金属材料铸造缺陷
铸造制品主要缺陷有偏析、气孔、缩孔与缩松、夹杂、裂纹、冷隔及其他缺陷。
01 偏析
偏析——在铸件中出现化学成分不均匀的现象。偏析使铸件的性能不均匀,严重时会造成废品。
偏析可分为两大类:微观偏析和宏观偏析。
晶内偏析(又称枝晶偏析)——是指晶粒内各部分化学成分不均匀的现象,是微观偏析的一种。凡形成固溶体的合金在结晶过程中,只有在非常缓慢的冷却条件下,使原子充分扩散,才能获 得化学成分均匀的晶粒。在实际铸造条件下,合金的凝固速度较快,原子来不及充分扩散,这样按树枝状方式长大的晶粒内部,其化学成分必然不均匀。为消除晶内偏析,可把铸件重新加热到高温,并经长时间保温,使原子充分扩散。这种热处理方法称为扩散退火。
密度偏析(旧称比重偏析)——是指铸件上、下部分化学成分不均匀的现象,是宏观偏析的一种。当组成合金元素的密度相差悬殊时,待铸件完全凝固后,密度小的元素大都集中在上部,密度大的元素则较多地集中在下部。为防止密度偏析,在浇注时应充分搅拌或加速金属液冷却,使不同密度的元素来不及分离。
宏观偏析有很多种,除密度偏析之外,还有正偏析、逆偏析、V形偏析和带状偏析等。
偏析金相组织见图1:
图1 边部灰色处为反偏析区
02 气孔
金属在凝固过程中,气体的溶解度急剧降低,在戮度很大的固态金属中难以逸出而滞留于熔体内形成气孔。与缩孔缩松的形态不同,气孔一般呈圆形、椭圆形或长条形,单个或成串状分布,内壁光滑。孔内常见气体有H2、CO、H2O、CO2等。按气孔在铸锭中出现的位置分为内部气孔、皮下气孔和表面气孔。气孔的存在减少了铸锭的有效体积和密度,经加工后虽可被压缩变形,但难以焊合,结果造成产品的起皮、起泡、针眼、裂纹等缺陷。
气孔形态金相组织见图2:
图2 浇铸时由模底和模壁产生的气体来不及逸出而沿结晶方向形成气孔
03 缩孔与缩松
金属在凝固过程中,发生体积收缩,熔体不能及时补充,而在最后凝固的地方出现收缩孔洞,称为缩孔或缩松。容积大而集中的缩孔称为集中缩孔,细小而分散的缩孔称为缩松,其中出现在晶界和枝晶间借助于显微镜观察的缩松称为显微缩松。
缩孔表面多参差不齐,近似锯齿状,晶界和枝晶间的缩孔多带棱角 , 有些缩孔常为析出的气体所充填,孔壁较平滑,此时的缩孔也是气孔,缩孔内往往伴生低熔点物。
缩孔均出现在断面的中心区。位于头部的缩孔多呈锥形,内表面参差不齐或 有粗大的结晶组织。位于中部的断续缩孔多为形状不规则的大小孔洞,内部有时会充有金属凝固时析出的气体,表面较光滑,在以后的加工中往往难以焊合而形成分层和气泡。缩孔的附近还易造成应力集中而在加工中产生裂纹。
缩松常分布于断面的中心附近或整个断面,有时出现在缩孔附近,呈细小分散的孔洞分布于晶界或枝晶间隙。有些细小的缩松肉眼难以发现,仅借助于显微镜或水压试验才能察觉。疏松造成金属组织的不致密,因而大大降低合金的机械性能和抗蚀能力。
缩孔和缩松区域的大小与合金的凝固收缩系数,金属液体的流动性,结晶温度范围的宽窄,铸锭的断面尺寸、浇铸温度以及凝固条件等因素有关。合金的凝固收缩系数愈大,铸锭断面的尺寸愈大,缩孔将愈严重。合金的结晶温度范围越窄,流动性越好,则缩孔越集中;反之如合金的结晶温度越宽,凝固时的结晶过渡带越宽,则愈易形成缩松。
