香港城大刘锦川院士团队金属顶刊《Acta 》创新设计室温和高温均具有高强度的 L12 强化 Co-Al-Nb 基合金!
导读:本研究介绍了一种具有高 γ′-固溶线温度以及在环境温度和高温下均具有出色的强度的新型 L12 强化 Co-Al-Nb 基合金。三元Co-10Al-3Nb合金在700 ℃等温时效后发现L12-Co3(Al,Nb)相与γ-Co基体和B2-CoAl相平衡;然而,随着时效温度升高到 800 °C,它转变为 Laves 相。Ni的合金化添加有助于抑制B2相的形成,从而产生完全的γ-γ‘双相微观结构。Ti 和 Ta 元素进一步稳定了 L12 结构并将 γ'-固溶线温度提高到 1150 °C,而不会引起其他有害金属间化合物相的形成。新开发的 Co-Al-Nb-Ni-Ti-Ta 多组分富Co合金在环境温度和高温下均表现出出色的屈服强度,在 25 °C 和 700 °C 时分别达到 1023 ± 27 MPa 和 897 ± 53 MPa。此外,详细的电子显微镜分析揭示了独特的变形亚结构,其可塑性主要通过纳米级矩阵通道限制的堆垛层错进行。正如第一性原理计算所确定的,在环境温度下变形时没有粒子剪切,这归因于多组分γ’沉淀物的超高平面断层能。高密度超晶格堆叠断层剪切及其相互作用是导致 700 °C 屈服异常的原因。这些发现不仅提供了对 L12 强化合金变形行为的基本理解,而且证明了开发基于多组分富Co合金系统的下一代高温结构材料的巨大潜力。
Co-Al-W三元合金中γ′-Co3(Al,W)析出物的发现为在富Co合金体系中开发下一代高温结构材料提供了新的机会。利用有序沉淀进行强化需要强化剂在工作温度下是热力学稳定的。然而,据报道,L12-Co3(Al, W) 相在高温下是亚稳态的,在 900 °C 长期退火后分解为 B2-CoAl 相和 D019-Co3W 相。出于比较目的,在先进的镍基高温合金中,L12 型 Ni3(Al,Ti) 析出物在高达 1100 °C 时仍保持稳定。此外,优选由“γ-基体+γ‘-沉淀物”双相组成的优化微观结构,而不会形成其他有害的金属间相。然而,在三元 Co-Al-W 合金中添加的大多数四元合金往往会导致脆性金属间化合物相的形成。这些不希望的金属间相可能在拉伸变形过程中导致严重的脆化和灾难性的脆性断裂。此外,这种金属间相还会耗尽基体中的难熔元素,从而降低固溶强化的有效性。难熔元素的消耗也会加速γ′析出物的粗化速度。抑制整体γ′粗化有利于开发具有高热稳定性和长使用寿命的高温结构材料。因此,本研究专注于稳定γ' 析出物而不破坏Co 基合金系统中的γ-γ' 双相微观结构。
L12 型 Co3Al 相曾在 Co-Al 二元合金中作为亚稳相被发现。尽管如此,在 600 °C 时效时,Co-Al 二元合金更容易形成与γ-Co 基体平衡的 B2 型 CoAl 相的不连续沉淀。值得注意的是,据报道,VB 和 VIB 族的某些过渡元素(Mo、W、Ta、V)通过形成三元 L12-Co3(Al,X)(X = Mo、W、Ta)来稳定 L12-Co3Al 相, V) 相 。密度泛函理论 (DFT) 计算还证实,这些过渡元素有望促进 Co-Al 基合金中的 L12 有序化。以 Co-Al-W 三元合金为例,第一性原理计算表明,Co3(Al,W) 相在 0 K 时相对于 B2 型 CoAl 和 D019-Co3W 相不是平衡相。然而,Co3(Al, W) 相的稳定性得益于非零温度下的熵贡献。此外,在 L12 型 A3B 金属间化合物相中占据 B 亚晶格位置的过量 Co 并没有保持严格的化学计量比 (3:1),还增强了 Co3(Al,W) 相的稳定性。