲线,判断启裂时间,同时对δ-t 曲线不发生变化的试样,试验时间适当延长。 试验完成后,用三点弯曲法在WDW-3100 型拉压试验机上将腐蚀试样压断,用JSM-6490LV 扫描电镜SEM( scanning electron microscopy) 观察腐蚀断口及腐蚀产物形貌。
3 试验结果及讨论
3. 1 恒载荷应力腐蚀
3. 1. 1 试验结果恒载荷试验获得数据如表4 所示。
从表4 看出,试样承受最大弯矩为27. 13 N·m时,5083P-H111、6005A-T6 铝合金都没有发生SCC 开裂,7N01P-T4 试样有很明显的SCC 开裂。
为了得到7N01P-T4 铝合金发生SCC 开裂的应力临界值,逐步减小加载弯矩,从表4 可以看出,HZ-4 ~ HZ-10 号试样加载弯矩一直减小到7. 255 N·m( 试验装置所能加载最小弯矩) 时,HZ-10号试样仍发生了SCC 开裂,由此可推断7N01P-T4 铝合金的KⅠSCC值应低于11. 238 MPa·m1/2 .
HZ-10 号试样在承受最小弯矩7. 255 N·m 时仍发生应力腐蚀,表明当7N01P-T4 铝合金构件处于潮湿含氯离子的环境中,裂纹前端KIi >11. 238 MPa·m1/2时,发生应力腐蚀破坏。
假设应力腐蚀裂纹尖端简单且完全平直,根据式( 4) 可得到疲劳裂纹尖端的正应力。 以试样加载K1SCC最小的HZ-10 号试样为模型进行计算,Mmin = 7. 255 N·m,试样的有效宽度、厚度分别为5. 735、5. 90 mm,则式中:
σ 为对试样施加载荷产生应力; Wz为试样弯曲截面系数。
经计算得到σ = 224. 3 MPa,此值为力学理想模型下估算值。
由于试件板厚尺寸的限制,该值理论上稍偏高。 对于7N01P-T4 铝合金母材,其抗拉强度σb为460 MPa,σ/σb = 0. 488,此估算值再次证明试验采用7N01P-T4 铝合金的应力腐蚀敏感性很高。
3. 1. 2 试样裂纹宏观形貌
恒载荷应力腐蚀实验中,5083P-H111 和6005A-T6 铝合金母材表面都未出现应力腐蚀裂纹,7N01P-T4 母材发生了应力腐蚀表面出现了细小的应力腐蚀裂纹,宏观形貌如图2 所示。
从图2 看出,5083P-H111 和6005A-T6 铝合金试样疲劳裂纹下面只有腐蚀产物的堆积,没有出现应力腐蚀。 7N01P-T4 的HZ-4 号试样疲劳裂纹下出现了明显的分叉式应力腐蚀裂纹,主裂纹比较平直,细小的裂纹分叉随机分布。
3. 1. 3 试样断口宏观形貌
恒载荷应力腐蚀试验中,5、6、7 系列铝合金试样断口宏观形貌如图3 所示。
图3( a) 中,HZ-1 号试样断口平整细腻,没有出现应力腐蚀沟槽。 图3( b) 中,HZ-2 号试样预制疲劳区断口比较粗糙,出现了直线沟槽,一直延伸到线切割切口处,但疲劳裂纹前端没有出现应力腐蚀裂纹,没有发生应力腐蚀开裂。 图3( c) 中,HZ-4试样断口上应力腐蚀区出现了明显的应力腐蚀裂纹,且疲劳区也出现了较深的直线沟槽,一直延伸穿过线切割区。 图3( d) 为HZ-10 号试样加载最小载荷经过12 d 腐蚀后的断口图,疲劳裂纹前段有细微的应力腐蚀开裂,说明应力腐蚀刚刚开始,而疲劳裂纹区上直线沟槽也有扩大变深的趋势。
3. 1. 4 试样断口微观形貌
应力腐蚀试样断口扫描电镜如图4 所示。
