YWH轮是2011年6月由中远南通川崎造船厂建造的好望角型船舶,配备的是国内厂家生产的燃油和废气组合型锅炉。
锅炉参数
型号:MISSION OC 建造年份:2010
最大工作压力:8.0 bar 蒸发量:1300kg/h(废气侧) 1500 kg/h(燃油侧)
该锅炉原理如图1所示。该锅炉为立式烟管锅炉,废气侧(废气炉)和燃油侧(辅锅炉)共用一个立式筒体作为水腔,燃烧室也设计成立式的。该型号锅炉为全焊接型,辅锅炉侧的主要换热件由针型管件组成,这种针型管由大口径的管子里面装有带针型肋片管组成,针型管上下开口用于水的进入和蒸汽的排出。里面的针型肋片主要是增加传热面和扰流,以获得最大热效率。废气炉侧主要换热件为中低压锅炉炉管。在组合锅炉的燃油侧和废气侧都设计有人孔和手孔,可以方便检修;锅炉废气侧的烟管采用中低压无缝锅炉管,没有进行额外的机加工,烟管垂直布置,管子两端经过胀管后在烟面焊接在上下管板中。
1、问题发现:该轮于2013年8月份对锅炉进行烟腔进行水洗的过程中发现有两根炉管发生了漏泄,这一现象引起了公司和船舶的高度重视,是单根炉管出现问题还是所有管子均存在腐蚀现象?为此我找到了锅炉厂的售后服务部门上船进行检验,售后服务部门上船对炉水水质进行检查并打开炉腔检查后,得出的结论是锅炉内部发生了氧腐蚀并给出了分析报告如下:
1.1炉管整体长度为2.23米,水管表面中部发现轻微水垢,根部结垢较严重,根部表面以及下管板表面发现腐蚀凹坑,而管子其他部位只是轻微的一层浮锈。
1.2蒸汽侧表面锈蚀较严重。见图2照片
水垢大多是指水中碳酸盐、硫酸盐成份,由于给水的硬度较高或炉内处理不当形成。对船龄较小的船舶来说,可能由于在造船时锅炉制造厂未能对炉腔进行系统的清洁、煮炉,或在厂期间未对炉水按照说明书规定化验投药进行化学品处理,都会导致水腔的结垢和腐蚀。水垢会降低锅炉热效率,增加耗油量,降低受热面金属强度,使钢板过热,变形,甚至爆裂事故。
1.3氧腐蚀的原因是由于水中溶解氧和铁进行反应生成氧化铁。氧腐蚀的特征为局部腐蚀,主要表现为局部的坑点或溃疡状腐蚀,腐蚀部位上覆盖有腐蚀产物。氧腐蚀会造成锅炉水管腐蚀穿孔而泄漏,严重时甚至可能因腐蚀而报废。
1.4. 对于蒸汽面锈蚀问题,可使用化学添加剂来减缓和防止。
厂家专业人员提请船舶注意提高热水井的给水温度,勤投药、勤化验炉水并及时上下排污以防止腐蚀继续恶化对于锅炉已经存在的水垢,可以在适当的时候停炉清洗,如果不能用物理方法如高压水、人工刮拭等方法,可以使用化学品酸洗来进行除垢。
出厂两年多的新锅炉出现严重腐蚀穿孔现象,作为船公司来讲是难以接受的,一定要找到锅炉失效的最根本的原因。船东的意见是:如果是设备生产质量问题,可以提请设备制造厂注意改善制造工艺和生产质量;如果是船员日常维护管理问题,船公司要对船员进行技能和责任心的培训,以避免再次出现类似的问题。笔者多方咨询和查阅专业资料,以求找到锅炉腐蚀的真正原因。
2、锅炉腐蚀的常见原因
船用锅炉腐蚀的常见类型分为氧腐蚀、酸腐蚀、炉内碱腐蚀、缝隙腐蚀等。
2.1氧腐蚀:
