摘要
为了探讨脉冲电流对1050铝合金微弧氧化过程的影响规律,利用涡流测厚仪和粗糙度仪分别测量陶瓷层厚度和表面粗糙度,采用SEM观察陶瓷层微观形貌,借助动电位极化曲线测试评价陶瓷层耐蚀性,并根据电压变化曲线计算微弧氧化过程能量消耗。结果表明:随着脉冲电流由100 A增加至800 A,微弧诱发时间由360 s缩短至15 s,诱发电压由341 V 升高至887 V;陶瓷层表面放电微孔孔径增大,微孔数量减少,陶瓷层厚度和表面粗糙度增加,耐蚀性略有下降;微弧诱发过程能量消耗先减少后增加,并在200 A时达到最小值仅为18.3 kJ;陶瓷层生长过程能量消耗随脉冲电流增大近似线性增加。
关键词: 铝合金 ; 微弧氧化 ; 脉冲电流 ; 耐蚀性 ; 能量消耗
微弧氧化 (MAO)[1,2,3,4]技术是以Al、Mg、Ti等有色金属及其合金作为阳极,不锈钢为阴极,置于脉冲电场环境的电解液中,在热化学、等离子体化学和电化学的共同作用下使金属表面产生微弧放电而生成一层与基体以冶金方式结合的陶瓷质氧化膜。铝合金经MAO处理后极大提高了其表面的硬度、耐磨、耐蚀、耐压绝缘及抗高温冲击等特性[5,6],但处理成本过高限制其推广应用[7,8]。众多研究[4,7-9]表明,MAO工艺主要依靠电源供给能量实现金属自我氧化,因此研究能量的消耗是降低铝合金MAO处理过程成本的重要方式。
电参量的模式是改变MAO过程能量消耗的主要因素[8],直流脉冲MAO电源因有较高的成膜效率且有良好的膜层性能而被广泛应用[10,11,12]。目前,国内外对MAO技术的主要研究集中在电参数和电解液对膜层性能以及微观结构的影响等方面[13,14,15,16],而脉冲电流对铝合金MAO过程能量消耗的影响规律尚不清楚。针对工艺过程环保、陶瓷层性能优异的MAO技术在成本组成中能量消耗太高限制其应用推广这一工程学问题,本文采用直流脉冲电源研究不同脉冲电流下1050铝合金MAO过程中能量的消耗,分析微弧诱发时间和电压,测量陶瓷层厚度和表面粗糙度,观察表面和截面形貌,比较耐蚀性,计算能量消耗,探寻脉冲电流对铝合金MAO过程能量消耗的影响,为低能耗MAO过程的电参数设置提供理论依据。
1 实验方法
实验采用1050工业铝合金,其化学成分 (质量分数,%) 为:Si 0.25,Fe 0.4,Mn 0.05,Zn 0.05,Cu 0.05,Mg 0.05,Al余量。试样尺寸为100 mm×50 mm×2 mm,并在其顶端钻一个Φ2 mm的通孔用于连接阳极。MAO电解槽容积为50 L,内置不锈钢板作为阴极,试样作为阳极,按浓度15 g/L Na2SiO3 (分析纯,西安三浦精细化工)、5 g/L (NaPO3)6 (分析纯,西安三浦精细化工)、5 g/L KOH (分析纯,西安三浦精细化工) 以及少量无机添加剂加入到去离子水中配置电解液。采用西安理工大学研制的MAO-PM500型直流脉冲电源来进行MAO处理,电源控制模式是脉冲电流控制。电源输出参数控制示意图见图1,其中,ip为脉冲电流,Δt为电流导通时间即脉冲宽度 (以下简称脉宽),N为频率,3个电参量均独立可变。铝合金于电解液中设置Δt为30 μs,N为500 Hz,ip分别为100,200,300,400,600和800 A进行MAO处理。铝合金试样MAO工艺流程为:表面打磨清洗→MAO→去离子水清洗→干燥。
图1 电源输出参数示意图
采用TT-240型涡流测厚仪测量陶瓷层厚度,试样正反面各取5个点,对所测数据求平均值;使用TR-240型表面粗糙度测试仪测量陶瓷层表面粗糙度,计算轮廓算术平均偏差Ra,试样正反面各取5个点,对所测数据求平均值;使用JSM-6700F型扫描电子显微镜 (SEM) 观察陶瓷层微观形貌;使用CHI660D型电化学工作站测量动电位极化曲线,腐蚀介质为3.5% (质量分数) NaCl溶液,同时保证腐蚀区域为10 mm×10 mm,分析Tafel曲线并通过腐蚀电位和电流比较耐蚀性。
MAO过程中能量的消耗是指整个通电过程中直流脉冲电源输出的总能量。从图1可知,能量消耗Q为通电时间内单脉冲能量作用在两极间的总和,如下式:
(1)
式中,T为通电时间 (s),Wsi为单个脉冲所含的能量 (J)。Wsi计算式如下:
(2)
式中,Ut为电压。
根据电流等通量变换原理,可知ip与平均电流ia的关系如下:
(3)
