镁锂合金是迄今为止密度最小的合金材料。由金属镁和金属锂为主要元素而制得的镁锂合金密度很小,一般为1.35~1.65g/cm3,是所有金属结构材料中最轻的,它比普通镁合金轻1/4~1/3,比铝合金轻1/3~1/2,所以镁锂合金也称为超轻合金。镁锂合金具有很高的比强度、比刚度和优良的抗振性能及抗高能粒子穿透能力,而且镁锂合金的密度远远小于新型航空用材铝锂合金的密度,是航天、航空、兵器工业、核工业、汽车、3C产业、医疗器械等领域最理想并有巨大的发展潜力的结构材料之一。随着世界范围内能源短缺,很多工业领域对轻量化材料和器件的需求极为迫切。镁合金材料以质轻、原料丰富和综合性能优良而被誉为21世纪最具发展潜力的绿色工程材料,而镁锂合金作为世界上最轻的合金,其优良的加工变形能力和低的密度在国民经济很多领域将会发挥其更大的作用,尤其是在航空航天和电子等工业领域更加受到人们的青睐。
典型镁锂合金组成
镁锂合金中的主要合金元素
二元镁锂合金力学性能很差,不能作为结构材料应用于工业领域。在镁锂合金中加入适量的合金元素,可以明显提高合金的各项性能,以求获得高性能的应用合金。在镁锂合金中的合金元素主要有三类:
①固溶度较大的元素,如Ag、Cd、Zn、Al、In、Tl等,其中研究较多的是Al、Zn、Cd、Ag
②固溶度较小的元素,如Ni、Co、Cu、Ca、Sr、Ba、Ce、Si、Ge、Sn、Pb、Sb、Bi等
③固溶度很小的元素,如K、Be、B、Cr、Mo、W、V、Ti、Zr、Th、Fe、Mn等
第一类元素的强化效果较好,但合金的组织性能稳定性较差,在室温或稍高于室温时易产生过时效现象;第三类元素的强化效果较差,但组织及性能稳定性好。到目前为止,研究较多的是第一类元素。
合金元素对镁锂合金的影响
1铝元素的影响
金属铝是镁锂合金中最主要的合金元素之一。镁合金中加入铝可以有效地降低液相线的温度,单位质量的原子数多,强化效果好,铝在镁中的固溶度大,在共晶温度437℃时的最大固溶度为12.5%,且随温度降低固溶度变化明显,可进行固溶强化。
α+β双相及β相单相Mg-Li-Al合金强化主要采用弥散强化和固溶强化。现有研究表明,随着铝含量的增加,Mg-Li合金的力学性能逐渐提高,当铝含量大于5%~6%后,再增加铝含量,合金强度提高并不明显,而延伸率却明显下降,所以在Mg-Li-Al系合金中,铝含量一般低于5%~6%。
在Mg-Li-Al系合金中,起强化作用的相主要是Mg17Al12、MgLi2Al等金属间化合物,而锂含量高的合金易发生过时效,亚稳相MgLi2Al易转变为AlLi,导致性能下降。实验表明,LA141A在室温下也会发生相的分解,此合金稳定性很差,LA141A在高于室温时,强度会降低,在90~150℃时的最终强度同室温相比大约降低50%。有研究表明,高锂合金时效存在这样一个过程β→MgLi2Al→AlLi。
当镁锂合金中锂含量不同时,铝对合金的影响也不一样,当铝含量达到3%以上时,铝除了固溶于合金基体内,还将出现AlI,i相。随着铝含量的增加,镁锂合金的外缩孔减少,而对于合金的内缩孔,锂含量在8%~20%的镁锂合金随着铝含量的增加其内缩孔减少,锂含量在1%~5%时,铝含量对于合金的内缩孔量无影响。对于锂含量小于14%的镁锂合金,铝含量越高,合金的气孔量越多,对于锂含量大于16%的镁锂合金,铝的添加有利于减少合金的气孔。
2锌元素的影响
