断裂失效分析
金属断裂的基本概念
在机电装备的各类失效中以断裂失效最主要,危害最大。断裂失效的分析与预防已发展为一门独立的边缘学科。
目前对断裂行为的研究有两种不同的方法:
一种是断裂力学的方法,其根据弹性力学及弹塑性理论,并考虑材料内部存在有缺陷而建立起来的一种研究断裂行为的方法。
另一种是金属物理的方法,从材料的显微组织、微观缺陷、甚至分子和原子的尺度上研究断裂行为的方法。
断裂失效分析则是从断口的宏观、微观特征入手,研究断裂过程和形貌特征与材料性能、显微组织、零件受力状态及环境条件之间的关系,从而揭示断裂失效的原因。它在断裂力学方法和金属物理方法之间架起联系的桥梁。
断裂与断口
构件或试样在外力作用下导致裂纹形成扩展而分裂为两部分(或几部分)的过程称为断裂。它包括裂纹萌生、扩展和最后瞬断三个阶段。断裂形成的断面称为断口。断口上详细记录了断裂过程中内外因素的变化所留下的痕迹与特征,是分析断裂机理与原因的重要依据。
断裂分类
断裂可按具体的需要和分析研究的方便进行分类。
1 按断裂性质分类
根据零件断裂前所产生的宏观塑性变形量的大小分为:
塑性断裂,断裂前发生较明显的塑性变形。延伸率大于5%的材料通常称为塑性材料;
脆性断裂,断裂前几乎不产生明显的塑性变形。延伸率小于3%的材料通常称为脆性材料;
塑性-脆性混合型断裂,又称为准脆性断裂。
2 按断裂路径分类
依断裂路径的走向可分为穿晶断裂和沿晶断裂两类。在实际断裂失效断口上,多数情况是既有沿晶断裂,又有穿晶断裂的混合型断裂。
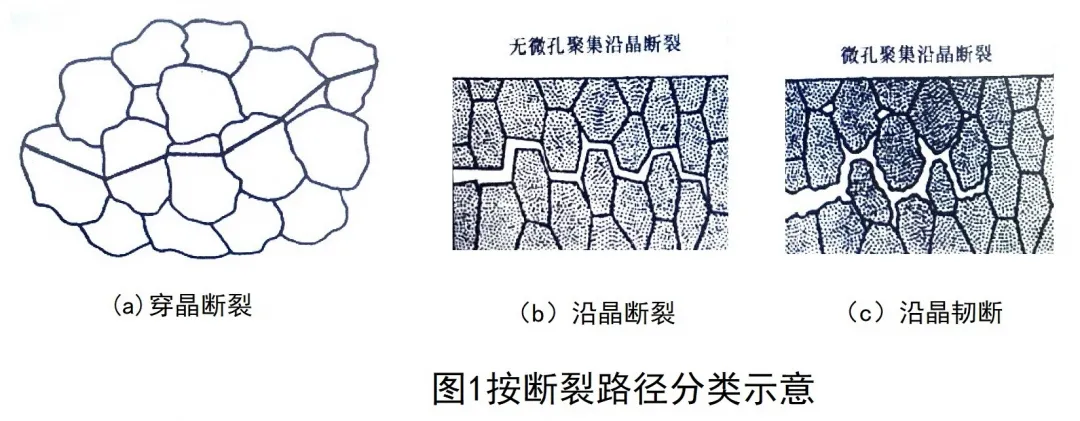
3 按断面相对位移形式分类
按两断面在断裂过程中相对运动的方向可分为:
张开型(Ⅰ型);
前后滑移型(Ⅱ型);
剪切性(Ⅲ型)。

4 按断裂方式分类
按断面所受的外力类型的不同分为正断、切断及混合断裂三种。
5 按断裂机制分类
可分为解理、准解理、韧窝、滑移分离、沿晶及疲劳等多种断裂。
6 其它分类法
可分为解理、准解理、韧窝、滑移分离、沿晶及疲劳等多种断裂。
按应力状态分类,可分为静载断裂(拉伸、剪切、扭转)、动载断裂(冲击断裂、疲劳断裂)等。
按断裂环境分类,可分为低温断裂、中温断裂、高温断裂、腐蚀断裂、氢脆及液态金属致脆断裂等。
按断裂所需能量分类,可分为高能、中能及低能断裂等三类。
按断裂速度分类,可分为快速、慢速以及延迟断裂三类。
按断裂形成过程分类,可分为工艺性断裂和服役性断裂。
过载断裂的宏观断口三要素
在金属光滑圆试样室温拉伸或冲击断口上,通常可分为三个宏观特征区,即如图所示的纤维区、放射区和剪切唇区。

图3光滑圆试样拉伸断口三要素示意图
使用断口三要素的应用案例:图4
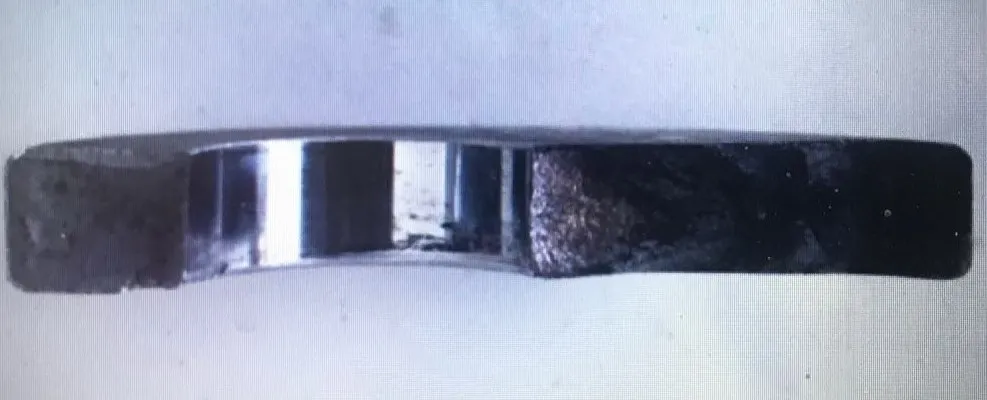
图4某飞机前起落架断裂耳片主、次两个断口
某型飞机起落架进行疲劳试验的过程中,试验耳片发生早期断裂。前起落架断裂耳片有两个断面剪切唇、放射区的人字纹特征明显。
