在石油化工行业, 热壁加氢反应器已普遍取代了冷壁加氢反应器。这些热壁加氢反应器大部分是由2.25Cr1Mo钢制成的。加氢反应器在高温高压、临氢条件下工作时, 构件材料面临着介质腐蚀、应力腐蚀、氢腐蚀、氢脆、回火脆化等一系列问题。同时反应器内的硫化型固定床催化剂,由于积碳、金属沉积或活性组分状态的变化,催化剂的活性存在下降的情况、影响长周期运行。因此,加氢反应器工艺保护措施的制定尤为重要。
反应器工艺保护措施
01防止氢致开裂
正常操作过程中,在高温高压操作条件下,反应器的钢材内部溶解大量氢原子。氢气在钢材中的溶解度随温度的降低而降低,随压力的降低而降低。在装置停工过程中如果降温速度过快,氢气来不及从钢材内部扩散出来,而出现过饱和状态,超过钢材的安全氢浓度,就会导致机械性能下降,甚至开裂。
由于氢气在母材与奥氏体不锈钢堆焊层中的溶解度和扩散速度不同,将在过渡层上吸存大量的氢,且因二者的线膨胀差别较大,而形成很大残余应力使母材与堆焊层出现剥离现象。因此,在装置停工过程中,需进行一定的“恒温氢解”操作,防止损坏设备。
在装置停工过程中,反应系统热氢带油结束之后,首先以0.5-1.0MPa/h速度将高分压力降低至操作压力的1/3左右,以10-20℃/h速度降低反应器入口温度(一般比正常操作温度低20-50℃),恒温氢解12h,然后将反应温度降低至250℃,恒温氢解12h。
02防止连多硫酸应力腐蚀
奥氏体不锈钢在高温、硫化氢存在的条件下,设备与介质接触的表面会形成一层腐蚀产物FeS。在停工过程中,当反应系统降温降压后有水汽冷凝下来或打开设备进行检查检修时,设备和管线内部的金属表面与湿空气接触,FeS与水和氧气接触发生化学反应,生产亚硫酸和连多硫酸。连多硫酸会引起奥氏体不锈钢晶间腐蚀,在晶间拉伸应力和连多硫酸作用下引起连多硫酸应力腐蚀开裂(PSCC)。
在装置停工过程中需对反应器加以保护。装有催化剂的反应器,先充氮气保护,保守氮气微正压。卸催化剂必须在气封闭的条件下进行,卸完催化剂后,反应器及内构件要立即进行中和清洗。中和清洗的中和液一般适用1.5%-2.0%的Na2CO3溶液,不得适用NaOH等强碱,以避免导致钢材应力腐蚀开裂,中和液中Cl-浓度不能超过20ppm。在中和液中增加0.5%的硝酸钠,可以防止氯化物应力腐蚀开裂。
强制循环中和清洗时间为4h以上,静止浸泡时间在6h以上,喷淋冲洗应该保持表面碱液湿润2h以上,并用塑料布覆盖,冲洗时候顺序从上往下,每个角落都要冲洗到,拆下的内构件应尽快放入碱液中浸泡,时间不小于6h。中和清洗完毕后,用软化水清洗干净,清洗完后反应器用干燥空气吹扫。
03防止回火脆性
热壁结构与冷壁结构相比有许多优点,冷壁结构不仅有效容积利用率低(一般只有50%~60%),而且在使用中比热壁结构更易产生局部过热,给安全操作带来危险,甚至被迫停产。
回火脆化是由于金相改变所致的韧性减少,长期在343℃—593℃条件下使用或在此温度范围内缓慢冷却而导致材料的韧性劣化的现象,造成的损伤会导致灾难性的脆断。
受影响的材料主要包括2.25Cr1Mo 低合金钢,3Cr1Mo以及高强度低合金CrMoV 转子钢。回火脆化不会显着影响C0.5Mo 和1.25Cr0.5Mo合金钢,但是其他高温损伤机理会促进金相改变,从而改变材料的硬度或高温延性。
为了使启动和关闭时出现脆断的可能性最小化,许多炼厂采用增压程序把系统压力限制在最大设计压力的25%内,使温度低于最小增压温(MPT)。
采用2.25Cr1Mo 低合金钢制造的反应器,遵规定的最低加压温度为93℃ , 在开停工工过程中都严格地执行了热态开停工方案,即在反应器壁温度大于93℃时,才能升高压力至反应系统设计压力的1/4以上,同时升降温速度要30℃/h。
加氢催化剂工艺防护措施
01监测控制原料金属含量,防止催化剂失活
催化剂的失活可以分为两种,一种是暂时性失活,可以通过再生的方法恢复其活性;另一种是永久性失活,无法恢复活性。金属元素沉积在催化剂上,会促使催化剂永久失活。常见的使催化剂中毒的金属有铅、铁、镍、钒、砷、钠、锌、钙等。