由于ip保持不变,将式 (3) 进行转换可以得到下式:
(4)
通过式 (2) 和 (4) 对式 (1) 进行转变,最后可以得到能量的计算公式如下:
(5)
通电至铝合金试样表面均匀布满微弧等离子体放电斑点的等待时间为微弧诱发时间,此时阴阳两极间电压值即为诱发电压,该过程能量消耗即为微弧诱发过程能耗Q1。铝合金试样表面微弧诱发后至停止通电,此过程能量消耗为生长过程能耗Q2。生长单位厚度陶瓷层能量消耗Q3计算公式如下:
(6)
其中,D为陶瓷层厚度。
2 结果与讨论
2.1 微弧等离子体诱发时间和电压
铝合金试样于电解液中设置Δt为30 μs,N为500 Hz,ip分别100,200,300,400,600和800 A进行MAO处理,试样表面发生MAO放电现象后记录时间及电压,结果见图2。可以看出,随着脉冲电流增加,铝合金试样诱发时间迅速降低并趋于稳定,由最长360 s缩短至15 s;微弧诱发电压近似于线性增长,由最低341 V至最高887 V。由单脉冲能量计算式 (2) 可知,脉冲电流是影响单脉冲能量的重要因素,随脉冲电流增大,单个脉冲能量也随之增加,更高能量作用于试样表面,间接造成了试样两端电压上升速度增加,有效促进铝合金MAO过程的进行,因此微弧诱发时间缩短,诱发电压升高。
图2 脉冲电流对铝合金微弧诱发时间和电压的影响
1050铝合金试样在不同脉冲电流的条件下MAO处理5 min,记录电压变化曲线见图3。通过对比电压变化曲线可看出,在相同时间点试样两端电压值随着脉冲电流的增大也相对较高;在脉冲电流一定的条件下,试样两端电压整体也呈增大趋势,但通电初期迅速增大,在时间推移过程中增速变缓,两个阶段基本上以微弧诱发为分界点。根据相关文献[7,10]分析可知,电源开始提供能量时,铝合金试样表面层的阻抗值迅速增加,促使试样两端电压急速上升,当阻抗层达到一定厚度且电压超过击穿电压时,试样表面出现击穿微弧放电现象,之后膜层生长的过程重复“击穿-熔融-淬冷”,因此膜层厚度增加使得击穿放电变得很困难,最终造成电压增速变缓。
图3 脉冲电流对铝合金MAO过程中电压的影响
2.2 MAO膜层的微观结构
表1为测得的铝合金试样表面MAO膜层的厚度和表面粗糙度。对比可见,在脉宽、脉数以及处理时间不变的条件下,当脉冲电流由100 A增加到800 A,膜层厚度逐渐增加,表面的粗糙度也逐渐增大。
表1 不同脉冲电流下铝合金MAO陶瓷层的厚度和粗糙度
采用SEM观察试样表面以及截面的形貌,结果见图4和5。从图4可以看出,当脉冲电流由100 A增加到800 A,试样表面放电微孔的孔径增大,放电微孔的数量减少,表面平整性变差,与表1中粗糙度测试结果一致。利用Nano Measurer随机选取5个微孔统计可得陶瓷层表面放电微孔的平均孔径。脉冲电流为100 A时,试样表面放电微孔孔径小于0.5 ?m;脉冲电流为200和300 A时,放电微孔孔径为0.8~1 ?m,数量略有减少;脉冲电流为400 A时,试样表面放电微孔孔径增大,平均为1.8 ?m,同时出现典型的“火山堆”状结构 (图4d中黑色圆圈所示);脉冲电流为600和800 A时,放电微孔孔径进一步增至3~4 ?m,试样表面出现大量微裂纹,同时局部还有大孔套小孔现象 (图4f黑色圆圈所示),说明局部发生了重复击穿,这种特殊结构导致陶瓷层致密度下降。从图5可以看出,脉冲电流为200,400和800 A时,膜层厚度分别为3.5,4.6和8.6 ?m,和涡流测厚仪测量出的结果 (表1) 基本一致。当脉冲电流由200 A增加至800 A,膜层的厚度增加,缺陷的数量增加,致密度也下降,直到出现较大放电微孔 (图5c黑色圆圈处),与表面形貌观察的结果一致。
图4 脉冲电流对铝合金MAO陶瓷层表面形貌的影响
图5 脉冲电流对铝合金MAO陶瓷层截面形貌的影响
从能量角度分析,当脉冲电流增大,单个脉冲承载的能量也就随之增大,使得微弧诱发之后电源所输出到铝合金表面的总能量增大,更大的能量会在单位时间产出更多熔融物,形成更大的放电微孔,然后在速冷的过程中形成了更厚的膜层。因此,在同样的时间内,脉冲电流越大,膜层的生长速度就越快。膜层表面与截面形貌表明,脉冲电流增大虽然能获得更厚的膜层,但是其表面的粗糙度增大,膜层质量也相对较差。
2.3 MAO陶瓷层耐蚀性分析
