导读:本文采用一种新颖灵活的方法制备了Mg/Al复合材料板。采用冷喷涂的方法在AZ31B镁合金板上直接沉积7075铝合金粉末,从而得到结合良好的Mg/Al复合板材。然后对喷射态复合材料板进行热轧(HR)以进一步提高(轧制态)力学性能。从滚动方向(RD)和横向(TD)两方面系统研究了喷射态和轧制态Mg/Al复合板材的界面组织、织构演变、金属间化合物(IMCs)形成、力学性能和断裂行为。结果表明:CS + HR法制备的Mg/Al复合材料板的力学性能与传统滚接、爆炸焊和扩散焊等法制备的Mg/Al复合材料板相当,甚至优于后者。喷射复合材料板材在界面处表现出较强的剪切结合强度,这是由CS过程引起的。HR增强了Al-Al颗粒间的结合,导致AZ31B Mg层晶粒细化。此外,在HR样品界面形成条状分布的内膜细胞。结果表明,Al、Mg组份板以及复合材料板的极限抗拉强度(UTS)均有所提高,而剪切强度略有降低。并详细研究了复合材料板的裂纹萌生和扩展过程,以了解其断裂机理。
近几十年来,镁及其合金因其自身的优良性能而引起了人们的广泛关注密度低,比强度高,电磁屏蔽性能好。镁合金作为最轻的结构金属,在汽车、航空航天和电子工业中具有广泛的应用前景。然而,镁合金的主要缺点之一是耐腐蚀性能差,这极大地限制了镁合金的广泛应用。要解决这个问题,一个有效的解决办法就是制造Mg/Al复合板材,其中铝可以提供优良的耐腐蚀性能,通过在其表面自然形成致密的保护性Al2O3膜。
目前,制备Mg/Al复合材料板的方法有辊焊、爆炸焊、扩散焊、共挤、带铸等。显然,爆炸焊接和扩散连接可以形成良好的结合界面,具有较高的结合强度和较薄的IMCs。然而, 从生产效率、生产成本和环境保护等方面来看,这些工艺并不适合镁铝复合板材的工业化生产。辊式粘接是一种高效、经济、环保的粘接技术制造复合材料,适合大规模工业生产。但文献表明,在HR过程中,Mg/Al界面处不可避免地会形成脆性的IMCs(如Al3Mg2, Mg17Al12),使其力学性能下降。例如Nie et al.在400℃热轧后在200-400℃退火1-4 h制备了Al /Mg/ Al层压板,结果表明界面处形成的厚IMCs大大降低了粘结强度和塑性。此外,在辊粘接前,必须对配合面进行研磨,以去除表面氧化层。此外,原料板需要用铆钉或焊接固定在一起,以防止轧制过程中的相对运动。由于原料板之间缺乏预粘结,通常需要真空炉进行加热,以防止界面氧化。因此,上述问题限制了轧制结合技术在制备高质量Mg/Al复合材料板中的应用。
CS作为一种很有前途的用于多种材料的固态沉积技术,近年来受到了广泛的关注。在CS过程中,原料粉末在高压高温推进气体的加速作用下,受到基体或预沉积层的冲击。冷喷涂沉积的持续生长很大程度上依赖于颗粒-颗粒界面的严重塑性变形和绝热剪切不稳定性。在整个CS过程中,原料粉末的温度保持在其熔点以下,从而避免了氧化、相变和最终镀层的热应力。迄今为止,已成功制备出各种组织致密、力学性能优良的金属镀层。其中包括纯铜、铝、镍、锌等及其合金。
在前人工作的基础上,CS与HR相结合(CS+HR)已被证明是一种制备金属层合板的有效方法。Zhao et al.利用CS在钢板上沉积纯钛粉末成功制备钛/钢复合板,并研究了热轧和喷淋后退火处理对其组织和力学性能的影响。采用CS+HR法制备层合材料,可以很好地控制各组成金属层的厚度。此外,高速颗粒撞击(沉积过程中)可以打破基材和原料粉末表面的氧化膜。该冷喷层压复合材料不仅可以作为某一用途的成品,还可以作为轧辊粘接的中间产品。也就是说,可以用CS代替传统轧制工艺中的铆钉固定和焊接工序,实现各组成金属板之间的紧密无空洞结合。因此,在轧制过程中不再需要真空炉,避免了不必要的界面氧化。
据作者所知,目前还没有通过CS+HR制备Mg/Al复合板材的尝试。在此,中科院金属所Jiqiang Wang教授团队探索CS+HR制备商业应用的Mg/Al复合板材的可行性。研究了不同工艺条件下Mg/Al复合材料的RD和TD界面组织和力学性能。利用混合物规则(ROM)预测Mg/Al复合材料板的抗静电强度,并将预测值与实验值进行比较。并详细研究了复合材料板的裂纹萌生和扩展过程,以了解其断裂机理。相关研究成果以题“An innovative and flexible approach to fabricate Mg/Al composite plates: Cold spraying and hot rolling post-treatment”发表在金属顶刊Materials Science and Engineering: A上。
