摘要
采用超音速火焰喷涂技术在T91钢表面制备了45CT、NiCr/Cr3C2和NiCrAlY 3种涂层。在T91钢和3种涂层表面涂覆37.5%Na2SO4+37.5%K2SO4+15%Fe2O3+10%SiO2的合成煤灰后通入模拟烟气在750 ℃下进行腐蚀,获得腐蚀动力学曲线,腐蚀200 h后观察涂层腐蚀前后厚度变化。采用XRD、SEM、EDS对高温腐蚀产物成分、结构、形貌进行分析。结果表明,T91钢腐蚀非常严重,腐蚀产物大量剥落。3种涂层在腐蚀前期均表现为增重,而在腐蚀后期均存在失重现象。经过200 h腐蚀后,45CT、NiCr/Cr3C2和NiCrAlY涂层分别减薄25、112.7和93.1 μm。T91钢腐蚀后表面残留的腐蚀产物主要为Fe2O3。45CT涂层表面主要的腐蚀产物相为Cr2O3,而NiCr/Cr3C2和NiCrAlY的腐蚀产物为Cr2O3和NiCr2O4。所有样品表层腐蚀产物中不同程度均嵌入了煤灰粒子。腐蚀介质会通过涂层扩散到涂层/基体界面导致基体一侧发生腐蚀。45CT、NiCr/Cr3C2涂层样品基体处腐蚀严重导致涂层/基体开裂,而NiCrAlY涂层由于孔隙率较低,以及稀土效应,界面的基体侧腐蚀轻微,未出现裂纹。
关键词: 45CT ; NiCr/Cr3C2 ; NiCrAlY ; 热喷涂涂层 ; 热腐蚀
我国是全球第二大电力生产国及电力消费国,因此以火电为主的电源结构在相当长的一段时期内会保持不变。蒸汽参数越高,热力循环效率越高。提高燃煤发电机组的蒸汽参数是提高机组效率的重要手段[1]。大力发展大容量、高参数值的超超临界燃煤技术已成为我国实现节能减排目标的一种重要手段,也是我国火电机组的主要发展方向[2]。在超超临界电站锅炉中水冷壁、过热器及再热器工作环境苛刻,易发生热腐蚀,影响电站锅炉的正常运行。由此可见,锅炉水冷壁、过热器管和再热器管的防护是锅炉安全服役的重要保障[3]。
目前,热喷涂抗高温腐蚀涂层是锅炉水冷壁等向火侧部位防护的重要手段,性能良好的热喷涂涂层可显著延长设备的服役寿命,同时降低成本,提高工作效率[4]。目前广泛使用的45CT涂层抗硫化物腐蚀能力为碳钢的60倍。在接近980 ℃的高温下抵抗锅炉工作中产生的腐蚀性气体 (S,V) 的侵蚀[5];NiCr/Cr3C2涂层具有耐高温、耐氧化、耐腐蚀、耐高温磨损和耐高温冲蚀等优点,尤其在提高工件表面的耐磨性能方面具有显著优势;NiCrAlY涂层广泛地被用作航空发动机抗氧化涂层或热障涂层 (TBC) 基体与陶瓷涂层间的粘结层,具有硬度高、抗氧化性能好,热膨胀系数与高温合金及陶瓷接近等优点[6]。我国发电锅炉使用的部分燃煤中硫和碱金属含量较高[7],燃煤高温燃烧过程中会生成硫酸盐及含硫气体。当硫酸盐中同时含有Na2SO4、K2SO4和碱金属氧化物时,在高温下会形成低共熔晶体,当复合硫酸盐中的Na与K的摩尔比在1∶1与1∶4之间时,盐的熔点可低至552 ℃[8]。上述热喷涂涂层能够提高金属在硫酸盐中的抗腐蚀性能[9],但长期服役过程中涂层也会逐渐失效。
燃煤锅炉向火侧服役环境复杂,气氛和表面沉积盐成分也有差异,目前报道的锅炉防护涂层的测试环境各异,涂层耐蚀数据的可比性差。本文针对我国高硫煤燃烧过程在水冷壁产生熔融态盐及含硫气体环境,对比研究了45CT、NiCr/Cr3C2和NiCrAlY 3种涂层涂覆模拟煤灰在0.3%SO2气氛中的腐蚀行为,对比了3种涂层耐蚀性,探讨了涂层腐蚀和失效机理,可为锅炉表面热喷涂选材提供依据。
1 实验方法
实验样品基体材料为T91钢,其尺寸规格为25 mm×15 mm×5 mm。样品热喷涂前在酒精、丙酮中清洗后采用压缩空气对样品表面进行喷砂处理至Sa2.5级,并采用洁净N2气将喷砂后的表面吹洗干净,然后将试样放入120 ℃烘箱中预热2 h待热喷涂。采用超音速火焰喷涂技术在试样表面喷涂45CT、NiCr/Cr3C2 (质量比为1∶3) 和NiCrAlY涂层,3种涂层粉末材料名义成分见表1。每种涂层均有3个平行试样。超音速火焰喷涂采用JP8000喷涂系统,以航空煤油作为燃料气体,以氧气作为助燃气体。喷涂厚度为450~550 μm。工艺参数为:O2流量 815.0 L/min,煤油流量0.45 L/min,载气流量 (N2) 10.5 L/min,送粉55 g/min,枪距345 mm,线速度500 mm/s。喷涂后采用金相法测定涂层的孔隙率,45CT、NiCr/Cr3C2和NiCrAlY的平均孔空隙率分别为0.85%、0.91%和0.82%。
