轴承,想必接触过机械的人们都熟悉,支撑机械旋转体,降低其摩擦系数,并保证其回转精度。在一些特殊领域,机械的运转对轴承的精度、性能、寿命和可靠性提出了高要求。那么,要使轴承得到这些要求,其材质是决定性因素之一。然而,中国的高端轴承钢仍在某些领域依赖进口,尤其是航空航天、核电等极限性能要求的轴承钢。目前,世界轴承巨头美国铁姆肯、瑞典SKF几乎垄断了全球高端轴承用钢的研发、制造与销售。
作为机械设备中不可或缺的核心零部件,轴承支撑机械旋转体,降低其摩擦系数,并保证其回转精度。无论飞机、汽车、高铁,还是高精密机床、仪器仪表,都需要轴承。这就对其精度、性能、寿命和可靠性提出了高要求。而在发动机中,轴承一直在“炼狱”中工作,它不仅要以每分钟上万转的速度长时间高速运转,还要承受着各种形式的应力挤压、摩擦与超高温。这对轴承的精度、性能、寿命和可靠性提出了高要求,而决定这四点的关键因素,在于其材质。
高端轴承钢的生产需要具备高精度的合金成分设计和冶炼工艺控制,以确保其具备优异的耐磨性、抗疲劳性、抗腐蚀性和高温稳定性等性能。尤其是需要在材料的微观结构(如晶粒细化、含碳量控制、夹杂物清除等)和表面质量(如硬度均匀性、抗剥离性等)上进行精确控制。此外,轴承钢的生产工艺也涉及到精密的热处理技术和加工技术,以确保其最终产品的高性能。
目前,中国在高端轴承钢的生产中仍面临技术“卡脖子”问题,特别是在以下几个方面:
合金元素的精确控制:高端轴承钢需要精确的合金成分设计,这对于冶炼技术的要求极高。某些高端轴承钢(如高温轴承钢、深冷轴承钢)的合金成分和制造工艺仍需要依赖进口。 微观组织控制和表面质量:轴承钢的疲劳寿命与其微观组织密切相关。控制钢材的晶粒结构、去除有害夹杂物及确保硬度分布均匀是生产过程中的难点。 表面处理技术:高端轴承钢的表面处理技术要求高,尤其是在大载荷、长寿命轴承的制造中,如何通过热处理、表面渗碳等技术提升其耐磨性和抗疲劳性仍是技术挑战。
高端轴承用钢的研发、制造与销售基本上被世界轴承巨头美国铁姆肯、瑞典SKF所垄断。前几年,他们分别在山东烟台、济南建立基地,采购中国的低端材质,运用他们的核心技术做成高端轴承,以十倍的价格卖给中国市场。炼钢过程中加入稀土,就能使原本优质的钢变得更加“坚强”。但怎么加,这是世界轴承巨头们的核心秘密。
在滚动轴承的四大组成部分中,除保持器外,内、外套圈、滚动体(滚珠、滚柱或滚针)都是由轴承钢组成,而轴承钢素有“钢中之王”的称号,是钢铁生产中要求最严的钢种。
轴承钢也有很多种类,根据使用要求的不同,化学成分也不相同,其中高碳铬轴承钢占很大的比例,是制造轴承和轴承零件最常用钢种。
轴承钢的质量主要取决于以下四个因素:一是钢中的夹杂物含量、形态、分布和大小;二是钢中的碳化物含量、形态、分布和大小;三是钢中的中心疏松缩孔和中心偏析;四是轴承钢产品性能的一致性。这四个因素可以归纳为纯净度和均匀性指标。
其中,纯净度要求材料中的夹杂物尽量少,纯净度的好坏对轴承的疲劳寿命有直接影响;而均匀性则要求材料中的夹杂物和碳化物颗粒细小、弥散,这会影响到轴承制造中热处理后的变形、组织均匀性等。
高端轴承钢中均匀细小的碳化物组织和热处理后均匀分布的细小碳化物
提高轴承钢的纯净度,首先要做的就是控制钢中的氧含量,炼钢中用ppm(每百万分之一)来作为氧含量的单位,一般来说8个ppm的钢就属于好钢,而高端轴承所需要的则是5个ppm的顶级钢。此外,钛等有害元素等留在钢中易形成多棱角的夹杂物,会引起局部的应力集中,产生疲劳裂纹,也都是应该要尽力避免的。