缩孔与缩松产生的主要原因有:熔炼工艺不合理,浇铸温度较低,补缩不良,断流;冷却强度较大,浇铸速度快;结晶器设计不合理,保温帽太低、潮湿;合金结晶温度范围宽,流动性差等。
缩孔与缩松形态金相组织见图3、图4:
图3 铸造终了时补缩不良而在头部形成缩孔,缩孔内有气体未得逸出图片
图4 横截面存在分散缩孔,周围并伴生缩松及小裂纹图片
04 夹杂
与基体有明显分界面,性能相差悬殊的金属或非金属物称为夹杂。
按夹杂的性质可分金属夹杂和非金属夹杂两类。金属夹杂指不溶于基体金属的各种金属化合物初晶及未熔化完的高熔点纯金属颗粒以及外来异金属;非金属夹杂包括氧化物、硫化物、碳化物、熔剂、熔渣、涂料、炉衬碎屑以及硅酸盐等。
按夹杂来源的不同可分内生夹杂与外生夹杂。内生夹杂可能以游离状态或与基体金属结合成化合物的状态存在,也可能是多种杂质的互相结合。
内生夹杂中先析出的高熔点金属化合物初晶或纯金属多呈规则的颗粒状、块状、片状或针状,分布极不均匀。而低熔点金属化合物则常沿晶界或枝晶轴间析出呈液珠状、球状、网络状或薄膜状等。压力加工时,塑性良好的夹杂可沿加工方向拉长变形,塑性不良的夹杂仍保持铸造时形态或破碎成更小的颗粒,呈断续的链状沿加工方向分布。
外来夹杂是在生产过程中从炉衬、工具上的剥落物,通常较粗大而形状不定。由于与基体有完全不同的化学组成和组织,因而在折断口或切削加工时即可根据不同的色泽与受蚀情况被发现。
钢铁中非金属夹杂物形态见图5:
图5 钢铁中非金属夹杂物
05 裂纹
金属在凝固过程中产生的裂纹称为热裂纹;凝固后产生的裂纹称为冷裂纹。裂纹破坏了金属的完整性,除少数可通过及时加工除去外,通常在以后的加工和 使用过程中会沿着应力集中区域进一步扩大,最后导致破裂。
热裂纹是在铸锭尚未完全凝固或虽已凝固而晶界和枝晶间尚有少量低熔点相时,因金属液态、固态收缩及凝固收缩受到阻碍,当收缩应力超过了当时的金属强度或线收缩大于合金延伸率时形成的。按出现的部位不同,热裂纹可分为表面裂纹、中心裂纹、放射状裂纹及侧面横裂纹等。热裂纹多沿晶界扩展,曲折而不规则,常出现分枝,裂纹内可能夹有氧化膜或表面略带氧化色。
影响热裂纹的因素有合金的本性(合金的凝固收缩系数和高温强度等),浇注工艺和铸锭结构等方面。合金中某些元素及不溶性的低熔点杂质能明显增大热裂倾向。半连续铸锭的冷却速度较大因而比铁模铸锭热裂倾向大得多,铸造中加大铸造速度也会增大热裂倾向,从铸锭结构看,截面尺寸越大,则愈易发生热裂。
冷裂纹是在铸锭冷却到温度较低的弹性状态时,若锭坯内外还存在较大的温差,则收缩应力可能集中于某些薄弱区域。一旦应力超过了金属的强度和塑性极限,铸锭将出现冷裂。冷裂纹的特征是多呈穿晶开裂,多呈直线扩展,裂纹较规则、挺拔平直。冷裂纹往往由热裂纹发展而来。
铸造裂纹产生的直接原因是存在铸造应力,引起的因素有:铸造温度不合适,速度快,冷却速度过大或过小,冷却不均匀;连铸拉停工艺不当;合金本身有热脆性,强度差;覆盖剂或润滑剂选择不合理;结晶器、坩埚、托座、浇铸管等设计不良,变形或安装不当。
铸造中冷热裂纹如图6、图7:
图6 因铸造速度过快引起的中心热裂纹图片
图7 内部应力冷裂纹
06 冷隔