判断锅炉是否发生了氧腐蚀的依据是锅炉水腔内的腐蚀凹坑,类似溃疡状或者小孔状局部腐蚀,其腐蚀产物表面颜色为黄褐色、黑色、砖红色不等,次层是黑色粉末,对金属强度破坏严重,腐蚀产物一般覆盖在金属表面,而腐蚀产物下的腐蚀仍然在继续,当腐蚀产物脱落后,腐蚀表面呈不规则形状,并出现深浅不一的凹坑。锅炉水侧氧腐蚀的特征:钢铁表面形成许多小型鼓泡,其直径1-30mm不等;鼓泡是钢铁腐蚀的产物,其表面的颜色由黄褐色到砖红色不等,但就整个腐蚀产物大致可分为三层。其中,最外层是三价铁的水合氧化物,成分为Fe2O3·nH20,最内层为二价铁的水合氧化物,呈黑色,即FeO•nH2O。中间层为粉末状的黑褐色水合氧化物,成为Fe304·nH2O,也可看成FeO和Fe2O3结合产物;所有铁腐蚀的产物结构都比较疏松。且氧和铁的结合量自外层到内层逐渐减少,当腐蚀产物除掉之后,便会出现因腐蚀而造成的蚀坑。坑底钢铁为阳极,在电化学的过程中,坑底底部的钢铁放出电子,并由钢铁本身传递到蚀坑上部周围处(阴极),在阴极处的水中溶解氧获得电子后起阴极还原反应,但阴极处钢铁不受腐蚀。此时水中的阴离子(例:C1-、OH-)向坑底迁移,而二价铁的亚铁离子则向上迁移,为此连续不断地构成电流回路、腐蚀不止,造成腐蚀坑向纵深发展,直至穿孔,虽然由氧腐蚀损耗的钢铁总量不大,但由于集中于局部,特别是大面积的溃疡腐蚀,对锅炉的强度危害很大,以致使锅炉报废,或更换受热面管子。锅炉水腔中的水温分布情况是从下往上是递增的,靠近下管板处的水温较低,所含的氧气浓度会稍高一些,这一区域的腐蚀也会更严重一些,这些由于氧腐蚀形成的凹坑严重发展就会造成管壁的穿孔以及下管板的严重腐蚀,如果穿孔的炉管数量较多,达到15%以上时,因为封堵炉管造成了主机废气通道有效面积的缩小,会造成主机透平效率下降、喘振等进而造成主机整机排烟温度升高,烧损排气阀和主机活塞头、扫气箱着火等一系列严重后果,甚至造成船舶停航修理而发生很高的修理费用以及严重的营运直接和间接损失。
补给水中所含的氧气是造成氧腐蚀的主要原因。锅炉给水中的溶解氧基本上是饱和的,如果给水除氧不力,在中性或碱性介质中,势必发生氧腐蚀,氧腐蚀会造成锅炉炉管和管板的严重损坏。
2.2 酸腐蚀:当炉水中氯化镁MgCl2含量较高时,在高温的作用下,会发生水解反应而生成盐酸。盐酸是一种强酸,它能破坏金属表面的氧化膜,又能腐蚀钢铁。在炉水pH值较低的情况下,腐蚀产物(铁的氯化物)又可能与氢氧化镁Mg(OH)2作用而生成新的氯化镁。新生成的氯化镁在适宜的条件下则又可能水解成盐酸,如此周而复始,使钢铁不断遭到酸腐蚀而被损坏。炉内酸腐蚀特点:锅炉内酸腐蚀多发生在水冷壁管上,其特征是:在水冷壁管皿状蚀坑上,有较硬的Fe304突起物,呈现层状结构,在附着物和金属交接处有明显的蚀坑,腐蚀部位金相组织发生变化,有明显的脱碳现象。
2.3 炉内碱腐蚀:在正常情况下,炉水PH值一般在9~11之间,此时炉管金属表面的氧化膜是稳定的,不会发生碱腐蚀。