断裂失效分析
金属断裂的微观机理与典型形貌
工程材料的显微结构都比较复杂,特定的显微结构在特定的外界条件下有特定的断裂物理机制和微观形貌特征。
穿晶韧窝断裂
韧窝是金属延性断裂的主要微观特征。韧窝又称作迭波、孔坑、微孔、微坑等。韧窝是材料在微区范围内塑性变形产生的显微空洞,经形核、长大、聚集,最后相互连接而导致断裂后,在断口表面所留下的痕迹。虽然韧窝是延性断裂的微观特征,但不能仅仅据此就作出断裂属延性断裂的结论。
1 韧窝的形成
韧窝形成的机理比较复杂,大致可分为显微空洞的形核、显微空洞的长大和显微空洞的聚集三个阶段。
2 韧窝的形状韧窝的形状
韧窝的形状主要取决于所受的应力状态,最基本的韧窝形状有等轴韧窝、撕裂韧窝和剪切韧窝三种。


滑移分离
金属断裂过程均起始于变形。金属的塑性变形方式主要有滑移、孪生、晶界滑动和扩散性蠕变四种。孪生一般在低温下才起作用;在高温下,晶界滑动和扩散性蠕变方式较为重要。而在常温下,主要的变形方式是滑移。过量的滑移变形出现滑移分离,其微观形貌有滑移台阶、蛇形花样、涟波等。晶体材料的滑移面与晶体表面的交线称为滑移线。滑移部分的晶体与晶体表面形成的台阶称为滑移台阶。由这些数目不等的滑移线或滑移台阶组成的条带称为滑移带。
滑移分离断口形貌
滑移分离的基本特征:断面倾斜,呈45°角;断口附近有明显的塑性变形,滑移分离是在平面应力状态下进行的。滑移分离的主要微观特征是滑移线或滑移带、蛇形花样、涟波花样、延伸区。
蛇形花样,多晶体材料受到较大的塑形变形产生交滑移,导致滑移面分离,形成起伏弯曲的条纹,通常称为蛇形滑移花样。
若变形程度加剧,则蛇形滑移花样因变形而平滑化,形成涟波花样。
如若继续变形,涟波花样也将进一步平坦化,在断口上留下了没有什么特殊形貌的平坦区,称为延伸区。
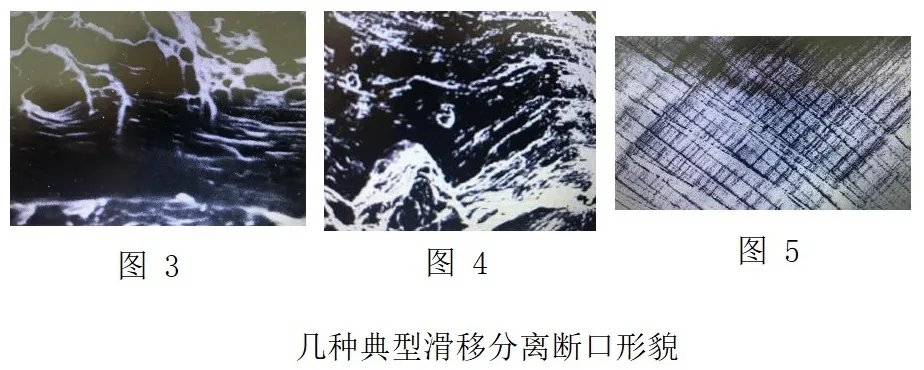
解理断裂
解理断裂是金属在正应力作用下,由于原子结合键的破坏而造成的沿一定的晶体学平面(即解理面)快速分离的过程。解理断裂是脆性断裂的一种机理,属于脆性断裂,但并不是脆断的同义语,有时解理可以伴有一定的微观塑性变形。解理面一般是表面能量最小的晶面。面心立方晶系的金属及合金,在一般情况下,不发生解理断裂。
解理断裂的形貌特征
典型的解理断口微观形貌有以下重要特征:解理台阶、河流花样、“舌”状花样、鱼骨状花样、扇形花样等。
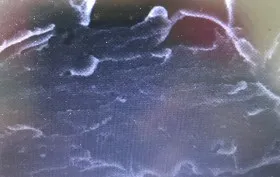
图6舌状花样
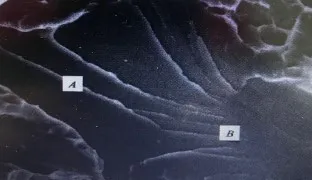
图7 典型的解理断口形貌特征 A台阶 B河流花样
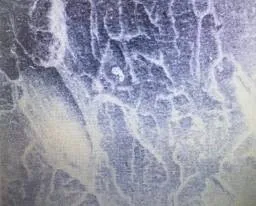
图8解理扇形花样
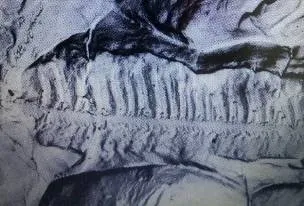
图9鱼骨状花样
