在DefenceTalk论坛中有一个讨论是关于“为什么美国海狼级核潜艇只用到了HY-100,而没有选用当时已经开发出来HY-130或更高等级的材料”(http://www.defencetalk.com/forums/navy-maritime/steel-alloy-modern-cold-war-subs-7346/),咱也凑个热闹聊聊为什么在当时没有采用更高级别的高强钢。
首先,检索了从上世纪50年代以后美国舰艇的实际使用材料,美国在1940年以前一直使用碳钢建造潜艇。1950年设计用STS钢建造“大青花鱼”号潜艇。1951年,在该艇建造期间将STS钢牌号改为HY-80,并首次发布了MIL-S-16216军用规范。60年代初启用HY-100钢开始建造潜艇,并于20世纪末用于建造海狼级的核潜艇。而20世纪60年代中期,美国又研制开发了900MPa级的HY-130钢,并于1968年列于MIL-S-24371中,1969年用于建造深海救援艇“DSRV-I”号,不久又用于建造“DSRV-II”号和核动力深海工作船“NR-I”号。1975年又对美国海军标准MIL-S-24371做再次修订。直到80年代才开始用HY-130钢建造一艘战斗潜艇的部分分段。另外60年代末美国还研制了1250MPa级的(HY-150)10Ni-8Co-2Cr-1Mo钢,但始终未用于建造潜艇。可以看出HY-130于上世纪60年代中期研发,到上世纪未期“海狼号”建造期间,也有过一些试用,但好像都在小型舰艇上应用,属于尝试性应用。最终“海狼号”的设计人员认为HY-100是当时最合适的材料。
潜艇下潜深度的增加可增加潜艇隐蔽性和减少反潜武器对潜艇的威胁,若潜深超过300米就可有效躲避反潜深水炸弹的攻击。但对于水下潜体而言,在海水中每增加10米深度,水的压力增加一个大气压(1kg/cm2)。因此,下潜深度越大,海水对壳体的压力也越大。大量设计经验表明,深潜器耐压壳体的壁厚是下潜深度和壳体直径的函数。若提高下潜深度、增大直径,必须增加壁厚或提高耐压壳体材料的屈服强度。壁厚增加导致备用浮力损失,即承载能力降低。所以为减轻舰体自重,增加有效载荷,提高机动性能,舰体结构用钢首先必须具有较高的屈服强度。表1示出了世界知名潜艇的材料及最大下潜深度。
表 1世界知名潜艇的材料及最大下潜深度
从表1中可见,为了增加下潜深度,减轻结构重量,必须提高材料的屈服强度或比强度。但一切客观事物的属性都具有矛盾性,没有一种事物只有好的一面,并且一直朝好的方向发展,材料强化也一样,有好的方面,如减轻自重,多拉快跑,节能减排等,但材料升级的同时也面临着巨大的挑战。
表 2 各国舰艇钢
材料是国民生产的基础,反应一个国家的整体综合制造实力。但材料的强化升级绝不是单单轧一块钢板,铸一个钢锭那么简单。一个完美的产品,与选材有关,但设计,制造,安装,检验,操作,维护,环境等各因素也都是息息相关的,人机物法环任一环节出现纰漏都会带来产品的失效,造成毁灭性的后果。
图 1 2019年8月13日,俄亥俄级弹道导弹潜艇“田纳西号”抵达佐治亚州海军潜艇基地国王湾的三叉戟改装设施干船坞进行维修
01 机