目前,随着钢的高纯净度冶炼平台系统的完善,轴承钢纯净度有了很大的提高,夹杂物水平得到有效控制,国外发达国家的钢中氧含量已经控制在5ppm以下,所以钢中碳化物的含量、分布、大小等逐渐变成了当下制约轴承钢质量的主要因素。
中国是世界轴承钢的主要生产国之一,如今,中国不仅能造出高端轴承钢,而且在国际市场闯出了名堂,中国的轴承钢已经供应给瑞典、德国、日本等国,同时高端轴承钢的疲劳寿命也达到甚至超过日本和欧洲的同期水平。有了好钢,下一步要解决的就是轴承的问题,高端轴承研发涉及材料、设计、轴承制造装备、高精度机械加工、检测与试验等一系列技术难题,还需要接触力学、润滑理论、摩擦学、疲劳与破坏、热处理与材料组织等基础研究和交叉学科的支持,高端轴承技术具有极端的复杂性,掌握难度非常之大。
目前国产轴承,相比于进口高端轴承,在精度、轴承振动、噪声与异音、可靠性、高速性能方面还有一定差距。
近年来,中国部分钢铁企业在高端轴承钢领域取得了一些技术突破。例如:
-
宝钢:宝钢集团在轴承钢领域进行了一系列技术攻关,推出了系列高性能轴承钢,如 GCr15 和 GCr15SiMn 等材料,这些材料广泛应用于高载荷、高精度轴承的生产。宝钢通过优化冶炼工艺、控制合金成分、精细化热处理工艺,提升了轴承钢的综合性能。
-
冶金研究院:中国冶金研究院在高端轴承钢的研发方面也取得了显著进展,成功开发了适用于高端轴承应用的高温轴承钢和高疲劳强度轴承钢,逐步解决了某些特种轴承钢的“卡脖子”问题。
-
长钢集团:长钢集团成功研发并实现了高性能轴承钢的工业化生产,解决了高温、低温环境下的轴承钢材料稳定性问题。
此外,国内轴承钢生产企业逐步掌握了高端轴承钢的制造工艺,如真空冶炼、精炼铸造、连续铸造等,显著提升了产品的质量和性能。尽管中国在高端轴承钢领域取得了显著进展,但在一些超高端应用领域,如航空航天、高速铁路、核电设备等,仍面临技术上的瓶颈。要彻底解决“卡脖子”问题,仍需要加大对先进冶炼技术、高温合金技术、表面处理技术等方面的研发投入。同时,国际竞争日益激烈,全球化背景下,如何提升自主创新能力,缩小与国际先进水平的差距,将是中国轴承钢产业面临的长期挑战。
航空钢材在航空航天领域扮演着至关重要的角色,主要用于制造飞机结构、发动机部件、起落架等关键组件。它们通常需要具备高强度、轻质、耐高温、耐腐蚀、抗疲劳等特性。
高温合金 航空高温合金(superalloy)是一种具有优异高温性能的材料,能够在600℃~1200℃的极端条件下长期工作。它广泛应用于航空航天和国防领域的关键部件,高温合金是航空发动机中涡轮叶片、燃烧室、导向叶片、涡轮盘等核心部件的首选材料,占发动机总重量的40%~60%。它直接决定了发动机的推重比、热效率和寿命,是航空发动机性能的核心保障。 以航空发动机涡轮叶片为例,这种核心部件通常采用单晶高温合金制成,需在高达1100°C的极端环境下长期承受高温、高压和高速旋转带来的复杂应力,同时抵抗氧化和腐蚀。其性能直接决定了发动机的推重比和使用寿命。然而,单晶高温合金的制造面临巨大技术难题,包括复杂的合金成分设计、晶体结构稳定性控制、微观缺陷消除以及高纯净度冶炼和精密铸造技术。目前,中国已自主研发第二代和第三代单晶高温合金并应用于部分航空发动机,但在单晶叶片的一致性和极限温度承受能力上,仍与国际顶尖水平存在差距。 超高强度钢 超高强度钢是用于制造承受较高应力结构件的一类合金钢。一般屈服强度大于1180MPa,抗拉强度大于1380MPa,这类钢一般具有足够的韧性及较高的比强度和屈强比,还有良好的焊接性和成形性。