图4( c) 中,5083P-H111 断口疲劳区平直无褶皱,其上很多点坑无序排列着,其尺寸比塑性区韧窝尺寸小很多,点坑很浅,可认为没有发生应力腐蚀。 腐蚀液中的Cl - 吸附在试样表面,氧化膜破坏的倾向增大,根据变形显微组织的特点,可知试样表面的点蚀将向纵深发展,沿晶间不断往纵向和横向扩展直到晶界处的β 相被腐蚀掉,晶粒脱落,当各蚀坑沿晶间彼此相连时,形成片层状金属脱落。 图4( a) 中,6005A-T6 疲劳区断口上有很多平行链状点坑,其方向与板厚方向平行,同时在断口上可看到明显的直线沟槽,其方向与点坑方向一致,推测直线沟槽是由链状点坑扩展而来。 在直线沟槽附近A 区进行能谱分析,结果如图5 所示。
由图5 可知,A 区域中,Mg 含量为1. 82%,高于标准的0. 4% ~ 0. 8%. Mg 含量越高时,合金耐蚀性能就比较差,从而产生链状点坑。
图4( b) 为7N01P-T4 试样SCC 区前段塑性压断区,很多二次裂纹平行分布并不相连,其裂纹起源于SCC 裂纹顶端,处在应力腐蚀裂纹尖端,同时裂纹间隙、深度较小,在塑性压断过程中没有与主应力腐蚀裂纹相连,其穿过塑性压断区韧窝,向塑性区扩展。 图4( d) 为图4( b) 中SCC 前端B 区,可在应力腐蚀裂纹底部发现类似冰糖状花样,晶粒边缘较钝可能是腐蚀时间过长所致,空洞可能是第二相粒子的脱落形成。 图4( e) 为7N01P-T4 试样在最小载荷作用下疲劳区前段发生应力腐蚀开裂,其裂纹附近覆盖了较厚的一层腐蚀物,说明应力腐蚀裂纹一旦开裂,腐蚀液沿着应力腐蚀裂纹向材料深处润湿,从而引发深处材料继续受到应力腐蚀。
3. 2 恒位移应力腐蚀
3. 2. 1 试样裂纹宏观形貌
恒位移腐蚀实验中,试样表面宏观形貌如图6所示。 图6 中试样表面被灰色腐蚀产物覆盖,三点弯支点处由于与钢接触产生了电化学腐蚀,出现了一些点蚀坑和剥蚀。 线切割开口处表面没有出现裂纹,试样表面其他位置由于包铝层的保护作用,没有出现明显的腐蚀现象。
3. 2. 2 试样断口宏观形貌
恒位移应力腐蚀试验中5、6、7 系列铝合金试验腐蚀80 d 后压断后断口宏观形貌如图7 所示。
在图7( a) 、( b) 中,5083P-H111 和6005A-T6铝合金试样断口平齐,机械切口下部并没有出现应力腐蚀裂纹; 图7( c) 中试样有应力腐蚀裂纹经压断形成的明显“舌状”突起,与板厚方向平行,中部还延伸有细微的二次裂纹,相互平行并不交叉。
3. 2. 3 试样断口微观形貌
7N01P-T4 铝合金试样发生了应力腐蚀,其断口扫描电镜如图8 所示。
图8 中可知,HW-5 断口上有多条相互平行的应力腐蚀裂纹,裂纹平直并不连续,有未连接的台阶裂纹,符合氢致破裂机理。 HW-5 断口微观形貌与图4( b) 的形貌相似,从而证明了7N01P-T4 试样在恒位移应力腐蚀实验中也发生了应力腐蚀现象。
4 分析讨论
关于铝合金应力腐蚀机理主要有3 种理论: 阳极溶解、钝化膜破裂和氢致开裂。 Burleigh 指出,对7 系铝合金应力腐蚀,适用性按以下顺序递减: 氢致开裂﹥钝化膜破裂﹥阳极溶解。 在很多7 系铝合金失效分析结果中认为,氢引起开裂的应力腐蚀。 7N01P-T4 铝合金中,Zn 和Mg 是形成强化相的主要合金元素,其主要强化相是η( MgZn2)相。 η 相在共晶温度下溶解度达28%,在室温下降低到4% ~ 5%,有很强的时效强化效果,并且时效时间越长其强化作用越显着。 7N01P-T4 铝合金轧制板材材,强度可高达460 MPa左右,其强化相η 相在晶界处容易聚集形成较细小的连续链状质点。 图6 中应力腐蚀裂纹附近Mg 元素含量偏高,除了时效相变造成η 相偏聚外,还有部分自由Mg在晶界偏析。 而自由Mg 在晶界偏析会促使氢在晶界偏聚,氢在晶界的偏聚使晶界结合能下降,促使裂纹扩展。 铝合金在潮湿空气中电化学腐蚀阴极析氢反应产生的原子氢是主要来源。