发生碱腐蚀的原因,是由于在炉管的局部地方发生了碱的浓缩。例如:由于水循环不良或在一些水平或倾斜度不够的炉管内,发生“汽水分层”现象时,使附在管壁的液膜浓缩。该部位的游离NaOH达到危险浓度,从而产生碱腐蚀。另外,在有沉积物的地方,其沉积物下炉水滞流,也可能使NaOH浓缩到危险的浓度。碱腐蚀形成机理:在高温高压的条件下,炉水中游离苛性钠溶解了钢铁金属表面的氧化保护膜(主要成分为Fe3O4),使其生成可溶性的亚铁酸盐,使铁金属遭碱腐蚀而破坏:Fe304+4Na0H→2NaFe202+Na2Fe02+H20;炉内发生碱腐蚀的特征是:炉内碱腐蚀多发生在锅炉水冷壁管的向火侧,热负荷较高或水循环不良的部位和倾斜管上;多孔沉积物下,和管壁与焊接的细小间隙处。碱腐蚀一般具有局部性的特征:腐蚀部位呈小沟槽或不规则的溃疡型,上附有腐蚀产物。腐蚀部位金属的机械性能和金相组织一般没有变化,金属仍保留它的延性。
2.4 缝隙腐蚀:缝隙也是氧腐蚀的一种形式。它是由于狭缝或间隙的存在,在狭缝内或近旁发生的腐蚀。发生缝隙腐蚀的缝隙必须宽到腐蚀溶液能够进入,但又必须窄到能维持溶液静滞。缝隙腐蚀通常发生在金属表面与垫片、垫圈、衬板、表面沉积物等接触的地方以及搭接缝、金属重叠处等地方。一般认为缝隙腐蚀是由于缝内外氧浓差引起的,由于缝隙内部贫氧,氧的还原反应主要在缝隙外部的金属表面上进行,缝隙内部金属溶解产生了过多的正离子(Fe2+),为了维持电解质平衡,Cl-等有害离子从外部迁入缝内,结果使缝内的金属氯化物浓度增加,金属氯化物水解产生游离酸(H+Cl-),从而加速了金属的溶解速率,形成一个自催化过程。由于炉水中Cl-含量较高,使Cl-诱发氧浓度差腐蚀,氧腐蚀点为阳极,周围金属成为阴极,这样只要有氧存在,腐蚀就不断进行下去,腐蚀产物下炉管就会越腐蚀越深直至穿孔。缝隙腐蚀常常伴有一个很长的孕育期,然而一旦开始,就不断以增加的速度发展;造成缝隙腐蚀还有一种物理现象,既炉管与下管板之间存在缝隙,在锅炉的运行过程中,缝隙中逐渐被炉水处理后的污泥或水垢填充,由于填充物是热的不良导体,炉管吸收的废气热量不能很好的传导到管板上,造成局部金属温度过高,钢材的强度会随着温度的升高而降低,由于水垢的存在会导致缝隙处金属温度升高很多,长时间运行会造成该部位金属的结构发生变化,更容易发生损害和腐蚀,一旦发生腐蚀速度会非常快,图3是辅助锅炉水管壁结垢或有油膜覆盖时的状况,废气炉可做参考。
结论:油膜厚度仅为0.5mm的炉壁的最高温度可从256摄氏度上升至633摄氏度。此外,热传递可从137 kW/m2降至82.3 kW/m2,降幅可达40%。
3、真实原因查找
锅炉内部的腐蚀是多种类型腐蚀共同起作用,某一种腐蚀占了主导地位,但是上述的锅炉到底是哪一种腐蚀占据主导地位呢?是否还有其他未被发现的制造工艺方面的潜在因素?我司新造船舶配置的是相同型号的锅炉,利用试航的机会对上述疑问进行验证。锅炉生产厂家给出的结论是氧腐蚀造成锅炉炉管与下部管板锈蚀,但我司有多条船舶安装有同类型的锅炉,船员对锅炉的管理水平相当,未在如此短的时间发生类似问题。
