油气混输管道作为油气开采现场常见的管道输送方式,具有简单高效的特点,但受混相流体的影响,流体介质对管道内壁的腐蚀更为严重。探讨了混输管道内CO2和H2S对管道内壁的腐蚀机理,提出了相应的腐蚀防护措施,为油气管道管理工作提供借鉴。
混输油气流体包含组分较多,气相主要为烃类气体、CO2、H2S、O2、N2 等,液相主要为地层水、地表注入水、原油,固相主要为地层采出的泥沙。复杂的多相流介质对油气管道腐蚀更加严峻,一旦产生管道腐蚀造成的风险事故,将会造成严重的经济损失和环境灾害。CO2、H2S 作为原油中通常含有的两种气体,与管道内地层水产生一定的化学反应,形成具有强烈腐蚀性的介质,因此这两种气体成为了引起管道内壁腐蚀的重要因素。
1 CO2 腐蚀
一般情况下CO2只有在溶于水后产生一系列的电解反应,生成酸性电解质引起金属管道全面腐蚀及局部腐蚀。总酸度的提高,使得金属管材整体腐蚀更加严重。
01 CO2 腐蚀机理
单纯的CO2不具有腐蚀性,但溶于溶解质后对金属管道产生电化学腐蚀,一般产生全面腐蚀及局部腐蚀的情况,根据电化学反应温度的差别,分为三种情况:
1)低温时金属管道碳钢产生酸性反应溶解,仅有少量情况FeCO3 腐蚀产物生成。该类情况下一般仅在管道内壁发生全面腐蚀。
2)较高温度时在管道内壁产生FeCO3 腐蚀产物,并在管道内壁形成分布不均匀的产物薄膜。此时将产生局部腐蚀的情况。
3)在管道内流体温度较高时,由于高温促使了电化学反应的产生速率,使得腐蚀产物大量生成,形成的产物薄膜附着在管道内壁。
产生的腐蚀反应见式(1):
CO2+H2O+Fe → FeCO3+H2
(1)通过以往的室内管道钢材管片研究表明,CO2 的腐蚀影响一般都是通过局部腐蚀产生。
02 CO2 腐蚀影响因素
经研究表明,CO2对管道内壁腐蚀的影响因素主要为以下几个方面:
1)CO2 在管道内流体介质中组分分压。根据SY/T0515-1997 标准,当CO2分压大于0.1MPa 时,管道内壁将会产生严重腐蚀,而分压小于0.05MPa 时产生的腐蚀影响几乎不用考虑,总体而言管道内壁腐蚀速率与CO2 分压有着正相关性。
2)管道内流体介质温度对腐蚀反应速率的影响。同时受反应速率影响的关系,导致管道内壁附着的反应物产生的速率也大不相同。研究表明,温度对CO2在管道内壁腐蚀呈现出两段式影响,在温度小于130℃之前时,温度与腐蚀影响成正相关,当温度大于130℃时,随着温度的增加,CO2 对管道内壁腐蚀效果逐渐降
图1 温度对CO2 在管道内壁腐蚀速率的影响
3)管道内流体流速的影响。当流体流速较高时,将产生冲刷作用,使得已生成的腐蚀反应产物薄膜损坏,造成管道内壁重新裸露,重复产生电化学腐蚀作用,加大了腐蚀作用的影响。
4)Cl-离子浓度的影响。地层水中常常含有大量的氯离子,吸附在腐蚀反应产生的产物薄膜表明时,破坏了产物膜造成开裂,加大了反应速率。
03 CO2 腐蚀防护
采用含铬钢具有较好的抗CO2 腐蚀的特性,同时添加咪唑琳、多胺类等缓蚀剂,在管道内壁涂抹环氧型、改性环氧型、酚醛环氧型抗腐蚀涂层。
2 H2S 腐蚀
01 H2S 腐蚀机理
H2S 作为易溶于水的气体,溶于管道内地层水后产生电化学腐蚀和应力腐蚀。H2S 在溶液内产生的电解反应见式(2):
H2S → HS-+H+HS- → H++S2-
(2)电解出的H+ 离子使得碳钢中Fe 发生电化学反应,阳极反应及反应产物见式(3)、(4)。
Fe-2e → Fe2+ (3)
Fe2++S2- → FeS (4)
应力腐蚀又见氢脆作用,反应生成的氢原子大量结合产生氢气,在管道内壁缺陷处富集后产生脆化,使得管道内壁产生裂纹。
图2 硫化氢壁腐蚀机理
02 H2S 腐蚀影响因素
以往研究表明,反应温度、H2S 分压、流体pH 值、管道内流体流速、管道自杀材质等,都会影响H2S 腐蚀速率。
免责声明:本网站所转载的文字、图片与视频资料版权归原创作者所有,如果涉及侵权,请第一时间联系本网删除。
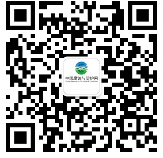
官方微信
《中国腐蚀与防护网电子期刊》征订启事
- 投稿联系:编辑部
- 电话:010-62313558-806
- 邮箱:fsfhzy666@163.com
- 中国腐蚀与防护网官方QQ群:140808414