根据对氢在金属中行为的了解,在应力腐蚀发生后,阴极析氢反应产生的活性氢原子能够扩散到铝合金内难溶相与基材间的空隙聚集,既使该处变脆,又复合成氢分子,由此形成的巨大内压使微裂纹产生并协助局部应力使裂纹解理扩展; 其次,因氢具有应力诱导上坡扩散的特性,氢原子会向裂纹尖端应力集中处扩散聚集,当氢量增至临界值后裂纹扩展,随后继续此过程。 因此,裂纹可以是异地萌生、扩展相连。 氢脆与应力腐蚀同时发生,由应力腐蚀阴极反应而导致的氢脆在裂纹源区附近则呈现典型的应力腐蚀特征,如图4( d) 所示。 图4( b) 和图8 断口氢脆裂纹特征明显裂纹平直没有分叉,整个过程与焊接时产生氢致裂纹十分相似,具有延迟、间歇扩展特点,并且是混合型断裂。
氢致穿晶裂纹形成过程的推测解释6、7 系铝合金断口疲劳区上直线沟槽的产生。 6、7 系列铝合金难溶相呈链式分布在晶界上,其方向与挤压或扎制方向平行。 由于力学性能与基体有差异,在疲劳裂纹扩展时,疲劳裂纹断口上形成直线沟纹。 当产生电化学腐蚀阴极析氢反应,产生活性氢原子,除就地参与应力腐蚀外,还长程扩散到难溶相周围聚集并复合成氢分子造成内压力促成裂纹生成,使原先的沟纹扩大伸长变成裂纹。 6 系铝合金属于Al-Mg-Si 系铝合金,没有出现应力腐蚀,电化学腐蚀析氢反应产氢量少,不足以使直线沟纹扩大。5083P-H111 属于非热处理铝合金,不仅没有发生应力腐蚀,也没有直线沟纹。
5 结论
( 1) 通过恒载荷和恒位移实验得到5083PH111、6005A-T6 铝合金应力腐蚀敏感性小,7N01P-T4 容易出现应力腐蚀裂纹,断口上有“舌状”凸起;( 2) 7N01P-T4铝合金K1SCC值应在11.238 MPa·m1/2以下,对应的应力临界极值为224. 3 MPa,σ/σb =0. 488,应力腐蚀敏感性高;( 3) 应力腐蚀裂纹容易引起二次微裂纹,应力腐蚀阴极反应导致的氢脆在裂纹源区附近则呈现典型的应力腐蚀特征,有明显冰糖状花样;( 4) 应力腐蚀阴极反应导致的氢脆在疲劳区附近则呈现氢致开裂特征,与7N01P-T4 断口上直线沟槽相符。
更多关于材料方面、材料腐蚀控制、材料科普等方面的国内外最新动态,我们网站会不断更新。希望大家一直关注中国腐蚀与防护网http://www.ecorr.org
责任编辑:王元
《中国腐蚀与防护网电子期刊》征订启事
投稿联系:编辑部
电话:010-62313558-806
邮箱:fsfhzy666@163.com
中国腐蚀与防护网官方 QQ群:140808414
免责声明:本网站所转载的文字、图片与视频资料版权归原创作者所有,如果涉及侵权,请第一时间联系本网删除。
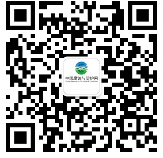
官方微信
《中国腐蚀与防护网电子期刊》征订启事
- 投稿联系:编辑部
- 电话:010-62313558-806
- 邮箱:fsfhzy666@163.com
- 中国腐蚀与防护网官方QQ群:140808414