表1 喷涂用粉末名义成分
称取质量比为37.5%Na2SO4+37.5%K2SO4+ 15%Fe2O3+10%SiO2置于碾钵中混合并碾磨至全部通过200目筛网后,搅拌均匀制得合成煤灰,将煤灰与无水乙醇按照质量比1∶10混合制成悬浮液,用刷涂法在试样表面涂覆合成煤灰,在刷涂前和刷涂烘干后分别称重,试样表面涂覆煤灰的量约为40 mg/cm2。腐蚀实验在真空高温管式炉中进行。测试前管内抽真空,到达实验温度后通入模拟烟气,烟气成分为:CO2 15%;O2 3.5%~5%;SO2 0.3%;N2余量。混合气体由质量流量计控制导入管式炉中,气体流量为80 mL/min。腐蚀后试样用蒸馏水清洗表面。用X射线衍射仪 (XRD,D8ADVANCE) 分析表面腐蚀产物的相组成,用扫描电镜 (SEM,QUANTA200) 观察样品的表面和截面形貌。
2 结果与讨论
2.1 腐蚀动力学
图1a为T91钢及喷涂3种涂层在750 ℃含0.3%SO2气氛/煤灰中的腐蚀动力学曲线。可以看出,T91钢增重非常严重,但增重过程中有明显的失重,说明有腐蚀产物剥落。NiCr/Cr3C2、45CT腐蚀初期表现为增重,但后期表现为失重,说明在腐蚀过程后期一直伴随腐蚀产物开裂、剥落。NiCrAlY涂层在初期表现为增重,腐蚀80 h后失重,随后一直表现为增重。图1b为3种涂层腐蚀200 h后涂层减薄柱状图。可以看出,NiCr/Cr3C2涂层和NiCrAlY涂层减薄比较严重,分别达到112.7和93.1 μm,而45CT涂层减薄仅为25 μm。
图1 样品腐蚀动力学曲线和腐蚀前后涂层厚度变化柱形图
2.2 宏观腐蚀形貌
图2为T91钢及喷涂3种涂层在750 ℃含0.3%SO2气氛/煤灰中腐蚀200 h后表面宏观形貌图。从图可见,T91钢表面有腐蚀产物大块剥落痕迹,表面有明显裂痕,与T91相比,45CT、NiCr/Cr3C2和NiCrAlY涂层样品腐蚀相对较轻微,腐蚀产物剥落较轻微。
图2 试样在750 ℃腐蚀200 h后宏观表面形貌图
2.3 XRD分析
图3为T91钢以及喷涂45CT、NiCr/Cr3C2、NiCrAlY涂层试样在750 ℃含0.3%SO2气氛/煤灰中腐蚀200 h后的XRD谱。可见,T91钢主要腐蚀产物为Fe2O3;45CT涂层的主要腐蚀产物为Cr2O3;NiCr/Cr3C2和NiCrAlY涂层的主要腐蚀产物均为NiCr2O4、Cr2O3。3种涂层XRD谱中均有较弱的Fe2O3衍射峰。
图3 样品在750 ℃含0.3%SO2模拟烟气/煤灰中腐蚀200 h后的XRD谱
2.4 表面形貌及能谱分析
图4为T91钢及喷涂45CT、NiCr/Cr3C2、NiCrAlY涂层在750 ℃含0.3%SO2气氛/煤灰中腐蚀200 h后的表面微观形貌图。从图4a和b可见,T91钢表面有明显裂纹和腐蚀产物剥落,能谱分析表明腐蚀层主要组成元素为Fe、O。从图4c和d可见,45CT涂层腐蚀后表面较粗糙,腐蚀层表面主要组成元素为Cr、Fe、Si、O。图中区域1所示颗粒,能谱分析表明其Si含量较高,应为嵌入的合成煤灰中的SiO2。从图4e和f可见,NiCr/Cr3C2涂层表面生成了瘤状腐蚀产物 (图中2所示),能谱分析其主要含Cr、Fe、O,腐蚀层主要组成元素为Cr、Fe、Si、O。从图4g和h可见,NiCrAlY涂层腐蚀后表面相对较平坦,腐蚀层主要组成元素为Cr、Al、Si、O。图中颗粒状附着物 (图中3所示),主要由Fe、Cr、O组成。
图4 T91钢及喷涂45CT、NiCr/Cr3C2、NiCrAlY涂层在750 ℃ 含0.3%SO2气氛/煤灰中腐蚀200 h后的表面形貌
2.5 截面微观形貌及微区成分分析
