摘要
镁合金基体首先进行超声滚压预处理后再进行微弧氧化镀膜,结合OM、SEM、EDS、XRD与电化学工作站 (模拟体液PBS) 对有无超声滚压处理的微弧氧化膜层性能进行测试分析,研究超声滚压处理对镁合金微弧氧化膜层性能的影响。结果表明:超声滚压处理后镁基体表面粗糙度降低、晶粒细化且硬度提升;与镁合金直接微弧氧化的膜层相比,超声滚压预处理之后再进行微弧氧化,膜层中的Si、P、Ca含量比例增大,膜层表面更为致密、光滑,大孔数量明显降低,表面孔隙率由31.7%降低至19.1%;从电化学测试结果看出,与直接微弧氧化的膜层相比超声滚压预处理后膜层的自腐蚀电位高出107 mV,腐蚀电流密度低了一个数量级,并且阻抗性能更优,镁合金超声滚压预处理可有效提升微弧氧化膜层在PBS溶液中的耐蚀性。
关键词: AZ31B镁合金; 超声滚压; 晶粒细化; 微弧氧化; 耐蚀
近年来,骨质疏松问题日益严重,钛合金、不锈钢等对于可恢复部位的应力遮挡、二次手术取出的问题逐渐凸显。由于镁合金具备与人骨相似的密度、弹性模量、压缩屈服强度及断裂韧性[1],避免了由于硬度过大而造成的应力遮挡,更主要的是可在体内溶解,避免了病人进行二次手术,减少病痛与手术风险[2],因此在医用材料中应用前景广泛[3,4]。但是,镁合金耐蚀性差是临床应用领域的主要难题,容易导致骨愈合速率不匹配[5]。当镁合金作为骨替代品植入到生物体内时,因为腐蚀过快,造成结构强度等发生改变,很难满足骨骼生长期所需的支撑力,使得镁合金在医学上的应用受到了极大的限制。因此,降低镁合金在人体内的腐蚀是目前面临的主要问题[6]。
微弧氧化 (MAO) 作为一种工艺简单、加工效率高、污染小的表面处理技术,成为最具前景的一种镁合金防腐技术[7-9],相关研究发现,MAO膜层具有良好的耐磨性与耐蚀性[10],与基体属于冶金结合,结合力强可以提供长期稳定的防护能力,避免腐蚀过快而导致骨愈合失败。但MAO膜层[11]存在气孔率高、表面积相对较大,制约了其推广应用。针对这一问题,许多学者对膜层进行了优化,目前改善微弧氧化膜的方法主要包括调整操作参数 (如工作电压、反应时间、频率、占空比等)、改变电解液配方、后期封孔处理等。Gheytani等[12]通过对基体与微弧氧化膜结合层的研究发现,微观结构对微弧氧化膜层的性能影响极其重要,增加基体的晶界、空位和位错密度有助于优化膜层的结构、降低孔隙率。Lei等[13]通过机械磨损处理细化表层晶粒,增加了膜层致密性,降低了微弧氧化膜层腐蚀速率,提高了自身耐蚀性。牛宗伟等[14]通过喷丸处理,微弧氧化膜致密性得到改善,自腐蚀电位提高了37 mV,耐蚀性增加。目前通过喷丸处理制备表面纳米层,使得工件表面微观受力方向性难以控制,在后期微弧氧化时所制得膜层均匀性差,机械磨损处理效率低,且不能有效改善微弧氧化膜。因此,很有必要发展一种新型微弧氧化膜优化技术。
超声滚压技术是近些年发展而来的一种新型金属表面强化技术,结合了滚压技术的导向作用与喷丸技术的超声振动技术,以期作为微弧氧化前的预处理手段,但是目前对于这方面研究较少。
因此本文针对AZ31B镁合金,利用超声滚压技术与微弧氧化技术相结合,对镁合金进行表面改性,将超声滚压作为预处理的方式,进而优化微弧氧化膜层性能,以期得出一种新型微弧氧化膜层的改善方法。
1 实验方法
采用车削加工去掉所有镁合金样品表面的氧化层,将镁合金实验试样分为两组:第一组为经过超声滚压预处理之后再进行微弧氧化 (UIRP+MAO);第二组为未经超声滚压预处理直接进行微弧氧化 (MAO)。对两种试样选取相同微弧氧化处理工艺,以便实验结果对比分析。
采用铸造AZ31B镁合金棒料,其质量分数 (%) 为:Al 3.2、Zn 1.2、Mn 0.8、Si 0.07、Ca 0.04、Cu 0.01,其余为Mg。所有试样均加工成规格为?30 mm×10 mm,并对其进行微弧氧化处理,待微弧氧化结束之后,分别用去离子水和酒精清洗,吹干备用。