某设备装配脱板螺母后发现有多个该型螺母在椭圆形收口处存在细小裂纹。裂纹附近未观察到塑性变形痕迹,裂纹较平直,由此说明裂纹开裂为脆性开裂。
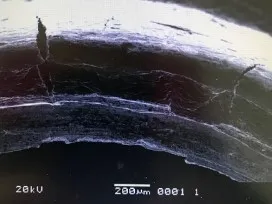
图10裂纹形态
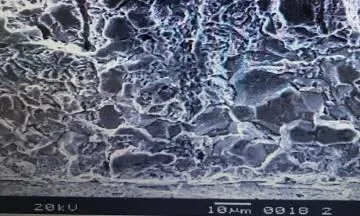
图11裂纹断口区域为解理+沿晶断裂的脆性断裂特征
准解理断裂
是介于解理断裂和韧窝断裂之间的一种过渡断裂形式。首先在不同部位,同时产生许多解理裂纹核,然后按解理方式扩展成解理小刻面,最后以塑性方式撕裂,与相邻的解理小刻面相连,形成撕裂棱。
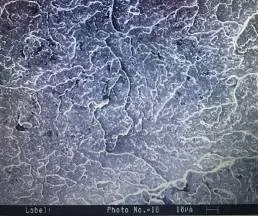
图12某设备十字槽扁圆头螺钉断口准解理断面形貌
准解理断口宏观形貌比较平整。基本上无宏观塑性或宏观塑性变形较小,呈脆性特征。其微观形貌有河流花样、舌状花样及韧窝与撕裂棱等。
案例:某厂设备弹簧发生断裂,断口如图呈准解理断裂形貌。
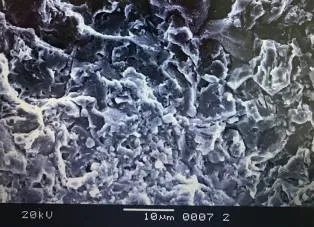
图13准解理断裂形貌
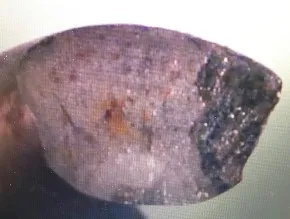
图14弹簧断口
沿晶断裂
沿晶断裂又称晶间断裂,它是多晶体沿不同取向的晶粒所形成的沿晶粒界面分离,即沿晶界发生的断裂现象。
按断面的微观形貌,通常可将沿晶断裂分为两类:沿晶韧窝断裂和沿晶脆性断裂。
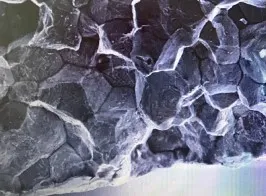
图15沿晶脆性断裂
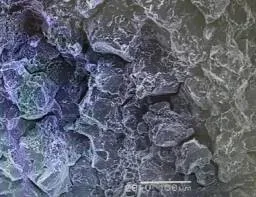
图16沿晶韧窝断裂
回火脆、氢脆、应力腐蚀、液体金属致脆以及因过热、过烧引起的脆断断口大都为沿晶脆性断裂特征;而蠕变断裂、某些高温合金的室温冲击或拉伸断口往往为沿晶韧窝形貌。
另外还有两种情况也属沿晶断裂范畴。一是沿结合面发生的断裂,如沿焊接结合面发生的断裂;二是沿相界面发生的断裂,如在两相金属中沿两相的交界面发生的断裂。
案例:
某发动机调试过程中,成功起动至慢车时,信号盘出“断开空调”信息,停车进行检查,发现空调系统中燃油—空气散热器出口处卡箍断裂(位置如图17)。
根据氢含量测定结果可知,钢带中的氢含量均远远高出一般钢中对氢含量的要求值,可以判断为氢脆导致沿晶断裂。
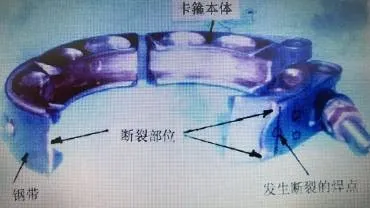
图17
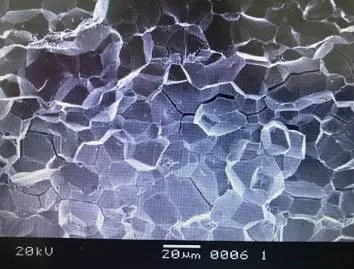
图18基体区域的沿晶断裂特征
疲劳断裂
1 定义
疲劳断裂是材料(或构件)在交变应力反复作用下发生的断裂。
2 疲劳断裂的危害性形状
多数机件承受的应力是周期性变动的;
疲劳破坏表现为突然断裂,断裂前无显著变形;
造成疲劳破坏时,循环交变应力中的最高应力一般远低于静载荷下材料的强度极限;
零件的疲劳断裂不仅取决于材质,而且对零件的形状、尺寸、表面状态、使用条件、外界环境等非常敏感;