铸锭表面出现折皱或层叠状的缺陷,或者内部出现金属不连续现象统称冷隔。
冷隔的铸锭外表面不平整,层与层之间不连续,横断面分层,中间往往有氧化膜并伴生气孔等缺陷。
冷隔按形态可分折皱式和层叠式两种。当浇铸温度较低,金属液面产生的薄膜凝壳未能与后来浇入的金属熔合,便产生折皱式冷隔。层叠式冷隔较为多见,这是由于金属液的静压力大于金属的表面张力和氧化膜的强度,金属液冲破氧化膜而进入结晶器壁,但强烈地冷却使金属的流动性很快降低,结果不能与氧化膜凝壳熔合而形成层叠式冷隔。
冷隔按出现的部位不同分表面冷隔、皮下冷隔和中心冷隔。
冷隔产生的原因:浇铸温度低,冷却水压高,浇速不稳定,液面波动大,中间断流,补缩不良是形成冷隔的重要因素;严重的表面冷隔向铸锭内延伸,还引起皮下冷隔;结晶器内壁结构设计不合理,选材不当等也能导致冷隔的出现。
冷隔是铸锭常见缺陷之一,影响金属表面和内部的完整性,且会影响加工和 使用,严重时引起加工裂纹和其他表面缺陷。
冷隔缺陷形态如图8所示:
图8 中心冷隔
07 晶粒不均
铸锭不同部位晶粒大小差异较大的现象称为晶粒不均。
常见的有:扁锭结晶中心线偏离中心,两侧粗大柱状晶,方向相差较大,柱状晶扭曲,方向紊乱;圆锭偏心严重,局部粗大柱状晶,局部晶粒细小;悬浮晶或其他异常粗大晶粒。
产生的主要原因:结晶器内壁粗糙,结晶器变形,润滑油涂料分布不匀;冷却强度差异较大,冷却水分流不均,射角不合理,方向紊乱;浇铸时间长,浇温低,冷却缓慢等。
典型晶粒不均如图9所示:
图9 晶粒严重不均匀,结晶方向絮乱
08 其他表面缺陷
铸锭常见的表面缺陷还有:疤痕、麻面、麻坑、毛刺、纵向条痕,横向竹节等。
(1)麻面
铸锭表面的各种不平整现象称为麻面。
麻面上常有颗粒状凸起和砂眼,并伴生有涂料、覆盖剂、氧化物等污物。产生的主要原因是铸造温度低、速度慢;结晶器内壁不光滑或覆盖剂不良;漏斗堵塞等。
(2)毛刺
铸锭表面、边角、出现尖锐状金属凸起现象称为毛刺。
产生的主要原因是结晶器内壁不光滑;空心铸坯连铸芯杆质量不好。
(3)纵向条痕
铸锭表面呈连续或断续的纵向条状凸起或凹陷称为纵向条痕。
产生的主要原因是结晶器内壁钻有金属或其他氧化物或其上产生磨损的凹槽;内衬装配缝隙较大。
(4)竹节
具有拉停工艺的连铸坯,表面出现较大的周期性的凹凸现象称为竹节。
产生的主要原因是拉停工艺不当或者结晶器、模具变形。
金属材料加工成形缺陷
01 过热与过烧
金属在加热或加工过程中, 由于温度高,时间长,导致组织及晶粒粗大的现象称为过热;当金属在近于熔化温度下加热或严重过热时,晶间局部低熔点组元熔化或晶界弱化现象称为过烧。
过热后表面出现粗糙的麻点,桔皮,晶粒粗大等现象。过热了的合金强度虽下降不多,但室温下的冲击韧性和塑性却大大下降。材料变脆,断口上显现粗大的结晶颗粒。高倍下观察除粗大的等轴晶外,或有粗大的第二相,或有粗大的魏氏组织。过热并非绝对废品,有时可通过再变形、再处理等方法予以矫正或降级使用。
过烧后表面粗糙,晶界变粗、变直、发毛,甚至出现裂纹,还会出现易熔化和氧化薄膜层;过烧使金属结合力大大降低;显微组织中出现晶界加粗,熔化空洞或共晶球,熔化的液相网,甚至在几个晶粒的交界处有熔化出现的不规则空洞等现象;轧制时或挤制后出现晶界裂纹、板材侧裂、棒材头部开花、张口裂或裂成碎块,开裂部位能看到粗大枝晶和熔化的痕迹。
