摘要
采用往复式销盘摩擦试验机和电化学工作站研究了2024铝合金/Al2O3陶瓷在海水环境下的腐蚀磨损行为以及腐蚀磨损之间的交互作用。结果表明:在模拟海水实验条件下,2024铝合金在开路电位下的腐蚀磨损量明显大于其在阴极保护条件下的磨损量,说明腐蚀与磨损发生交互作用。纯磨损量约占总腐蚀磨损量的比例 (W0/T ) 为70.3%~98.2%,在腐蚀磨损过程中磨损作用明显大于腐蚀作用。腐蚀磨损交互作用量占总腐蚀磨损量的比例 (S/T ) 为1.8%~29.7%,腐蚀磨损交互作用同样不可忽视。
关键词: 2024铝合金 ; 海水 ; 腐蚀磨损 ; 交互作用
1 前言
铝合金具有较低的密度、良好的力学性能、加工性能、导热性、导电性以及耐蚀性和低成本等一系列优点,在船用设备领域中的应用日趋广泛,对减轻船体结构质量、提高航行速度和减少能耗等方面有着重要作用,同时在航空方面一直是大飞机机体结构的主要用材[1,2]。然而,随着船舶、飞机以及海洋设备等服役时间的增长,铝合金结构受到苛刻的海洋环境影响而产生的腐蚀问题日益突出,腐蚀损伤会削弱结构的承力面积,“降低结构的疲劳性能”,进而威胁航行和飞行安全并影响机体的结构寿命。尤其是海军的特种飞机如水上飞机、舰载机等常遇到海水、盐雾、潮湿等腐蚀性较强的自然环境,飞机机身铆接和销钉连接的构件极易受微动腐蚀的影响,自1975年以来,在美国发生的多起飞行事故中,腐蚀和/或微动是造成事故的主要原因之一[3,4]。但关于铝合金的性能研究,国内外研究的热点多集中于各类介质中的单纯耐腐蚀性方面,如海水、酸雨、潮湿的大气腐蚀等。黄桂桥[5]研究了铝合金在海水中的耐蚀性与腐蚀电位的关系,耐海水腐蚀性能较好的铝合金,其初始电位、稳定电位均较负。张有宏等[6]对遭受不同程度腐蚀损伤的铝合金结构性能进行了研究,表明铝合金疲劳寿命随着腐蚀损伤深度的增加而降低,且通过有限元分析很好的验证了这一结论。林乐耘等[7]做了大量不同海域挂样实验,表明不同海域的海水对铝合金显示不同的腐蚀性,其内在原因是海水自身的“电解质效应”使铝合金的腐蚀电位上升,局部腐蚀敏感性增强。近年来,随着对矿产资源的深部勘探开发的需求,与钢钻杆相比,铝合金钻杆具有比强度高、密度低、弯曲应力小、耐腐蚀等优点,具有应用于深井、超深井和酸性气井勘探开发的巨大优势[8,9]。2006年,我国依据欧盟制定的国际标准,发布了国标GB/T20659-2006/ISO15546-2002《石油天然气工业铝合金钻杆》,并于2007年5月1日起实施,这为我国高强度铝合金钻杆的研制和应用奠定了基础。但我国石油勘探用铝合金钻杆的应用还处于起步阶段,钻杆磨损行为研究仍处于空白[10]。
在海洋环境中海工装备的使用损伤则同时受到腐蚀与磨损共同作用。腐蚀磨损一般是指发生在腐蚀介质中的磨损现象,是力学因素、化学因素以及电化学因素及其交互作用的结果[11]。当材料在腐蚀环境中滑动时,力学和电化学因素的共同作用可能会产生复杂的反应并促进其失效。海水是一个非常复杂的多组分盐溶液,含有许多如Na+,K+,Ca2+,Mg2+等阳离子和Cl-,Br-,HCO3-,CO32-,F-等阴离子,虽然铝合金是易钝化的金属,但在磨损过程中,当金属的钝化态被局部破坏时,这些离子很容易侵蚀到缺陷处对基体进行破坏,从而改变材料的摩擦学行为。
而在铝合金的腐蚀磨损方面,科研人员[12,13]研究了铝合金在不同介质环境下腐蚀对摩擦磨损的影响,但未能做到对铝合金腐蚀磨损的动态监控以及定量分析。考虑到这些因素,本文将电化学工作站和摩擦磨损试验机连用,对海工装备常用的2024铝合金在海水中的腐蚀磨损行为进行研究,探寻铝合金在海水环境中的腐蚀磨损交互作用机理,为铝合金作为海工材料的选用奠定理论基础。
