高温合金的概念、原理和分类
高温合金通常是指能在 600~1200°C的高温下抗氧化、抗腐蚀、抗蠕变,并能在较高的机械应力作用下长期工作的合金材料。
高温合金强调的不是耐受温度指标,耐受温度比高温合金高的材料有很多,比如难熔合金、陶瓷及碳碳复合材料等。高温合金最根本的特性在于一定温度下所具有的高强度。以普通的建筑用钢材为例,它在室温下强度很高,但在建筑失火燃烧时强度会急剧下降,从而导致建筑坍塌。高温合金的好处是,在 600~1200°C的高温下,它依然能保持极高的强度和硬度以承受较高的载荷。因此俄罗斯将其称为热强合金,而欧美称之为超合金(superalloy)。
普通钢材含有十多种化学元素,而高温合金通常含有超过 30-40 种元素,高温合金之所以能在高温下保持较高的强度和硬度主要原因在于这些元素在组织中发挥着强化金属性能的作用。
高温合金的分类有多种:
1)按制造工艺分为变形高温合金、铸造高温合金和粉末高温冶金三类。
2)按合金的主要元素分为铁基高温合金、镍基高温合金和钴基高温合金三类。3)按强化方式分为固溶强化、时效强化、氧化物弥散强化和晶界强化等。
以工艺分类来看,变形高温合金应用范围最广,占比达 70%,其次是铸造高温合金,占比 20%。以合金主要元素来看,镍基高温合金应用范围最广,占比达 80%,其次为镍-铁基,占比 14.3%,钴基占比最少,占比 5.7%。
高温合金发展历程及概况
高温合金最早诞生于 20 世纪初期的美国,被用作车站的防腐支架。从二战开始,高温合金的研制进入了高速发展时期,镍基高温合金、钴基高温合金、铁基高温合金纷纷研制成功,并大量应用。
目前镍基高温合金是现代航空发动机、航天器和火箭发动机以及舰船和工业燃气轮机的关键热端部件材料(如涡轮叶片、导向器叶片、涡轮盘、燃烧室等),也是核反应堆、化工设备、煤转化技术等方面需要的重要高温结构材料。
高温合金的发展主要经历了几个阶段:二十世纪 40 年代以前提出概念,40-50 年代实现在喷气发动机的应用,50-60 年代在真空熔炼技术取得重大进展,60-70 年代集中在合金化方面,70 年代后主要在工艺研究方面,定向凝固、单晶合金、粉末冶金、机械合金化和陶瓷过滤等新工艺成为高温合金发展的主要动力,其中定向凝固工艺制备的单晶合金尤为重要,在航空发动机涡轮叶片中应用尤为广泛。
二十世纪 80 年代以来,国内外广泛开展数值模拟研究,取得了重要进展,并在此基础上开展了显微组织及冶金缺陷预测研究。
经过近一个世纪的发展,国外已拥有数十家实力强劲的高温合金研制企业,承温能力提升到 1140°C,已近金属材料使用温度极限。
镍基高温合金
在整个高温合金领域中,镍基高温合金占有特殊重要的地位,与铁基和钴基合金相比,镍基合金具有更好的高温性能、良好的抗氧化和抗腐蚀性能。镍基高温合金是高温合金中应用最广、高温强度最高的一类合金。
其主要原因,一是镍基合金中可以溶解较多合金元素,且能保持较好的组织稳定性;二是可以形成共格有序的 A3B 型金属间化合物[Ni3(Al,Ti)]相作为强化相,使合金得到有效强化,获得比铁基高温合金和钴基高温合金更高的高温强度;三是含铬的镍基高温合金具有比铁基高温合金更好的抗氧化和抗燃气腐蚀能力。可以说,镍基高温合金的发展决定了航空涡轮发动机的发展,也决定了航空工业的发展。采用定向凝固技术制备出的镍基单晶合金,其使用温度已接近合金熔点的 90%,成为当代先进航空发动机热端部件不可替代的重要结构材料。
镍基高温合金含有十多种元素,添加合金元素对高温合金的性能起关键的作用。以铸造镍基高温合金为例,铸造镍基高温合金以γ相为基体,添加铝、钛、铌、钽等形成γ‘相进行强化,γ’相数量较多,有的合金高达 60%;加入钴元素能提高γ‘相溶解温度,提高合金的使用温度;钼、钨、铬具有强化固溶体的作用,铬、钼、钽还能形成一系列对晶界产生强化作用的碳化物;铝、铬有助于抗氧化能力,但铬降低γ’相的溶解度和高温强度,因此铬含量应低些;铪改善合金中温塑性和强度;为了强化晶界,添加适量的硼、锆等元素。研究表明,GMR235铸态合金的含碳量为 0.18%时,高温持久寿命和抗拉强度最大,且具有较好的塑性,添加硼和锆的合金持久性明显改善,合金的枝晶间距减少,碳化物的析出量减少且碳化物颗粒细化,从而改善各方面性能。
镍基高温合金是 20 世纪 30 年代后期开始研制的。英国于 1941 年首先生产出镍基高温合金 Nimonic75;为了提高蠕变性又添加了铝,研制出 Nimonic80。美国于40 年代中期,苏联于 40 年代后期,中国于 50 年代中期也研制出镍基合金。
