第三章 全面腐蚀 ▲
3.4 全面腐蚀机理
全面腐蚀(均匀腐蚀)是由化学腐蚀或电化学腐蚀引起的。腐蚀介质能够较均匀地抵达金属表面的各部位,而且金属的成分和组织比较均匀,使腐蚀在整个金属表面以几乎相同的速度进行。
全面腐蚀多发生在碳钢和低合金钢材料上。不锈钢和其他依靠钝化膜耐蚀的材料在低pH值的腐蚀环境中,也可以因钝化膜溶解而活化,发生全面腐蚀;或者在高温条件下,钝化膜转化为疏松多孔的氧化皮,附着性差易剥落,而失去保护作用。
无论是化学腐蚀,还是电化学腐蚀引起的全面腐蚀,其共同的特点是材料表面不能形成具有保护作用的钝化膜,腐蚀产物可溶于介质中,或形成疏松多孔的氧化皮,使腐蚀得以持续进行。
Vol.3.4.1 化学腐蚀
化学腐蚀通常发生在一些干燥气体和非电解质溶液环境中,工业中常见的化学腐蚀有金属高温氧化、高温硫化、卤素腐蚀等其它的氧化剂(H2O、CO2、SO2、SO3、H2S等)引起的化学腐蚀,在这些腐蚀条件下金属表面会形成氧化膜(层、皮)、硫化膜(层、皮)、氮化膜(层、皮)、卤化膜(层、皮)等;在渗碳、脱碳、氢腐蚀等还原性气氛引起的腐蚀,会形成渗碳或脱碳层;在熔盐中产生碱性或酸性熔融腐蚀导致金属厚度减薄;金属在非电解质溶液中的腐蚀、某些金属在某些有机溶剂中的腐蚀现象(如:Al在CCl4、Mg和Ti在甲醇中的腐蚀)等也属于化学腐蚀。腐蚀反应热力学和动力学见“化学腐蚀”。金属被氧化的化学腐蚀表现为氧化膜(皮)或其他腐蚀产物形成的膜逐渐增厚,腐蚀能否持续进行和腐蚀速率,取决于所生产的氧化膜(皮)对基体金属的保护作用。
01 氧化
在空气或高温含氧的工艺气、烟气、水气等环境中,金属被氧化,产生全面腐蚀。主要化学反应见式2-1~2-4。高温氧化的典型过程为当金属达到高温氧化起始温度时开始氧化,在金属表面形成一层致密的金属氧化膜阻止金属发生进一步氧化,但随着温度上升,氧化膜成分发生变化,氧化膜逐渐增厚,失去对金属的保护作用。金属中的铬含量的增高有助于提高氧化膜的稳定性,阻止氧化皮的剥落。
碳钢的基体组成为Fe,因此它的氧化皮主要是由FeO、Fe3O4、Fe2O3组成,故它的抗氧化性和纯Fe的差别并不大,即570℃以下碳钢具有较好的抗氧化性,温度高于700℃时碳钢脱碳严重,它比纯Fe的抗氧化性更差,这是因为脱碳时逸出气态CO2使氧化皮中出现更多缺陷的缘故。
提高钢铁抗高温氧化性能的主要合金元素,除Cr外还有Al和Si。虽然Al和Si的作用比Cr更强,但加入Al和Si对钢铁的力学性能和加工性能不利,而Cr能提高钢材的常温和高温强度,所以Cr成为耐热钢必不可少的主要合金元素。Ni-Cr合金由于Cr的选择性氧化,合金表面可形成致密的NiCr2O4及Cr2O3保护膜,使合金的抗氧化温度达1100℃。Ni-Cr-Al合金由于Al2O3的热稳定性比Cr2O3更高,所以Ni-Cr-Al合金可以在1300℃下使用。
02 高温硫腐蚀
高温硫腐蚀指金属在高温下与含活性硫介质作用,生成硫化物的过程,它是炼油石油化工、火力发电和工业中各种燃料炉的一种常见的失效方式。高温环境中硫的存在形式不同, 硫腐蚀的类型也呈多样性,可大致分为: 高温硫化,高温混合气氛下的硫化-氧化所导致的热腐蚀。
① 高温硫化腐蚀
高温硫化是指高温下金属与硫反应而导致的腐蚀。通常是指含H2S、单质S蒸气和有机硫化物在高温下与金属发生高温硫腐蚀,形态为均匀减薄,可在金属表面生成硫化物膜,硫化物膜厚度较大,可达几十nm,甚至更高,某些硫化膜也可以对基体金属产生保护作用。如在240℃以上的重油部位硫、硫化物和硫化氢形成的腐蚀环境,常减压蒸馏装置中的常压塔减压塔下部及塔底管线、常压重油和减压渣油的高温换热器,硫化催化裂化装置分馏塔的下部、延迟焦化装置分馏塔的下部等位置。加氢装置、催化重整装置、延迟焦化装置的焦炭塔、分馏塔、硫磺回收装置、硫磺尾气脱硫装置以及聚苯乙烯装置的脱氢炉等都存在高温硫的腐蚀。