铝合金MAO陶瓷层的耐蚀性是由膜层组成、厚度和显微结构等各种因素综合作用决定[2]。不同脉冲电流下制备铝合金MAO陶瓷层的耐蚀性通过在3.5%NaCl溶液中进行动电位极化曲线测试来评价,极化曲线见图6。
图6 脉冲电流对铝合金MAO陶瓷层在3.5%NaCl溶液中动电位极化曲线的影响
由Tafel区域外推法从图6极化曲线得到基体和不同厚度陶瓷层的阴/阳极Tafel斜率 (ba和bc)、腐蚀电位 (Ecorr) 和腐蚀电流密度 (Icorr),结果列于表2。从热力学上讲,Ecorr主要是由材料本身性质决定,材料腐蚀电位越正,腐蚀倾向越低。表2中陶瓷层的Ecorr与基体相比略有正移,说明腐蚀倾向减小;同时,随脉冲电流增加,Ecorr基本趋于稳定。但Ecorr只能说明腐蚀倾向,判断耐蚀性还要看其在具体腐蚀环境中的腐蚀电流密度。从表2还可以看出,与基体相比,陶瓷层的Icorr降低3个数量级,说明经过MAO处理的1050铝合金耐蚀性明显提高;同时随着脉冲电流增大,陶瓷层的Icorr逐渐增大,因此耐蚀性呈下降趋势。结合表2陶瓷层厚度和图5截面形貌综合分析,脉冲电流为800 A时,尽管所得陶瓷层很厚,但是其致密度相对较差,导致Icorr增大,耐蚀性变差。
表2 铝合金试样在3.5%NaCl溶液中动电位极化曲线计算结果
2.4 MAO过程能量消耗计算
为了研究脉冲电流对1050铝合金MAO过程能量消耗的影响,按照式 (5) 对图3中电压变化曲线以微弧诱发时间为分界点进行分段积分,得到不同脉冲电流下微弧诱发过程能耗Q1和陶瓷层增厚生长过程能耗Q2,结果见图7。分析图7中Q1的变化曲线可以看出,随着脉冲电流增大,Q1先减小后增大。由式 (5) 分析可知,Q1是由电压、时间和平均电流这3个参量共同决定的,脉冲电流较小时 (如100 A),虽然微弧诱发的电压低且平均电流比较小,但是消耗时间却很长,所以Q1很大;脉冲电流比较大时 (如600和800 A),虽然微弧诱发时间较短,但是诱发电压比较高且平均电流较大,所以Q1较高。综合对比微弧诱发的电压和时间,脉冲电流为200 A时Q1达到最小值仅为18.3 kJ。从图7中Q2的变化曲线可以看出,随着脉冲电流增大,Q2基本呈现线性增加。在脉宽和脉数一定条件下,随着脉冲电流由200 A增大至800 A,根据式 (4) 可知,作用于样品两端的平均电流成倍地增大,与此同时样品两端的电压也相对较高,所以Q2近似成倍增大。
图7 脉冲电流对微弧诱发和陶瓷层生长过程能量消耗的影响
鉴于各种脉冲电流下铝合金表面的MAO膜层厚度不一致,为了让能量的消耗更加有可比性,根据式 (6) 计算出生长单位厚度膜层能量消耗Q3,结果见图8。可以看出,随着脉冲电流的增大,长出单位厚度膜层所消耗的能量呈线性增加趋势,在200 A达到最小值42.1 kJ/?m。MAO膜层增厚过程是试样表面在脉冲电场作用下“击穿-熔融-淬冷”循环作用后的结果,在相同击穿次数下单脉冲击穿所产出熔融物的数量是决定膜层生长速率的关键因素。因此,脉冲电流越大,熔融产物相对也越多,膜层生长的速度越快,生长单位膜层厚度需要消耗能量也就越多。结合微观结构分析,小脉冲电流输出模式下,铝合金的MAO效率比较低,虽然膜层生长的速度慢,但是膜层质量较好,生长单位厚度所消耗的能量较少;大脉冲电流输出模式下,铝合金的MAO效率比较高,膜层生长的速度快,但是膜层质量较差,生长单位厚度所消耗的能量较多。
图8 脉冲电流对MAO陶瓷层生长单位厚度能量消耗的影响
3 结论
(1) 随着脉冲电流由100 A增至800 A,1050铝合金微弧诱发时间由360 s缩短至15 s,诱发电压由341 V升高至887 V。
(2) 微弧诱发过程能量消耗随脉冲电流增大先减少后增加,并在200 A时达到最小值18.3 kJ;陶瓷层生长过程能耗随脉冲电流增大近似成倍增加。
(3) 小脉冲电流输出模式下,1050铝合金MAO效率较低,陶瓷层生长速度慢,但膜层质量好,生长单位厚度消耗的能量少;大脉冲电流输出模式下,1050铝合金MAO效率较高,陶瓷层生长速度快,但膜层质量差,生长单位厚度消耗的能量多。
(4) 随脉冲电流增加,陶瓷层表面放电微孔孔径增大,微孔数量减少,陶瓷层厚度增加的同时表面粗糙度升高,耐蚀性略有降低。
参考文献