主要应用航空制造产业,而飞机起落架的制作材料,基本上都是300M超高强度钢! 飞机起落架是支撑飞机的唯一部件,尤其是在飞机降落阶段,其承载的载荷不仅仅来自机身重量,还有飞机垂直方向的巨大冲力。因此,起落架的材料强度必须十分优异,只能依靠特种钢材才行。目前使用范围最广的是美国的300M钢,该材料采用真空热处理技术,避免了渗氢,零件表面光亮,无氧化脱碳、增碳和晶界氧化等缺陷,提高了表面质量。而国内用于制作起落架的国产超强度钢材有时会出现点状缺陷、硫化物夹杂、粗晶、内部裂纹、热处理渗氢等问题,这些问题都与冶炼过程中纯净度不够有关系。所以我国在高纯度熔炼技术方面与美国还有较大差距,存在很大提升空间。 近年来,中国在航空钢材的研发和生产方面取得了显著进展。特别是在中低端航空钢材和一些高性能钢材的生产上,国内已经具备了较强的技术基础和产业能力。以下是中国航空钢材发展现状的几个关键点: 技术突破与产业化:中国航空工业集团公司(AVIC)和中国商飞公司(COMAC)等大型航空企业在钢材研发方面取得了突破,尤其是在基础航空钢材的国产化方面取得了积极进展。例如,国产飞机C919的制造中,已经开始应用一定比例的国产航空钢材,并逐步向高端钢材领域迈进。C919项目中的航空钢材应用:1)机身和机翼结构钢材:在C919的制造过程中,部分机身、机翼和支撑结构采用了国产高强度结构钢。例如,C919飞机的部分结构使用了由宝钢生产的高强度钢,满足了高强度、抗腐蚀和耐疲劳的要求。2)发动机零部件钢材:尽管C919的发动机部分关键材料(如涡轮叶片等)仍依赖进口高温合金,但在某些基础零部件上已经实现了国产化替代。中国航空工业集团公司(AVIC)旗下的研究所正在加大对高温合金、钛合金等航空发动机材料的研发力度,逐步实现国产替代。 关键合金钢的研发进展:国内钢铁企业如宝钢、鞍钢等在航空用钢的合金化设计、冶炼技术和热处理工艺方面不断取得进展。例如,宝钢成功研发了满足民用航空需要的2000MPa级别高强度结构钢,宝钢集团和中信特钢在汽车用钢领域研发出第三代AHSS,广泛用于汽车碰撞吸能部件和车身结构件,目前部分飞机零部件(如机翼、机身结构等)已经开始采用国产钢材。 产量和品种的提升:中国在航空钢材的品种上不断扩展,除了常规的碳钢和低合金钢外,高温合金、钛合金、铝合金等高性能合金的生产技术也逐步成熟,且开始向高性能钢材(如用于航空发动机的钢材)领域扩展。在高端航空钢和军用钢领域,已开发出30CrMnSiNi2A、40CrNiMoA等具有自主知识产权的材料。一些航空起落架钢和装甲钢的性能已接近国际先进水平,如300M(飞机起落架钢)的国产化率逐步提升。 超高性能需求领域: 航空发动机与高性能弹体钢:例如3000 MPa级别的钢材仍需依赖进口。 超大规格板材和异形钢:大尺寸、异形件的加工技术仍落后于发达国家,特别是在应力均匀性和性能稳定性方面存在差距。 工艺与设备不足: 超高强度钢对冶炼、轧制设备要求高,部分关键设备仍依赖国外进口。 热处理、焊接、表面强化工艺等仍需进一步优化。 中国在航空钢材领域的国产化替代取得了显著进展,尤其是在民用航空领域,C919等项目中已经实现了部分关键钢材的国产替代。随着技术的不断突破,中国航空钢材的国产化进程将继续推进,尤其是在高温合金、钛合金等高端材料的研发和生产上,国内企业正在加大投入,逐步缩小与国际先进水平的差距。然而,要完全解决“卡脖子”问题,还需要在高端航空材料的研发、生产工艺和应用领域加大技术创新和突破,特别是在航空发动机、涡轮叶片等关键领域的高性能钢材上,仍需长期努力。