金属锌对镁锂合金的强化有一定的影响。锌的熔点(419.58℃)较低,与镁的晶体结构(hcp)相同,与镁原子半径相差不大,可与镁形成连续固溶体。锌在镁中有较大固溶度(约为6.2%),随温度降低,固溶度减小,而产生时效强化。锌对镁锂合金的塑性损害不大,时效强化效果明显,但锌的加入使合金密度增大,为保持镁锂合金的低密度,锌的含量不宜过大。另外,锌能提高合金的应力腐蚀敏感性,从而提高合金的疲劳极限。
锌具有与铝类似的作用,即随着锌的增加,合金的强度提高而塑性下降,不同的是单位质量的强化效果比铝要差,若要达到相同的强化效果则需加大锌的含量,这样会使合金的密度变大。Mg-Li-Zn合金中生成q‘相(MgLi2Zn),经时效处理后q’相发生粗化并转变为稳定的q相(MgLiZn),这种转化过程与铝在镁锂合金中的变化规律相同。
由于锂含量及锌含量的差异,镁锂合金中第二相析出行为不同,导致其时效硬化行为的差异,图1为不同成分Mg-Li-Zn合金的时效硬化行为曲线。由图可知,当合金中锂含量较小时,合金由α相组成,时效时在基体α相中析出稳定相q(MgLiZn)而产生硬化;当合金为α+β双相组织时,α晶粒基本无时效硬化效应,β晶粒出现时效硬化和过时效软化现象;β相单相合金同样也会发生时效硬化和过时效软化现象,过时效软化是由q‘相转化为q相,在β相中析出造成的。
在镁锂合金的合金化过程中,一般把铝和锌同时作为合金化元素加入,这样即可充分发挥铝和锌各自的优势。
图1 不同成分Mg-Li-Zn合金的时效硬化行为曲线
3硅元素的影响
硅是提高镁锂合金的高温强度和蠕变性能的主要元素,加入硅元素后,合金组织中出现高熔点的Mg2Si相,这种相的熔点较高(1085℃),硬度较高(460HV),是提高镁锂合金耐热性能的主要因素。硅在锂液中的溶解度很小,其固溶度更小,硅在镁锂合金中的固溶度很小,主要以化合物的形式存在。美国研制了Mg-14Li-(0.5~1)Si和Mg-14Li-3Ag-5Zn-2Si耐热合金,并将该合金用于航天器铸件,合金的σb为131~138MPa,σs为104MPa,δ为10%。
4银元素的影响
金属银是抑制镁锂合金过时效的少数元素之一。银在镁中有一定固溶度,随温度降低固溶度减小,并析出γ-AgMg相;锂在银中的固溶度很小,但银在锂中有较大固溶度,随温度的降低而减小,并析出AgLi相。银含量小于10%时,合金的强度随银含量的增加呈线性增加,但增加幅度较小;合金的塑性随银含量增加而下降,但下降幅度不大。同时,含银合金的组织及性能的稳定性好,时效强化相是两个平衡相MgAg-AgLi固溶体,不是亚稳相,故稳定性较好。
无论在镁还是在锂中,银均有较大的固溶度,因此,银在镁锂合金中的强化作用主要是固溶强化效果,表1列出了不同银含量下Mg-12Li合金的力学性能。由表可以看出,当银含量小于10%时,合金的强度随银含量的增加呈线性增加,但增加幅度较小,只有当银含量大于10%时,合金的强度才会随着银含量的增加有较大幅度的提高,但单位质量的强化效果与铝和锌相比较小;镁锂合金的塑性随着银含量的增加有所下降,但下降幅度不大,即使10%的添加量时,其塑性也仍处于较高的水平(δ=38%)。此外银还具有显著改善Al、Zn、Cd强化Mg-Li合金组织及性能稳定性的作用,如在镁锂合金中添加1%银时可显著避免或推迟Mg-12Li-7.5Zn及Mg-12Li-18Cd的过时效产生。其不足之处是,银的密度较大,单位质量的强化效果较小,银的价格高也会使成本较高,因此,银一般只作为改善Mg-Li基三元合金组织及性能稳定性的用途添加到合金中。