图5为T91钢在750 ℃含0.3%SO2气氛/煤灰中腐蚀200 h后的截面形貌图。从图5a~c可见,T91钢表面残留的腐蚀层很厚,腐蚀层内有大量横向和纵向裂纹,局部腐蚀层剥落严重;腐蚀产物层中有一薄层白色区域带 (如图5b所示),能谱分析其富W和O,腐蚀后涂层/基体界面的白色产物中也探测到W(如图5e所示),推测应为腐蚀过程中T91钢中Fe向外快速扩散而导致的富W相;腐蚀层主要由Fe、Cr、O组成。在涂层与基体的界面可见明显裂纹。从图5d和e可见,45CT涂层表面深灰色腐蚀产物中嵌入了少量浅灰色颗粒。能谱分析表明,深灰色相主要由Cr、O及少量的Fe、Ni组成,而浅灰色相主要由Fe、Si、Al、K、Na、O组成。说明腐蚀过程中煤灰粒子嵌入到腐蚀产物层中。在涂层/基体界面处可见明显裂纹,裂纹处白色产物富含W和O。涂层/基体界产生裂纹,且O含量高,说明T91基体发生了氧化。从图5f和g可见,NiCr/Cr3C2涂层表面腐蚀产物层较厚且有剥落痕迹,该腐蚀层主要含有Ni、Cr、S、O。在涂层/基体界面有深灰色腐蚀产物带,能谱分析其主要由Fe、O组成,表明在涂层下基体发生了腐蚀生成了氧化物。在涂层与基体界面处可观察到较宽裂纹。从图5h和i可见,NiCrAlY涂层表面覆盖有浅灰色腐蚀产物层,但腐蚀产物层厚度比45CT和NiCr/Cr3C2涂层薄,能谱分析该层主要含有Ni、Fe、Cr、O。在涂层/基体界面处有较薄且不连续的的深灰色产物带,其主要元素组成为Fe、O。涂层下基体侧生成了厚度不一的深灰色腐蚀产物带,这主要是由于热喷涂涂层中有缺陷,O和S等介质通过缺陷或涂层晶界扩散到涂层/基体界面,导致耐蚀性较差的基体发生腐蚀,形成腐蚀产物带
图5 T91钢及喷涂45CT、NiCr/Cr3C2、NiCrAlY涂层在750 ℃ 含0.3%SO2气氛/煤灰中腐蚀200 h后的截面形貌
2.6 腐蚀机理分析
本实验模拟涂层在水冷壁的腐蚀环境,3种涂层表面涂覆合成煤灰,并通入烟气在高温下腐蚀,腐蚀后所有涂层表面均覆盖了氧化物为主的腐蚀层,在涂层/基体界面也生成了氧化物层。根据其腐蚀行为建立如图6所示的涂层腐蚀模型。
图6 热喷涂涂层的腐蚀和失效模型
首先,在烟气中的SO2可与O2反应生成SO3,并与煤灰中的Fe2O3及碱金属硫酸盐发生反应 (1) 生成相应的熔融碱性铁硫酸盐,附着在样品表面,样品在液态盐膜下发生腐蚀。在腐蚀初期涂层表面由于氧分压较高在模拟煤灰下会生成如图6a中所示的一薄层氧化层,如45CT涂层Cr含量大于25%,在高温腐蚀初期,表面会生成一层有保护性的Cr2O3膜[10],可抑制硫酸盐导致的热腐蚀。
其次,随着腐蚀的进行,样品表面的硫酸盐发生分解反应 (2)[11],涂层表面发生碱性熔融热腐蚀如图6b所示,涂层表面腐蚀产物层加速增厚,腐蚀过程生成的及环境中的SO2和O2通过涂层的缺陷和晶界向涂层内部进一步扩散并导致涂层缺陷的周边区域发生腐蚀。
随后,随着腐蚀继续进行,SO2和O2通过涂层向内扩散,涂层中镍、铬离子和基体中金属离子 (主要为铁离子) 向外扩散,导致在涂层表面和涂层/基体处形成腐蚀产物层,由于扩散导致腐蚀层中缺陷不断增多,在腐蚀层中形成如图6c所示的孔洞等缺陷,另外腐蚀层中的生长应力也不断增加,可导致外层腐蚀产物脱落[12]。
最后随着腐蚀的不断发展,由于腐蚀层表面氧分压较高,生成的金属硫化物会在外层氧化生成氧化物,释放的硫会向内扩散,可按反应 (3) 所示的生成硫化物,氧向内扩散生成金属氧化物,导致表面生成的腐蚀产物结合力较差,可出现局部严重剥落形成腐蚀坑。在涂层/基体处生成的腐蚀层最终也会形成裂纹。造成涂层与基体的弱结合,在外力作用下可导致涂层脱落失效。
本实验中所有热喷涂涂层的Cr含量较高,从热力学角度看,Cr硫化生成CrS的Gibbs自由能小于Ni硫化生成NiS的,且硫化物易与氧发生反应 (4)[13]。因此在涂层表面生成的氧化物中难于探测到金属硫化物,而在氧化物内层能探测到少量金属硫化物。众所周知,Cr是抗热腐蚀的有效元素,因此涂层中Cr含量越高涂层的抗热腐蚀性能越好[14]。3种涂层中NiCr/Cr3C2涂层Cr含量相对较低,在腐蚀初期可能未形成连续致密、完整的Cr2O3保护膜,同时涂层表面的Cr3C2易与表面的氧发生反应[15],快速生成瘤状氧化物对氧化膜造成进一步的破坏[16],且Cr3C2在氧化过程中生成CO或CO2气体,这些气体释放会形成更疏松的腐蚀层[17],对腐蚀层结合力有破坏作用,可导致硫酸盐与合金直接接触并发生反应 (5)[18]。生成的Ni3S2易与Ni形成共晶低熔点相加速涂层的腐蚀,因此其抗热腐蚀性能较差[14]。
