换热设备利用率的高低直接影响到炼油工艺的效率以及成本的费用问题。由于换热器工作介质复杂且腐蚀性强,运行工况条件苛刻,出现的腐蚀泄漏问题极大的影响着装置的安全、平稳及长周期运行。
典型案例某炼厂稳定塔油气冷却器E309/B,管束型号BES1200-2.5-495-6/19-4II,该换热器壳程为减一中油,管程为循环水。换热器2014年大检修更换新换热器管束,运行至2015年2月底,新管束在仅投用三个月后即发生泄漏,换热器管束出现内漏,对检修期间更换的旧管束进行抽真空试压,堵管10根后管束回装,上水打压合格。该水冷器漏损发生在管程水侧,即管束内壁,并包括管板与循环水接触侧,失效形式为形成腐蚀坑及穿孔。
1 检测与分析
该水冷器的管束材质为20#钢,规格ф19×2mm光管;管板材质为16MnⅡ。管程介质循环水,温度(入口)32/(出口)40℃,压力0.4MPa;壳程介质减一线油,温度(入口)90/(出口)50℃,压力0.98MPa。
根据管束运行期间循环水采样分析结果来看,在此期间共采样137次,水样分析结果显示,部分水质数据较要求控制指标偏差较大,详见表1。
表1 管束运行期间循环水检测数据
项 目 |
要求控制指标 |
实测值 |
1、PH值 |
7~9.5 |
<7,最低6.5 |
2、总磷 |
12~15mg/L |
9.7~35mg/l |
3、浊度 |
≤35NTU |
138~220NTU |
4、浓缩倍数 |
≥3.5 |
2.6~3.5 |
5、石油类 |
<10mg/L- |
10~500mg/L |
6、余氯 |
0.1~1mg/L |
1~5.6mg |
01 宏观检测
从水冷器中不同部位取腐蚀并穿孔及未失效管样,并将管样纵向剖开,并对腐蚀穿孔管样进行了清洗。然后对管束内壁(水侧)及管板水侧的腐蚀状况拍照,可见管束内壁呈现溃疡状腐蚀,管板上也存在许多圆形腐蚀坑,其中有些大的腐蚀坑穿孔,见图1、图2。
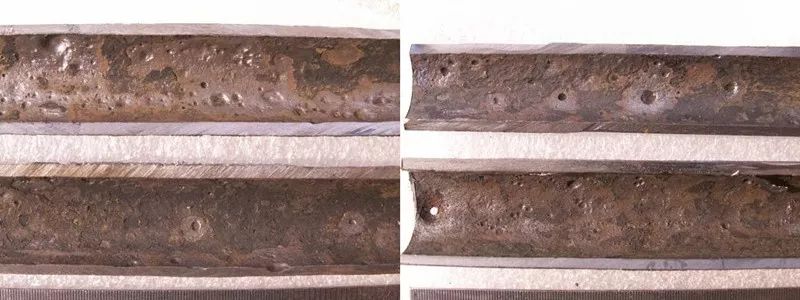
图1 换热管剖面腐蚀点坑及穿孔
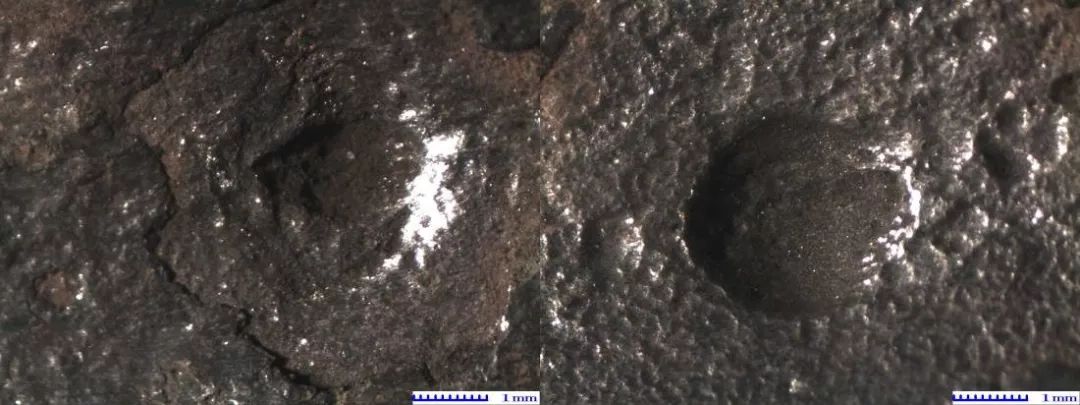
图2 腐蚀点坑放大图貌
02 金相组织分析
从泄漏管束及未失效管束取金相样品,在显微镜下观察分析。失效失效管束内壁形成圆弧形腐蚀坑,造成管壁严重减薄;由于管束受到过清洗,在腐蚀坑底未见明显的腐蚀产物附着;管壁金相组织为铁素体+珠光体,发生严重腐蚀的管束与未失效管束的金相组织完全相同。
03 扫描电镜分析
