蒸汽发生器热交换管是压水堆核电站中最重要的关键部件之一,其作用是将核电一回路的热量传到二回路。800合金作为蒸汽发生器合金的重要材料之一,它在一般情况下是自钝化的,因此耐蚀性较好。但在热交换管与支撑管板等局部的缝隙处,由于Cl-和S2O32-等杂质离子的积累,导致局部环境侵蚀性较强,易使钝化膜发生破裂,影响其服役寿命。近年来,蒸汽发生器合金在模拟局部缝隙中的腐蚀电化学行为成为了重要研究方向之一[1,2,3,4,5]。科研工作者主要围绕温度[6,7]、pH值[8,9]、杂质离子种类[10]等环境因子的变化对蒸汽发生器腐蚀行为的影响规律与机理开展了研究,其中包括S2O32-在内的还原态硫对蒸汽发生器合金的腐蚀被认为是引发应力腐蚀开裂的重要原因,要了解此环境下的应力腐蚀萌生机理,需对钝化膜再钝化动力学进行研究。
S2O32-作用下钝化膜再钝化过程被认为是在低温条件下进行的[11],而再钝化过程是影响孔蚀发展以及应力腐蚀开裂的关键步骤。划伤方法是研究钝化膜再钝化过程的重要手段[12,13]。本文主要采用划伤方法研究800合金表面钝化膜在模拟缝隙水化学中的再钝化过程,研究硫代硫酸根离子和应力对再钝化过程的影响,得到再钝化电流和再钝化时间等特征参数,为进一步研究应力腐蚀开裂奠定基础。
1 实验方法
实验材料为加拿大Sandvik公司提供的外径为15.88 mm、厚度为1.13 mm的800合金管,其化学成分为 (质量分数,%):C 0.017,Si 0.46,Mn 0.50,P 0.12,S 0.001,Cr 21.87,Ni 32.78,Co 0.10,Ti 0.48,Cu 0.02,Al 0.29,N 0.016,Fe余量。将合金管制成C形环试样以便进行加载,加载载荷为450 MPa,加载后的试样焊上铜导线并封装在环氧树脂胶泥中。制好的试样分别用400,800,1000,1500,2000目的砂纸打磨并进行抛光处理,露出面积为0.5 cm×2.5 cm的平整表面。然后用无水乙醇清洗,丙酮除油,放在干燥器中备用。
测试所用溶液按照加拿大原子能公司制定的模拟二回路缝隙水化学成分配置[8],如表1所示。其中NC2含有0.075 mol/L的S2O32-。NC1中不含有还原态硫─硫代硫酸根作为对照组。所有化学试剂由天津市元立化工有限公司,纯度为分析纯。模拟缝隙水化学溶液采用二次去离子水配置。
实验所用的划伤实验装置如图1所示。图1为划伤装置示意图,主要包括饱和甘汞参比电极 (含盐桥)、800合金工作电极、Pt片对电极以及氧化锆陶瓷针组成。陶瓷针装置设有压缩弹簧,利用该装置可控制每次划伤的长度相同,约为5 mm。划伤时间非常短,大约几个毫秒。
划伤测试前,800合金试样在溶液中静置30 min以形成稳定钝化膜,然后进行不同的钝化电位下的划伤实验。图2为加载后的800合金试样在NC2溶液中的极化曲线,钝化电位区间范围为-0.8~0 VSCE,因此选择-0.7、-0.6、-0.4和0 V等电位作为划伤时的钝化电位。不同电位下的划伤实验在不同样品上进行,采用PARSTAT2273电化学测试系统进行恒电位测试并记录电流的数据记录,实验至少重复5次。划伤后,用Hatchi S-4800场发射扫描观察划痕处的微观形貌。
2 结果与讨论
2.1 划伤过程的电流-时间曲线
图3给出了划伤过程中未加载和加载应力的试样在两种测试溶液中不同电位下的电流-时间曲线,所选的电位区间是钝化电位的范围。4种情况下,峰值电流均随着电极电位增加而升高,而划伤后的再钝化电流值增大,说明随着电极电位的正移,划伤部位的金属的溶解速度加快,再钝化过程越来越难。通过比较图3a和b,图3c和d,发现加载后,峰值电流增加,说明应力的增加导致划伤部位的金属溶解加快,这主要是由于对800合金C型环进行加载后试样外侧的拉应力可降低金属原子之间的结合能。通过比较图3a和c,图3b和d,发现硫代硫酸根的加入会增加金属的溶解速度,这主要是因为硫代硫酸根可在裸金属表面吸附还原,削弱金属原子之间的结合能,吸附的S离子可与Fe和Ni原子结合生成硫化物[14,15],而硫酸根则没有此作用。
图4给出了不同条件下的结果对比。图4a给出了不同条件下的电流峰值对比。加载应力的800合金在含硫代硫酸根的溶液中的电流值最大,说明硫代硫酸根会阻止再钝化过程。图4b给出了4种情况下钝化电位均为0 V时的电流时间曲线,明显看出施加载荷后再钝化电流值有所增加,加载试样在含硫代硫酸根的溶液中的再钝化电流值为0.35 mA·cm-2,而未加载的约为0.2 mA·cm-2,加载后再钝化电流增大了1.7倍。NC1溶液中再钝化电流只有0.05~0.07 mA·cm-2,说明硫酸根对再钝化过程的影响作用远远小于硫代硫酸根。
表2给出了不同情况下的再钝化时间对比,即划伤后电流值基本达到稳定所需的时间。施加应力后,在两种溶液中,划伤部位的再钝化时间均变长。-0.1 V钝化电位下,加载的800合金在NC2溶液中的再钝化时间最长。值得注意的是,0 V条件下,NC2溶液中,800合金无法长期钝化,极化时间15 min后,电流值迅速上升,出现孔蚀。
2.2 划伤后的表面形貌
图5给出了0 V电位下划伤部位的形貌。图5a和b给出了在NC1溶液中的划伤形貌,可以看出划伤部位无明显蚀孔,从电流时间曲线可以看出这两种条件下800合金划伤后仍然可以钝化。图5c和d给出了在NC2溶液中的划伤形貌,在此电位下,800合金无法长时间钝化,因此划伤部位出现均蚀孔;加载应力试样的腐蚀程度比未加载试样严重,主要是因为应力使原子之间的结合力降低,增加金属的溶解速度,从而使孔蚀发展速度变快。
NC2溶液中含有Cl-和S2O32-,两种离子对孔蚀有协同作用,且这种协同作用只发生在Cl-的吸附作用占主导的情况,即溶液中Cl-和S2O32-的比例必须足够高。此时,当电位较高时,Cl-主要作用是破坏钝化膜,使钝化膜破裂发生亚稳态点蚀,少量的S2O32-可电迁移至亚稳态点蚀区域,电化学还原成为吸附S,吸附在金属表面阻止再钝化,进而稳定亚稳态孔蚀,使钝化膜发生孔蚀。蚀孔内S2O32-的分解反应为:
Cl-和S2O32-的协同作用可发生在690合金[16]、304不锈钢[3]以及600合金[17]。另外,Cl-和S2O32-的比例对孔蚀发展速率有显著影响[18]。文献[18]采用原位形貌观察研究了800合金在室温条件下只含0.6 mol/L NaCl以及0.6 mol/L NaCl+0.075 mol/L NaS2O3溶液中的孔蚀发展速率,结果表明:只含Cl-时,蚀孔数量多、非常小,只有在扫描电镜下才可见;当含Cl-溶液中含少量S2O32-时,蚀孔数量少且尺寸大。造成这种差异的根本原因是:在Cl-环境中钝化膜易修复,因此孔蚀不容易发展,可导致其他区域继续发生孔蚀的萌生;当含有少量S2O32-时,由于形成吸附的S导致钝化膜不易修复,因此孔蚀发展速率较快[19]。
3 结论
(1) 采用划伤和电化学测试相结合的方法可有效的研究不同电位下金属表面钝化膜的再钝化过程。
(2) 硫代硫酸根的加入、应力的增加以及电极电位的升高均导致划伤过程的峰值电流和再钝化电流增加,表明金属溶解速度加快,再钝化过程变难。
(3) 硫代硫酸根阻止再钝化主要是因为其在裸金属表面还原成元素S,对孔蚀发展具有催化作用。
The authors have declared that no competing interests exist.
参考文献View Option
[1] Gao Z M, Wang Z Q, Sun Y H, et al.Passivity degradation of nuclear materials in reduced sulfur environments: A review[J]. Trans. Tianjin Univ., 2016, 22: 189
DOI:10.1007/s12209-016-2811-y URL
[本文引用: 1]
[2] Gao Z M, Lu X B, Xia D H, et al.Pitting corrosion mechanism of Alloy 800 in simulated crevice chemistries containing thiosulfate[J]. Electrochemistry, 2016, 84: 585
DOI:10.5796/electrochemistry.84.585 URL
[本文引用: 1]
[3] Mohammadi M, Choudhary L, Gadala I M, et al.Electrochemical and passive layer characterizations of 304L, 316L, and duplex 2205 stainless steels in thiosulfate gold leaching solutions[J]. J. Electrochem. Soc., 2016, 163: C883
DOI:10.1149/2.0841614jes URL
[本文引用: 2]
[4] Wang Y S, Wu G X, He L, et al.Effect of thiosulfate on metastable pitting of 304L and S32101 in chloride- and thiosulfate-containing environment[J]. Corrosion, 2016, 72: 628
DOI:10.5006/1955 URL
[本文引用: 1]
[5] Zakeri M, Naghizadeh M, Nakhaie D, et al.Pit transition potential and repassivation potential of stainless steel in thiosulfate solution[J]. J. Electrochem. Soc., 2016, 163: C275
DOI:10.1149/2.0381606jes URL
[本文引用: 1]
[6] Xia D H, Behnamian Y, Chen X Y, et al.A mechanistic study of sulfur-induced passivity degradation of Alloy 800 in a simulated alkaline crevice environment at 300 ℃[J]. J. Solid State Electrochem., 2015, 19: 3567
DOI:10.1007/s10008-015-2822-y URL
[本文引用: 1]
[7] Xia D H, Sun Y F, Shen C, et al.A mechanistic study on sulfur-induced passivity degradation on Alloy 800 in simulated alkaline crevice chemistries at temperatures ranging from 21 ℃ to 300 ℃[J]. Corros. Sci., 2015, 100: 504
DOI:10.1016/j.corsci.2015.08.026 URL
[本文引用: 1]
[8] Xia D H, Zhu R K, Behnamian Y, et al.pH effect on sulfur-induced passivity degradation of Alloy 800 in simulated crevice chemistries[J]. J. Electrochem. Soc., 2014, 161: C201
DOI:10.1149/2.063404jes URL
[本文引用: 2]
[9] Luo B, Xia D H.Characterization of pH effect on corrosion resistance of nuclear steam generator tubing alloy by in-situ scanning electrochemical microscopy[J]. Acta Phys.-Chim. Sin., 2014, 30: 59