[1] Lia H X, Rudnev V S, Zheng X H, et al.Characterization of Al2O3 ceramic coatings on 6063 aluminum alloy prepared in borate electrolytes by micro-arc oxidation[J]. J. Alloy. Compd., 2008, 462: 99
[2] Wang C J, Jiang B L, Liu M, et al.Corrosion characterization of micro-arc oxidization composite electrophoretic coating on AZ31B magnesium alloy[J]. J. Alloy. Compd., 2015, 621: 53
[3] Guo P Y, Wang X F, Shao Y.Formation mechanism and corrosion behavior of micro-arc oxidation ceramic layers on 1050 pure aluminum[J]. Corros. Sci. Prot. Technol., 2011, 23: 490(郭平义, 王晓璠, 邵勇. 1050纯铝微弧氧化陶瓷层的生长动力学与腐蚀性能研究[J]. 腐蚀科学与防护技术, 2011, 23: 490)
[4] Gupta P, Tenhundfeld G, Daigle E O, et al.Electrolytic plasma technology: Science and engineering?An overview[J]. Surf. Coat. Technol., 2007, 201: 8746
[5] Jaspard?Mécuson F, Czerwiec T, Henrion G, et al. Tailored aluminum oxide layers by bipolar current adjustment in the plasma electrolytic oxidation (PEO) process[J]. Surf. Coat. Technol., 2007, 201: 8677
[6] Jiang B L, Zhang X F.Growth process and corrosion resistance ofceramic coatings formed by micro-oxidation on magnesium alloy[J]. J. Chin. Soc. Corros. Prot., 2005, 25: 97(蒋百灵, 张先锋. 镁合金微弧氧化陶瓷层的生长过程及其耐蚀性[J]. 中国腐蚀与防护学报, 2005, 25: 97)
[7] Ge Y F, Jiang B L, Shi H Y.Effect of current pulse width on micro-arc oxidation process for aluminum alloy[J]. Trans. Mater. Heat Treat., 2013, 34: 165(葛延峰, 蒋百灵, 时惠英. 电流脉冲宽度对铝合金微弧氧化过程的影响[J]. 材料热处理学报, 2013, 34: 165)
[8] Jiang B L, Liu D J.Scientific aspects of restricting development and application of micro-arc oxidation technology[J]. Chin. J. Nonferrous Met., 2011, 21: 2402(蒋百灵, 刘东杰. 制约微弧氧化技术应用开发的几个科学问题[J]. 中国有色金属学报, 2011, 21: 2402)
[9] Yerokhin A L, Shatrov T A, Samsonov V, et al.Oxide ceramic coatings on aluminium alloys produced by a pulsed bipolar plasma electrolytic oxidation process[J]. Surf. Coat. Technol., 2005, 199: 150