NiCrAlY涂层在腐蚀过程中减薄较多,其减薄介于45CT和NiCr/Cr3C2之间,但涂层/基体界面腐蚀最轻微,这可能与该涂层的成分有密切关系。从合金成分看,NiCrAlY涂层Cr含量介于两者之间,且含有约10% (质量分数) Al,有研究表明[16],在600~800 ℃范围发生低温热腐蚀,M-Al合金的耐蚀性比M-Cr合金差,因此涂层在覆盖模拟煤灰/烟气环境下涂层减薄较严重。值得注意的是,NiCrAlY涂层/基体界面腐蚀最轻微,可能是由于以下两方面原因造成的:一方面是由于NiCrAlY涂层中Al的熔点较低,在热喷涂过程中能充分熔化,涂层较致密,阻挡了腐蚀介质通过孔隙到达涂层/基体界面,从而抑制了界面处T91钢的腐蚀。另一方面是由于涂层中含有少量稀土元素Y,稀土元素活性高,能够在涂层内捕获S等元素,抑制了S向基体扩散[20]。由于稀土具有抑制杂质元素在晶界偏聚的效应,晶粒界面结合力提高,也提高了涂层的抗氧化性能[21,22]。EDS分析表明3种涂层表面均有较多的Fe,可能是表面涂覆的Fe2O3发生了碱性溶解[19],并成为了腐蚀产物的一部分。3种涂层中45CT的Cr含量最高,因此其抗热腐蚀性能最好,但由于其涂层中空隙等缺陷较多,难以阻挡腐蚀介质通过涂层扩散进而腐蚀基体,造成基体与涂层界面的弱结合。
3 结论
(1) 采用超音速火焰喷涂技术在T91钢表面制备了45CT、NiCr/Cr3C2和NiCrAlY涂层。3种涂层在动力学上均表现为先增重后失重和增重规律,T91钢增重非常严重。经200 h腐蚀后,45CT、NiCr/Cr3C2和NiCrAlY涂层分别减薄25、112.7和93.1 μm。
(2) 在模拟烟气/煤灰腐蚀条件下,45CT涂层Cr含量较高表面腐蚀产物主要为Cr2O3,而NiCr/Cr3C2、NiCrAlY涂层Cr含量较低,表面腐蚀腐蚀产物主要为NiCr2O4、Cr2O3。
3种涂层表面腐蚀产物均不致密,腐蚀介质通过涂层扩散到基体一侧导致基体发生腐蚀。NiCr/Cr3C2由于Cr含量较低,涂层孔隙率较高,涂层/基体界面产生了明显裂纹。45CT涂层本身耐蚀性能优良,但涂层/基体界面有明显裂纹。而NiCrAlY则虽然涂层减薄较多,但涂层/基体界面无裂纹,涂层/基体界面处的基体一侧腐蚀较轻微
参考文献
1 Tang L P. Development of ultra supercritical boiler steel [J]. Appl. Energy Technol., 2007, (10): 20
1 唐利萍. 超超临界锅炉用钢的发展 [J]. 应用能源技术, 2007, (10): 20
2 Lin F S, Cheng S C, Xie X S. Ultrasupercritical power plant development and high temperature materials applications in China [J]. Energy Mater., 2008, 3: 201
3 Kawahara Y. Application of high temperature corrosion-resistant materials and coatings under severe corrosive environment in waste-to-energy boilers [J]. J. Therm. Spray Technol., 2007, 16: 202
4 Wang J. Study on high-temperature property and principle of 45CT coating [D]. Shenyang: Shenyang University of Technology, 2012
4 王剑. 45CT涂层高温性能及其机理研究 [D]. 沈阳: 沈阳工业大学, 2012
5 Liu P F, Tao K, Zhou X L, et al. Research progress in wear and corrosion resistance coating of boiler tubes [J]. Surf. Technol., 2007, 36(1): 75
5 刘鹏飞, 陶凯, 周香林等. 锅炉“四管”用耐磨耐蚀涂层研究进展 [J]. 表面技术, 2007, 36(1): 75
6 Nelson W A, Orenstein R M. TBC experience in land- based gas turbines [J]. J. Therm. Spray Technol., 1997, 6: 176