我们查阅大量资料和锅炉厂家的设计建造规范,我们作为船东代表进厂检查在建船的锅炉水腔内部,以确认制造厂的制作工艺是否存在问题,是否在炉管和下管板之间存在缝隙造成锅炉水腔炉管根部腐蚀。检查中发现部分炉管与管板间隙较大,现场用塞尺测量,炉管与上下管板间隙为0.4mm左右(如图3所示)。查阅锅炉厂家建造规范,发现设计和建造规范上要求炉管与管板的间隙最大为0.1mm。 我们分析:炉管与下管板的间隙较大,锅炉制造厂在建造完毕后煮炉、钝化处理以及在船东使用过程中所投药的药液、水垢就会沉积在缝隙中,发生短路原电池反应,在缝隙中发生强烈的腐蚀,也就是业界所称的缝隙腐蚀。虽然上管板与炉管间隙与下部类似,但下管板与炉管结合处处于蒸汽空间,药液、水垢等不易进入,因而腐蚀较轻;双方都认为这是造成锅炉发生腐蚀的因素之一;解决的方案是锅炉厂专业人员重新对间隙较大的炉管进行了胀管操作,消除这些间隙;发生腐蚀的YWH轮锅炉由锅炉厂进行无损检测,投药除去铁锈和水垢并在适当时机更换腐蚀严重的锅炉管。
其他可能的原因:
锅炉出厂时直接在水腔内加入了防锈粉末,防锈粉末是一种白色物质,在锅炉内挥发后产生含气态氨,如有水分存在将溶解在水中形成弱碱性的氨水,能阻止锈蚀产生,但是船厂人员不懂得煮炉和钝化的程序,锅炉厂也不提供化学品和技术支持,在首次运行时,只是投药和加水,因此交给船东时存在先天不足现象。
船东接过船舶时并没有检查锅炉水腔内部状况便直接使用,如果水腔内存在垃圾、污泥等物质覆盖在下管板和炉管根部区域,这些物质将阻碍热的传导,使管板和根部炉管温度升高,金属晶体发生变化,更容易造成管板和炉管根部的腐蚀,一旦发生腐蚀,腐蚀产物覆盖在金属表面就会形成垢下腐蚀,如果不及时清除这些锈蚀产物,垢下腐蚀就不会停止,直到将金属腐蚀穿透为止,所以锅炉水腔要每半年打开一次检查状况,发现有锈包一定要清除干净,露出金属为止,这样在药液的作用下,腐蚀才会停止,为此需要根据投药量定期进行上、下排污操作,排掉下部的污泥和上部的浮渣,浮渣浓度太大也会覆盖并粘帖在管子上部,影响管子的传热容易形成腐蚀。
综上所述,该轮锅炉水腔的腐蚀可以说是多种因素共同作用导致严重腐蚀,需要引起重视,下面就从各方面来探讨如何防止出现这种现象。
4、维护管理的注意事项
这件事的成功解决,作为机务管理人员深有感触:总结经验、加强正规管理是保证设备正常运转的前提,设备从交给船厂开始阶段和船员的日常管理都非常重要,该轮锅炉的腐蚀损伤可以说是设备厂家和船员都有一定的责任,出厂时就存在一定的不满足规范的缺陷,在日常的维护中,船员在排污操作上也有一定的过失,致使锅炉下管板有铁锈和垃圾(处理后的污泥)沉积,但是前后时间段比较长,无法查到具体责任人,以后要对船员加大培训力度,避免其他船舶出现类似的现象,因此船用锅炉要维持长时间的无故障运转,需注意以下几点。
4.1严把出厂关:确保锅炉的制造工艺要达标。锅炉在设计制造过程中,选用材质不合理,工艺粗糙,缝隙太大,煮炉、钝化处理之前没有对炉膛内部彻底清洁,造成炉膛内部有腐蚀源等都会造成锅炉在使用过程中产生异常腐蚀;因此公司在决定造船谈建造规格书时就要开始把关,选用有信誉的厂家,厂家的制造规范供公司机务人员学习和掌握,锅炉从制造厂出厂到达船厂装船开始,需要监造组人员进行把关,严格按照干保养的标准保养锅炉,初次运行时要先进行煮炉和钝化。