Ni及Ni合金对H2S和含硫气体在高温下特别敏感,这种腐蚀往往带有灾难性。因为,液态硫化物迅速进入金属晶界,从而使金属碎裂。但铁基合金、300系列不锈钢在这种环境下耐蚀性较好。
金属与硫反应的速度比氧化反应快得多,其主要原因为:
a.硫化物的扩散系数大于氧化物的扩散系数;
b.硫化物的熔点比氧化物的低,金属可与这些硫化物形成低熔点的共晶物,进而导致加速硫化反应;
c.金属硫化物的分子体积大于氧化物,硫化物产生的应力比氧化物产生的应力大许多, 易使硫化层破裂,从而加速金属的硫化。
能与金属起反应的硫称为活性硫,主要有元素硫、硫化氢、硫醇硫、二硫化物、亚砜、硫醚,硫醚、噻吩、苯并噻吩、二苯并噻吩、砜为非活性硫。高温硫腐蚀与温度关系密切,不同温度下各种硫化物的腐蚀性不同。所以,在含硫原油的加工过程中,由于非活性硫不断向活性硫转变,使硫腐蚀不仅存在于一次加工装置,也存在于二次加工装置,甚至延伸到下游化工装置。可以说硫腐蚀贯穿于炼油的全过程。再加上硫腐蚀与氧化物、氯化物、氮化物、氰化物等腐蚀介质的共同作用,形成了错综复杂的腐蚀体系,对硫腐蚀的动力学和热力学研究以及防护措施的制定带来很多困难。主要机理为:
a.t≤120℃硫化物未分解,在无水情况下,对设备无腐蚀;但当含水时,则形成炼厂各装置中轻油部位的各种H2S-H20型腐蚀;
b.≤240℃,原油中活性硫化物未分解故对设备腐蚀轻微;
c.240℃<t≤340℃,硫化物开始分解,生成H2S对设备腐蚀开始,并随着温度升高而腐蚀加重;
d. 340℃<t≤400℃,H2S开始分解为H2和S,H2S分解出来的硫为活性硫,腐蚀性很强。该温度下,低级硫醇能直接与铁反应而腐蚀。腐蚀反应式为:
H2S = H2 + S(3-1)
Fe + S = FeS(3-2)
RCH2CH2SH + Fe = FeS + RCH=CH2 + H2 (3-3)
炼油厂中高温硫的腐蚀是以H2S为主的活性硫腐蚀,由于原油所含硫化物组成及性质不同,腐蚀性也可能不同。原油中不同有机硫化物有不同分解温度,硫醚和二硫化物在130~160℃开始分解,其他有机物的分解反应在250℃左右开始。温度升到375~425℃时未分解的H2S也能与铁直接反应;
e.420℃<t≤430℃,高温硫对设备腐蚀速率最快;
f.t>480℃,硫化物近于完全分解,腐蚀率下降;
g.t>500℃,硫化物不稳定,腐蚀转化为高温氧化腐蚀。
不同硫化物的腐蚀性强弱不一样,二硫化物腐蚀最强。含有活泼氢的硫化物在高温下对金属的腐蚀服从催化反应机理,无活泼氢的硫化物在高温下对金属的腐蚀服从硫自由基机理。单质硫在高温下不需要离解或催化过程,可直接在金属表面吸附发生反应腐蚀金属,所以单质硫在这些硫化物中表现出了最强的腐蚀性。二硫化物官能团“-S-S-”化学性质十分活泼,受热易分解,生成硫自由基,因此对金属具有很强的腐蚀性。H2S在高温下由于通过氢原子吸附在金属表面,其吸附作用和硫自由基相比稍弱,因此其腐蚀性应弱于元素硫和二硫化物。硫醇在热作用下可以形成·SH自由基,也可以在金属表面催化腐蚀金属,因此腐蚀性应比硫化氢弱,但强于其它非活性硫化物。硫醚中的官能团“-S-”化学性质较为稳定,只有分解或生成硫自由基才能腐蚀金属。噻吩类硫化物由于其双环作用,大大增强了其分子内的共轭作用,因此噻吩类化合物性质十分稳定,在热作用下几乎不分解,同时由于其强共轭作用,分散了硫的电子云密度,使硫具有一定的亲电性,因此其可以在金属表面具有一定的吸附量,因而在一定条件下,噻吩类化合物具有一定的缓蚀作用。