随着航空产业的不断发展和政策的持续支持,中国的航空钢材国产化替代进程有望在未来取得更加显著的成果。 高强度不锈钢和奥氏体不锈钢广泛用于航空航天、核能设备、医疗器械、化工设备等高端领域。然而,由于其对材料纯度、组织均匀性及性能稳定性要求极高,中国在高端生产工艺及质量控制上与国际先进水平仍有差距。例如,某些耐腐蚀性能极高的奥氏体不锈钢和超纯铁素体不锈钢依赖进口,尤其是在关键零部件中的应用。 高强度不锈钢在火箭发动机制造中发挥着关键作用,主要用于承受高温、高压和腐蚀等极端环境条件。用于火箭发动机的钢材需具备多种特性,其中高强度是必须满足的重要指标。然而,不锈钢的强度和防锈性能,却是鱼和熊掌般难以兼得的矛盾体。火箭发动机材料如果如果严重生锈,将带来很大影响。完全依靠材料自身实现高强度和防锈性能兼备,这是世界性难题。 目前,通过冶炼工艺优化、合金配方改进和质量控制技术,中国企业在提高高强度不锈钢的耐久性、抗腐蚀性和加工精度方面取得显著进展。例如,太钢不锈钢公司成功研发出满足航天器和发动机要求的高强度不锈钢,填补了国内空白。此外,X39CrMo17-1等不锈钢材料已在火箭发动机制造中得到应用,显示出国产化替代的可行性。 高强度不锈钢的国产化替代在多个领域已取得突破: 核电领域:核电站使用的核级高强度不锈钢已实现国产化。例如,太钢和中科院合作开发了具备高抗腐蚀性和高强度的核级不锈钢,用于核反应堆核心部件。 航空航天领域:用于航天器和发动机的高强度耐热不锈钢已逐步完成自主研发和生产。宝钢特钢开发的高强度不锈钢在航空发动机的特定部件中取得应用。 超薄精密箔材:太钢生产的0.02毫米不锈钢箔材在电子设备、医疗器械等精密制造领域实现了进口替代。 能源装备:国产高强度不锈钢在LNG(液化天然气)储罐和深海石油开采设备中得到应用,显著减少了对进口材料的依赖。 尽管取得了进展,但在高强度不锈钢的生产工艺、材料纯度和性能稳定性等方面,仍需持续努力。未来,应加强材料研发,提升生产技术,以满足火箭发动机对高强度不锈钢的需求,确保航天事业的安全与可靠性。 奥氏体不锈钢以其良好的耐腐蚀性、可加工性和美观性,在多个领域有着广泛的应用,包括食品加工、化工、建筑、汽车、航空航天和医疗器械等。它们通常用于需要高强度和耐腐蚀特性的场合。 难点: 加工难度:奥氏体不锈钢在加工过程中存在切削力大、切削温度高、加工硬化严重、容易粘刀和刀具磨损加快等问题。 技术壁垒:在某些高端应用领域,如超级奥氏体不锈钢,国外对我国进行了材料封锁,存在技术壁垒。 关键技术突破:超级奥氏体不锈钢的发展伴随着关键冶金技术的进步,包括炉外精炼技术和氮合金化技术。 316H奥氏体不锈钢已不折不扣地成为核电装备“卡脖子”材料。2019年1月1日,鞍钢集团有关领导组织召开316H奥氏体不锈钢生产动员会,并将316H奥氏体不锈钢开发确定为鞍钢“一号工程”。面对国家需求,鞍钢核电用钢项目团队结合合同全面承担了项目研发、生产及供货任务。在克服不锈钢研发、生产经验少,产品涉及单位众多、工序繁杂及技术指标要求严格等诸多不利因素情况下,充分发挥集团公司优势,依靠鞍钢联众、鞍钢铸钢公司、鞍钢股份,建立了该钢种适宜的生产工艺路线并成功实现产品开发和首批合同供货。 日前,鞍钢成功实现四代核电600MW示范快堆项目316H奥氏体不锈钢产品开发,并完成首批合同供货,解决了该产品从无到有的“卡脖子”难题。鞍钢因此成为全球唯一一家全部依靠自身装备生产该产品的企业。鞍钢集团的这一成就标志着中国在高碳奥氏体不锈钢的研发和应用上取得了重要进展,打破了国外技术垄断。 