[本文引用: 1]
[10] Lu B T, Luo J L, Lu Y C.Effects of pH on lead-induced passivity degradation of nuclear steam generator tubing alloy in high temperature crevice chemistries[J]. Electrochim. Acta, 2013, 87: 824
DOI:10.1016/j.electacta.2012.10.006 URL
[本文引用: 1]
[11] Zhang W, Carcea A G, Newman R C.Pitting of steam-generator tubing alloys in solutions containing thiosulfate and sulfate or chloride[J]. Faraday Discuss., 2015, 180: 233
DOI:10.1039/C5FD00008D URL
[本文引用: 1]
[12] Wang J Z, Li X H, Wang J Q, et al.Development of a scratch electrode system in high temperature high pressure water[J]. Corros. Sci., 2015, 95: 125
DOI:10.1016/j.corsci.2015.03.006 URL
[本文引用: 1]
[13] Wang J Z, Han E-H, Wang J Q.The repassivation kinetics study of Alloy 800 in high-temperature pressurized water[J]. Electrochem. Commu., 2015, 60: 100
DOI:10.1016/j.elecom.2015.08.017 URL
[本文引用: 1]
[14] Newman R C.Pitting of stainless alloys in sulfate solutions containing thiosulfate ions[J]. Corrosion, 1985, 41: 450
DOI:10.5006/1.3583826 URL
[本文引用: 1]
[15] Newman R C, Wong W P, Ezuber H, et al.Pitting of stainless steels by thiosulfate ions[J]. Corrosion, 1989, 45: 282
DOI:10.5006/1.3577855 URL
[本文引用: 1]
[16] Fang Z, Staehle R W.Effects of the valence of sulfur on passivation of Alloys 600, 690, and 800 at 25 ℃ and 95 ℃[J]. Corrosion, 1999, 55: 355
DOI:10.5006/1.3283997 URL
[本文引用: 1]
[17] Roberge R.Effect of the nickel content in the pitting of stainless steels in low chloride and thiosulfate solutions[J]. Corrosion, 1988, 44: 274
DOI:10.5006/1.3583937 URL
[本文引用: 1]
[18] Wu S B, Wang J Q, Song S Z, et al.Factors influencing passivity breakdown on UNS N08800 in neutral chloride and thiosulfate solutions[J]. J. Electrochem. Soc., 2017, 164: C94
DOI:10.1149/2.0541704jes URL
[本文引用: 2]
[19](夏大海, 宋诗哲, 王俭秋等。 690和800合金在高温高压水中硫致腐蚀失效研究进展[J]. 金属学报, 2017, 53: 1541)
Xia D H, Song S Z, Wang J Q, et al.Research progress on sulfur-induced corrosion of Alloys 690 and 800 in high temperature and high pressure water[J]. Acta Metall. Sin., 2017, 53: 1541
DOI:10.11900/0412.1961.2017.00198 URL
[本文引用: 1]
更多关于材料方面、材料腐蚀控制、材料科普等方面的国内外最新动态,我们网站会不断更新。希望大家一直关注中国腐蚀与防护网http://www.ecorr.org
责任编辑:王元
《中国腐蚀与防护网电子期刊》征订启事
投稿联系:编辑部
电话:010-62313558-806
邮箱:fsfhzy666@163.com
中国腐蚀与防护网官方 QQ群:140808414
免责声明:本网站所转载的文字、图片与视频资料版权归原创作者所有,如果涉及侵权,请第一时间联系本网删除。
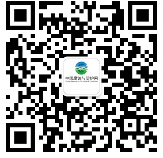
官方微信
《中国腐蚀与防护网电子期刊》征订启事
- 投稿联系:编辑部
- 电话:010-62313558-806
- 邮箱:fsfhzy666@163.com
- 中国腐蚀与防护网官方QQ群:140808414