铅中毒主要发生在重整原料预加氢过程,原料油中混有含铅汽油,会造成加氢催化剂铅中毒。
铁、镍、钒等重金属有机物在临氢条件下发生氢解,生产的金属以硫化物形式沉积在催化剂孔口和表面,造成催化剂失活、床层压降上升。一般加氢反应器需装填加氢脱金属剂,原料中的铁离子含量控制在1.0mg/kg以内。
砷对加氢催化剂有中毒作用,含砷1.2%的催化剂,再生后的脱氮活性仅为新鲜催化剂的70%。一般汽油加氢类装置应设置脱砷反应器,柴油加氢类装置应重点监控常减压柴油中的砷含量。
钠、锌、钙等碱性金属或碱土金属对催化剂酸性中心具有中和作用,进而造成催化剂中毒。在加氢过程中,这些金属的化合物很快发生氢解,沉积在催化剂颗粒之间和孔口,造成催化剂失活、床层压降上升。
02强化过程控制,防止催化剂结焦还原
催化剂干燥阶段,干燥介质禁止含烃,干燥过程中不得出现窜油、窜气事故。
催化剂硫化阶段,不得选择烯烃含量过高的硫化油,升温注硫速度不得过快,控制好各床层温度。硫化结束后,应进行初活稳定或钝化,不得直接进原料油。因初期活性较高,直接进原料油会导致催化剂快速结焦。
正常生产过程中,循环氢纯度、氢油比、氢分压、空速等指标不得低于设计值,监控原料中硫、氮、残炭、烯烃、稠环芳烃等杂质含量,防止催化剂结焦。
装置异常停电、停机等事故应急过程中,应尽快降低床层温度、防止催化剂快速结焦。
装置停工阶段,对循环氢中的H2S浓度进行监测,一般要求不小于500?g/g,以防止催化剂还原。
03原料系统设置氮封
原料与空气接触,会发生氧化、生产胶质、沥青质,进入反应器后,这些胶质会沉积在催化剂床层上,增加床层压降,缩短装置运转周期。因此,原料油要采用氮封隔绝空气。
04监测控制新氢杂质含量,防止甲烷化反应
新氢作为补充氢进入反应系统,其杂质CO+CO2过高、一方面降低了新氢纯度,另一方面会在反应器内发生氢解脱氧(甲烷化)反应,放出大量反应热,将引起反应器床层温度波动,甚至会造成反应器床层超温。一般CO+CO2含量规定不得大于30mL/m3。
05监测控制原料水含量
水对催化剂的活性和强度都会造成影响,严重时影响催化剂寿命。水汽化会增加装置系统压力,引起压力波动。进反应器原料油中的含水量最大值为500 mg/kg,一般要求小于300 mg/kg。
06优化自动反冲洗过滤器运行
原料油中的各种杂质,会污染催化剂或使催化剂结垢、结焦,降低催化剂活性,造成床层压降升高,缩短运转周期。
通过自动反应洗过滤器的优化运行,可去除20?m的固体颗粒,完全去除掉原料油中的机械杂质和锈焊渣等杂质,同时过滤掉一部分大分子质量的胶质、沥青质及焦炭等物质进入反应器,保护催化剂,防止床层压降增大。
07焦化装置采用无硅消泡剂
为减少焦化塔顶泡沫层的高度,在焦化塔中需注入消泡剂。若消泡剂含硅,其焦化汽油会携带硅进入加氢装置,硅在加氢条件下生产易挥发的硅化物,在床层中迁移而穿透床层。催化剂上沉积3-5%SiO2时,就能封闭活性中心,使催化剂失活。因此,焦化装置应采用无硅消泡剂。
08加氢装置采用无磷阻垢剂
随着生产周期的延长,原料油/反应产物换热器管束内壁易生产一层结垢物,主要成分是稠环芳烃,难溶于水、油、酸、碱等溶液,影响长周期运行。为解决这个问题,通常在反应进料泵入口注入阻垢剂。若阻垢剂含磷化物,在加氢条件下会生产PH3引起催化剂中毒,使催化剂活性下降。因此,加氢类装置加阻垢剂应采用无磷阻垢剂。
免责声明:本网站所转载的文字、图片与视频资料版权归原创作者所有,如果涉及侵权,请第一时间联系本网删除。
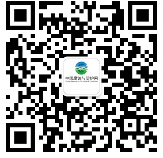
官方微信
《中国腐蚀与防护网电子期刊》征订启事
- 投稿联系:编辑部
- 电话:010-62313558-806
- 邮箱:fsfhzy666@163.com
- 中国腐蚀与防护网官方QQ群:140808414