表1 银含量对Mg-12Li合金力学性能的影响
5锆元素的影响
金属锆是很多合金的晶粒细化剂,而锆对镁锂合金也有极为显著的细化效果,可提高合金的力学性能,改善铸态组织。锆与镁具有相同的密排六方结构,且二者点阵错配度很小,在熔体中含有熔点较高的。Zr弥散质点可以起异质形核的作用。锆除了可以起到异质形核作用,还能减缓合金元素的扩散速度,阻止晶粒长大。当锆加入量较大时,由于对元素扩散的阻碍作用,在一定程度上会影响均匀化效果;当锆加入量大时,元素扩散速度显著降低,合金中的枝晶组织和合金元素在晶界上的富集相未完全溶解,均匀化不充分,使合金的强度和塑性均有所下降。藤谷涉等的研究表明,0~0.2%的锆可提高Mg-8Li合金的超塑性,原因是锆可以细化再结晶组织,有利于获得细小等轴晶,并且锆溶质原子抑制位错移动促使均匀变形,改善合金超塑性。
6锰元素的影响
在镁锂合金中添加锰元素并不能大幅度提高合金的抗拉强度,但是能稍微提高屈服强度。锰有与铁等形成稳定化合物的能力,加入少量锰可以除去镁锂合金液中的铁及其他重金属元素,避免产生有害的金属间化合物,进而提高Mg-Li-Al合金和Mg-Li-AI-Zn合金的抗海水腐蚀能力,在熔炼过程中部分有害的金属间化合物会分离出来。此外,锰还可以细化晶粒,而且本身也起一定的固溶强化作用。镁锂合金中锰的含量通常低于1.5%,而在含铝的镁锂合金中,锰的固溶度仅为0.3%。
7钙元素的影响
钙在镁合金中具有晶粒细化、熔体阻燃、提高合金的高温蠕变性能等作用,此外还有成本低廉、密度小等优点。因此,钙在镁锂合金中作为合金化元素同样具有很好的技术优势。
在Mg-12Li二元合金组织在添加钙前是β单相组织,添加钙后,合金组织由初生的枝晶状β相和分布于β枝晶相间呈层片状的共晶组织β+CaMg2构成,如图2所示。经冷轧加工后,合金内的层片状共晶组织被打乱并且重新分布。合金在表面氧化过程中,优先在β相区域发生氧化,而在共晶组织区域几乎没有氧化现象,这验证了钙在镁锂合金中具有阻燃或防止氧化功能。
图2 Mg-12Li-5Ca合金显微组织
在LZ系合金中,加入微量的钙就能够显著细化晶粒,并提高合金的力学性能。在LZ92合金中,钙添加量为0.1%时,对合金组织的细化效果最好,同时合金的强度和延伸率与未加钙的LA92相比分别提高19%和6%,继续增加钙含量会使合金的强度略有提高,但延伸率有所下降。
8稀土元素的影响
镁锂合金中加入稀土元素,通过固溶强化和形成细小弥散的金属间化合物,提高其综合性能,并可通过提高析出相的热稳定性,改善合金在较高温度下的力学性能,加入稀土元素还可以提高镁锂合金的再结晶温度,并促使镁锂合金的时效强化。稀土元素在镁锂合金中的固溶度均较小,能与镁形成多种金属间化合物,表2为轻稀土在镁中的最大固溶度,表3为镁和稀土的原子半径及电负性。
表2 轻稀土元素在镁中的最大固溶度
表3 镁和主要稀土元素的原子半径和电负性
1钕(Nd)在镁锂合金中的作用
钕在Mg-8Li二元合金中对于合金的力学强度和耐热性能没有明显提高这是由于虽然钕在合金中主要以Mg3Nd的形式存在,Mg3Nd的存在对于合金的力学强度和耐热性能是一有利因素,但是由于钕的加入使合金中α初生相减少,影响了合金力学强度和耐热性能的提高。此外,钕的加入提高了Mg-8Li二元合金的再结晶温度,并使合金具有时效硬化现象(使得α相从过饱和的β相中析出)。