2 实验方法
2.1 实验材料
选用2024铝合金在海水环境下进行腐蚀磨损实验,其化学成分 (质量分数,%) 为:Cu 4.2,Si 0.5,Fe 0.5,Mn 0.6,Mg 1.2,Zn 0.25,Cr 0.1,Ti 0.15,Al余量。将铝合金切割成直径6 mm,高4 mm的圆柱样品。实验前,分别用600#,1200#,1500# SiC砂纸逐级打磨样品、再用3 μm的金刚石研磨膏抛光处理,并在丙酮和乙醇中各超声清洗10 min,以除去样品表面的油污,减少实验误差。为了避免在实验过程中异种金属接触可能产生的电位干扰以及电偶腐蚀,对偶材料选用不导电的Al2O3陶瓷块,Al2O3试样尺寸为25 mm×20 mm×2 mm。实验用海水为按照ASTM G1148—98标准配置的人工海水[14],用0.1 mol /L的NaOH溶液调节pH值至8.2。
2.2 腐蚀磨损测试
实验采用Rtec摩擦磨损试验机对2024铝合金在海水环境下的摩擦磨损性能进行测试,摩擦方式为栓-盘式往复运动。为了监控2024铝合金在摩擦过程中的电位和电流变化,同时连接Modulab ECS电化学工作站。以2024铝合金试样作为工作电极,Ag/AgCl电极作为参比电极,Pt丝电极作为辅助电极,组成三电极系统,进行相应的电化学测量和监控,测定其在不同实验条件下的腐蚀磨损性能。腐蚀磨损装置如图1所示。摩擦实验载荷分别为5,10,25和50 N,滑动速率为20 mm/s,测试时间为30 min。每次实验前后将样品清洗干净,烘干并称重,取3次失重数据的平均值作为铝合金磨损量。采用维氏显微硬度仪、FEI Quanta 250 FEG 场发射扫描电镜 (FE-SEM)、AXIS UTLTRA DLD X射线光电子能谱仪 (XPS) 分别测试磨损前后样品的硬度变化,不同载荷下的磨损形貌以及磨损表面不同深度元素分析。
图1 腐蚀磨损试验机示意图
2.3 电化学测试
为了研究腐蚀与磨损间的交互作用,需要对海水环境的腐蚀作用进行屏蔽,采用阴极保护作用来抑制海水对材料的腐蚀,其阴极保护电位为-1400 mV (vs Ag/AgCl)。
为了研究滑动磨损对铝合金电化学性能的影响,利用电化学工作站测试不同载荷下铝合金的开路电位和动电位极化曲线,其中开路电位测试过程为:首先将测试样品在人工海水中浸泡10 min,待开路电位稳定后,启动滑动磨损30 min,测试开路电位变化,待滑动停止后再测试磨损样品的开路电位;极化曲线测试条件:测量静态腐蚀以及滑动磨损过程中的动电位极化曲线,扫描范围为-0.5~1 V(vs OCP),扫描速率为2 mV/s,通过Tafel曲线得到腐蚀电流密度,并计算腐蚀速率。
2.4 腐蚀磨损定量测试
在腐蚀磨损过程中,材料的破坏受材料因素、力学因素和环境因素的共同作用。在腐蚀介质中,电化学因素和力学因素对材料产生明显的腐蚀磨损交互作用[15]。实验中腐蚀与磨损的交互作用和磨损量的计算按照ASTM G119-09标准进行。在腐蚀环境中摩擦的总磨损量T要大于纯机械磨损量W0与纯腐蚀量C0之和,其增加量可认为是腐蚀和磨损的交互作用量S:
(1)
而S又可分为两部分:腐蚀对磨损的促进量
以及磨损对腐蚀的促进量 ,即:
(2)
所以式 (1) 也可以改写为:
(3)
而T又可以分为磨损分量W和腐蚀分量C,且:
实验采用失重法分别测得开路电位下和阴极保护电位下的磨损量,即可分别得到T和W0;根据实测极化曲线得到2024铝合金在静态腐蚀条件下以及摩擦过程中的腐蚀电流密度,按照标准ASTM G119-09即可计算得到C0和摩擦过程中的C。
3 结果与讨论
3.1 载荷对摩擦磨损的影响
