导读:近日,美国橡树岭国家实验室Richard A. Michi本综述了有关使用粉末基增材制造 (AM) 的几种具有潜力和前景的高温铝合金的现有文献。在此回顾了三类潜在高温合金的现有增材制造文献,讨论了优化微观结构以提高高温性能的策略,并强调了当前研究中的差距。尽管对这些合金进行了广泛的微观结构表征,但我们得出结论,对其高温机械性能和腐蚀响应的评估严重不足。将合金大致分为三类:具有热稳定强化相(HTPSA)的沉淀强化合金、含有高体积分数(>10%)金属间化合物(HiFI)的合金以及具有非反应性陶瓷颗粒分散体的合金(CDA)。研究认为大多数研究集中在加工、微观结构和环境温度机械性能上,但该领域在评估高温机械性能,特别是蠕变和疲劳以及高温氧化和腐蚀性能方面严重不足。此处引用的研究中只有约15%评估了高温机械性能。从性能和经济的角度来看,基于AM的高温铝合金都处于有利地位,可以填补250-450°C极端环境中结构材料长期存在的技术空白,并作者提出了一个强有力的建议。未来将重点放在这些领域,并在本次审查中概述了高温性能的几个重要考虑因素。
相关研究以题“Towards high-temperature applications of aluminium alloys enabled by additive manufacturing”发表在International Materials Reviews上。
链接:https://www.tandfonline.com/doi/full/10.1080/09506608.2021.1951580
AM HTPSA通常含有Zr/Sc,是迄今为止这三类中研究最全面的,有大量研究致力于加工/微观结构、热处理、机械性能(环境温度和高温)和腐蚀。合金的热处理和细化的晶粒结构导致出色的环境温度强度,但微观结构的稳定性尚不能与铸件相提并论。AM HTPSA 中强化析出物的总体积分数将受到可被困在基体中用于后续时效的最大溶质量的限制。然而,热处理优化仍有很多机会,包括原位热处理,提高高温强度和抗粗化性能。关于含有L12强化析出物的合金的大量铸造文献可能会为未来的研究提供灵感。
AM CDA的研究几乎仅限于加工,并且各种分散颗粒对高温机械性能的影响尚不清楚。由于陶瓷分散体在高达 Al 熔点的温度下具有固有的热稳定性,因此这类合金值得进行更全面的评估,包括高温强度和稳定性。此外,随着分散体体积分数的增加,应解决颗粒分布和团聚问题,因为这些可能是AM CDA强度的限制因素。
图1 常规锻造和时效铝合金的拉伸强度示意图,以及与Ti-6Al-4V具有相同比强度的铝合金的参考线。
图2 (a)在准静态条件下激光增材制造过程中形成的熔池示意图,其中激光沿速度矢量以恒定速度移动并显示了沿液相线等温线的代表性路径(白色箭头),也显示了(b)投影到y-z平面。沿着这条路径的凝固条件在(c)中示意性地表示在固-液界面速度V和合成热梯度的大小G中,并与柱状和等轴晶粒形成的示例预测进行比较。
图3 以Si和Zr作为示例溶质元素,Al中估计的速度相关分配系数。根据LPBF工艺条件,预计分配会在固液界面速度范围内发生很大变化。
图4 (a-d)用Zr/Sc改性的AM HTPSAs合金中的双峰“扇壳”晶粒结构示例。亚微米等轴晶粒带倾向于在MPB附近形成,在熔池中形成微米级柱状区域。图像是样品沿构建方向(z方向,参见e中的插图)的电子背散射衍射(EBSD)反极图(IPF)图。在(e)中使用ZrH2纳米颗粒功能化的原料粉末获得具有细化晶粒带的完全等轴结构。(a)Al-4.6Mg-0.66Sc-0.42Zr-0.49Mn;(b)Al-1.5Cu-0.8Sc-0.4Zr;(c)Al-5.8Zn-2.3Mg-1.6Cu-0.4Sc-0.25Zr以及(d)中等轴晶粒的详细信息;(e)Al-5.4Zn-2.25Mg-1.54Cu+1 vol.-%ZrH2纳米粒子。
图5 TEM显微照片显示了AM Al-3.6Mg-1.2Zr合金中细小等轴晶粒区域的细节。暗长方体是主要的Al3Zr,它们在熔池中形成并充当晶粒成核位点。
图6 原子探针断层扫描(APT)重建图(a)SLM处理的Al-2.5Zr-1.2Sc合金打印后下在350 °C下峰值时效24小时,Al3(Zr,Sc) 纳米沉淀物使用蓝色3 at.-%Zr+Sc等值面描绘;(b)铸造Al-0.27Zr-0.03Sc-0.03Er-0.10Si合金在640 °C下固溶2小时,然后在375 °C下进行峰值时效24小时,观察到Al3(Sc,Zr,Er)纳米沉淀物作为Zr、Sc和Er原子簇。(a)中纳米沉淀物的数量密度大于一个数量级(1×1024vs.9×1022 m-3),并且(a)中纳米沉淀物的体积分数是8倍以上(2.5vs.0.3%)。