影响高温硫腐蚀的主要因素有:
a.材料合金成分。增加材料中Cr元素含量可提高其抗高温硫腐蚀性能,加工高含硫原油的高温(288℃)以上部位,Cr5Mo的腐蚀速率较大,应选用更高等级材质,见SH/T 3096[1],300系列不锈钢可耐硫腐蚀。工程设计上耐硫腐蚀金属材料的选择是根据腐蚀性评价数据或曲线和实践经验来确定,不片面追求合金化和不锈钢化。McConomy曲线可以预测材料高温硫的腐蚀程度,工程上用来确定选材,API RP 939C [2] 对McConomy曲线进行了修正和补充。该项推荐作法适用于操作温度在230℃~540℃条件下,不论是否有氢存在的含硫化合物的烃类工艺流体。这里没有规定含硫量的下限,因为在过去10多年中,一些加氢处理装置的重沸器/分馏塔在硫或H2S含量低至1×10-6的情况下也出现了比较严重的腐蚀。API RP 939C的适用范围不包括镍基合金腐蚀和由于燃烧含硫燃料所导致的加热管外壁腐蚀;
b.温度和流速。介质流速和温度的升高均能导致材料的腐蚀速率增加,温度的影响大于流速的影响。流速超过30m·s-1腐蚀加剧,和环烷酸腐蚀一样,在涡流高的位置保护性的硫化膜被冲刷,腐蚀加剧;
c.原油的硫含量与其腐蚀性没有线性关系;同一种原油不同馏分油的硫含量决定油品的腐蚀性能,油品的腐蚀速率随硫含量的升高而增加。
② 高温混合气氛下的硫化-氧化
高温混合气氛下的硫化-氧化腐蚀是指在含氧和硫的混合气氛下,金属受到氧化、硫化或硫化-氧化为主的腐蚀,主要形式有:
a.在氧分压高于氧化物分压时,反应主要是氧化,形成氧化物;
b.在硫分压高于硫化物分压时,反应主要是硫化,形成硫化物;
c.当环境气氛的硫分压、氧分压正处在硫化物、氧化物的分压时,同时发生硫化、氧化,硫化物和氧化物能平衡共存。
03 环烷酸腐蚀
环烷酸在石油炼制过程中,随原油一起被加热、蒸馏,并与其沸点相同的油品冷凝,且溶于其中,从而造成该馏分对设备材料的腐蚀。
环烷酸是非电解质,与金属的反应是化学腐蚀过程。腐蚀大多发生在液相,在220℃以下腐蚀很轻,在沸程为270~280℃,350~400℃时腐蚀最严重,气相腐蚀很小。环烷酸腐蚀的反应为:
2RCOOH + Fe = Fe(RCOO)2 + H2↑ (3-4)
2RCOOH + FeS = Fe(RCOO)2 + H2S↑ (3-5)
可以看出,环烷酸除了与铁直接作用产生腐蚀外,还能与腐蚀产物如FeS反应,生成可溶于油的环烷酸铁,当环烷酸与腐蚀产物反应时,不但破坏了具有一定保护作用的FeS膜,同时游离出H2S又可进一步腐蚀金属:
H2S + Fe = FeS+ H2↑ (3-6)
从动力学角度考虑,环烷酸与金属反应通常经过环烷酸分子向金属表面传输、在金属表面吸附、与表面活性中心发生反应、腐蚀产物脱附4个步骤,上述步骤中最慢的步骤是整个腐蚀反应的控制步骤。因原油性质和设备材质不同, 反应温度和流速流态等因素的差异, 环烷酸腐蚀的控制步骤也会发生变化。环烷酸腐蚀为吸热反应,因此升高温度,显著加速碳钢在高温环烷酸介质中腐蚀速率。
影响环烷酸腐蚀的因素主要有油品的酸值、硫含量、温度、流速和流态、材质、环烷酸的种类和分子量大小。介质的酸值、流速、流态和温度是环烷酸腐蚀的重要参数,流速和酸值、温度存在着一个临界值,对环烷酸腐蚀的影响很复杂。在不同的流速流态下,环烷酸腐蚀形态和机理都可能发生改变。针对高温环境下影响原油中环烷酸腐蚀的主要因素, 一般主要采用以下方法控制其腐蚀:
a.合理设计,改进炼油工艺,采用混炼或掺炼技术、注碱工艺以降低原油酸值或控制硫含量等方法,将高酸值和低酸值的原油混合到酸值低于环烷酸腐蚀发生的临界值以下控制环烷酸腐蚀;
b.选材,在较高流速下,耐蚀性从低到高排列顺序为碳钢、低合金钢和不锈钢。Cr对耐蚀性起决定作用,主要是提高合金热稳定性和产生钝化作用,在钢表面形成富氧的氧化膜,扩大钢在酸中的钝化范围,提高钢的抗氧化能力。有研究表明[3],在酸值小于4 mg KOH/g、流速大于73 m·s-1时,5Cr-0.5Mo 和12%Cr钢有比碳钢更好的耐蚀性能。
中国石化集团防腐蚀研究中心对S32168(321)、S31603(316L)、S41008(0Cr13)、Cr5Mo和20G在环烷酸腐蚀速率进行了试验研究,结果见图3-11、12。介质流速在25m·s-1时,不锈钢明显优于碳钢和低合金钢,在300℃以上S31603仍能维持钝态,而S32168、S41008已活化,腐蚀速率明显上升。
图3-11S31603、0Cr13、Cr5Mo和20G腐蚀评价结果(25m·s-1)
图3-12 S32168和S31603的腐蚀评价结果对比(25m·s-1)
c.注碱中和或原油脱羧。在原油进入蒸馏装置之前,可注入苛性钠中和环烷酸,然后分离;
d.控制流速流态。包括适当降低物料流速、在可能的情况下改变管长、扩大管径以降低流速, 尽量在结构上平缓过渡, 减少急弯走向以控制流态等方法来控制环烷酸对设备的腐蚀。但是由于工艺的限制,对于流速、流态的改变受到很大的局限,因此对环烷酸腐蚀的抑制作用也有限;
e.添加缓蚀剂,常用的环烷酸缓蚀剂主要有磷系缓蚀剂以及非磷系缓蚀剂,磷系缓蚀剂主要有磷酸酯类、亚磷酸芳香酯类缓蚀剂,非磷系缓蚀剂是一些含氮、硫等元素的有机化合物。在缓蚀效果方面磷系缓蚀剂优于非磷系缓蚀剂,而将两者混合使用缓蚀效果最佳。
f.涂镀层表面保护。在基材表面喷涂耐高温涂层或采用化学镀层等。该方法实际上将环烷酸与钢铁界面变成环烷酸与耐高温涂层间的界面。耐高温涂层或化学镀层难溶于环烷酸或原油,故可有效防止环烷酸腐蚀。
g.加强在线腐蚀监测,采用腐蚀挂片、旁路、馏分油铁离子分析、超声波测厚、安装电阻或电感腐蚀探针等方法在线监测材料的腐蚀速率。
04 高温氢腐蚀(HTHA)
HTHA是氢原子扩散到钢中并与微观组织中的碳化物发生反应的结果。在临氢条件下,吸附在钢表面的分子氢通过金属晶格和晶界向钢内扩散,使钢严重脱碳产生沿晶腐蚀裂纹,力学性能下降。这种腐蚀速度取决于温度、氢分压、加热时间、钢的含碳量和合金元素等因素。有2种反应和HTHA相关,一个是氢分子(H2)分解成能在钢中扩散的氢原子(H),第二个反应发生在原子氢和金属碳化物之间,4H + MC = CH4 + M。对钢材的破坏也有2种形式,一是因甲烷气体在碳化物基体界面上积聚,形成了很高的局部应力,而产生内部脱碳和裂纹或鼓包,其力学性能发生显著的劣化。二是原子氢和钢材表面或临近表面的碳化物发生反应产生的表面脱碳,在该表面甲烷气体可溢出而不会形成裂缝。内部裂缝一般可在碳钢、C-0.5Mo钢和高氢分压下的Cr-Mo钢中观察到,而表面脱碳在高温和低的氢分压下的Cr-Mo钢中更普遍。增加钢中合金的Cr、Mo元素,碳化物的稳定性提高,可减缓HTHA。
钢的抗氢腐蚀性能与钢的显微组织也有密切关系。所以,压力容器的制造和热处理制度对设备的抗HTHA性能影响也很大,对于淬火状态,只需经很短时间加热就出现了氢腐蚀,但进行回火处理,且回火温度越高,由于形成稳定了的碳化物,抗氢腐蚀性能也得到改善。另外,对于在临氢环境下使用的铬-钼钢设备,进行焊后热处理同样具有提高抗氢腐蚀能力的效果。试验证明,2.25Cr-1Mo钢焊缝若不进行焊后热处理,则发生氢腐蚀的温度将比纳尔逊(Nelson)曲线表示的温度低100℃以上。