[10] Liu R M, Guo F, Li P F.Effect of voltage on formation of ceramic coating prepared by micro-arc oxidation on aluminum alloy[J]. Trans. Mater. Heat Treat., 2008, 29: 137(刘荣明, 郭锋, 李鹏飞. 电压对铝合金微弧氧化陶瓷层形成的影响[J]. 材料热处理学报, 2008, 29: 137)
[11] Hou W A, Hu J H, Song X J.The influence of power supply modeon the process and performance of coating of micro-arc oxidation[J]. Nonferrous Met.(Extr. Metall.), 2007, (S1): 122(侯伟骜, 胡江辉, 宋希剑. 电源工作模式对微弧氧化过程和膜层性能的影响[J]. 有色金属 (冶炼部分), 2007, (S1): 122)
[12] Yerokhin A L, Snizhko L O, Gurevina N L, et al.Discharge characterization in plasma electrolytic oxidation of aluminium[J]. J. Phys. D: Appl. Phys., 2003, 3: 2110
[13] Cui X J, Wang R, Wei J S, et al.Effect of electrical parameters on micromorphology and corrosion resistance of micro-arc oxidation coating on AZ31B Mg alloy[J]. J. Chin. Soc. Corros. Prot., 2014,34: 495(崔学军, 王荣, 魏劲松等. 电参数对AZ31B 镁合金微弧氧化膜微观形貌及耐蚀性的影响[J]. 中国腐蚀与防护学报, 2014, 34: 495)
[14] Jiang B L, Zhang S F, Wu G J.Study of corrosion resistance on ceramic coatings formed by micro-arc oxidation on magnesium alloys[J]. J. Chin. Soc. Corros. Prot., 2002, 22: 300(蒋百灵, 张淑芬, 吴国建等. 镁合金微弧氧化陶瓷层耐蚀性的研究[J] .中国腐蚀与防护学报, 2002, 22: 300)
[15] Zhao J, Song R G, Li H X, et al.Effects of nano-additive on microstructure and properties of micro-arc oxidation coatings on 6063 aluminum alloy[J]. Trans. Mater. Heat Treat., 2010, 31: 125(赵坚, 宋仁国, 李红霞等. 纳米添加剂对6063铝合金微弧氧化层组织与性能的影响[J]. 材料热处理学报, 2010, 31: 125)
[16] Lv G H, Gu W C, Chen H, et al.Characteristics of ceramic coatings on aluminum formed by plasma electrolytic oxidation in silicate and phosphate electrolyte[J]. Appl. Surf. Sci., 2006, 253: 947
免责声明:本网站所转载的文字、图片与视频资料版权归原创作者所有,如果涉及侵权,请第一时间联系本网删除。
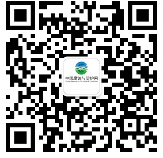
官方微信
《中国腐蚀与防护网电子期刊》征订启事
- 投稿联系:编辑部
- 电话:010-62316606-806
- 邮箱:fsfhzy666@163.com
- 中国腐蚀与防护网官方QQ群:140808414