海水环境中2024铝合金在不同载荷下摩擦的摩擦系数见图2a。随着载荷的增加,摩擦系数均减小。这是因为随着载荷的增加,局部应力将迅速增加,使得表面的微凸峰容易在正应力的作用下产生屈服、疲劳而最终脱落成小磨屑,这些小磨屑在有限的实际接触区内主要充当“滚珠”的角色,从而使铝合金的摩擦系数随着载荷的升高呈单调的下降趋势[12]。同时也可以看出,纯机械磨损 (阴极保护下) 的摩擦系数均要略小于腐蚀磨损的摩擦系数,这是由于在海水坏境下,腐蚀的发生会使材料表面形成一层粗糙的、疏松的腐蚀产物膜[16],使材料的摩擦系数增大。
图2 海水中2024铝合金在不同载荷下的摩擦系数, 磨损量和显微硬度的变化曲线
海水环境中2024铝合金在不同载荷下摩擦之后的磨损量变化如图2b所示。可见,随着载荷的增加,磨损量增加。这是因为随载荷的增加,在正应力的作用下使得表面的微凸峰容易产生屈服、疲劳而最终脱落成小磨屑,使两体摩擦转变为三体摩擦,磨屑被氧化后硬度提高,充当磨粒的作用,在剪切应力的作用下,在磨痕表面留下犁沟痕迹如图3所示,证实了以上摩擦系数逐渐减小的趋势。从图2b中也可以看出,纯机械磨损工况下的磨损量均要小于腐蚀磨损下的磨损量,即说明在摩擦过程中,海水对2024铝合金的腐蚀作用加速磨损。
图3 不同载荷下纯机械磨损和腐蚀磨损后2024铝合金试样表面形貌的SEM像
海水环境中2024铝合金在不同载荷下摩擦后的表层硬度变化如图2c所示。可见,随着载荷的增加,材料的显微硬度增加,而且纯机械磨损条件下的硬度要大于腐蚀磨损条件下的硬度。这是因为在不同载荷作用下,材料发生了不同程度的塑性变形,导致位错能堆积,增加了化学反应发生的可能,同时硬度上升[17]。腐蚀的发生会使材料表面形成一层粗糙的、疏松的腐蚀产物膜,降低或抑制材料的形变强化,其切变强度变小,磨损量上升。
3.2 磨损表面形貌和XPS分析
2024铝合金在海水中不同载荷下摩擦后的磨损表面形貌如图3所示。可以看到磨损表面沿着摩擦方向有明显的划痕,且载荷越大,沟槽越深。另外,从图3a~d可以看出,随着载荷的增加沿摩擦方向出现许多块状撕裂边,表明海水中2024铝合金在阴极保护下载荷较小时,磨损机理以磨粒磨损为主;载荷较大时,主要磨损机理为磨粒磨损加粘着磨损[13]。而直接在海水中摩擦时 (图3e~h),磨损表面存在许多犁沟和撕裂边的同时,还有许多黑色小斑。在载荷较大时 (图3d),在撕裂边缘和划痕周围存在裂纹。对于这种现象有两种可能,一种可能是在海水中,由于电化学的作用,在滑移处将产生微观缝隙腐蚀,微观腐蚀在交变应力作用下可发展成裂纹[13,17]。另一种可能是,铝合金在海水中形成一层以非晶γ-Al2O3为主的含水氧化物表面膜,形成的钝化膜孔率大、不致密、保护能力差,且含水的Al2O3H2O在室温下质脆、易剥落,高载下的磨损很容易导致脆性Al2O3薄膜受损形成机械裂缝[12],在往复载荷的作用下剥落,加速铝合金磨损。所以会出现图2f中腐蚀磨损下的磨损量要大于纯机械磨损工况下的磨损量的现象,即在摩擦过程中,海水对2024铝合金的腐蚀作用加速磨损。
为了研究磨损表面腐蚀磨损产物膜的主要成分,对磨损表面做不同深度的XPS分析,如图4所示。可以看出,Al2p谱均为双峰,分别在结合能为74.9和72.5 eV附近,对比标准数据库和手册可知,磨损表面形成一层以γ-Al2O3 (74.9 eV) 为主的氧化层,且随着刻蚀时间的增长,即不同深度亚表层的γ-Al2O3减少,金属Al (72.5eV) 的含量上升。验证了铝合金在海水中形成一层以非晶γ-Al2O3为主的含水氧化物表面膜,形成的钝化膜孔率大、不致密、保护能力差,且含水的Al2O3H2O在室温下质脆、易剥落,高载下的磨损很容易导致脆性Al2O3薄膜受损形成机械裂缝,在往复载荷的作用下剥落,加速铝合金磨损。而经抛光处理的铝合金表面较为活泼,在大气中也会形成一层氧化层,具有一定的耐蚀性,但厚度较薄,在实验开始摩擦2~5 min内就已经磨损 (如图5所示),表现为开路电位急剧下降。腐蚀磨损过程中形成的孔隙率大、不致密的产物膜,不同于实验前经抛光处理的铝合金表面形成的均匀、较薄的氧化膜,也不同于未经处理的铝合金表面的致密、较厚的氧化层。