超声滚压采用HK30C毫克能金属表面加工设备,原理示意图如图1,主要加工参数为:转速为800 r/min、进给速度0.05 mm/r、振动频率40 kHz、振幅8 μm、静压0.12 MPa。采用JHMAO-380 V/20A型微弧氧化电源,制备膜层采用恒压模式,主要工艺参数为:电压420 V、频率500 Hz、占空比15%、时间10 min (经过预实验,当微弧氧化10 min时,膜层生长完整并具有一定厚度);电解液配方为 (g/L):Na2SiO3 5、NaOH 4、(NaPO3)6 4、Ca10(PO4)6(OH)2 2。
图1 超声滚压示意图
为了研究超声滚压对膜层的影响,首先对镁合金经过超声滚压处理之后,使用D2 PHASER型X射线衍射仪 (XRD) 对超声滚压处理前后镁合金表面相结构进行分析,扫描范围从20°到90°,扫描速率为4°/min;使用ZeGage Plus型白光干涉仪测量粗糙度;使用DM2700M型金相显微镜 (OM) 对其截面金相组织进行观察,配合200、100和20 μm深度的JEM-2010透射电镜 (TEM) 明场图像对镁合金超声滚压后的性能进行评价,最后使用402MVD型维氏显微硬度计对截面力学性能进行评估,每个压痕实验点重复实验3次。
然后对UIRP+MAO与MAO试样使用XRD进行相成分测试,扫描范围从20°到80°,扫描速率为4°/min;使用Quanta 400F型扫描电镜 (SEM) 对两种类型试样的表面与截面微观形貌进行观察,并对膜层表面孔隙率进行计算;结合自带的能谱分析 (EDS) 对两种试样表面元素分布进行分析。
最后将UIRP+MAO与MAO试样随机选取圆柱面1 cm2的检测部分,其余表面全部使用硫化硅橡胶密封,使用Zahner Zennium X电化学工作站对试样电化学性能在标准磷酸盐缓冲液 (PBS模拟体液) 中进行测试,所有测试均在室温下进行。本次测试采取以R232饱和甘汞 (SCE) 为参比电极,10 mm×10 mm×0.2 mm铂片为辅助电极,暴露面积为1 cm2的试样为工作电极的三电极体系。其中,PBS成分 (mmoL/L) 为:NaCl 68.5、KCl 1.35、Na2HPO4 5、KH2PO4 1。动电位极化扫描速率为5 mV/s,扫描范围为-1.8 V到2 V (绝对电位)。在自腐蚀电位下进行阻抗实验,频率从为105~10-2 Hz,正弦扰动电压为10 mV,当频率小于66 Hz时每十位区间取5个点,当频率大于66 Hz时每十位区间取10个点,每个取样点测试10次。
2 结果与讨论
2.1 镁合金超声滚压预处理微观结构与力学性能分析
由图2可以看出,经过超声滚压后,未出现新的衍射峰,图谱显示AZ31B镁合金中仅包含α-Mg和β-Mg17Al12两相,表明在UIRP处理后无新相产生。超声滚压处理后衍射峰强度显著增加,试样的衍射峰峰值增大。其中 (002) 晶面衍射峰强度提高表明基面滑移系统活跃,同时高强度 (101) 晶面表明AZ31B镁合金的锥面滑移系统被激活[15]。另外,(101) 晶面与材料的孪晶面有关,这种类型孪晶属于压缩孪晶可以协调沿c轴方向的压缩变形。由于压缩孪晶的产生需要相当高的临界剪切应力,这也证明了超声滚压处理过程中产生了剧烈的塑性变形。另外,UIRP处理后衍射峰明显变宽,例如 (101) 衍射峰的半峰宽急剧增加,处理后试样的衍射峰与未处理试样相比,由于超声滚压处理过程中产生的晶粒细化、晶格微应变和微变形,从而出现了衍射峰宽化和衍射峰向右轻微偏移现象[16]。结合金相截面形貌,可以判断是晶粒细化引起的峰强度改变。
图2 超声滚压前后镁合金表面XRD谱
将未经过超声滚压试样与经过超声滚压后的试样使用白光干涉仪对表面形貌进行了分析,如图3所示,经过超声滚压的试样,表面平整光滑,无重大缺陷,“峰谷”幅度较小,表面粗糙度急剧减小,“峰谷波动极值之差”从4.818 μm降低到1.351 μm。
图3 超声滚压前后镁合金表面形貌
如图4所示,镁基体通过超声滚压处理后,在靠近滚压面的一侧,有明显的晶粒细化层,随着深度的增加,晶粒明显逐渐增大,呈梯度分布。图5为距超声滚压表层200、100和与20 μm不同深度的明场图像。由于受超声滚压力作用较大,随着超声滚压深度减小滑移量增加,从板条状晶粒逐渐形成亚晶粒,在亚晶粒周围形成了大量的亚晶界。有研究[17]发现,超声的作用比较容易使内部发生动态再结晶,在变形极端中心,容易诱导形成新的晶粒,此时,动态再结晶[11]也是细化晶粒的重要组成部分。由图5明场图像中都能发现存在有聚集的位错线,并且在一定程度上由于位错密度的增大而形成了位错胞,随着距离表层深度减少,位错线聚集形成位错胞现象越明显,位错胞数量增多,因此位错能密度增加、镁基体表面处晶粒得以细化。