国产替代材料: 超级奥氏体不锈钢:酒钢不锈钢成功研发并批量稳定供货904L、254SMO超级奥氏体不锈钢中厚板和NO.1、2B全系列产品,替代了进口,提升了品牌影响力。 技术创新:河钢集团张宣科技特种材料研究制造生产现场,为某高端客户定向研制、可替代进口的超级奥氏体不锈钢气阀合金材料,关键性能优于客户标准要求。 随着我国近年来高铁的迅猛建设,钢轨养护问题也愈加让业内专家忧心。若养护不到位,不仅折损生命周期,还存在高风险隐患。铣刀作为钢轨维护的重要工具,成为了一个关键的“卡脖子”问题。铣刀主要用于对钢轨进行打磨和修复,以确保轨道的平整与稳定,保证高铁运行的安全和平稳。然而,由于钢轨的强度和硬度极高,这对铣刀的制造提出了非常高的要求。目前,全球范围内,铣刀的制造技术主要由德国和奥地利的公司垄断,国内还未完全掌握这一核心技术。我国自主创新研发的双动力电驱铣磨维护机器人装备——被称为钢轨‘急救车’的铣磨车可为钢轨“保驾护航”。但铣磨车最核心部件铣刀仍需从国外进口。铣刀的材料是一种超硬合金材料。对其中金属成分我们已然了解,但就是不知晓是怎么配比、合成的。国内企业虽已进行多次技术攻关,甚至尝试拆解进口铣刀进行学习,但仍未成功突破这一技术难关 由于建造钢轨的材料强度极高,这就决定了钢轨的强度,所以在制造时只能用铣刀对其打磨,而当它出现变形时也只能用铣刀对其进行矫正。目前,我国已经在加紧对这一项目的攻关, 中国五矿所属中钨高新金州公司突破0.01mm直径铣刀:2021年,中国五矿所属中钨高新金州公司成功突破了0.01mm直径铣刀的生产技术,解决了易折断、难监控等难题,为我国的工业制造提供了国产铣刀支持。这种极小径铣刀是目前世界上用于工业生产的最小的硬质合金铣刀,其直径仅相当于头发丝的八分之一,能够在头发丝上铣出字母,在米粒上铣出汉字,展现了极高的精度和强度。 四川天虎工具有限责任公司攻克“卡脖子”技术:四川天虎工具有限责任公司通过自主创新研发的铣刀攻克了高铁钢轨“整容”的“卡脖子”技术。该公司成功研发的钢轨在线修复铣刀打破了依靠国外进口的局面,让钢轨“急救车”的铣磨车用上了中国铣刀。 中国铝业公司铜合金双面铣国产化取得重大突破:中国铝业公司实施的铜合金双面铣削机刀具国产化取得重大突破,国产铣刀已替代进口刀具正常运行180余天,经检验获得成功。国产刀片完全可替代进口刀片,且维修方便,交货时间短,后续服务好,价格只有进口的25%左右。
我国合金粉末产品品种依然不足,中低端产品产能过剩和高端、高品位金属粉末依赖进口的矛盾日渐突出。尤其是粉末高温合金和粉末高速钢,目前应用于现代航空发动机、航天器和火箭发动机以及舰船和工业燃气轮机的关键热端部件材料(如涡轮叶片、导向器叶片、涡轮盘、燃烧室等)基本依赖进口,“卡脖子”问题日益突出。 粉末高温合金,是现代高性能航空发动机涡轮盘等关键部件的必选材料。与美欧、俄罗斯等航空强国相比,我国的民用航发刚起步,军用航发勉强交付。 真空雾化高温合金粉末 我国在粉末高温合金领域取得了很大的进步,部分粉末高温合金制件已获得应用。西北有色金属研究院等机构在粉末高温合金的研发和生产技术方面都取得了突破性进展,成功研发出新一代粉末高温合金,形成了成熟的粉末高温合金生产工艺路线。钢研高纳是国内最早开始研发和生产粉末高温合金制品的企业,目前已研制出10余种型号,其中FGH4091、FGH4095、FGH4096、FGH4097、FGH4098等粉末高温合金盘锻件满足了国家多个重点型号航空发动机的设计和应用需求,市场占有率达60%。