因此,Co-Al-X 体系(X 是 VB 或 VIB 族的过渡元素)有望用于设计新型 L12 强化 Co 基合金。值得注意的是,作为 VB 族的过渡元素,铌 (Nb) 有望沿着这一思路促进Co基合金中的 L12 有序化。事实上,在最近的 DFT 研究中已经报道了形成 L12 型 Co3(Al, Nb) 相的可行性。另一项早期工作也表明,L12-Co3(Al, Nb) 金属间化合物比 D019 型金属间化合物更稳定。除了这些理论计算之外,实验研究还表明,Nb 被分配到γ' 沉淀物中,并在钴基合金中充当γ' 稳定剂。值得注意的是,L12 结构的 Co3Nb 以前曾在 Co-Nb 二元合金中报道过,但只是作为仅在热处理早期形成的亚稳相。亚稳态 γ′-Co3Nb 相最终转变为 富Nb Laves 相,时效时间延长。总的来说,这些初步结果表明在 Co-Al-Nb 合金体系中形成有序 L12 沉淀物的潜力很大。
除了相稳定性外,在评估其工程应用潜力时,还应充分考虑质量密度。由于在 Co-Al-W 基合金中稳定 L12 相需要很大比例的高密度钨,因此它们的质量密度通常过高(例如,9.82 g cm-3 的Co-9Al-9.8W 合金)。因此,开发具有降低质量密度的无 W 钴基合金最近受到了优先关注。而且,Nb 的质量密度仅为 8.57 g cm-3,不到 W (19.3 g cm-3) 质量密度的一半。因此,设计新型无W的 Co-Al-Nb基合金可以有效降低质量密度,这为开发具有高比强度的新型结构材料开辟了一条潜在的有希望的道路。
香港城市大学刘锦川院士和杨涛教授等人系统地研究了利用有序 L12 析出物在多组分 Co-Al-Nb 基合金中进行强化的潜力。首次对三元Co-Al-Nb合金的相平衡、γ′-固溶线温度和微观结构稳定性进行了仔细研究。更重要的是,本研究还仔细研究了在环境温度和高温下均具有高强度的 L12 强化 Co-Al-Nb 基合金的创新设计。在环境温度下的塑性变形时,也揭示了由纳米级基质通道限制的堆垛层错组成的变形行为和相关的变形子结构。基于高密度超晶格堆叠故障的粒子剪切及其相互作用是导致 700 °C 屈服异常的原因。这些发现不仅促进了对 L12 强化合金变形行为的基本理解,而且证明了在多组分富钴合金系统中开发下一代高温结构材料的潜力。相关研究结果以题“L12-strengthened multicomponent Co-Al-Nb-based alloys with high strength and matrix-confined stacking-fault-mediated plasticity”发表在金属顶刊Acta Materialia上。
链接:
https://doi.org/10.1016/j.actamat.2022.117763
摘要图
图1 (a) Co-10Al-3Nb合金在700°C下时效168小时后的背散射电子显微图。(b)放大的晶界三联结区域的TEM显微图。代表性的“FCC+L12”双相区以黄色突出显示。如绿色箭头所示,B2型CoAl相可以沿晶界和晶粒内部找到。(c) 暗场TEM图像显示了排列良好的L12粒子。(d) 衍射图显示基体相的[011]区轴较长,B2型CoAl相的[1?13]区轴较长。L12超晶格点以黄色圆圈突出显示。(e) “FCC+L12”双相区的EDS图,显示Nb与L12颗粒之间存在强烈的分离。
图2 (a) Co-10Al-3Nb合金在700°C下时效168 h的X射线衍射图。(b)不对称(002)峰的去卷积,显示出属于FCC和L12相的峰。