图7 铸件上的单个激光轨迹 (a) Al-Fe-Ni(成分未指定),插图显示精炼金属间结构的细节;(b)Al-3Co(at.-%)和(c,d) Al-12Ce铸造合金。单轨熔池内的精细结构是明显的。(c)显示了Al-12Ce中MPB的细节,其中从粗铸结构过渡到细枝晶/蜂窝状结构。
图8 打印时大块MPB的粗金属间结构(a)Al-10Ce,(b)Al-10Ce-8Mn,(c)Al-8.5Fe-1.3V-1.7Si和(d)Al-8.6Cu-0.45Mn-0.9Zr。在(c)中,FZ是融合区。熔体边界区(MBZ)和热影响区 (HAZ)均包含该合金中的MPB区域,在该区域观察到显微组织粗化。
图9 LPBF制造的(a,c)Al-10Ce和(b,d)Al-2.5Fe合金沿构建方向Z成像的熔池结构和相应的晶粒取向图。晶粒结构主要是柱状,单个晶粒横跨多个熔池。单个熔池由(b)中的箭头表示。
图10 (a)HiFI合金和AA7075的温度与固化分数的Scheil凝固示意图。凝固后期温度的大幅下降促进了AA7075的热撕裂;(b)两种合金的凝固微观结构示意图,HiFI合金中的枝晶间区域填充了高体积分数的共晶。
图11 (a-b)添加2 wt-% 3.5-6 μm-TiB2颗粒显着改善了由LPBF制造的Al-12Si的柱状结构。(c-d)当0.5 wt-%100 nm LaB6粉末添加到Al-10Si-0.3Mg中时,可以看到类似的效果。插图表示沿构建方向的晶粒结构(a-b中的BD,c-d中的Z)。单个熔池由(c)中的白色虚线表示。(c,d)中的方框区域表示中附加晶粒结构分析的区域。
图12 (a)在SLM处理Al-10Si-0.3Mg和7.5 wt-%TiC期间熔池内流体流动的计算二维矢量场;(b) Al-10Si-0.3Mg基体中Al2O3颗粒的分布,考虑了Marangoni流动和反冲压力效应;(c)在多个激光轨迹和层之后产生的Al2O3的带状分布。
图13 带有Al-10Si-0.3Mg基体的打印CDAs中沿微观结构特征的弥散体收集示例;(a)15 wt-% 27 μm- Al2O3,(b)5 wt-% 50 nm-TiC,(c)2 wt-% 80 nm-TiN,(d)7 vol.-% 100 nm-TiB2(TiB2在用于粉末气体雾化的铸锭铸造过程中引入),和(e)1 wt-% 30 nm×30 μm碳纳米管。在(d)中,红色和蓝色箭头分别指向沿细胞边界分布并在细胞连接处聚集的TiB2。
图17 根据方程(7)-(11),以L12-Al3(Zr,Er)析出物为例,总粒子强化增量等值线图作为沉淀物/颗粒体积分数和平均半径的函数。(b)显示铸造和AM HTPSA所在区域的详细信息。注意从沉淀物的位错剪切到围绕沉淀物的位错循环的明显过渡区域。绘制了几种AM和常规加工合金,数据点的大小与粒子强化屈服强度的估计增量成正比。
图18. LPBF处理的(a)Al-4.52Mn-1.32Mg-0.79Sc-0.74Zr和(b)Al-10Ce-8Mn维氏显微硬度与时效时间和温度的函数关系。在(b)中还绘制了铸造Al-Cu-Mn-Zr (ACMZ)合金的数据以进行比较。
图20 LPBF Al-10Si-0.3Mg合金在300 °C和117 MPa 下进行(a、c)环境温度拉伸试验和(b-d)蠕变试验后的断裂表面。LPBF 加工的激光轨迹清晰可见,蠕变后明显有较大的空隙。
图21 与A 铝合金高温下疲劳裂纹萌生相关的微观结构特征:(a)近表面孔隙率,(b)缺乏熔合缺陷,(c)夹杂物/硬颗粒,(d)表面粗糙度,(e)持久滑移带,以及(f)熔池边界。
图22 影响含Zr/Sc的 AM HTPSA耐腐蚀性的因素汇总。(a-b)构造取向和晶粒结构对Al-4.2Mg-0.4Sc-0.2Sc腐蚀的影响;(c-d)在Al-4.2Mg-0.4Sc-0.2Sc的XY构建平面上形成了更高数量密度的较浅凹坑。坑清楚地勾勒出MPB;(e-f)热处理对 Al-14.1Mg-0.47Si-0.31Sc-0.17Zr腐蚀的影响,热处理促进深坑的形成。构建方向沿Z。
在突出显示的材料中,初始高温机械测试表明AM HiFI 合金显示出填补250-450°C技术空白的巨大希望。它们在微观结构上类似于快速凝固(RS)和粉末冶金 (PM)铝合金——迄今为止开发的最热稳定性和强度最高的高温铝合金——但不会受到相同的几何限制。迄今为止,研究是全面的,但数量有限。随着合金化学、加工参数以及机械性能和拉伸强度以外的高温行为评估的进一步修改,(例如蠕变、刚度、氧化)AM HiFI 合金有望实现RS和PM从未实现的商业承诺铝合金。
免责声明:本网站所转载的文字、图片与视频资料版权归原创作者所有,如果涉及侵权,请第一时间联系本网删除。
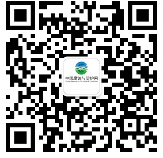
官方微信
《中国腐蚀与防护网电子期刊》征订启事
- 投稿联系:编辑部
- 电话:010-62316606-806
- 邮箱:fsfhzy666@163.com
- 中国腐蚀与防护网官方QQ群:140808414