过热与过烧产生的主要原因有:加热温度高,时间长或局部长时间处于高温源处;热加工终了温度过高或者在高温区停留时间过长;合金中存在低熔点组元,或低熔点夹杂较多。
02 裂纹与开裂
(1)加工裂纹
加工工艺不当或工序存有缺陷时均能引起加工裂纹。加工裂纹也可分为热裂纹和冷裂纹两类,其区别在于裂纹周围的显微组织,前者无明显变化而后者有严重变形。就形态上来分有纵向裂纹、横向裂纹、侧裂、张口裂、螺旋状裂纹、周期性横裂、断裂、呈45°的斜裂纹以及不规则裂纹等。按分布则可分局部裂纹、头部开裂、表面裂纹、中心裂纹以及晶间裂纹等。
加工裂纹的产生原因应从金属本身及加工工艺两方面来分析。
属于金属本身的有以下几方面因素:合金的成分和杂质含量;铸锭存在冷隔、斑疤和偏析瘤等表面缺陷,缩孔、疏松、气孔、夹杂、偏析等内部缺陷时,加工时易沿此而产生裂纹;发达的柱状晶构明显弱面时易沿晶界或弱面开裂;合金在上道工序存有裂纹、过烧、过热,或第二相分布不良,组织不匀,以及相变引起的微裂纹等缺陷。
(2)热处理裂纹
①合金内部存在较大的残余应力时,如加热引起的热应力与残余应力方向一致而叠加超过金属强度时会造成开裂。
②合金在加热过程中有第二相沿晶界析出而形成第二类附加应力,或因相变而发生明显的体积改变时亦可发生裂纹。
图10为轧制时出现的各种裂纹示意图:
图10
03 夹杂
加工制品表面和内部出现的与基体有明显分界面,性能相差悬殊的金属或非金属物称为夹杂。
加工制品中夹杂主要来源于铸锭中未熔化完的金属颗粒,形成大块初晶或异金属进入;或夹有金属化合物以及硅酸盐、覆盖剂等。
其分类和特征与铸造制品夹杂基本一致。加工制品夹杂一般呈颗粒状、长条状沿加工方向分布,有一定形态和颜色,界面明显,不用侵蚀即可在金相显微镜下发现。
04 异物压入
金属或非金属压入制品表面称为异物压入。
金属压入物与基体有明显分界面,轮廓清楚,有不同的金属光泽,呈点状、块状,剥落后形成凹坑;非金属压入物形态不一,颜色各异,多呈脆性,无金属光泽,呈点状、片状、长条状沿加工方向分布,不易剥离。
异物来源:加热形成的氧化皮、润滑剂黏附在工模具和制品表面;工模具的碎片及黏附物;裂边的金属屑、毛刺及飞边;热处理炉的炉屑、油污;乳液内的杂物;轧道及导板上的异物。
05 鼓泡
制品经加工或退火后,表面出现沿加工方向分布的条状或泡状鼓起,剖开后为一空腔这种鼓起称为鼓泡。
鼓泡多呈条状,表面光滑,沿加工方向拉长,剖开后内壁呈光亮的金属色泽,个别伴有氧化物或其他夹杂。鼓泡大多两面对称分布,在较薄的板带材或薄壁管中比较明显。
鼓泡产生的主要原因有:铸锭中存在气孔,缩孔等缺陷;坯料退火时,炉内气氛控制不当,炉温过高;管棒材挤压时铸锭与挤压筒、挤压垫配合不良或者挤压筒、穿孔针润滑过量,挤压筒清理不干净,穿孔针有裂纹等。
06 分层
制品厚度方向出现缝隙,对应的加工方向分开成层。
层与层之间接触平整,面积较大,有些有氧化物或夹杂,常出现在薄带材中或薄带材经焊接后表现出来。管棒材断口检查时也会出现断口分层现象。