钕在Mg-Li-Al三元合金中并不以Mg3Nd相的形式存在,而是以Al2Nd相的形式存在。此外,钕的存在对LA141合金具有显著的晶粒细化作用,当钕质量分数为0.6%左右时,合金的晶粒尺寸最细小,减小30%(图3);在Al2Ni相的存在和钕对合金晶粒细化效果的共同作用下,合金的强度随着钕含量的增加迅速提高,最高时提高45%左右(图4)。
图3 Nd含量对LA141合金晶粒尺寸的影响
图4 Nd含量对LA141合金强度的影响
2铈(Ce)在镁锂合金中的作用
铈在Mg-Li-Al三元合金中主要以Al2Ce相的形式存在,在LA81合金中添加质量分数为1%的铈后,合金内Al2Ce相呈棒状均匀分布,经挤压变形后,棒状Al2Ce相被破碎成为短棒状并沿挤压方向分布。挤压后的强度和延伸率均得到提高,抗拉强度由160MPa上升到187MPa,延伸率由16%上升至33%。当铈质量分数大于0.6%时,Al2Ce相割裂基体,从而降低合金的力学性能。
3钇(Y)在镁锂合金中的作用
在高钇含量的Mg-Li二元合金中,将形成γ相(Mg24Y5),在Mg-7.28Li-8.02Y合金中除了存在呈长条状分布于基体β相中的α相,还存在沿晶界分布且呈网状结构的γ相(Mg24Y5)。此合金在淬火处理过程中,随着淬火温度的升高,实验合金中的Mg和Mg24Y5在β相中的固溶度随之增加,导致硬度增加;同时温度的升高使Mg24Y5的形貌逐渐变为圆球状且均匀分布。因此,固溶度的提高和Mg24Y5相的球化及均匀分布是导致在升高淬火温度时合金硬度和强度提高的原因。淬火态合金经150℃时效后,会使合金的强度和塑性均有所下降,分析其原因:一方面,在时效过程中合金的晶粒长大;另一方面,长时间的保温时效后Mg在β相中的固溶度降低,α相和Mg24Y5相沿β相晶界析出,导致合金的强韧性下降。
4钪(Sc)在镁锂合金中的作用
Wu等[1]研究了微量钪(质量分数为0.01%)对于LAZ1010合金组织和性能的影响。微量钪的加入使合金只能在室温下进行时效处理,否则将发生时效软化现象,而不加钪的合金可要室温或50℃下进行时效硬化热处理,如图5所示。时效温度下降的原因可能与时效过程中在LAZ1010Sc合金内存在Widanstatten型组织的α相有关(图6)。微量钪的加入将促进q相(MgAlLi2相)分解成平衡相AlLi相。合金在加入微量钪后,力学性能发生微小变化,屈服强度由154.8MPa上升到172. 1MPa,抗拉强度由172.5MPa上升到186.4MPa,延伸率由28.9%下降至25.2%。
图5 不同温度下合金的时效曲线
图6 时效后合金的显微组织
[1] Wu R Z,Zhang M L, Wang T. Microstructure characterization and mechanical properties of Mg-9Li-5Al-1Zn-0.6RE alloy. Transactions of Nonferrous Metals Society of China,2007,17(s1A):s448~s451.
免责声明:本网站所转载的文字、图片与视频资料版权归原创作者所有,如果涉及侵权,请第一时间联系本网删除。
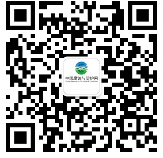
官方微信
《中国腐蚀与防护网电子期刊》征订启事
- 投稿联系:编辑部
- 电话:010-62316606-806
- 邮箱:fsfhzy666@163.com
- 中国腐蚀与防护网官方QQ群:140808414