7 Gong X M, Zhang W Z. Mechanism of high temperature corrosion of heating surface in boiler and countermeasure [J]. Electr. Power Sci. Eng., 2007, 23: 72
7 弓学敏, 张文忠. 锅炉受热面高温腐蚀的机理及防范措施 [J]. 电力科学与工程, 2007, 23: 72
8 Sidhu T S, Prakash S, Agrawal R D. Hot corrosion studies of HVOF sprayed Cr3C2-NiCr and Ni-20Cr coatings on nickel-based superalloy at 900 ℃ [J]. Surf. Coat. Technol., 2006, 201(3/4): 792
9 Zhang Y L, Mao X F, Liu G M, et al. Hot corrosion behavior of Ni-based coating with various Ni and Cr content in simulated fuel gas [J]. Surf. Technol., 2017, 46(9): 191
9 章亚林, 毛晓飞, 刘光明等. 不同Ni、Cr含量镍基涂层在模拟烟气中的热腐蚀行为 [J]. 表面技术, 2017, 46(9): 191
10 Liu G M, Yang H C, Liang Q, et al. Corrosion behavior of the Ni-Cr-Fe base superalloy GH984G in a synthetic coal ash and flue gas environment [J]. Acta Metall. Sin. (Engl. Lett.) , 2017, 30: 863
11 Wang X J, Wang B S, Yang C, et al. Corrosion of pure nickel and its weld joints in molten Na2SO4-K2SO4 salts [J]. J. Chin. Soc. Corros. Prot., 2018, 38: 495
11 王希靖, 王博士, 杨超等. 纯Ni母材及焊缝在熔融Na2SO4-K2SO4中热腐蚀研究 [J]. 中国腐蚀与防护学报, 2018, 38: 495
12 Li M. Corrosion behavior of Nickel-based alloys with different chromium contents [D]. Shenyang: Shenyang University of Technology, 2009
12 李墨. 不同Cr含量的Ni基合金腐蚀行为 [D]. 沈阳: 沈阳工业大学, 2009
13 Ye Y, He G Q, Dai L Q, et al. The research on hot corrosion behaviors of Inconel 625 alloy under sulfate condition [J]. Met. Funct. Mater., 2016, 23(6): 33
13 叶赟, 何国球, 戴礼权等. 硫酸盐条件下Inconel 625合金的热腐蚀行为研究 [J]. 金属功能材料, 2016, 23(6): 33
14 Hong J. Study on corrosion behavior in simulated flue-gas/coal-ash environment of several kinds of coatings prepared by thermal spraying [D]. Nanchang: Nanchang Hangkong University, 2018
14 洪嘉. 几种热喷涂涂层在模拟烟气/煤灰环境中的腐蚀行为研究 [D]. 南昌: 南昌航空大学, 2018
15 Miao X L, Wang Y K, Liu G M, et al. Hot corrosion behavior of subersonic sprayed NiCr/Cr3C2 coating on P91 steel [J]. Surf. Technol., 2011, 40(5): 25