4.1.1煮炉煮炉是为了清除新锅炉内的保护性油脂和可能存在的油污,煮炉的步骤如下(以德鲁公司的LAC碱性清洁剂和LIQUID COAGULANT杂质凝结剂为例):
Ø 尽可能人工清除锅炉内部油污
Ø 确保无清洁工具遗留在锅炉内
Ø 按照锅炉系统水容量及投药比例,计算所需LAC和LIQUID COAGULANT数量
Ø 加炉水并同时添加2/3数量的LAC 和LIQUID COAGULANT(剩余的1/3将在每次排污后添加)
Ø 加炉水到正常水位
Ø 缓慢提升压力到7公斤
Ø 在压力达到7公斤时,每2小时进行下排污一次,排除悬渣,每4小时上排污一次,排除固体杂质颗粒。
Ø 整个煮炉过程需要12小时。即下排污6次,上排污3次。剩余的化学品9等分。
Ø 每次排污后,加炉水,同时提升压力到7公斤。
Ø 煮炉12小时后,让锅炉自然冷却
Ø 当温度降到65度时,排净炉水
4.1.2钝化钝化的目的是在水侧表面形成一层惰性保护膜,以阻止炉水中的有害性成分同更深层的金属发生反应,起到保护锅炉的作用,保护膜的形成可以通过不同的方法获得。德鲁公司的AMERZINE的用量为1.3升兑每顿炉水,程序如下:
Ø 加炉水到最高安全水位
Ø 隔离蒸汽管路
Ø 从汽鼓加入AMERZINE,或通过专门添加处理剂的旁通罐加入。
Ø 锅炉点火到正常工作压力的一半。
Ø 间歇性点火保持此状态8-12小时
Ø 通过排污,使炉水降到正常水位,钝化完成。此时的锅炉可以添加处理剂并投入正常运行。
4.2 盯住管理关:
机关管理人员和船员需从以下几点做好管理
l 降低给水氧含量降低氧腐蚀
保持热水井的高温度:船用锅炉结构设计较简单,没有专门的除氧设施,而且大多都是敞开式的给水柜(热水井),很容易混入氧气,为此锅炉说明书中要求保持热水井85-90°C,这样可以保持给水中较低的氧含量,见图5所示。
但是由于热水井本身没有保温设施,冬季、夏季机舱内温度变化很大,冬季时很难保持高温,由于外界温度低回水温度即使不冷却也达不到85度,而且仅靠减少回水冷却器(condenser—康定生)冷却海水的流量来调节回水温度会导致康定生热交换管海水侧严重结垢,严重时管路堵塞清通非常困难;为此部分厂家设计了热水井的自动加温装置,利用蒸汽喷射入热水井保持高温除氧的有效性。见图6所示
l 给水中添加除氧剂的方法除氧。锅炉给水的除氧剂常用的有亚硫酸钠(Na2SO3)、联氨(N2H4)等。Unitor的产品中Liquitreat是一种常用的炉水处理剂,Liquitreat 中除氧剂主要成份为亚硫酸钠,该成份为传统除氧剂,能快速和氧发生反应生成硫酸钠从而达到除氧目的,但是为了保证浓度需要经常添加。该除氧成份没有钝化功能,不能挥发到蒸汽管路中从而形成保护,硫酸钠会增加电导率,所以要求船员必须严格按照排污程序每天进行锅炉排污从而减少水垢和腐蚀的产生。
l 锅炉的给水盐度、硬度控制:给水盐度需小于5ppm,从源头上减少水的硬度和结垢的风险。可以通过投药来进行,需要注意的是尽管化学品可以疏松钙镁盐类,减少水垢在水管表面的形成但是水中的钙镁盐类并没有消失,我们还是需要通过排污的方式来去除钙镁盐类。对炉水盐度含量要求越低越好以此来减少腐蚀,保证蒸汽品质。所以要求一定做好日常的排污和给水水质控制。最好使用船上造水机造的水。(一般盐度为2 ppm)。