图3 (a) Co-10Al-3Nb三元合金分别在700 ℃和800 ℃时效的时间显微硬度演变。(b) Co-10Al-3Nb合金在700 °C下时效336小时后的SEM显微照片显示,在整个γ-Co基体以及块状B2相中形成了纳米级L12型沉淀。(c) Co-10Al-3Nb合金在800 ℃下时效336小时后的SEM图像。随着时效温度升高至800°c,γ′-Co3(Al,Nb)相消失并转变为Laves相。
图4 (a)Co-15Ni-10Al-3Nb(15Ni)和(b)Co-30Ni-10Al-3Nb(30Ni)合金在700 °C下时效168小时后晶界三联区的代表性SEM显微照片。在15Ni合金的晶界处观察到微量B2相,而30Ni合金中保持了干净的γ-γ′双相显微结构。800℃时效168小时后,(c)Co-10Al3Nb-30Ni(30Ni),(d)Co-10Al-3Nb-30Ni-2Ti(30Ni2Ti),(e)Co-10Al-3Nb-30Ni-2Ta(30Ni2Ta)和(f)Co-10Al-3Nb-30Ni-2Ti-2Ta(30Ni2Ti)合金晶界三连接区的代表性SEM显微图。放大的晶粒内部显微图显示在相应的插图中。
图5 (a) 基体、15Ni和30Ni合金的γ′-固溶体和γ-固相线温度。(b) 30Ni、30Ni2Ti、30Ni2Ta和30Ni2Ti2Ta合金的γ′-溶质、γ-固相线和液相线温度。(c) 800 ℃时Co-Al-Nb基合金中γ′相的体积分数。(d)Co-Al-Nb基合金在700 ℃和800 ℃时效168 h后的显微硬度演变。
图6 元素分配系数Ki在多组分富钴合金中,镍、铝、铌、钛和钽被分配到γ′析出相,而镍、铝、铌、钛和钽被分配到γ′析出相。
图7 (a) 30Ni2Ti2Ta合金的SEM显微照片和(b)相应的示意图,表明高密度的γ′沉淀将γ相分为纳米级通道。(c)APT重建纳米尖端的离子图。(d)γ/γ′界面上的邻近直方图,显示了γ相和γ′相之间明显不同的元素组成。
图8 30Ni2Ti2Ta合金、其他L12强化钴基合金(Co-11Ti-15Cr、Co-9Al-9W、Co30Ni-12Al-4Ta-12Cr和Co-30Ni-10Al-5V-4Ta-2Ti合金)、常规碳化物硬化钴基合金(Haynes 188)和商用镍基高温合金(Waspaloy)的屈服强度和变形温度之间的曲线。
图9(a) 30Ni2Ti2Ta合金在室温下约2%塑性变形后的TEM亮场(BF)和暗场(DF)显微照片。高密度γ′沉淀被窄的基体通道分离。相应衍射图(插图)中的弱条纹线(由白色箭头突出显示)表明存在层错。利用条纹线拍摄DF显微照片,这些条纹线照亮了许多基体通道限制的层错。(b) 高分辨率TEM(HRTEM)图像显示了基质约束层错的近景。还显示了从γ′粒子(黄色方块)和含有层错的γ矩阵通道(蓝色方块)获得的快速傅里叶变换(FFT)衍射图。超晶格斑点用红色圆圈突出显示,表明γ′粒子的有序性质。在故障γ矩阵相位的FFT中可以发现条纹线(如白色箭头所示),这也证实了矩阵通道之间存在层错。(c) 典型的HRTEM图像显示,层错通过部分位错扩展受到γ′沉淀的阻碍,并在γ/γ′界面处停止。(d) 显示层错区原子结构的HRTEM显微照片。
图10 30Ni2Ti2Ta合金在700°C下变形的TEM显微照片,塑性应变约为2%。立方γ′沉淀(黄色方块)均匀分布在基体相上。如白色箭头所示,在基质通道中观察到高密度层错。在此温度下,通过超晶格层错(SSF)的粒子剪切被激活(蓝色箭头)。
