胜利海上油田的累计开发时间长达26年,部分平台采油井已进入开采后期,出砂严重,含水率高达90%以上,平台间大量采用油气水混输,这导致油井至计量间的单井管线容易受到冲蚀,形成沟槽,弯头位置尤为严重, 且随着采出液含水率不断上升以及化学驱影响,油井采出液携带砂的能力增强,管道的冲蚀风险加剧,管线寿命缩短,原油泄漏事故频发。
固体颗粒冲蚀是结构壁面受到离散微粒冲击产生损伤的一种现象。影响冲蚀的因素多达三十余种,其中比较重要的影响因素有颗粒速度,冲击角,颗粒尺寸、形状、材质,以及被冲击表面的材料属性等。含固体颗粒的多相流管道的冲蚀非常复杂,管道内的流型多变。这导致离散颗粒的运动更为复杂,而颗粒的运动及分布又直接决定了管道的冲蚀特性。
近年来,国内外学者对于管道的冲蚀进行了一系列研究,但关于油气水砂三相流环境中的冲蚀研究尚不多见。为此,西安石油大学石油工程学院和中石化胜利油田分公司海洋采油厂的研究人员利用计算流体力学(CFD)数值分析方法,连接海底与海上平台相连的输送管道内的砂粒流动特性及其对管壁的腐蚀特性,考虑更为真实的油气水三相黏性湍流态流体与砂粒之间的相互作用。
1 研究方法
针对海上油田的典型管道布置方式,选取冲蚀风险较大的海上平台至海底的管段进行分析研究,管道三维模型如图1所示。管道流动计算模型的网格剖分使用六面体单元进行划分,最终得到的模型网格数量为670万。计算网格模型如图2所示。
图1 管道结构示意
图2 网格划分示意
使用CFD程序对输送管道内的油气水砂多相流的物理现象进行求解,分别使用欧拉-欧拉多相流体系和欧拉-拉格朗日多相流体系求解连续相及离散相。在计算中,CFD多相流控制方程主要包含质量守恒和动量守恒方程,使用Edwards等给出的一种可应用于CFD的磨损预测模型预测颗粒腐蚀,该模型考虑了颗粒的碰撞速度、侵入角、形状、直径和质量流量等因素,其表达式为:
式中:V为磨损量;p为靶材流动应力;K为常数,经试验验证;a为冲击角;m为颗粒质量;v为颗粒速度。
本工作并不需要考虑流体的化学属性,因此近似将任意一相流体介质考虑为物性接近的纯净物。选取油田的典型输量和含砂率进行分析。
2 试验结果
流场计算结果
管道各处横截面上的流速分布情况如图3所示。可以发现,在重力和浮升力的作用下,油气水混合物的高速区向下方偏移。进入立管弯头时,在离心力的作用下在速度分布上体现为偏心程度更强。总体而言,速度分布在水平管段主要受重力作用,在弯头附近主要受离心力作用。
图3 截面流速分布云图
油气两相的相含率分布情况如图4所示。可以发现,各相在进入平台水平管段的初始分布接近于均匀混合,随着在水平管段的流动,在重力和浮升力的作用下气相和油相逐渐向管顶聚集。进入立管弯头后,在离心力的作用下气相迅速向弯头外侧移动。在立管段,油气两相又逐渐恢复均匀混合分布,当由立管段进入海底水平段时气相又向弯外侧偏移。
(a)油相
(b)气相
图4 截面相分布云图
冲蚀计算结果
管道两个弯头附近的含砂率分布如图5所示。可以发现,砂粒在重力和自身惯性的作用下在平台进入立管的弯头附近时主要向弯心聚集。而在立管进入海底管的弯头附近时,重力不再影响砂粒的偏转,在重力的作用下砂粒向弯头外侧聚集。可见,冲蚀将主要发生在弯头外侧的壁面。
图5 截面颗粒相分布云图
图6和图7所示为不同条件下管道弯头附近壁面当量冲蚀量,表示因冲蚀而产生的壁面单位面积材料损失量。可以发现,由于在弯头附近离心力的作用,砂粒在弯头外侧的运动速度更高。而随着输液量的增加,砂粒对下弯管处管壁的冲蚀随之增大,冲蚀范围也有所增加,尤其是在输液量达到1万立方米/天时,上部弯管也开始出现砂粒冲蚀较明显的区域。
(a) 0.2万方/天 (b)0.5万方/天
(c)1万方/天 (d)2万方/天
图6 不同输量下管道弯头处腐蚀量分布图
(a)0.005% (b)0.01%
(c)0.02% (d)0.04%
图7 不同含砂率下管道弯头处腐蚀量分布图
图8 不同条件下的管道最大腐蚀量
结合图6~8可知,随着输液量的增加,冲蚀范围有所增加,冲蚀率也随之增长。相同输液量的情况下,含砂率的增加虽然不会对冲蚀范围造成影响,但却会导致冲蚀率的增长。
3 结 论
(1) 使用CFD数值计算方法,选取适当的物理及数学模型能够良好捕捉到管道中的流动形态以及相分布规律。选取领域内经过验证的颗粒冲蚀模型能够良好捕捉到管道中的腐蚀分布规律;
(2) 在惯性和连续流体介质共同作用下,砂粒堆积主要发生在管道弯头的外侧区域。而在本工作研究的海上油田低含砂量范围下砂粒在管道内的总体冲蚀量仍然较低;
(3) 冲蚀率随着输液量的增加而增大,冲蚀范围也同时增加。相同输液量下,冲蚀率随着含砂率的增加而增大,但对冲蚀范围无明显影响。
免责声明:本网站所转载的文字、图片与视频资料版权归原创作者所有,如果涉及侵权,请第一时间联系本网删除。
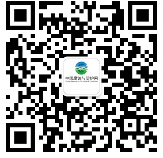
官方微信
《中国腐蚀与防护网电子期刊》征订启事
- 投稿联系:编辑部
- 电话:010-62316606-806
- 邮箱:fsfhzy666@163.com
- 中国腐蚀与防护网官方QQ群:140808414