近期美国拉英澳组建军事小集团,要以核潜艇武装澳大利亚,澳大利亚方面也宣布与美国和英国建立一个名为AUKUS的全新军事联盟,该联盟将使澳大利亚能够获得核动力潜艇以及其他先进军事技术,理由是对抗中国在亚太地区的“侵略心态”。这令许多分析人士质疑,是否仅仅是右翼政客强行绑架澳大利亚社会与人民,因为其中大量细节根本并未敲定,整个项目于一种浑沌状态。铁血胖兵也在其文章《制造核潜艇需要什么?不是谁都能玩得起!它哪来的勇气》中从技术细节分析了核潜艇制造的难度,即使不考虑高强度材料问题,宽板幅轧机,大吨位卷板机,大型船坞都是摆在澳面前的现实问题,而这仅仅是壳体结构的制造。别的行业不了解,拿商用车制造行业来举例,在澳洲年产量超过千台的厂家绝对算是大企业,从侧面也能反应其加工制造业的规模。材料的升级也必然要求加工设备的升级,才能较好的完成加工任务。
图 2 德国 HDW 214 壳体焊接
02 人
另外,前段时间,印度又传出了一个新闻,维克兰特号航母所在的造船厂发生了“生化爆炸”,甚至还造成十几人伤亡。据悉,这艘排水量达37500吨的航空母舰于2005年4月开始建造,建了12年才完成,打破了建造轻型航母最长时间的世界纪录。维克兰特号航母刚刚完成舰身,连舰岛都还没安装,印度海军就兴奋地举行了隆重的下水仪式,“炫耀”完了以后,维克兰特号又返回船坞继续进行建造,就这样进行了3次下水仪式,打破了航母下水仪式次数的世界纪录。之后就发生段首提到的那起最出名的“生化袭击”事件,对此印度方面也提高了警惕,不仅如此还在第一时间派出生化部队,专门成立了调查组进行调查,但调查结果却另人啼笑皆非,维克兰特号建造期间,旁边还有一艘正在维修的钻井船,这艘钻井船也是本次事故的“罪魁祸首”。钻井船化粪池中存在大量沼气,当时船上有个临时工躲到厕所抽烟,烟头不幸引爆化粪池中的沼气,钻井船也在瞬间被炸开,据悉,200多吨粪便将一旁的维克兰特号航母包围,遗憾的是,16名工作人员最后活活被熏死。虽然航母造船厂的爆炸是被涉及,但也是操作人员违反标准操作所导致,操作人员的素质对产品的最终质量有决定性影响,而制造材料强度等级的升级同时也更是提升了对实践操作人员的操作水平的要求。之所以这样说,因为高强度钢的加工难度要较普通钢难的多,请看下面关于加工的介绍。
图 3 印度维克兰特号航母
03 法
其实,目前高强钢的应用已经从军用扩展到民用并得到了广泛的普及,起重设备采用超高强度钢材(屈服强度900/1100MPa甚至1300MPa)作为臂架可以吊起几百吨的重物;高强度耐磨钢(一般采用布氏硬度划分等级,HBW 400/450/500,换算成屈服强度为1000/1250/1450MPa)在矿山设备广泛应用极大提高设备的耐磨寿命;近年来,国家严格限制公路运输车辆的超载行为,城市渣土车大量采用HBW450等级的耐磨钢作为车斗制作材料,各大主要城市已经普及,如图4 为采用屈服强度为1250MPa的耐磨钢的城市渣土车。但从加工工艺上来说,高强度钢和普通低碳钢Q355相比具有明显的区别,高等级大厚度的高强钢切割、焊接有氢裂风险,需要采取更严格的预热措施,选用低氢焊材,严格控制层间温度及热输入;折弯需要大吨位折弯机并采用较大的折弯半径,机加工和钻孔也需要采用特殊的工具。由于高强钢对裂纹的敏感性较大,所以应尽量避免在其表面留下划痕,所以在吊装存储时都应仔细对待,要求严格的应用也建议打磨切割毛刺,因为所以的细小裂纹都可以在后续工作过程中成为失效的隐患。对于对民用高强度结构钢来说,目前瑞典钢铁公司是世界最知名的高强度钢供应商,在其公司网站可以找到详细的加工指导。
图 4 由屈服强度为1250MPa的耐磨钢做成的车斗