在高温氢腐蚀中,在高温氢气中材料的蠕变强度会下降。特别是由于二次应力(如热应力或由冷作加工所引起的应力)的存在会加速高温氢腐蚀。当没有变形时,氢腐蚀具有较长的“孕育期”;随着冷变形量的增大,“孕育期”逐渐缩短,当变形量达到一定程度时,则无论在任何试验温度下都无“孕育期”,只要暴露到此条件的氢气中,裂纹立刻就发生。
高温高压氢环境下的设备选材是按照“纳尔逊(Nelson)曲线”来选择的,该曲线最初是在1949年由G·A·Nelson收集到的使用经验数据绘制而成,并由API提出,于1970年作为API出版物941(第一版)公开发行。从1949年至今,根据实验室的许多试验数据和实际生产中所发生的一些氢腐蚀破坏的事例,相继对曲线进行过多次修订,API RP 941一直是最有用的抗高温氢腐蚀选材的一个指导性文件,该准则提供了炼油厂和石油化工厂加工高温高压氢气或含氢流体设备用钢的安全范围,相关国家标准正在制定中。该曲线是本推荐准则中所列的临氢作业用钢防止脱碳和开裂的操作极限,在温度和氢分压范围,这些钢已经得到成功应用而没有因HTHA造成的破坏。材料默认为退火状态,不能用于含As、Sb、Sn和P等高含量混入元素的钢,如怀疑高含量混入元素,则临界Pv系数应降低,对于高含量的混入元素的钢的熔炼炉次,临界Pv系数可低至0.25。
05 渗碳
在高温及含碳的环境气氛(如CO和烃类)中,环境中的碳化物在与钢接触时发生分解并生成游离碳,使钢表面的氧化膜破损,并渗入钢中生成碳化物的现象。一般在表面发生,碳的浓度在表面最大。渗碳危害有:
a.渗碳裂纹;
b.蠕变断裂;
c.650℃以下的脆性断裂;
d.渗碳引起的金属粉化;
c.承载壁厚减薄。
06 脱碳
钢的脱碳是由于钢中的渗碳体Fe3C在高温下与介质作用被还原成铁发生脱碳反应,使得钢表面渗碳体减少。由于Fe3C含量的减少将使钢表面的碳含量降低,致使钢铁表面硬度减小,疲劳极限降低,此现象称为碳钢的脱碳。主要化学反应有:
07 氮化(渗氮)
某些合金暴露在含氮化合物(氨、氰化物)很高的高温工艺环境中时,尤其是在还原条件下,形成一个硬脆的氮化表面层。受影响的合金主要有碳钢,低合金钢、300系列和400系列不锈钢。会导致高温蠕变强度、室温力学性能(尤其是强度/韧性)、焊接性能和耐蚀性能的降低,严重降低材料的耐蚀性。
渗氮是一个扩散控制过程,由温度、时间、氮的分压和金属成分决定。温度必须足够高,以使氮从氨或其它化合物中热分解出来,并使氮向金属内部扩散。渗氮在温度高于316℃时开始发生,在高于482℃时加重。高气相氮活性(高的氮分压)促进渗氮。
渗氮通常发生在部件的表面,形成一个暗灰色的外观。但是,在渗氮的初始阶段,只能通过金相来发现。在更严重的阶段,金属会显示出很高的表面硬度。在多数情况下,容器或设备表面硬度的轻微增加不会影响设备的整体力学性能。但是,在渗氮层内潜在的裂纹扩展可能会穿透整个基体金属。12% Cr(mass)以下的低合金钢的渗氮伴随着体积的增加,渗氮层会开裂和破碎。高于410℃,优先的晶界渗氮可能会导致微裂纹和脆断。不锈钢会形成一个薄的脆性层,在热循环或外加应力的作用下发生开裂和破碎。
防护措施,需要采用更耐蚀的含有30%到80%的镍的合金,而不采用改变工艺条件来降低氮分压或降低温度。
Vol.3.4.2 电化学腐蚀