链接:https://doi.org/10.1016/j.msea.2022.143515
1.采用冷喷涂技术成功地制备了界面结合良好的(预粘合)Mg/Al复合材料板。7075 Al镀层与AZ31B Mg镀层之间形成了较强的机械联锁,这是由CS过程中的严重冲击引起的。喷射态Mg/Al复合板材的抗拉强度、EL强度和剪切强度分别为262 + 5.7 MPa、4.4 + 0.2%和127 + 6.5 MPa。
2.热轧后,板条分布的IMCs、新的结合界面和微孔交替分布在原始界面上。IMCs由AlsMg2和Mg17Al12组成。
3.热轧强化了Al-Al颗粒间的结合,导致AZ31B Mg层晶粒细化。结果表明,Al、Mg组份板及复合材料板(RD: 369 + 7.6 MPa, TD: 366 + 14 MPa)的抗压强度均有所提高。对于喷涂和轧制后的RD样品,Pre. UTS(由ROM预测)和Exp. UTS很好地一致。然而,As - Roll TD样本的Pre. UTS略低于Exp. UTS,因为ROM没有考虑到条带分布的IMC的影响。
4.断裂后,Mg/Al复合板材没有发生完全的分层,EL值始终保持在7075 Al和AZ31B Mg组份之间。由于7075层固有的低延性,裂纹最初产生于7075层的外表面,并向界面扩展。
图1 冷喷涂(a)和热轧(b)工艺的示意图。面板(c)显示了轧制时Mg/Al复合材料板的数字图像不同的观点。
图2 拉伸试样的原理图和精确尺寸(a)剪切(b)试验。
图3 7075原料的SEM显微图(a-c)和粒度分布(d)粉。图(e)为S1和S2的EDS点分析结果。
图4 ND-RD (c, d)和ND-TD (e, f)面喷射(a)和轧制(a) Mg/Al复合材料板的截面SEM图。图(b)显示了图(a)的EDS映射结果。图(g-i)显示了分别对新键合界面、IMCs和孔隙进行的EDS线扫描。面板(j)汇总了面板(d)和(f)的点分析结果。
图5 喷射态和轧制态Mg/Al复合材料板的XRD谱图界面区域。
图6 研究了喷射态(a, b)和轧制态(c, d) Mg/Al复合材料板沿界面分离的断口形貌。界面IMCs分布示意图(e)。
图7 图像质量图像(a, d),反极图(b, e)和极图(c, f)喷射态7075 Al镀层和接收态AZ31B Mg镀层图。
图8 图像质量图像和反向极点图取自于喷射时(a, d),轧制时RD (b, e)和轧制时RD (c, f)复合材料板的截面积。面板(g-i)显示了Mg层的极线图。
图9 不同工艺条件下Mg/Al复合材料板界面附近的维氏显微硬度分布:喷态(黑色)、轧制态(红色)和轧制态(蓝色)。图中为典型的7075 Al、AZ31B Mg和界面压痕的SEM图像。
图10 喷射态(a)、轧制态(b)、轧制态(c)复合材料板和薄板的典型工程应力-应变曲线。抗剪强度(d)与剪切粘结强度(e)的柱状图。
图11 拉伸试样的断裂形貌: 喷射态(a-d); 轧制态RD (e-h); 轧制态TD (i-l).
图12 不同应变水平下拉伸试样的OM截面图像,它代表了复合材料板的断裂过程:裂纹萌生(a)、裂纹扩展(b)和断裂(c)。
图13 剪切试样的断裂形貌:喷射态(a, d)、轧制态RD (b, e)和轧制态TD (c, f)。不同加工条件下的界面断裂示意图:喷射态(g)、轧制态RD (h)和轧制态TD
综上所述,首次采用冷喷涂与热轧相结合的工艺制备出了具有优良组织和力学性能的Mg/Al复合板材。研究了Mg/Al复合材料在不同工艺阶段的组织和力学性能。喷涂后的样品具有较高的剪切强度(127 + 6.5 MPa),这是由于其具有较强的机械联锁作用。热轧后,RD (78 + 6.9 MPa)和TD (124 + 4.6 MPa)的剪切粘结强度均有所下降。轧制态RD和轧制态TD试样剪切粘结强度的差异可能与内模组织的带材分布形态有关。
免责声明:本网站所转载的文字、图片与视频资料版权归原创作者所有,如果涉及侵权,请第一时间联系本网删除。
相关文章
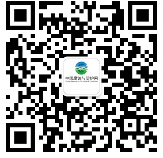
官方微信
《腐蚀与防护网电子期刊》征订启事
- 投稿联系:编辑部
- 电话:010-62316606-806
- 邮箱:fsfhzy666@163.com
- 腐蚀与防护网官方QQ群:140808414
点击排行
PPT新闻
“海洋金属”——钛合金在舰船的
点击数:8148
腐蚀与“海上丝绸之路”
点击数:6486