钢研高纳为ODS高温合金领域龙头企业,市场占有率100%。氧化物弥散强化(ODS)高温合金是采用纳米氧化物对合金基体进行强化的一类特殊高温合金,具有优异的高温强度和抗氧化耐腐蚀性能。我国在粉末高温合金领域正通过技术突破和自主研发,逐步解决“卡脖子”问题,并在部分领域实现了国产替代,提升了国内粉末高温合金的竞争力和自给能力。 对于粉末高速钢,其良好的组织均匀性和碳化物无偏析特点,弥补了普通高速钢的先天缺陷,使钢材质量和性能得以全面提升。中国粉末冶金高速钢占高速钢比例仅0.3%,应用尚处于初级阶段,下游公司认知不足,市场尚未充分挖掘。根据我国高速钢年产量8-10万吨,我国粉末冶金高速钢市场需求1.5-2万吨,但国内产量仅300吨左右,显示出较大的市场空间。随着国内企业加大研发投入,提升产品质量和技术水平,逐步打破了国外企业的技术垄断,实现了进口替代。天工国际投资建设了国内首条工具钢粉末冶金生产线,设计年产量达2000吨,填补了国内供应空白,生产的粉末高速钢已取代进口,成功用于汽车、航空航天以及复杂刀具生产制造。国内粉末高速钢市场规模近年来保持稳步增长态势,从2014年增长至2023年,增幅明显。预计未来几年,市场规模将继续保持快速增长,成为推动中国制造业转型升级的重要力量。 据世界钢铁协会统计,2023年中国的粗钢产量为10.19亿吨,占全球粗钢总产量的比重达到53.86%,稳居全球第一,超过全球产量的一半。但是我国铁矿资源并不多,中国铁矿石对外依存度长期保持在80%左右,主要还是依赖进口。其中最优质的铁矿石来自两个国家,一个是澳大利亚,一个是巴西,其中澳大利亚每年的铁矿石产量占全球的80%。但自从我国进入钢铁市场之后,铁矿价格一路飙升,我国钢铁行业的成本一路飙升。这种高度依赖性使得中国在全球铁矿石价格波动中处于被动地位,容易受到国际市场价格波动的影响。 据了解,三井物产是日本财团三井的核心企业,三井的成员包括了新日铁这样的大型钢铁企业,也包括了丰田汽车这样的钢铁产品使用大户。中国的宝山钢铁甚至也和三井有密切的关系。力拓、必和必拓、淡水河谷世界三大铁矿石巨头,而三井物产与它们都建立了联合经营的关系,对于这些企业的经营决心有很大的影响力。所以说日本对“三大矿山”进行控股,铁矿价格提高,“三大矿山”盈利,日本也能从中分一杯羹,所以对于日本来说不论铁矿价格高低都是稳赚不赔的,而我国的钢铁企业就会受到损失。 好在我国的钢铁企业经过几十年的发展,在铁矿上的定价权也有举足轻重的程度。目前我国正在积极寻求从非洲、南美等地区进口铁矿石,以减少对澳大利亚和巴西的依赖。同时,国内加大了对低品位铁矿石的开发和利用,以提高国内铁矿石的自给率,还在积极推动铁矿石期货市场的建设,以提高市场的透明度和价格发现功能,通过这些措施,中国正在努力减少对外部铁矿石的依赖,增强自身的资源保障能力,并推动钢铁行业的可持续发展。 研究认为,我国海外建设优质铁矿项目不仅可以提升中国钢铁工业在成本、环保等方面的竞争力,而且将给项目所在国带来税收、就业、人才培养、基础设施建设及社会经济发展等方面的切实收益,实现双方的互利共赢。
免责声明:本网站所转载的文字、图片与视频资料版权归原创作者所有,如果涉及侵权,请第一时间联系本网删除。
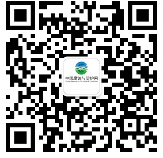
官方微信
《腐蚀与防护网电子期刊》征订启事
- 投稿联系:编辑部
- 电话:010-62316606
- 邮箱:fsfhzy666@163.com
- 腐蚀与防护网官方QQ群:140808414