造成压力容器全面腐蚀的电化学腐蚀过程,主要取决于腐蚀微电池的作用。腐蚀原电池由微观腐蚀电池组成,其单个阴、阳极的面积非常小,甚至用微观方法也无法辨认,而且微阳极和微阴极的位置随机变化;整个金属表面在电解质溶液中处于活化状态,只是各点随时间(或地点)有能量起伏,能量高时(处)呈阳极,能量低时(处)呈阴极,从而使整个金属表面遭受均匀的腐蚀。
金属与溶液的界面特性―双电层,金属浸入电解质溶液内,其表面的原子与溶液中的极性水分子、电解质离子相互作用,使界面的金属和溶液侧分别形成带有异性电荷的双电层。双电层的模式随金属、电解质溶液的性质而异,一般有以下3种类型,图3-13。
图3-13 金属在电解质溶液中的双电层模型
a.离子的水化能超过了晶格上的键能,金属侧荷负电、溶液侧荷正电的相对稳定的双电层,电负性强的金属,如锌、镉、镁、铁等浸入水、酸、碱、盐溶液中形成这种双电层;
b.离子的水化能小于金属上晶格的键能,金属侧荷正电、溶液侧荷负电,通常比较不活泼的金属浸在含有浓度较高的正电性较强的金属离子的溶液中,如铂浸在铂盐溶液中、铜浸在铜盐溶液中等形成这种双电层;
c.离子的水化能等于金属上晶格的键能,形成金属侧荷正电、溶液侧荷负电,如铂浸在溶有氧的中性溶液中,氧分子被吸附在铂表面,并离解为原子,再夺得铂表面的电子而成为荷负电的负离子。
双电层如同平板电容,由于两侧之间的距离非常小(一般约为5×10-10 m左右),所以双电层中的电场强度特别高,达到109 ~ 1010 V·m-1。双电层两层“极板”分处于不同的两相—金属相(电子导体相)和电解质溶液(离子导体相)中,双电层的内层有过剩的电子或阳离子,当系统形成回路时,电子即可沿导体流入或流出电极,形成腐蚀电流,使腐蚀反应得以进行。金属的电化学腐蚀历程包含着两个同时进行而又相对独立的过程,即阳极的氧化反应和阴极的还原反应,当电极反应正逆过程的电荷输送速度和物质迁移速度相等时,反应达到动态平衡状态。
金属的热腐蚀是高温腐蚀的一种重要形式,在工业上,典型的热腐蚀环境主要有燃烧动力系统和燃料电池等。这两种环境的沉积岩类型分别为硫酸盐和碳酸盐。
a.硫酸盐体系。硫酸盐沉淀热腐蚀是指金属材料由于高温环境因素,在其表面沉积物形成熔融盐层而加速腐蚀的现象。碱金属等硫酸盐的熔点低,在高温下呈熔融状态。若在灰渣附着层中存在焦硫酸盐时会形成反应速度更快的熔岩型腐蚀。当温度在680℃左右时,熔融硫酸盐的腐蚀速度约为气态时的4 倍。并随壁温度增高而加剧。
如,在各种燃油和燃煤的动力装置中,由于燃料中含有S、K、C、Na、V等杂质,在燃烧时形成SO2、CO2、SO3、V2O5等杂质,与含O2和NaCI再作用形成硫酸盐沉积在材料表面。纯Na2SO4熔点为844℃,如果混合其他盐,混合盐的熔点会降低。
b.碳酸盐体系。碳酸盐体系背景主要是第二代燃料电池-熔融碳酸盐燃料电池。
由于表面沉积一层熔融盐而引起的金属热腐蚀与常规的金属在水溶液中腐蚀有相似之处。已明确,如果介质是离子导体,那么金属腐蚀过程总是按电化学腐蚀的途径进行。与水溶液相似,热腐蚀的电化学机制模型认为,在熔盐体中至少存在两个电化学反应,金属阳极溶解和氧化剂的阴极还原。
免责声明:本网站所转载的文字、图片与视频资料版权归原创作者所有,如果涉及侵权,请第一时间联系本网删除。
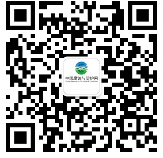
官方微信
《中国腐蚀与防护网电子期刊》征订启事
- 投稿联系:编辑部
- 电话:010-62316606-806
- 邮箱:fsfhzy666@163.com
- 中国腐蚀与防护网官方QQ群:140808414