很大一部分机件承受弯曲扭转应力。
3 疲劳断裂过程
疲劳裂纹的萌生、稳定扩展及失稳断裂三个阶段。
4 疲劳裂纹的萌生
交变载荷产生局部滑移→滑移线变粗形成滑移带→驻留滑移带的形成→驻留滑移带挤入槽和挤出峰的形成→萌生疲劳裂纹。
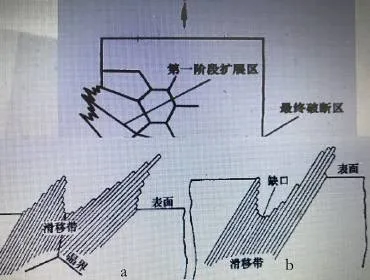
(a)在晶界附近起源 (b)在滑移带的缺口处起源
图19疲劳裂纹的萌生示意图
5 疲劳裂纹稳定扩展的两个阶段
疲劳裂纹稳定扩展第一阶段
与正应力呈45°,扩展深度很浅。
断裂形貌特征:
√类解理小平面
√平行锯齿状断面

图20叶片疲劳断裂第一阶段锯齿状断面
疲劳裂纹稳定扩展第二阶段
疲劳裂纹按第一阶段方式扩展一定距离后,将改变方向,沿着与正应力相垂直的方向扩展。此时正应力对裂纹的扩展产生重大影响。这就是疲劳裂纹稳定扩展的第二阶段,疲劳裂纹扩展第二阶段断面上最重要的显微特征是疲劳条带,又称疲劳辉纹。
6 疲劳条带的类型与形态
延性疲劳条带(晶体学和非晶体学)、脆性疲劳条带(晶体学和非晶体学)
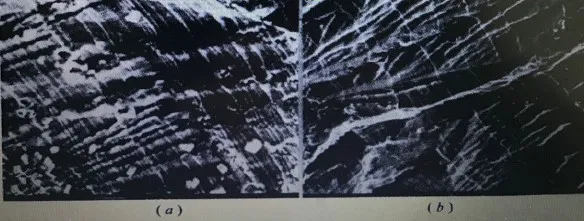
图21 a.延性疲劳条带 b.脆性疲劳条带
案例:某蓄压油箱疲劳裂纹
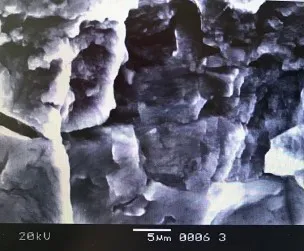
图22 源区处疲劳条带
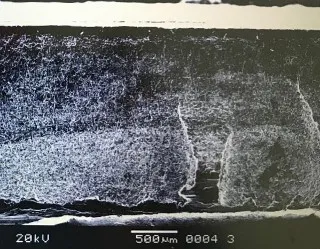
图23 源区位置疲劳弧线
断裂失效分析
疲劳断裂
分类

疲劳断裂的宏观分析
典型的疲劳断口按照断裂过程的先后有三个明显的特征区,即疲劳源区、扩展区和瞬断区。
01 源区的宏观特征
氧化或腐蚀严重,颜色较深;
断面平坦、光滑、细密,有些可见闪光小刻面;
有放射台阶或放射棱线;
向外发射疲劳弧线的中心。
02 扩展区的宏观特征
断面平坦、与主应力垂直,颜色介于源区和瞬断区,最基本的特征是疲劳弧线,也称海滩花样或贝壳花样。
03 瞬断区的宏观特征
与静载拉伸断口相近,瞬断区面积的大小取决于载荷的大小、材料的性质环境介质等因素。
案例:某电气控制盒固定脚焊缝附近断裂,断口可见疲劳弧线和源区的磨损特征,扩展较充分,瞬断区面积较小,断口具有典型的疲劳断裂特征。

图1 断口疲劳弧线与源处的磨损
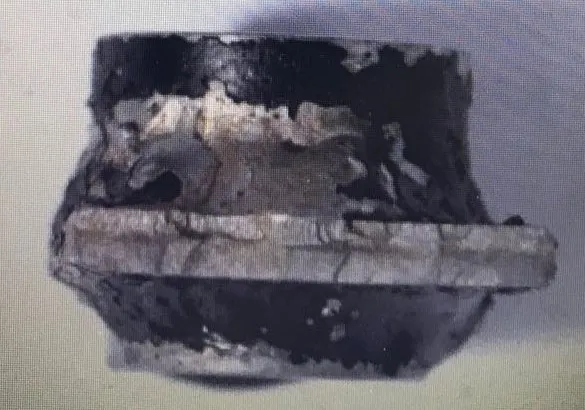
图2 断口宏观形貌
疲劳断口的微观分析
疲劳断裂的微观分析一般包括以下内容:
01 源区的微观分析
具体位置:多源疲劳:主源、次源;微观形貌特征:加工及材质缺陷
02 扩展区的微观分析
第一扩展区:有无疲劳条带、韧窝、台阶二次裂纹等;
第二扩展区:有无疲劳条带及疲劳条带的性质。
03 瞬断区的微观分析(韧窝形态)
低周疲劳断裂的判断依据
01 宏观特征
多源,且多为线状;
瞬断区面积大;
疲劳弧线间距大,稳定扩展区棱线粗、短;
断口高差较大。
02 微观特征