15 繆筱玲, 汪元奎, 刘光明等. P91钢亚音速喷涂NiCr/Cr3C2涂层的热腐蚀行为研究 [J]. 表面技术, 2011, 40(5): 25
16 Li M S. High Temperature Corrosion of Metals [M]. Beijing: Metallurgical Industry Press, 2001
16 李美栓. 金属的高温腐蚀 [M]. 北京: 冶金工业出版社, 2001
17 Liu G M, Li M S, Zhou Y C. Hot corrosion of Ti3SiC2-based ceramics coated with Na2SO4 at 900 and 1000 ℃ in air [J]. Corros. Sci., 2003, 45: 1217
18 Hu F E. High temperature oxidation, hot corrosion and thermal fatigue behavior of GH4698 superalloy [D]. Nanjing: Nanjing University of Aeronautics and Astronautics, 2006
18 胡发恩. GH4698合金的高温氧化、热腐蚀及热疲劳性能的研究 [D]. 南京: 南京航空航天大学, 2006
19 Fu G Y, Yu L Y, Liu Q, et al. Effect of Y2O3 on hot corrosion behavior of mechanical alloying Fe-20Cr-2.5Al alloy [J]. Foundry, 2016, 65(3): 280
19 付广艳, 俞立艳, 刘群等. Y2O3对机械合金化Fe-20Cr-2.5Al合金电化学腐蚀行为的影响 [J]. 铸造, 2016, 65(3): 280
20 Huang Y W, Sun L X, Xu Z Q, et al. The effect of alloying elements (Cr, Ni, Al, Y) on high temperature sulfur corrosion of Cr, Ni, Fe-based alloys [J]. J. Chin. Soc. Corros. Prot., 1991, 11(3): 255
20 黄元伟, 孙兰祥, 徐之强等. 合金元素 (Cr、Ni、Al、Y) 对Cr、Ni、Fe基合金高温硫腐蚀的影响 [J]. 中国腐蚀与防护学报, 1991, 11(3): 255
21 Zhu M, Zhou G Y, Zhang H H. Corrosion behavior of 316 stainless steel in mixed molten nitrate salts with and without Rare earth element [J]. J. Chin. Soc. Corros. Prot., 2017, 37: 16
21 朱明, 周嘏玥, 张慧慧. 316不锈钢在添加微量稀土元素硝酸熔盐中腐蚀行为研究 [J]. 中国腐蚀与防护学报, 2017, 37: 16
22 Ni J F, Hong J, Liu G M, et al. Hot corrosion behavior of NiCrAlY coating in simulated flue gas [J]. Corros. Prot., 2019, 40: 578
22 倪进飞, 洪嘉, 刘光明等. NiCrAlY涂层在模拟烟气中的热腐蚀行为 [J]. 腐蚀与防护, 2019, 40: 578
免责声明:本网站所转载的文字、图片与视频资料版权归原创作者所有,如果涉及侵权,请第一时间联系本网删除。
-
标签: 45CT, NiCr/Cr3C2, NiCrAlY, 热喷涂涂层, 热腐蚀
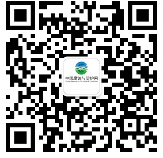
官方微信
《中国腐蚀与防护网电子期刊》征订启事
- 投稿联系:编辑部
- 电话:010-62316606-806
- 邮箱:fsfhzy666@163.com
- 中国腐蚀与防护网官方QQ群:140808414