镍基合金的发展包括两个方面:合金成分的改进和生产工艺的革新。50 年代初,真空熔炼技术的发展,为炼制含高铝和钛的镍基合金创造了条件。初期的镍基合金大都是变形合金。50 年代后期,由于涡轮叶片工作温度的提高,要求合金有更高的高温温度,但是合金的强度高了,就难以变形,甚至不能变形,于是采用熔模精密铸造工艺,发展出一系列具有良好高温强度的铸造合金。60 年代中期发展出性能更好的定向结晶和单晶高温合金以及粉末冶金高温合金。为了满足舰船和工业燃气轮机的需求,60 年代以来还发展出一批抗热腐蚀性能较好、组织稳定的高铬镍基合金。在从 40 年代初到 70 年代末大约 40 年的时间内,镍基合金的工作温度从 700°C提高到 1100°C,平均每年提高 10°C 左右。
镍基高温合金按照制造工艺,可分为变形高温合金、铸造高温合金、粉末冶金高温合金。
变形高温合金
变形高温合金是高温合金中应用最广的一类,占比达到 70%。变形高温合金主要采用常规的锻、轧和挤压等冷、热变形手段加工成材。我国镍基变形高温合金以拼音字母 GH 加序号表示,如 GH4169、GH141 等。
变形高温合金塑性较低,变形抗力大,使用普通的热加工手段变形有一定困难,因而需要采取钢锭直接轧制、钢锭包套直接轧制和包套墩饼等新工艺来加工,也采用加镁微合金化和弯曲晶界热处理工艺来提高塑性。
铸造高温合金
随着使用温度和强度的提高,高温合金的合金化程度越来越高,热加工成形越来越困难,必须采用铸造工艺进行生产。另外,采用冷却技术的空心叶片的内部复杂型腔,只能采用精密铸造工艺才能生产,因此镍基铸造高温合金在实际生产应用中不可缺少。铸造高温合金应用也较为广泛,占比约 20%。国内的铸造高温合金以“K”加序号表示,如 K1、K2 等。
粉末冶金高温合金
随着耐热合金工作温度越来越高,合金中的强化元素也越来越多,成分也越复杂,导致一些合金只能在铸态上使用,不能够热加工变形。并且合金元素的增多使镍基合金凝固后成分偏析严重,造成组织和性能的不均匀。采用粉末冶金工艺生产高温合金就能解决上述问题。因为粉末颗粒小,制粉时冷却速度快,消除了偏析,改善了热加工性,把本来只能铸造的合金变成可热加工的形变高温合金,屈服强度和疲劳性能都有提高,粉末高温合金为生产更高强度的合金产生了新的途径。目前国内粉末高温合金已应用于先进型号发动机上的涡轮盘、压气机盘等重要部件上。
航发集团航材院生产的粉末涡轮盘及空心单晶叶片
高温合金的应用
涡轮喷气式航空发动机及燃气轮机
涡轮喷气式航空发动机是各类军机、民航客机及巡航导弹的动力装置。燃气轮机是现代大型军舰的首选动力装臵。在军舰动力方案选择上,燃气轮机的主要竞争对手是柴油机和蒸汽轮机,但是由于燃气轮机功率密度大、启动速度快、噪声低的先天优势与军舰动力系统性能要求更为吻合,因此燃气轮机成为了各国军舰动力系统发展的首要选择。燃气轮机和航空涡轮喷气发动机工作原理和核心机的结构组成基本相同,因此本节一并讨论。
高温合金在航空发动机中的应用情况
航空发动机高温合金结构件
火箭发动机
火箭发动机是运载火箭和弹道导弹的动力装臵,火箭发动机根据推进剂形态分为固体火箭发动机和液体火箭发动机。
固体火箭发动机中高温合金的使用量较少。固体火箭发动机结构相对简单,主要由药柱、燃烧室(壳体)、喷管组件和点火装置等四部分组成。在推进剂燃烧时,燃烧室须承受 2500~3500°C的高温,压力通常为 1~20MPa,一般采用高强度合金钢、钛合金或复合材料制造,并在药柱与燃烧内壁间装备隔热衬。
截至目前,固体火箭发动机壳体材料大体经历了四代发展过程,第一代为金属材料;第二代为玻璃纤维复合材料;第三代为有机芳纶复合材料;第四代为高强中模碳纤维复合材料。
由于固体火箭发动机结构简单,内部没有转动部件,且通常工作时间较短,因此尽管温度超高,但结构件承受的载荷较低,因此固体火箭发动机对兼具高温、高载荷、长时工作特性的高温合金需求较少。
固体火箭发动机和液体火箭发动机
我国高温合金的发展
我国高温合金的发展可分为三个阶段
目前世界上仅有 4 个国家形成自己的高温合金体系,分别为美国、英国、俄罗斯、中国。自 1956 年第一炉高温合金 GH3030 试炼成功,迄今为止,我国高温合金的研究、生产和应用已经历了 50 多年的发展历程。回顾 50 多年的历史,我国的高温合金从无到有,从仿制到自主创新,合金的耐温性能从低到高,先进工艺得到了应用,新型材料得以开发,生产工艺不断改进且产品质量不断提高,并建立和完善了我国的高温合金体系,使我国航空、航天工业生产和发展所需的高温合金材料立足于国内,也为其它工业部门的发展提供了需要的高温材料。