我们再说一下设计,一般而言,对于所有结构用金属(特别是对于钢),当其强度增加或温度降低时,它们对于断裂或裂纹扩展的敏感性显著增加。所以在设计阶段必须仔细考查基础材料的裂纹敏感性,结构上避免应力集中,特别是关键点应力水平及焊缝质量。目前,很多挂车的大梁钢还是采用工字梁结构,由翼板和腹板焊接而成,为减轻自重,已经升级到600MPa或700MPa等级的高强钢,但继续提高强度就会引起焊缝的疲劳裂纹,为进一步减轻自重实现多拉快跑的优势,有些国外设计采用900MPa等级高强钢,通过折弯和栓接无焊缝设计大大提高了产品的可靠性。为了最高程度发挥高强钢的优势,必须采取更合适的设计结构才能保证产品的可靠性,而不是单纯依靠提高强度减薄厚度这一单一的手段,这样只是保证了强度水平,但却不能保证结构的稳定性,疲劳性等结构完整性目标。
视频:无焊缝、折弯+栓接设计挂车车架
04 物
凡是结构的灾难性破坏事故,如果追根溯源,总可以发现起因于金属的一些细微部分的微观力学过程,船只、桥梁和其他大型结构的破断是由几毫米大小的裂纹引起的。而现实中的任何结构都是非完美的,或多或少都存在着一些缺欠。在设计上必须充分考虑所用材料裂纹的敏感性与所设计结构可能存在的初始缺欠水平之间的关系。随着钢材强度的提高,这种敏感性是趋于增加的,在设计和制造均需根据敏感性水平做精确的控制,海军在历史上一直采用保守的结构完整性原理来鉴定舰艇,制定了精确地确定裂纹敏感性和检验可靠性的容限方法,而所有的控制都是以材料的初始测试为基础的。
在上篇文章,介绍了《美国舰船用钢标准》,里面列出了非常详细的材料测试方法及准则,提到船舶材料标准必须提到佩尼利,他在美国海军研究实验室工作了几十年,从解决舰船断裂等实际问题入手,把材料、断裂、设计、制造和环境载荷等理论融汇成为总的结构完整性的设计方法。其所发明的落锤冷脆转变温度(Drop-Weight NDT)工程实验分析方法,为美国材料试验学会(ASTM)收录用于表征金属断裂强度。他所创立的适用于工程设计的结构完整性的设计方法,宏微观相结合,科学与工程相沟通,既可用于指导材料的微观设计以利于宏观结构的可靠性,又成为美国乃至世界目前仍遵循的舰船材料评价规范的基础。《美国舰船用钢标准》中的夏比冲击能量,断口形貌标准、动态撕裂冲击、爆炸膨胀试验都是基于佩尼利所创建的理论。
我们所使用的钢铁材料一个很有意思的特点就是其延展性能随着温度发展明显变化,当温度较高时可以表现出非常好的延展性,如铁匠打铁前把铁烧红。钢铁韧性较好时其断裂为韧性断裂,断裂需要较大的驱动能量,并且有明显的相对缓慢的塑性变形可以做为报警信号;但当温度较低时又可表现出像玻璃一样的脆性。钢铁韧性不好时的断裂一般表现为脆性断裂,脆性断裂所需的能量小,并且断裂迅速几乎不发生塑性变形。材料从可延性到脆性或脆性到韧性的温度点,被称为“韧性到脆性过渡温度”。清楚了解某一金属(材料)的韧-脆性过渡温度的信息可以防止可能的灾难。在第二次世界大战期间,在自由轮的断裂就是一个坚实的例子,表明了脆性过渡温度的重要性。在生产过程中,船的金属的过渡温度被错误的计算。当船在寒冷的海水中航行时,船的金属体突然从延性变成了脆性并发生严重的断裂。
图 5 钢铁材料冲击功与温度的关系
对于大多数工程应用,较低的脆性过渡温度是最受欢迎的,以确保更大的延性范围。我们常用的夏比冲击测试就是为保证材料在使用温度不发生脆性断裂一种材料测试方法,常用的标准是以某一固定的能量来确定脆化温度。例如,第二次世界大战期间焊接油轮出现脆断事故后,进行了大量研究发现,如果用20J作为门槛值来确定船用钢板的脆性转化温度,则具有低于此脆化温度的材料,将不会发生脆性破坏。20J是在1950年针对当时船用钢板的指标,随着低合金高强度钢逐渐代替低碳钢,即由于材料强度的提高,能量标准值也在相应提高,如27J等,具体细节请参考《美国二战断裂自由轮钢板测试报告---钢材冲击功标准值“27J”是怎么定的?》。
