图1. Microstructures of the Co-10Al-3Nb alloy after aging at 700°C for 168 h.
图2. The X-ray diffraction patterns of the Co-10Al-3Nb alloy aged at 700°C for 168 h.
图3. Temporal microhardness evolutions of the ternary Co-10Al-3Nb alloy aging at 700°C and 800°C, respectively.
图4. Representative SEM micrographs of grain boundary triple junction region of the (a) Co-15Ni-10Al-3Nb (15Ni) and (b) Co-30Ni-10Al-3Nb (30Ni) alloys after aging at 700°C for 168 h. Representative SEM micrographs of grain boundary triple junction region of the (c) Co-10Al-3Nb-30Ni (30Ni), (d) Co-10Al-3Nb-30Ni-2Ti (30Ni2Ti), (e) Co-10Al-3Nb-30Ni-2Ta (30Ni2Ta), and (f) Co-10Al-3Nb-30Ni-2Ti-2Ta (30Ni2Ti2Ta) alloys after aging at 800°C for 168 h.
图5. (a) The γ′-solvus and γ-solidus temperatures of the base, 15Ni, and 30Ni alloys. (b) The γ′-solvus, γ-solidus, and liquidus temperatures of the 30Ni, 30Ni2Ti, 30Ni2Ta, and 30Ni2Ti2Ta alloys. (c) The volume fraction of the γ′ phase among the Co-Al-Nb-based alloys at 800°C. (d) Microhardness evolutions of the Co-Al-Nb-based alloys after aging at 700 and 800°C for 168 h.
图6. Elemental partitioning coefficients of the multicomponent Co-rich alloys, showing Co partitioned to the γ matrix phase, whereas Ni, Al, Nb, Ti, and Ta partitioned to the γ′ precipitates.
图7. (a) SEM micrograph of the 30Ni2Ti2Ta alloy and (b) corresponding schematic diagram, showing that high-density γ′ precipitates divide the γ phase into nanoscale channels. (c) Ion maps of reconstructed nanotips by APT. (d) Proximity histograms across the γ/γ′ interfaces, showing distinctly different elemental compositions between the γ and γ′ phases.
图8. The plots between the yield strength and deformation temperature of the 30Ni2Ti2Ta alloy, together with other L12-strengthened Co-based alloys (Co-11Ti-15Cr, Co-9Al-9W, Co-30Ni-12Al-4Ta-12Cr, and Co-30Ni-10Al-5V-4Ta-2Ti alloys), a conventional carbide-hardened Co-based alloy (Haynes 188), and a commercial Ni-based superalloy (Waspaloy).
图9. Deformation mechanism of the 30Ni2Ti2Ta alloy after ?2% plastic deformation at room temperature.
图10. Deformation mechanism of the 30Ni2Ti2Ta alloy deformed at 700°C with a plastic strain of ?2%.
图11. Schematic diagrams of the deformed substructures at 25 and 700°C. Abbreviations: SF, stacking fault; SSF, superlattice stacking fault.
图12. Enthalpy formation energies of the L12-type Co3(Al, Nb) phase as a function of Nb concentrations.
图13. (a) Phase fraction of the L12 structure and the B2 structure as a function of Ni concentration in the Co-10Al-3Nb-xNi alloy. (b) L12 phase fraction as a function of temperature among Ti- and Ta-alloyed Co-10Al-3Nb-30Ni-based alloys.
图14. The critical resolved shear stress required for perfect dislocations gliding through the narrow matrix channels and dissociation into partial dislocations is plotted as a function of the stacking fault energy of the matrix phase. Various matrix spacings are considered in this plot to reveal the extra resistance from the geometric constraint to the movement of dislocations.
免责声明:本网站所转载的文字、图片与视频资料版权归原创作者所有,如果涉及侵权,请第一时间联系本网删除。
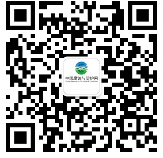
官方微信
《中国腐蚀与防护网电子期刊》征订启事
- 投稿联系:编辑部
- 电话:010-62316606-806
- 邮箱:fsfhzy666@163.com
- 中国腐蚀与防护网官方QQ群:140808414