历经 50 多年的发展,我国已形成了生产装备比较先进、具有一定规模的生产基地。其中有变形高温合金生产厂:东北特殊钢集团抚顺特殊钢公司,宝钢股份公司特钢事业部和攀钢集团长城特殊钢公司;有锻件的热加工厂:西南铝业公司,第二重型机械集团万航模锻厂,中航工业宏远航空锻铸公司和安大航空锻造公司(均为中航重机子公司);有生产精密铸件的中国航发集团各航空发动机公司的精密铸造厂;也形成了一批研究水平较高、研究手段较齐备的科研单位:钢研高钠(原钢铁研究总院高温合金研究所)、航发集团北京航空材料研究院(621 所),中国科学院金属研究所,北京科技大学、东北大学、西北工业大学等。
高温合金市场容量
全球高温合金市场概况
2012 年,全球高温合金消费量为 28 万吨,占钢铁总消费量的 0.02%,市场规模达100 亿美元。高温合金的价格远高于其他钢铁品种,均价为 1.6 万美元/吨,用于航空航天的高端产品价格可达 3.6 万美元/吨,远高于不锈钢的 0.33 万美元/吨,粗钢的 0.07 万美元/吨。
高温合金被广泛应用于各个领域,其中航空航天领域占比一半以上,达 55%。其次是电力领域,占比 20%。
全球范围内能够生产航空航天用高温合金的企业不超过 50 家,主要集中在美国、俄罗斯、英国、法国、德国、日本和中国。发达国家一般将涉及航空航天应用领域的高温合金产品作为战略军事物资,很少出口。
可以看出,美、德、法、日为世界上高温合金的主要生产国。国内上钢五厂(即宝钢特钢),抚顺特钢产量位于全球前 30 位。但整体看,国内产量较低,合计不到全球产量的十分之一。
国内高温合金市场容量
2009 年,我国高温合金材料年生产量在 1 万吨左右,需求达 2 万吨以上。到 2013年,这一市场供给并未发生太大变化,但需求已增长至 3 万吨左右。截止 2016年,国内高温合金的产量已达 2 万吨左右。
2009 年我国航空航天、发电领域使用的高端和新型高温合金市场需求量在 3000余吨,在其后的 5~10 年内,每年呈 15%以上的速度增长。以此推算,保守估计 2017年航空航天、发电领域的高端高温合金市场需求已达 9000 吨以上。
国内军用高温合金市场容量测
国内高温合金领域最为确定的刚性需求来自于军机航空发动机、舰船燃气轮机及巡航导弹航空发动机方向。
目前全球民航机队中所使用的航空发动机基本被罗罗、GE、普惠(及其合资公司 CFMI、IAE)三大航发制造巨头垄断,其很少向我国的高温合金研制企业采购高温合金产品。而中航工业商发为我国自主研制的大飞机 C919 提供的发动机预计要2025 年服役。
因此短期内我国高温合金研制企业进入民航发动机领域阻力较大。而在军用航空发动机领域,由于军品的特殊性,国外企业进入国内军品市场存在天然壁垒。加之我国高温合金经过多年发展,已拥有多种对标国外高温合金的基础牌号,国外高温合金企业难以进入我国军用市场。
目前军工领域高温合金的应用方向主要为军机航空发动机、舰船燃气轮机及巡航导弹航空发动机。我们对军用高温合金的市场空间进行初步测算。
我国是目前世界上仅有 4 个形成自己的高温合金体系的国家之一
尽管与国外先进水平仍然存在差距,但从近年来的公开资料看,我国高温合金及其制品的研制生产单位已取得了巨大进步,当前的技术能力和生产水平基本能够支撑先进航空发动机、燃气轮机等产品型号的发展。
国内军工用高温合金母合金的主要供应商,上游母合金材料主要有传统优势企业抚顺特钢、钢研高钠、航材院、中科院金属所及其控股企业中科三耐以及新兴的民营企业图南股份等。精密铸造企业主要为钢研高钠、航材院、中航精铸,此外还有新兴企业图南股份、中科三耐、江苏永瀚等。锻件生产商主要有钢研高钠、中航重机旗下的陕西宏远和贵州安大、中国铝业旗下的西南铝业、中国二重旗下的万航模锻以及新兴企业无锡透平叶片、贵州航宇科技等。
免责声明:本网站所转载的文字、图片与视频资料版权归原创作者所有,如果涉及侵权,请第一时间联系本网删除。
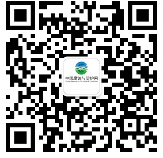
官方微信
《中国腐蚀与防护网电子期刊》征订启事
- 投稿联系:编辑部
- 电话:010-62316606-806
- 邮箱:fsfhzy666@163.com
- 中国腐蚀与防护网官方QQ群:140808414