从传统角度来看,异常屈服行为的开始可归因于APB耦合超部分位错的螺旋段从{111}到{100}平面的热辅助交叉滑移,导致商业镍基高温合金中形成Kear-Wilsdorf锁。在本研究中,我们观察到峰值温度下的高密度SSF剪切,而不是通过APB耦合位错对和相关的交叉滑移事件进行粒子剪切(图10)。主要部分位错滑动后形成的层错界面,为后续部分位错剪切提供了障碍。此外,SSF之间的相互作用导致了无柄阶梯杆位错组态,阻止了层错的进一步扩展。因此,屈服异常可以通过L12颗粒中密集的SSF相互作用和相关的硬化效应合理化。在高温压缩下,在Co-Ti-Cr合金中观察到类似的SSF剪切事件,这也导致了屈服异常。应注意的是,SSF剪切仅在高于峰值温度的温度下在Co-Al-W-Ta合金中被激活,这使得Co-Al-W-Ta合金在该温度区域保持其大部分强度。因此,更详细地了解独特的SSF基颗粒剪切是值得研究的,并进一步提高富钴高温合金的温度性能。
图11 25°C和700°C下变形子结构示意图。缩写:SF,层错;SSF,超晶格层错
图12 L12型Co3(Al,Nb)相的焓生成能是Nb浓度(0,3,6,10,15,20,25 at.%)的函数。
图13(a) 在Co-10Al-3Nb-xNi合金中,L12结构和B2结构的相分数是镍浓度的函数。(b) Ti和Ta合金化Co-10Al-3Nb-30Ni基合金中L12相分数随温度的变化。
图14理想位错滑过狭窄的基体通道并分解成部分位错所需的临界分辨剪切应力被绘制为基体相的层错能的函数。在该图中考虑了不同的基体间距,以揭示几何约束对位错移动的额外阻力。
这项研究证明了在多组分Co-Al-Nb基合金体系中设计新型高温结构材料的可行性。目前的研究结果可以总结为以下几点:
1)强调了三元Co-10Al-3Nb合金中L12-Co3(Al,Nb)沉淀的形成,在700 °C下与γ基体和B2-CoAl相平衡。Al和Nb优先分配给L12沉淀,有助于增强相稳定性。不幸的是,L12相转变为Laves阶段。随着时效温度升高至800℃,表明在三元Co-Al-Nb合金系统中,这种类型的L12沉淀的热稳定性不足。
2) 研究发现,几种合金添加剂有利于Co-Al-Nd合金的微观结构稳定性。合金化添加Ni抑制了B2相的形成,在不诱导脆性金属间化合物相形成的情况下形成了清洁的γ′-γ双相组织。Ti和Ta通过强烈分配到γ′沉淀中,被确定为有效的γ′稳定元素。这些元素显著提高了L12沉淀的热稳定性,并将改性后的Co-Al-Nb基合金中的γ′solvus温度提高到1150 ℃。这些关于L12-Co3(Al,Nb)相的热稳定性和Co-Al-Nb基合金之间的合金化效应的实验结果与第一性原理计算和热力学计算非常一致。
3) 新开发的多组分富Co合金在环境温度和高温下均表现出优异的强度,分别在25 °C和700 °C下达到1023±27 MPa和897±53 MPa。在整个温度范围内,富钴合金的强度甚至优于商用镍基高温合金Waspaloy。值得注意的是,在室温下变形时,纳米尺度的层错被几何限制在基体通道中,并作为主要的塑性载体。低层错能量矩阵和窄矩阵通道有望促进基体通道中高密度层错的形成。室温下没有颗粒剪切是由于多组分γ′沉淀的超高平面断裂能以及由此产生的对基体位错的高剪切阻力。在700 °C下应变后,观察到超晶格层错基粒子剪切的激活,其相互作用是该温度下屈服异常的原因。
免责声明:本网站所转载的文字、图片与视频资料版权归原创作者所有,如果涉及侵权,请第一时间联系本网删除。
相关文章
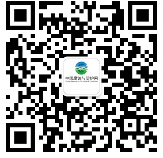
官方微信
《中国腐蚀与防护网电子期刊》征订启事
- 投稿联系:编辑部
- 电话:010-62316606-806
- 邮箱:fsfhzy666@163.com
- 中国腐蚀与防护网官方QQ群:140808414
点击排行
PPT新闻
“海洋金属”——钛合金在舰船的
点击数:7736
腐蚀与“海上丝绸之路”
点击数:6189