图4 超声滚压前后镁合金截面OM像
图5 超声滚压距表层不同深度TEM组织
将未经过超声滚压试样与经过超声滚压后的试样进行了截面的维氏显微硬度测试。镁合金经过超声表面滚压处理后形成一定厚度的纳米梯度层,从图6可知,表层数值最大,随后进入急剧下降阶段,在距表面距离约300 μm处出现转折,进入缓慢下降阶段,而越接近基体时变化趋势越平稳;未经过超声滚压的试样截面硬度分布比较均匀,在54~64 HV范围内进行波动;经过超声滚压表面预处理的试样,由显微硬度结果发现,随着距离表层深度的增加,试样截面的维氏显微硬度以梯度方式减小,最大硬度到132 HV。随着深度增加,能量传递过程中逐渐损失,因此强化效果呈梯度变化。由于试样经超声滚压处理过程中其表面产生了严重的塑性变形,材料内部产生高密度位错堆积及位错间相互作用,这些均对材料硬度的提高起到了积极的作用。
图6 距表层不同深度截面显微硬度曲线
2.2 MAO与UIRP+MAO膜层微观结构分析
图7为UIRP+MAO与MAO的XRD谱,可以看出,在该图中所有的样品包括Mg、Mg3(PO)4、HA、MgO、Mg2SiO4相。根据相组成可证明电解液中Si、P、Ca等积极参与成膜反应的生长过程。
图7 UIRP+MAO与MAO膜层XRD谱图
图8a3和b3为UIRP+MAO与MAO的EDS测试结果,膜层的元素组成为O、Na、Mg、Si、P、Ca。对Si、P、Ca的检测表明电解质离子参与了成膜反应,在UIRP+MAO膜层中,Si、P、Ca含量大于MAO膜层。由于膜层呈现多孔形状,图8a2和b2为UIRP+MAO与MAO的表面孔隙率计算结果,分别为:19.1%、31.7%。经过预处理极大地减小了微弧氧化膜层表面孔隙率,并且从图8a1和b1可以看出,相较于MAO,UIRP+MAO膜层表面大孔隙明显减少,膜层变得光滑,很有可能是因为超声滚压对镁基体进行预处理之后,微弧氧化膜放电通道变小,膜层变的更致密。
图8 UIRP+MAO与MAO膜层表面SEM形貌、孔隙率分析和EDS分析
图9所示为两种膜层侧面形貌和元素分布图,从图9a1可以看出,UIRP+MAO膜层的厚度约为10 μm,膜层非常致密,且与镁基体相接触部位比较光滑;图9a2为UIRP+MAO膜层的横截面元素分布图,在膜层上镁元素相对镁基体含量降低,元素种类与膜层表面未发生改变;图9b1可以看出MAO膜层的厚度同样约为10 μm,与镁基体接触部位有明显的孔洞,相较UIRP+MAO膜层比较疏松,孔隙较大,图9b2为MAO膜层的横截面元素分布图,Mg在膜层上相对镁基体含量减少,但是截面元素与表面元素种类相同,这说明膜层主要由O、Mg、Si、Na、P、Ca元素组成。
图9 UIRP+MAO与MAO膜层侧面形貌与元素分布图
2.3 MAO与UIRP+MAO膜层电化学性能分析
由图10可以看出,UIRP+MAO自腐蚀电位明显正移,UIRP+MAO试样的腐蚀电流密度小于MAO,说明了UIRP+MAO表面所形成的微弧氧化膜层对基体的保护能力大于MAO表面膜层对基体的保护能力。并且由图中可以得知,UIRP+MAO的钝化电流远小于MAO钝化电流,点蚀电位也大于MAO试样,这表明UIRP+MAO表面所形成的钝化膜层稳定性好,不易遭受外界破坏。
图10 UIRP+MAO与MAO膜层极化性能分析
表1为MAO与UIRP+MAO阻抗拟合结果。利用Tafer外推法对极化曲线进行分析,通过MAO与UIRP+MAO两组试样的极化曲线可以得出自腐蚀电位Ecorr、腐蚀电流密度Icorr。UIRP+MAO的腐蚀电位是-0.667 V,腐蚀电流密度为7.94×10-3 mA;MAO的腐蚀电位是-0.784 V,腐蚀电流密度为2.57×10-2 mA。从结果可以看出,UIRP+MAO腐蚀电位远大于MAO,且腐蚀电流密度相较于MAO小了一个数量级,说明在PBS溶液中UIRP+MAO试样的腐蚀的倾向性小于MAO。