对低周疲劳,由于宏观塑性变形较大,静载断裂机理就会出现在疲劳断裂过程中,在断口上出现各种静载断裂所产生的断口形态。
案例:
某发动机的涡轮叶片和轮盘上多个榫齿出现了超过修理标准的裂纹,且裂纹部位基本上在第三齿,多数为单裂,少数为对裂,亦有邻裂的情况。
断口源区为穿晶滑移类解理断裂形貌,呈多源特征,扩展区主要为扇形解理扩展形貌和疲劳条带特征,为起始应力较大的以低周疲劳为主的疲劳开裂。
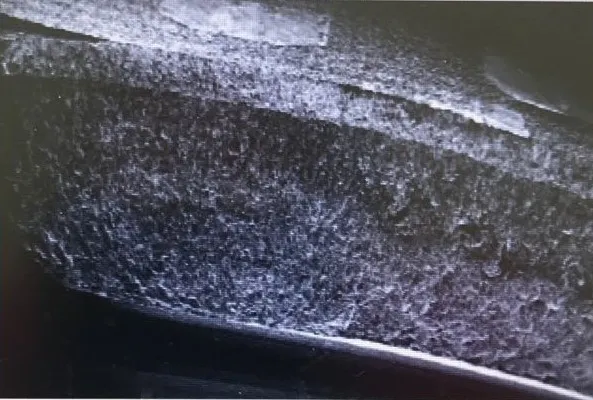
图3 叶片槽位处裂纹断口低倍
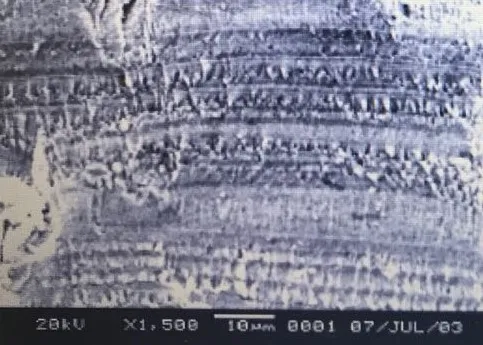
图4 扩展区载荷变化较大的条带特征
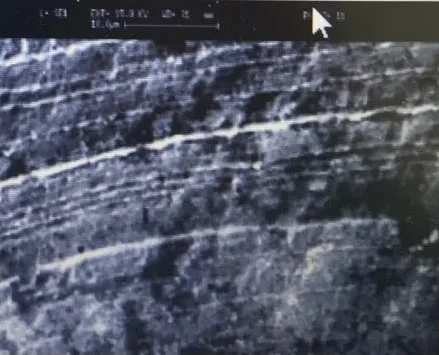
图5 据源区较远处条带特征
腐蚀疲劳断裂失效分析
腐蚀疲劳断裂是在腐蚀环境与交应载荷协同、交互作用下发生的一种失效模式。
01 腐蚀疲劳的断裂特征
断口低倍呈现明显的疲劳弧线;
源区和扩展区一般有腐蚀产物;
一般起源于表面腐蚀损伤处;
扩展区具有某些明显的腐蚀特征,如腐蚀坑、泥纹花样等;
穿晶解理脆性疲劳条带是其重要的微观特征;
若腐蚀损伤占主导地位,则断口呈现穿晶与沿晶混合型;
当Kmax> KIscc,在频率很低的情况下,其断口呈现出穿晶解理与韧窝的混合特征。
02 影响腐蚀疲劳断裂的因素
环境、受力状态、材质
03 腐蚀疲劳断裂失效分析的判断依据
交变应力和腐蚀环境;
断面灰暗、无金属光泽,有明显疲劳弧线;
有腐蚀产物和腐蚀损伤的痕迹;
疲劳条带多有脆性解理特征。
热疲劳断裂失效分析
零件在没有外加载荷的情况下,由于工作温度的反复变化而导致的开裂叫热疲劳。
热疲劳断口的形貌特征
01 热疲劳裂纹易产生于应变集中处;
02 光滑表面零件,则易产生于温度高,温差大的部位,可发现热疲劳裂纹发展极不规则,裂纹多为沿晶开裂;
03 微观形貌为韧窝和疲劳条带;
04 热疲劳裂纹附近,显微硬度降低。
断裂失效分析
沿晶断裂
金属零件的沿晶断裂大都归入脆性断裂失效范畴,主要包括热脆、低温脆、铜脆、回火脆、氢脆、应力腐蚀致脆、液态金属致脆等。
沿晶断裂失效模式的判别
01 金属零件沿晶断裂失效的主要宏观特征是:
断口的两匹配面很好地吻合一致,断口附近没有或极少有塑性变形,绝大部分断面结构粗糙呈颗粒状,称为“岩石状”断口、断面平齐,边缘无剪切唇、一般与主应力轴垂直;
断面无纤维状和放射状特征,一般看不出加载速度影响,且宏观上难以判明裂纹扩展方向;
02 沿晶断裂的典型微观特征是:
沿晶分离,晶界面光滑无特征,呈冰糖块状,或者显示撕裂痕和细小的韧窝花样。
沿晶断裂失效原因分析
产生沿晶断裂的原因除环境介质作用外还有以下3种情况:
01 晶界沉淀相引起的沿晶断裂
由晶界沉淀相所造成的沿晶断裂多是沿晶韧窝断裂。在晶界,沉淀相总是以分散粒子的形式存在,并且不连续;