l 对炉水的碱度控制。要求控制酚酞碱度150-300 ppm ,PH 值要求9.5-11.5. 在此碱性条件下,能很好的防止酸性腐蚀对锅炉的影响。
l 冷凝水质量的控制。为了对蒸汽侧和冷凝管路也能得到保护而不受腐蚀,我们要求冷水的PH 值呈弱碱性,PH值要求控制在8.3-9.2之间。这个我们可以通过化学品的投放得以实现。
l 运行检查 锅炉每运行半年需要打开水腔进行检查是否有水垢沉积或者管路和管板的腐蚀现象,如果发现管路或者管板出现锈蚀现象,应该立即汇报公司请求岸基支持,包括酸洗锅炉,以便及时除去腐蚀产物,使腐蚀停止;每个长航次对烟腔进行水洗并目视检查,确保锅炉效率和确认烟侧是否有腐蚀现象,
l 炉水中直接添加化学品:对于低压锅炉化学品厂家推荐综合性防腐处理剂以方便船员进行管理。推荐的Autotreat 和Oxygen Scavenger Plus, Autotreat 中含有DEA(二乙醇胺),该成份能挥发到蒸汽管路中形成弱碱性的氨水从而保护整个冷凝和给水系统;Oxygen Scavenger Plus 成份为二乙基羟胺,该化学品不会增加炉水电导率,挥发性强,可以随蒸汽进入冷凝系统从而对整齐冷凝系统有一个全面除氧保护,该品毒性极低且能和氧气快速反应。但是这两种药剂需要通过投药泵直接添加到炉水中,一般是通过专用投药泵从锅炉给水管路上添加,才能保证药剂的连续性和有效性,这种药剂投到热水井中没有效果。
l 停用保养 锅炉停用时,如果防护措施不当,大气可能侵入锅炉内而造成腐蚀。锅炉停用时发生的氧腐蚀,通常是整个水汽系统中,特别容易发生在积水不易放干的部分,这与锅炉运行时发生的氧腐蚀常常局限在某一部位是不同的,锅炉短期停用时按照要求使用湿保养方法;长期停用时要使用干保养,彻底除去锅炉内水分,并添加防锈粉末防止腐蚀发生。
5、结论
综上所述,设备的维护要从源头上把关,而且后天的保养也是不容忽视的,无论是在设备制造和日常管理中,注意每个细节,设备厂家严格按照施工规范施工,使用者严格按照设备厂和化学品厂产品说明书的要求进行维护和保养,给设备一个良好的运行环境,以充分延长设备的无故障运行期,这是每一个机务人员的最高期望。
参考文献
1、张玉忠等编. 低压锅炉运行中的氧腐蚀及新型除氧剂的应用 第24卷第10期
2、刘升泉周金宝 中国井矿盐第32卷第3期
3、杨坤黑龙江科技信息 2011年第11期
4、张栓成张兆杰《锅炉水处理技术》第2版
免责声明:本网站所转载的文字、图片与视频资料版权归原创作者所有,如果涉及侵权,请第一时间联系本网删除。
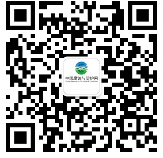
官方微信
《中国腐蚀与防护网电子期刊》征订启事
- 投稿联系:编辑部
- 电话:010-62313558-806
- 邮箱:fsfhzy666@163.com
- 中国腐蚀与防护网官方QQ群:140808414