表1 MAO与UIRP+MAO阻抗拟合结果
图11为UIRP+MAO与MAO试样的Nyquist图及其电路拟合图。两种膜层的阻抗谱均由高频与低频区的两个容抗弧组成,且UIRP+MAO试样的容抗弧弧径远大于MAO试样的弧径。其中Rs表示电阻,R1表示微弧氧化膜/PBS溶液的电荷转移电阻,CPE1表示基体/溶液双电层电容,R2表示微弧氧化膜电阻,CPE2表示微弧氧化膜/溶液之间的双电层电容。
图11 UIRP+MAO与MAO膜层Nyquist图及拟合电路
对应于Nyquist图中,高频阻抗一般表示电极表面电荷转移,低频阻抗表示微弧氧化膜层的阻抗性能。从表1的拟合结果可知,在高频部位,UIRP+MAO阻抗性能与MAO相当,但在低频区域,UIRP+MAO阻抗性能远大于MAO试样,说明UIRP+MAO膜层对镁基体的保护性能远大于MAO。这是因为经过超声滚压预处理之后的膜层表面孔径更小,更加的致密,所以PBS溶液中的腐蚀性离子在穿过UIRP+MAO的阻力远大于MAO膜层。
通过动电位极化与阻抗分析可知,UIRP+MAO试样在PBS中的耐蚀性能优于MAO试样,也就是经过超声滚压预处理后的微弧氧化膜显示出更耐蚀的性能。通过超声滚压工艺预处理改善膜层耐蚀性是先通过超声滚压处理之后表面晶粒细化,晶界增多,位错缠结越[18]来越严重,因此位错能密度[19]相对增大,形成大量的细小晶粒。细化后的晶粒能够增加微弧氧化膜层的成核点[11]。从图8a3和b3可以看出,微弧氧化膜表面孔隙率从31.7%降低到19.1%,并且膜层表面大孔急剧减小。因此腐蚀性溶液不易通过微小的孔隙进入到镁基体,UIRP+MAO试样在PBS溶液中更耐蚀。
3 结论
(1) AZ31B镁合金超声滚压处理后并未出现新相,但 (101) 衍射峰峰值明显增强,晶粒细化效果显著,显微硬度急剧增加,与此同时超声滚压后镁合金表面粗糙度急剧减小,“峰谷波动极值之差”从4.818降低到1.351 μm。
(2) AZ31B镁合金表面的差异性导致表面微弧氧化膜显示出不同的性能。UIRP-MAO膜层中Si、P、Ca含量大于MAO膜层,超声滚压处理后的膜层表面更加平整光滑,大孔数量明显较少,孔隙率由31.7%降低到19.1%。并且UIRP+MAO膜层的自腐蚀电位高于MAO膜层、腐蚀电流密度低于MAO膜层,UIRP+MAO膜层在PBS溶液中阻抗性能远大于MAO,因此镁合金超声滚压预处理可有效增强微弧氧化膜层耐蚀性。
参考文献
[1]Hornberger H, Virtanen S, Boccaccini A R.
Biomedical coatings on magnesium alloys-A review
[J]. Acta Biomater., 2012, 8: 2442
[本文引用: 1]
[2]Mueller W D, de Mele M F L, Nascimento M L, et al.
Degradation of magnesium and its alloys: Dependence on the composition of the synthetic biological media
[J]. J. Biomed. Mater. Res., 2010, 90A: 487
[本文引用: 1]
[3]Witte F.
The history of biodegradable magnesium implants: A review
[J]. Acta Biomater., 2010, 6: 1680
[本文引用: 1]
[4]Kim J H, Lee S K, Hwang K S, et al.
Nano-tribological properties of topographically undulated nanocrystalline diamond patterns
[J]. J. Nanosci. Nanotechnol., 2011, 11: 344
[本文引用: 1]
[5]Zhang S X, Zhang X N, Zhao C L, et al.