合金的成分、热加工中的加热温度、冷却速度、热处理制度等都有可能引起第二相在晶界析出,弱化晶界,引起沿晶韧窝断裂;
引起沿晶韧窝断裂的主要因素有:微量元素引起第二相质点沿晶析出和缓冷引起第二相质点沿晶析出。
02 杂质元素在晶界偏聚引起的沿晶断裂
沿晶断裂的另一个主要原因是某些杂质元素在晶界上聚集,降低了晶界的聚合能,最常见的脆性杂质元素有Si、Ge、Sn、P、As、Sb、S、Se、Te等;
包括第一类回火脆引起的沿晶断裂和第二类回火脆引起的沿晶断裂。
03 金属过热、过烧引起的沿晶断裂
金属零件在热加工过程中,或使用过程中在过热、过烧温度区间内长期或短期停留,均会引起零件整件、或局部过热与过烧,从而在应力作用下导致沿晶脆性断裂;
过热、过烧断口宏观上呈粗大的颗粒状,无明显的断裂起源特征,断口附近无明显变形,过烧断口无金属光泽。过热断口微观形貌为晶粒粗大,晶界分离面上有细小的韧窝。过烧断口微观形貌为晶粒粗大,晶界粗而深,晶界分离面上有氧化膜、熔化的孔洞等特征。
故障概述
某活塞杆进行电镀后发现活塞杆表面中间部位存在裂纹。该活塞杆的工艺过程为:管材→机加→焊接→探伤→热处理→校正→机加→磁粉探伤→表面电镀处理(镀铬)→表面精加工→交工。一根活塞杆在外表面去镀后发现表面存在裂纹,另一根在外表面二次电镀后发现表面存在裂纹。活塞杆所用材料为30 CrMnSiA。
◆宏观观察
断口表面为黄褐色,锈蚀较严重。可见明显的从外表面向内表面的放射棱线特征。
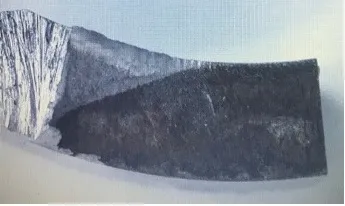
◆微观观察
裂纹起始于外表面,线源。源区局部为沿晶断裂特征,未见明显的冶金缺陷。

源区另一处放大后的形貌主要为龟裂特征,为典型的腐蚀产物特征;扩展区主要为沿晶断裂特征,存在大量的二次裂纹。

◆能谱分析
对活塞杆断口进行微区能谱分析,除二次电镀活塞源区沿晶处存在少量的CL元素外,两个断口上发生龟裂及裂纹扩展区均未发现腐蚀性元素存在。另外,整个断口上的Cr元素含量均高于钢自身的Cr含量(0.8~1.10wt%),且源区的Cr含量高于扩展区的Cr含量,说明断口受到了镀铬与去铬工艺的污染,裂纹应该在镀铬过程中已经产生。
◆金相组织检查
在断口附近制取试样,经腐蚀后在金相显微镜下观察,为回火马氏体组织,组织未见异常。
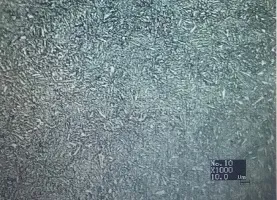
◆硬度检测:
平行于断口方向截取试样进行洛氏硬度检测,结果表
明活塞杆的硬度符合相关技术要求。
◆氢含量测定
在两个活塞杆裂纹打开断口附近截取试样进行氢含量测试,结果表明活塞杆的氢含量均低于0.1ppm
◆结果分析与讨论
★根据断口观察可知,两个活塞杆裂纹打开的断口均为典型的沿晶脆性断裂。
★能谱分析结果表明,两个活塞杆表面裂纹是在镀铬过程中产生的。
★断口观察源区未见明显的冶金缺陷,金相组织检查组织未见异常,说明裂纹的产生与材料本身质量无关。