借助于扫描电镜,对右下第17排第5根管内壁点蚀坑进行形貌观察和能谱分析。观察可见,点蚀坑内附着有疏松状态的腐蚀产物;能谱分析确定,点蚀坑内的腐蚀产物主要由Fe、O元素组成,还有S、Cl、Si等,见图3
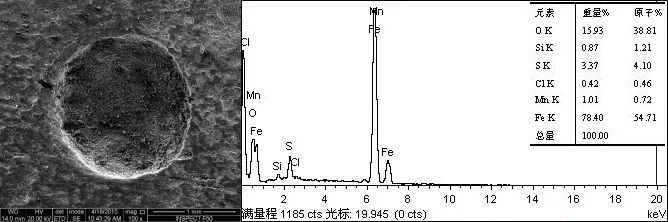
图3 腐蚀点坑能谱分析
2分析与讨论
通过前面对腐蚀失效管束的多项理化检验分析,金相检验未发现组织异常等现象。管束腐蚀破坏是从管束内壁发生并发展,以形成溃疡状腐蚀并穿孔的破坏形式。溃疡状腐蚀是氧腐蚀的典型形貌,因此初步判断管束的失效是由氧腐蚀造成的。
由于水冷器的管程通循环冷却水,因此管束的腐蚀破坏与循环冷却水有直接地关系。冷却水系统常采用敞开式循环水系统。该系统均经水质稳定处理。钢铁受水中溶解氧的腐蚀其实质是一种电化学腐蚀,即溶解在水中的氧会造成钢铁的腐蚀,形成铁锈。水中溶解氧浓度越大,钢铁的腐蚀速度越大。
其反应式为:
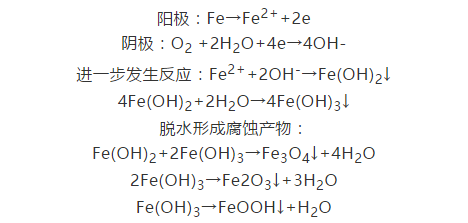
溶解氧腐蚀的特征是:在金属表面形成直径不等的鼓疱,直径一般为1~30mm,鼓疱表面颜色由黄褐色到砖红色不等,下面是黑色粉末状物,这些均是腐蚀产物,将这些腐蚀产物清除后,便会出现凹坑,这种腐蚀也称为溃疡腐蚀。
循环水系统在运行过程中,悬浮于冷却水中的污泥会牢固地附着在设备表面上,形成氧的浓差电池,使铁被溶解,引起垢下腐蚀,导致水冷器管束的腐蚀穿孔的可能性是存在的。其次,从送检方的描述中也证实管壁内部有一定结垢,由于使用时间较短,因此,垢层沉积并不严重。
水质监测显示总磷、浊度、总铁、石油类、余氯等均超要求控制指标。这些因素均会导致或促进垢下腐蚀的发生。总磷就是水中磷元素的总含量,磷含量过多会引起藻类植物的过度生长,水质富营养化,甚至造成水质污秽异臭,死亡的藻类将成为污泥。浊度表示水中悬浮微粒的含量,包括粘泥、腐蚀产物、杂质、微生物等。浊度高说明水中含有大量的悬浮微粒。总铁含量超标表明水中铁离子含量高,意味着水冷器管束腐蚀严重石油类含量严重超标说明系统漏油,油品进入到循环水中。油是微生物的营养源,有助于其生长和繁殖;另一方面油品又不断地消耗循环水系统内投加的用于抑制微生物生长的氧化性灭菌剂氯。由于漏油,循环水浊度急剧增加,水质变差,油品粘附力强,与系统中的悬浮微粒粘合在一起,在管壁、管板的死角处沉积,使投加的药剂作用得不到有效地发挥,而且形成大量的污泥,为细菌生存与繁殖创造条件,促进垢下腐蚀的发生。
3防治措施