除了冲击能量标准外,为确保所选用材料的十足可靠性。《美国舰船用钢标准》中还采用断口形貌标准,及更严格的动态撕裂冲击标准及爆炸膨胀试验标准方法来评价材料,以克服不同标准方法由于材料或材料尺寸效应所引起的结果差异,极尽可能做到万无一失,对舰船用钢提出了近乎苛刻的要求,具体可参考《康涅狄格号核潜艇及壳体耐压钢》。
脆性转变温度NDT<=-84℃, 下平台的能量 >47 J (HY-80) / >54 J (HY-100)
上平台能量 > 81 J (HY-80) / (HY-100)
最近一份报道称,位于堪萨斯城的供应商Bradken Inc.为海军承包商ElectricBoat和Newport News Shipbuilding提供钢铸件,用于制造潜艇船体。几十年来,该供应商提供的金属性能低于标准值,因为该公司的一名长期雇员伪造了实验室结果,使船员在发生碰撞或其他影响的情况下面临更大的风险。这位66岁的铸造厂冶金主任伊莱恩·托马斯曾在该实验室从事过40年的各种工作,马上就要享受退休生活,但晚节不保被控一项伪造了240种钢材的测试结果,占Bradken为海军潜艇生产的高强度钢材的近一半,而所涉及的测试就是通常在零下100华氏度下进行冲击韧性测试。诉状称,她这么做可能是因为她认为在如此寒冷的温度下进行测试是“愚蠢的要求”。这一事件从侧面也说明了,《美国舰船用钢标准》的要求是极其严格苛刻,产品合格率低,生产肯定是既费时又费力,导致冶金主任为赶工期铤而走险伪造了测试结果。
05 环
潜艇一般在水下温度-2.2~28.8℃,水面温度-34~49℃的环境中航行和战斗。潜艇在服役期间的上浮下潜使壳体承受周期性的交变载荷,还可能受到敌方反潜武器的攻击。因此,要求耐压壳体材料具有比强度大(屈服与密度比)、高韧性、良好的焊接性、抗低周疲劳性、抗爆性、冷热加工性等综合性能。
材料强度的提升会带来设备装备的升级,但同时也会牵一发而动全身引起设计、制造、安装,检验,操作,维护等一系列过程难度的提升,所以上世纪90年代美国海狼级核潜艇制造时选择了,强韧性匹配更好,更经济的HY-100作为主要壳体材料,据报道当时的预算达30亿美元,为节减开支进行了多轮的论证,如采用更高等级的材料,必将大大增加其预算。另一方面,即使采用更高强度的钢铁,也不一定就可以得到更好性能的潜艇,这与上述其他的因素还息息相关,材料决定一小部分。
基础材料的升级换代,需要经过多年的理论准备,人员素质的提升,前期大量的工程经验积累及标准法规的建立 ,只有在这些充分准备基础上,新材料才能得到普及。2019年亨廷顿·英格尔斯工业公司(HII)下属的纽波特纽斯造船厂举行了首艘哥伦比亚级弹道导弹核潜艇(SSBN-826)钢板切割仪式,但其所选用的材料还未知。
图 6 哥伦比亚级弹道导弹核潜艇(SSBN-826)钢板切割仪式
免责声明:本网站所转载的文字、图片与视频资料版权归原创作者所有,如果涉及侵权,请第一时间联系本网删除。
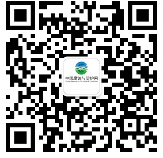
官方微信
《中国腐蚀与防护网电子期刊》征订启事
- 投稿联系:编辑部
- 电话:010-62316606-806
- 邮箱:fsfhzy666@163.com
- 中国腐蚀与防护网官方QQ群:140808414