★材料产生沿晶脆性断裂有三种可能原因:氢脆、液态金属致脆与应力腐蚀。根据氢含量测定可以看出,活塞杆氢含量均低于0.1ppm,30 CrMnSiA钢自身的强度不是很高,对氢脆不是很敏感,可以排除氢脆的可能;另外断口观察表明,断口上未见明显的低熔点金属,活塞杆在制备过程中也未曾与液态金属接触,所以也可以排除液态金属致脆的可能;两个活塞杆裂纹打开的断口观察表明,源区存在大量的龟裂特征,为典型的腐蚀特征,可以确定两个活塞杆表面裂纹是由于应力腐蚀所致。
★活塞杆采用30CrMnSiA制造,该材料对应力腐蚀敏感,在潮湿的空气中或腐蚀介质环境下极易产生应力腐蚀。断口表面存在大量的龟裂特征,说明其受到了腐蚀介质的作用。断口表面能谱分析只有源区局部存在腐蚀介质元素,可能是由于断口表面锈蚀较严重,影响了能谱分析的结果。
◆结论
裂纹位于活塞杆表面的中间部位,在活塞杆校正后此处存在较大的残余应力,在去应力退火时残余应力没有完全消除,在随后的电镀过程中发生了应力腐蚀。
◆故障概述
某厂生产的摇臂轴在装配后放置一段时间发现摇臂轴端部螺纹根部断裂。摇臂轴材料为20 CrMnTi。基本的机械加工及热处理过程为:锻造→粗加工→渗碳+直接淬火→局部(螺纹部分)高频回火→精磨→装配。
◆宏观观察
无明显宏观塑性变形,断口比较平齐,断面较粗糙,断口局部存在明显的擦伤形貌。断口上存在一个明显的弧形凸起台阶特征,将断口分为两部分。断口较平坦,裂纹从外表面呈线性起源,源区较平坦,呈黑色,与扩展区相比氧化较严重。从整个断口的宏观特征来看,断裂是从两部分区域外表面同时呈线性起源,并向心部扩展,最终两部分裂纹在中心附近区域交汇,形成断口上弧形的凸起特征。

◆微观观察
源区:裂纹均是起源于零件表层以下约几十个微米的次表面,呈线性起源特征,源区均呈典型的冰糖状沿晶断裂特征,晶面平坦,没有附着物,并且局部区域存在鸡爪形的撕裂棱线,二次裂纹较少。

扩展区微观形貌也均以沿晶断裂特征为主;交界区域附近断口存在少量的韧窝,并且可见二次裂纹特征。

◆能谱成分分析
结果表明断口表面无腐蚀性元素,断口上也未发现冶金等材质缺陷。
◆硬度测定
断口处硬度值在HRC35左右;断裂区域硬度值较高,与其组织有关。
◆氢含量测定
摇臂轴螺纹段的氢元素分布比较均匀,含氢量较高5ppm。
◆化学成分分析
符合GB/T3077的要求
◆分析与讨论
摇臂轴的化学成分符合要求,硬度值也符合零件设计要求,且摇臂轴断裂部位未发现材质缺陷,可以判断此次摇臂轴的断裂与材质无关。在摇臂轴断口上没有发现有腐蚀产物以及腐蚀性元素,也可以排除是由于应力腐蚀而造成摇臂轴断裂的可能。
●摇臂轴宏观断口无明显塑性变形,断口比较平齐,有放射花样;
●微观断口沿晶分离,晶粒轮廓鲜明,晶界面上伴有变形线(鸡爪痕),二次裂纹较少,撕裂棱较多;
●失效部位由于结构、装配以及加工刀痕等因素,存在应力集中,断裂源位于次表面;
●工作应力主要是静拉伸应力;
●摇臂轴断裂部位硬度偏高,造成强度偏高,对氢脆的敏感性增加;