分层产生的主要原因有:铸锭中有气孔、缩孔、缩松、夹杂等缺陷,经加工后形成分层;板带材热轧道次压下量分配不当,压下量过大;铸锭加热不均匀,加热温度过高或过低;管棒材挤压筒或穿孔针润滑过量,穿孔针有裂纹或挤制品缩尾未切净,经进一步拉伸、轧制形成分层。
07 腐蚀
制品表面与周围介质接触,发生化学或电化学反应,在表面形成产物膜的过程称为腐蚀。
腐蚀后表面失去金属光泽,形成颜色各异的腐蚀色斑。
腐蚀形成的原因有:制品表面不清洁,残留有水、乳液等残液,或者放置保管不当,气候潮湿或水滴侵入表面;环境中有腐蚀性气氛。
08 氧化
制品在较高温度下,与氧接触生成氧化物称为氧化。
氧化后呈现深浅不同的氧化色,失去金属光泽,严重的出现氧化皮。
氧化产生的主要原因有:退火炉呈氧化性气氛;退火出炉温度高或在空气中暴露时间长,表面自然氧化;轧件余温较高,卷取或堆垛后形成氧化。
09 起皮、起刺
制品表面局部破裂翻起称为起皮。制品表面出现针尖状金属细丝状翘起称为起刺。
起皮或起刺一般沿轧制方向呈连续的或断续的分布,起皮部位往往有氧化皮或其他污物、夹杂等。管棒材起皮一般沿加工方向形成舌状、鱼鳞状翘起,严重的贯穿整个制品,局部严重的形成结疤。起刺多出现于轧制品的最后工序。
起皮产生的主要原因有:铸锭有缺陷,表面不平整;加工温度过高致制品表面氧化或上道工序导致表面有缺陷;轧辊上、挤压筒内、穿孔针上有水、油等脏物;加工工具有缺陷,加工过程机械损伤。
起刺产生的主要原因有:轧辊龟裂;坯料边部不平整,有不规则凹陷等。
10 起皱
制品表面不平整,呈轻微波纹状凹陷和凸起称为起皱。
起皱一般与轧向一致或斜向分布,呈单条或多条隆起,手感较圆滑,面积较大。
起皱产生的主要原因有:轧件不平整,或单向弯曲平直度差;张力不均匀(张力辊或张力套筒不平整);管材坯料塑性差,偏心严重;厚壁管变形不均匀,或变形量过大;轧辊调节不良及其他工艺缺陷。
11 麻面
制品表现出现微小的点状凹陷不平的粗糙面称为麻面。
麻面呈局部或连续成片分布,个别的称为麻点,严重的称为麻坑。晶粒粗大引起的麻面俗称桔皮。
麻面产生的主要原因有:退火温度过高,时间过长,晶粒粗大;过酸洗;加工率过小,表面不光滑;轧辊表面硬度不均匀,磨损严重,轧制工具锈蚀、有氧化皮或异金属。
12 机械损伤
外力作用于制品表面或板带箔材层与层之间的错动,引起表面呈条状、束状、凹坑状、尖锐沟槽状及其他形状的伤痕,常见的有擦伤、划伤、碰伤和压伤。
13 成分不均、组织不均
制品经轧制或退火后,不同部位化学成分存在较大差异的现象称为成分不均。成分不均能引起颜色或变形特性差异,宏观检验能看到成分偏析点或偏析区,显微组织和性能有差异,甚至出现开裂。
免责声明:本网站所转载的文字、图片与视频资料版权归原创作者所有,如果涉及侵权,请第一时间联系本网删除。
相关文章
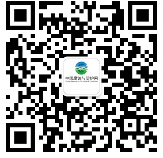
官方微信
《中国腐蚀与防护网电子期刊》征订启事
- 投稿联系:编辑部
- 电话:010-62316606-806
- 邮箱:fsfhzy666@163.com
- 中国腐蚀与防护网官方QQ群:140808414
点击排行
PPT新闻
“海洋金属”——钛合金在舰船的
点击数:7564
腐蚀与“海上丝绸之路”
点击数:6055