在日常生产中,应从以下几方面加强管理,提高换热器管束生命周期:
01在生产操作方面要进一步改善循环水质量
加强腐蚀监控数据异常分析,充分利用循环水在线含油分析等在线监测系统,建立制度,定期查看分析,及时定位,及时预警处理。建立检漏、查漏相关管理制度并组织查漏,杜绝泄漏的油品加剧结垢和腐蚀,造成腐蚀加剧漏油的恶性循环。按照工艺卡片,循环水水质监测每天一次,指导加药、旁滤、排污换水。
02加强循环水流速管理
应定期对循环水流速进行检测,管程循环冷却水流速不宜小于0.9 m/s;壳程循环冷却水流速不宜小于0.3 m/s。水量小、流速低、结垢严重;水量大、流速高、腐蚀严重;工艺介质超温导致结垢;热负荷大换热面积不够;热负荷小导致浪费。
(1)采用便携式流速测定仪(多普勒超声波流量计)现场测循环水流速,调节并控制流速在合理的范围,调整流量不合理的用水装置和冷却器;定期检查阀门开度,控制冷换设备循环水阀门开度不宜小于全开的20%,防止流速过低,造成结垢腐蚀;分析腐蚀挂片器监测的碳钢、不锈钢、铜材质挂片腐蚀速率,根据循环水效果监测分析,进行水质控制效果评价,指导循环水流速控制。
(2)对各系统的给水、回水总量、进出压力、温度,对各用水装置的循环水进出总流量、温度、进出口压力,对各个冷却器循环水的流量、进出口温度、压力及介质进出口温度进行标定和优化。
(3)对用水量超200m?/h,管程流速超1.5m/s的单台冷换设备进行调整;将负荷较低、流速低于1m/s的冷却器由并联改为串联,例如催化重整有6台由并联改串联,催化有7台由并联改串联;对于循环水阀门开度过小,流速低于1m/s的冷却器,督促车间开大阀门,提高流速;经过优化调整, 系统共减少循环水量1500 m?/h,循环水系统达到了合理、节约用水的目的,同时解决了部分冷却器腐蚀结垢问题。
03更换管束
对于使用超过两周期的管束,应按照介质种类、检修腐蚀检查情况,有计划的逐步更换。
免责声明:本网站所转载的文字、图片与视频资料版权归原创作者所有,如果涉及侵权,请第一时间联系本网删除。
相关文章
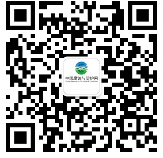
官方微信
《中国腐蚀与防护网电子期刊》征订启事
- 投稿联系:编辑部
- 电话:010-62313558-806
- 邮箱:fsfhzy666@163.com
- 中国腐蚀与防护网官方QQ群:140808414
点击排行
PPT新闻
“海洋金属”——钛合金在舰船的
点击数:5768
腐蚀与“海上丝绸之路”
点击数:4763