●摇臂轴断口氢含量基本在5×10-6,达到了产生氢脆断裂的氢含量范围。
符合氢脆判定条件①、③、④、⑤、⑥、⑦
判断依据:
①宏观断口表面洁净,无腐蚀产物,断口平齐,有放射花样。氢脆裂区呈结晶颗粒状亮灰色;
②显微裂缝呈断续而曲折的锯齿状,裂纹一般不分叉;
③微观断口沿晶分离,晶粒轮廊鲜明,晶界面上伴有变形线(发纹线或鸡爪痕),二次裂纹较少,撕裂棱或韧窝较多;
④失效部位应力集中严重,氢脆断裂源位于表面;应力集中小,氢脆断裂源位于次表面;
⑤失效件存在工作应力主要是静拉应力,特别是三向静拉应力;
⑥氢脆断鲜明的临界应力极限随着材料强度的升高而急剧下降;一般硬度低于HRC=22时不发生氢脆断裂而产生鼓泡。
⑦一般钢中的含氢量在(5-10)×10-6以上时就会产生氢致裂纹,但对高强钢,即使钢中含氢量在1×10-6以下,由于应力的作用,处在点阵间隙中的氢原子会通过扩散集中于缺口所产生的应力集中处,氢原子与位错的交互作用,使位错线被钉扎住,不能再自由活动,从而使基体变脆。
发生氢脆断裂必须同时具备三个条件:一定的氢含量,对氢脆敏感的组织,一定的拉应力。
▲摇臂轴的氢脆断裂氢的来源于渗碳热处理过程中,是由于甲醇和丙酮在高温下分解形成氢原子,且氢在金属中的溶解度随着温度而变化,当温度降低或组织转变,氢的溶解度由大变小时,氢便从固溶体中析出,而由于冷却速度较快,就会残留在金属材料基体中。
▲通过金相组织观察可知,发生断裂的位置仍为马氏体组织,而且其硬度和强度均较高,而随着强度的升高材料对氢脆断裂的敏感性必然增大,因此,从这个角度说摇臂轴也具备了发生氢脆断裂的条件。
▲摇臂轴断裂位置正好位于螺纹与花键的圆弧过渡处,该处应力集中较大,无论是加工过程中的残余应力还是装配时的装配应力都会在该处产生应力集中,使零件实际受力增大,而且零件装配应力在该处也属于拉应力
◆改进措施
●降低材料内部的氢含量:加大除氢时间改进渗碳工艺,如渗碳后空冷,再重新进行加热淬火,这样渗碳时产生的氢就会在淬火加热时从材料内部析出,这样改进后零件材料内部的氢含量会大大降低,从而也会使其发生氢脆的可能性减小。
●减小应力集中:从零件加工角度考虑,应尽量提高加工精度,从而降低该处的应力集中,这样也会大大降低该处发生氢脆断裂的几率。
●应从设计和生产两个方面进行综合治理,一方面在工艺设计上进行改进,另一方面加强生产过程的质量控制。
免责声明:本网站所转载的文字、图片与视频资料版权归原创作者所有,如果涉及侵权,请第一时间联系本网删除。
相关文章
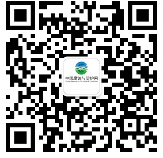
官方微信
《中国腐蚀与防护网电子期刊》征订启事
- 投稿联系:编辑部
- 电话:010-62316606-806
- 邮箱:fsfhzy666@163.com
- 中国腐蚀与防护网官方QQ群:140808414
点击排行
PPT新闻
“海洋金属”——钛合金在舰船的
点击数:7130
腐蚀与“海上丝绸之路”
点击数:5741