Research on an Mg-Zn alloy as a degradable biomaterial
[J]. Acta Biomater., 2010, 6: 626
[本文引用: 1]
[6]Chen Y J, Xu Z G, Smith C, et al.
Recent advances on the development of magnesium alloys for biodegradable implants
[J]. Acta Biomater., 2014, 10: 4561
[本文引用: 1]
[7]Wu S K, Yang W, Gao Y, et al.
Preparation and characterization of new yellow ceramic coating by micro arc oxidation on 6061 aluminum alloy
[J]. Surf. Technol., 2019, 48(7): 142
[本文引用: 1]
武上焜, 杨巍, 高羽等。
6061铝合金表面新型黄色微弧氧化陶瓷层的制备与表征
[J]. 表面技术, 2019, 48(7): 142
[本文引用: 1]
[8]Zhong T S, Jiang B L, Li J M.
Characteristics, applications and research direction of micro-arc oxidation technology
[J]. Electropl. Finish., 2005, 24(6): 47
钟涛生, 蒋百灵, 李均明。
微弧氧化技术的特点、应用前景及其研究方向
[J]. 电镀与涂饰, 2005, 24(6): 47
[9]Das D K, Joshi S V, Singh V.
Effect of prealuminizing diffusion treatment on microstructural evolution of high-activity pt-aluminide coatings
[J]. Metall. Mater. Trans., 2000, 31A: 2037
[本文引用: 1]
[10]Lin X, Wang X, Tan L L, et al.
Effect of preparation parameters on the properties of hydroxyapatite containing micro-arc oxidation coating on biodegradable ZK60 magnesium alloy
[J]. Ceram. Int., 2014, 40: 10043
[本文引用: 1]
[11]Cao H H, Huo W T, Ma S F, et al.
Microstructure and corrosion behavior of composite coating on pure mg acquired by sliding friction treatment and micro-arc oxidation
[J]. Materials, 2018, 11: 1232
[本文引用: 3]
[12]Gheytani M, Bagheri H R, Masiha H R, et al.
Effect of SMAT preprocessing on MAO fabricated nanocomposite coating
[J]. Surf. Eng., 2014, 30: 244
[本文引用: 1]
[13]Wen L, Wang Y M, Jin Y, et al.
Design and characterization of SMAT-MAO composite coating and its influence on the fatigue property of 2024 Al alloy
[J]. Rare Met. Mater. Eng., 2014, 43: 1582
[本文引用: 1]
[14]Niu Z W, Sun P, Shao Z H, et al.
Effect of the ultrasonic shot peening-rare earth precursor films on the corrosion of micro arc oxidation of aluminum alloy AC7A
[J]. Plat. Finish., 2015, 37(12): 1
[本文引用: 1]
牛宗伟, 孙鹏, 邵珠恒等。
超声喷丸稀土预制膜对铝合金微弧氧化耐蚀性的影响
[J]. 电镀与精饰, 2015, 37(12): 1
[本文引用: 1]
[15]Hassani F Z, Ketabchi M.
Nano grained AZ31 alloy achieved by equal channel angular rolling process
[J]. Mater. Sci. Eng., 2011, A528: 6426
[本文引用: 1]
[16]Ungár T.
The meaning of size obtained from broadened X-ray diffraction peaks
[J]. Adv. Eng. Mater., 2003, 5: 323
[本文引用: 1]
[17]Qian M, Ramirez A, Das A, et al.
The effect of solute on ultrasonic grain refinement of magnesium alloys
[J]. J. Cryst. Growth, 2010, 312: 2267
[本文引用: 1]
[18]Ling X, Yang W S, Zhao Q Q, et al.
Effect of extrusion treatment on the microstructure and mechanical behavior of SiC nanowires reinforced Al matrix composites
[J]. Mater. Sci. Eng., 2017, A682: 38
[本文引用: 1]
[19]Cordero N M, Forest S, Busso E P, et al.
Grain size effects on plastic strain and dislocation density tensor fields in metal polycrystals
[J]. Comput. Mater. Sci., 2012, 52: 7
[本文引用: 1]
免责声明:本网站所转载的文字、图片与视频资料版权归原创作者所有,如果涉及侵权,请第一时间联系本网删除。
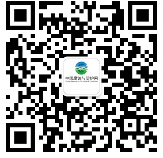
官方微信
《中国腐蚀与防护网电子期刊》征订启事
- 投稿联系:编辑部
- 电话:010-62316606-806
- 邮箱:fsfhzy666@163.com
- 中国腐蚀与防护网官方QQ群:140808414