图4 海水环境中2024铝合金试样在50 N载荷下摩擦不同时间后的磨损表面的XPS谱
图5 2024铝合金在人工海水中不同载荷下摩擦前后以及摩擦过程中的开路电位变化
3.3 载荷对电化学腐蚀行为的影响
在海水环境下,2024铝合金在不同载荷下从静态到滑动磨损再到滑动结束3个阶段的开路电位变化如图5所示。可以看出,在静态条件下,开路电位约在-0.67 V。当达到600 s开始滑动时,开路电位急速下降,而且载荷越大,开路电位越负;但是在载荷为25和50 N时,在滑动过程中有先降低至最负点再回升趋于动态平衡的现象。在2400 s时,滑动结束,电位开始快速回升。这是因为Al是化学性质很活泼的金属,Al及其合金在大气中就可生成一层钝化膜,当开始滑动时,所形成的钝化膜在滑动磨损下被破坏,使铝合金基体开始暴露在海水环境下,故电位开始急剧下降,而暴露的部位在海水中易形成钝化膜。因此滑动过程就是钝化膜破坏与修复的动态平衡过程。其次,载荷越大,上下试样接触面塑性变形越严重,对钝化膜的破坏越严重,开路电位下降的幅度越大[18]。最后,滑动磨损结束,开路电位迅速增大,而后缓慢增加至趋于平衡,这主要是由于滑动停止后铝合金磨损面迅速形成钝化膜,随着浸泡时间大,纯机械磨损量和总磨损量都很大,此时铝合金在两种工况下磨损均进入严重磨损阶段,因此,此时纯机械磨损量占总磨损量的比例要大于载荷为10 N时的,即交互作用量占总磨损量的比例要小于10 N时的。另外,从表2和图7中还可以看出,2024铝合金在海水环境下,随载荷的增加,ΔCW逐渐增加,但ΔCW占T的比例非常小 (不到1%),而ΔWC占T的1.8%~29.7%。以上结果表明,在海水环境中2024铝合金在不同载荷下腐蚀磨损的交互作用主要体现在腐蚀对磨损的促进作用。
图6 2024铝合金试样在静态和腐蚀磨损过程中的极化曲线
图7 腐蚀磨损过程中各组成部分占总磨损量的比例随载荷的变化
表2 腐蚀磨损过程中各组成部分以及所占的比例
4 结论
(1) 在人工海水中2024铝合金腐蚀磨损时开路电位降低,腐蚀电流密度大幅增加,磨损作用明显提高了2024铝合金的腐蚀速率,即磨损促进腐蚀。
(2) 2024铝合金在海水中摩擦以磨粒磨损和粘着磨损为主要磨损机理。在海水介质中,2024铝合金表面会形成在室温下质脆、易剥落含水的Al2O3H2O氧化膜,高载下的磨损很容易导致脆性Al2O3薄膜受损,加速材料的剥落,腐蚀磨损加重。
(3) 2024铝合金在海水环境下的腐蚀磨损过程中,磨损作用明显大于腐蚀作用,力学因素是造成腐蚀磨损失重的主要因素;同时腐蚀与磨损的交互作用也是不可忽视的,其主要源于腐蚀对磨损的促进作用。
The authors have declared that no competing interests exist.
免责声明:本网站所转载的文字、图片与视频资料版权归原创作者所有,如果涉及侵权,请第一时间联系本网删除。
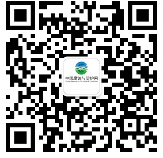
官方微信
《腐蚀与防护网电子期刊》征订启事
- 投稿联系:编辑部
- 电话:010-62316606-806
- 邮箱:fsfhzy666@163.com
- 腐蚀与防护网官方QQ群:140808414